Unlocking Superior Thermal Management with Custom Silicon Carbide
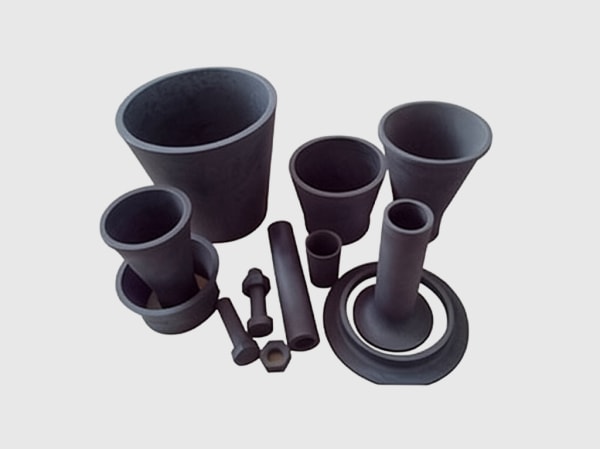
Share
In today’s technologically advanced industrial landscape, the demand for materials capable of performing under extreme conditions has never been greater. As electronic devices become smaller, more powerful, and operate at higher frequencies, efficient thermal management is no longer a luxury but a critical necessity. Poor heat dissipation can lead to reduced performance, decreased reliability, and even catastrophic failure of components and systems. This is where custom silicon carbide (SiC) emerges as a champion material, offering unparalleled thermal conductivity, stability, and mechanical robustness for the most demanding applications. This blog post delves into the world of silicon carbide for thermal management, exploring its applications, advantages, design considerations, and how choosing the right supplier, like CAS new materials (SicSino), can be a game-changer for your high-performance industrial needs.
Introduction to Silicon Carbide’s Superior Thermal Management Capabilities
Silicon Carbide (SiC) is an advanced ceramic material renowned for its exceptional combination of physical and chemical properties. Composed of silicon and carbon, SiC boasts incredibly strong covalent bonds, giving rise to its high hardness, strength, and, crucially for thermal management, outstanding thermal conductivity. Unlike traditional heat sink materials like copper or aluminum, silicon carbide maintains its excellent thermal properties even at elevated temperatures, making it indispensable in environments where other materials falter.
The primary reason SiC is favored for thermal management is its ability to efficiently conduct heat away from critical components. Its thermal conductivity can be significantly higher than many metals, especially at higher operational temperatures. This efficiency in heat dissipation helps to maintain optimal operating temperatures for sensitive electronics and industrial equipment, thereby enhancing their lifespan and performance. Furthermore, custom silicon carbide thermal management solutions allow for designs tailored to specific application requirements, maximizing thermal efficiency in complex systems. Industries are increasingly turning to advanced ceramic solutions like SiC to push the boundaries of performance and reliability.
At CAS new materials (SicSino), located in Weifang City, the heart of China’s silicon carbide manufacturing hub, we have witnessed firsthand the transformative impact of SiC. Since 2015, we have been instrumental in advancing SiC production technology, supporting local enterprises in achieving large-scale production and technological breakthroughs. Our deep understanding of SiC material science and manufacturing processes positions us uniquely to deliver high-quality, custom SiC components optimized for superior thermal management.
Key Applications Leveraging SiC for Optimal Thermal Performance
The exceptional thermal properties of silicon carbide make it an ideal material for a wide array of applications where efficient heat dissipation is paramount. As industries push for higher power densities and operational efficiencies, the role of industrial SiC components and high-temperature SiC parts continues to expand.
One of the most significant application areas for SiC in thermal management is power electronics. Devices such as MOSFETs, SBDs, and IGBTs made from SiC can operate at higher voltages, temperatures, and switching frequencies than their silicon-based counterparts. This increased performance generates more heat, necessitating advanced cooling solutions. SiC substrates and heat spreaders provide the necessary thermal pathways to keep these powerful devices within their optimal operating temperatures, ensuring reliability and longevity. Applications include:
- Inverters and converters for renewable energy systems (solar, wind)
- Electric vehicle (EV) power modules and charging stations
- Industrial motor drives
- Uninterruptible Power Supplies (UPS)
Heat exchangers represent another critical application. In high-temperature industrial processes, such as chemical processing, waste heat recovery, and metal treatment, SiC heat exchangers offer superior performance due to their high thermal conductivity, excellent corrosion resistance, and ability to withstand extreme temperatures and thermal shock. This leads to more efficient energy utilization and longer service life compared to metallic alternatives.
In the realm of LED lighting, particularly for high-power LEDs used in industrial, automotive, and large-venue lighting, SiC serves as an excellent substrate material. Efficiently dissipating the heat generated by LED chips is crucial for maintaining light output, color consistency, and extending the lifespan of the lighting system. SiC thermal spreaders play a vital role here.
The aerospace and defense industries also rely on SiC for thermal management in demanding applications. From avionics cooling to thermal protection systems for spacecraft and missiles, SiC’s lightweight nature (compared to some high-temperature metals), high thermal stability, and mechanical strength are highly valued.
Other notable applications include:
- Semiconductor manufacturing equipment: Components like wafer chucks and processing chamber parts that require precise temperature control.
- High-temperature furnaces: Linings, kiln furniture, and heating elements where thermal stability and shock resistance are critical.
- Laser systems: Heat sinks for high-power laser diodes and optical components.
The versatility of custom silicon carbide products means that solutions can be engineered for very specific thermal challenges across these diverse industries, ensuring optimal performance and reliability.
The Advantages of Custom Silicon Carbide in Thermal Systems
Opting for custom silicon carbide components in thermal systems offers a multitude of advantages that go beyond what standard off-the-shelf materials can provide. The ability to tailor the material properties and component design to specific application needs is crucial for achieving peak thermal performance, longevity, and cost-effectiveness in advanced industrial systems. Key benefits include:
- Exceptional Thermal Conductivity: SiC exhibits high intrinsic thermal conductivity, often ranging from 120 to over 270 W/mK depending on the grade and manufacturing process. This allows for rapid and efficient heat dissipation from heat-generating sources, minimizing thermal gradients and preventing overheating. This is particularly vital for advanced ceramic heat sinks and SiC thermal spreaders designed to cool high-power density electronics.
- Low Coefficient of Thermal Expansion (CTE): Silicon carbide has a relatively low CTE, which is closely matched to that of semiconductor materials like silicon. This minimizes thermo-mechanical stress at the interface between the SiC component and the device it’s cooling, especially during thermal cycling. Reduced stress leads to improved reliability and prevents premature failure of the assembly.
- High-Temperature Stability: Unlike metals whose thermal and mechanical properties degrade significantly at high temperatures, SiC maintains its excellent thermal conductivity, strength, and structural integrity even at temperatures exceeding 1000∘C (and up to 1650∘C or higher for certain grades in controlled atmospheres). This makes it an ideal choice for applications involving extreme heat, such as furnace components or exhaust systems.
- Superior Mechanical Strength and Hardness: SiC is an exceptionally hard and strong material, resistant to wear, abrasion, and erosion. This ensures that thermal management components made from SiC can withstand harsh operating conditions, including high pressures or particulate-laden flows, without significant degradation. This durability contributes to longer service life and reduced maintenance requirements.
- Excellent Chemical Inertness and Corrosion Resistance: Silicon carbide is highly resistant to a wide range of corrosive chemicals, acids, and alkalis, even at elevated temperatures. This makes it suitable for thermal management in chemically aggressive environments, such as those found in chemical processing plants or applications involving corrosive coolants.
- Design Flexibility with Customization: Custom SiC manufacturing allows engineers to design complex geometries and integrate features specifically optimized for their thermal challenges. This includes intricate channel designs for liquid cooling, precise mounting features, and optimized surface areas for enhanced heat transfer. CAS new materials (SicSino), with its deep expertise in SiC processing and design, excels in providing such tailored solutions.
- Electrical Resistivity (Tunable): While some grades of SiC are semiconducting, others can be highly resistive. This property can be advantageous in applications where electrical isolation is required in addition to thermal conductivity, preventing short circuits or electrical interference.
The table below summarizes some key advantages of SiC in thermal systems compared to common alternatives:
Property | Silicon Carbide (SiC) | Aluminum (Al) | Copper (Cu) | Alumina (Al2O3) |
---|---|---|---|---|
Thermal Conductivity | High to Very High (120-270+ W/mK) | High (~200-240 W/mK) | Very High (~400 W/mK) | Moderate (20-30 W/mK) |
Max Operating Temp. | Very High (>1000∘C) | Low (<200∘C) | Moderate (<300∘C) | Very High (>1500∘C) |
CTE Compatibility (Si) | Good | Poor | Poor | Fair |
Mechanical Strength | Very High | Moderate | Moderate | High |
Corrosion Resistance | Excellent | Fair (forms oxide layer) | Poor (oxidizes) | Excellent |
Electrical Resistivity | Tunable (Semiconducting to High Resistivity) | Conductive | Conductive | High Insulator |
By leveraging these inherent benefits through customization, businesses can significantly improve the performance, reliability, and efficiency of their thermal management systems, gaining a competitive edge in their respective markets.
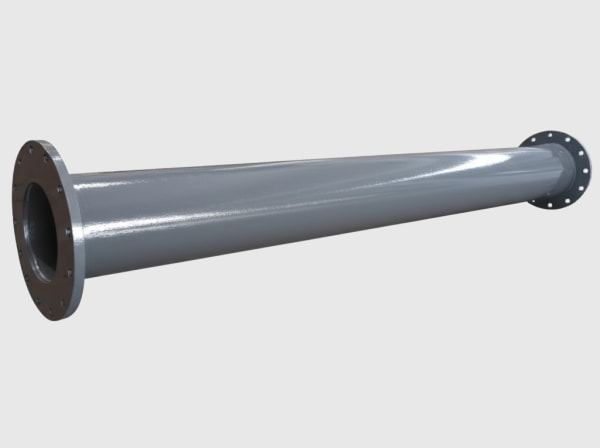
Recommended Silicon Carbide Grades for Thermal Management
Silicon carbide is not a monolithic material; it exists in various grades, each produced through different manufacturing processes and exhibiting a unique set of properties. Selecting the appropriate SiC grade is crucial for optimizing thermal management performance, as well as considering mechanical strength, cost, and manufacturability. CAS new materials (SicSino), with its extensive experience in Weifang City’s SiC manufacturing cluster, offers expertise in guiding customers to the ideal custom SiC grades for their specific thermal applications.
Here are some commonly recommended SiC grades for thermal management:
- Reaction-Bonded Silicon Carbide (RBSiC or SiSiC – Silicon Infiltrated SiC):
- Manufacturing: Produced by infiltrating a porous preform of SiC grains and carbon with molten silicon. The silicon reacts with the carbon to form additional SiC, which bonds the initial grains. The remaining pores are typically filled with free silicon.
- Properties:
- Good thermal conductivity (typically 120-180 W/mK).
- Excellent thermal shock resistance.
- High strength and wear resistance.
- Good dimensional stability and ability to produce complex shapes with tight tolerances.
- Operating temperature generally limited by the melting point of the free silicon (around 1410∘C).
- Thermal Management Applications: Heat exchangers, burner nozzles, kiln furniture, wear-resistant components requiring good thermal dissipation, pump components.
- Considerations: The presence of free silicon can be a limitation in certain highly corrosive environments or at very high temperatures above silicon’s melting point.
- Sintered Silicon Carbide (SSiC):
- Manufacturing: Made from fine SiC powder mixed with sintering aids (typically non-oxide, like boron and carbon). It is then formed and sintered at very high temperatures (over 2000∘C) in an inert atmosphere, leading to a dense, single-phase SiC material.
- Properties:
- Very high thermal conductivity (can exceed 200-270 W/mK for high-purity grades).
- Excellent high-temperature strength and creep resistance (usable up to 1600∘C or higher).
- Superior corrosion and erosion resistance, even against aggressive chemicals.
- High hardness and wear resistance.
- Thermal Management Applications: High-performance heat sinks, substrates for power electronics, furnace components, seal faces, bearings, components for semiconductor processing equipment.
- Considerations: Typically more expensive than RBSiC due to higher processing temperatures and raw material purity requirements. Machining can be more challenging due to its extreme hardness.
- Nitride-Bonded Silicon Carbide (NBSiC):
- Manufacturing: SiC grains are bonded by a silicon nitride (Si3N4) phase.
- Properties:
- Moderate thermal conductivity.
- Excellent thermal shock resistance.
- Good resistance to molten metals and abrasion.
- Thermal Management Applications: Kiln furniture, components for non-ferrous metal contact, crucibles.
- Considerations: Generally lower thermal conductivity compared to SSiC or RBSiC.
- Chemical Vapor Deposited Silicon Carbide (CVD-SiC):
- Manufacturing: Produced by chemical vapor deposition, resulting in an ultra-pure, theoretically dense SiC coating or bulk material.
- Properties:
- Potentially very high thermal conductivity (can exceed 300 W/mK).
- Exceptional purity and chemical resistance.
- Can produce thin films or coatings on other substrates.
- Thermal Management Applications: High-end semiconductor processing components, optics, protective coatings for demanding thermal environments.
- Considerations: Significantly more expensive and typically limited in size and thickness compared to other SiC grades.
The choice of SiC grade will depend on a thorough analysis of the application’s thermal requirements, mechanical stresses, chemical environment, operating temperature, and budget. CAS new materials (SicSino) leverages its position within China’s leading SiC production hub and its collaboration with the Chinese Academy of Sciences (CAS) to offer a comprehensive range of these SiC grades and provide expert consultation to ensure optimal material selection for custom SiC thermal management solutions. Our access to diverse manufacturing technologies allows us to recommend and supply the most suitable and cost-competitive customized silicon carbide components in China.
SiC Grade | Typical Thermal Conductivity (W/mK) | Max Operating Temp. (approx.) | Key Advantages for Thermal Management | Common Thermal Applications |
---|---|---|---|---|
RBSiC / SiSiC | 120 – 180 | 1350−1400∘C | Good thermal shock resistance, complex shapes, cost-effective | Heat exchangers, kiln furniture, general thermal components |
SSiC | 200 – 270+ | 1600−1700∘C | Highest thermal conductivity, excellent corrosion & temp. resistance | Power electronic substrates, high-performance heat sinks |
NBSiC | 50 – 100 | 1400−1500∘C | Excellent thermal shock, molten metal resistance | Kiln components, non-ferrous metal contact |
CVD-SiC | >300 | >1600∘C | Ultra-high purity, highest thermal conductivity (theoretical) | Semiconductor processing, specialized optics, coatings |
Working with a knowledgeable supplier who can explain the nuances of each grade and assist in the selection process is paramount for achieving the desired thermal performance and overall system success.
Designing Custom SiC Components for Effective Heat Dissipation
The design of custom silicon carbide components plays a pivotal role in maximizing their effectiveness for heat dissipation. While SiC’s inherent material properties are excellent, a well-thought-out design ensures that these properties are fully leveraged within the specific thermal management system. Engineers and procurement managers should consider several key aspects when specifying custom SiC manufacturing for thermal applications. Adherence to SiC manufacturing design guidelines can significantly improve performance and reduce costs.
Key Design Considerations:
- Optimizing Geometry for Heat Flow:
- Maximize Surface Area: For components like heat sinks, increasing the surface area exposed to the cooling medium (air or liquid) enhances convective heat transfer. This can be achieved through fins, pins, or complex lattice structures.
- Minimize Thermal Path Length: The shorter and more direct the path for heat to travel from the source to the cooling medium, the lower the thermal resistance. Design components to ensure efficient conduction pathways.
- Consider Heat Spreading: If the heat source is small and concentrated, the SiC component should be designed to spread this heat effectively over a larger area before it is transferred to the ultimate heat sink or cooling fluid. The high thermal conductivity of SiC is particularly beneficial for this.
- Managing Thermal Stress:
- CTE Mismatch: While SiC has a favorable CTE compared to silicon, mismatches with other materials in the assembly (e.g., metallic housings or PCBs) can induce stress during thermal cycling. Designs should incorporate features to accommodate this, such as compliant interface materials or stress-relief structures.
- Sharp Corners and Stress Concentrators: Avoid sharp internal corners or abrupt changes in cross-section, as these can become points of stress concentration, potentially leading to cracking, especially in a brittle material like SiC. Generous radii are recommended.
- Uniform Temperature Distribution: Aim for designs that promote a more uniform temperature distribution across the SiC component to minimize internal thermal stresses.
- Interface Materials and Assembly:
- Thermal Interface Materials (TIMs): The thermal resistance at the interface between the SiC component and the heat source (or other parts of the thermal path) is critical. Selecting an appropriate TIM (e.g., thermal grease, phase change materials, conductive adhesives, or metallic layers for brazing) is essential to minimize this interface resistance. The surface finish of the SiC component also plays a role here.
- Mounting and Clamping: The method of mounting or clamping the SiC component can affect both thermal contact and mechanical stress. Ensure uniform pressure distribution and avoid point loads.
- Integration with Existing Systems:
- Form, Fit, and Function: Custom designs must seamlessly integrate into the larger system. This includes considerations for size, weight, mounting holes, and connections for fluid flow if applicable.
- Manufacturability: While aiming for optimal thermal performance, the design must also be manufacturable within reasonable cost and lead time constraints. Complex features can increase manufacturing difficulty and expense. Early consultation with an experienced SiC manufacturer like CAS new materials (SicSino) is highly beneficial. Our team in Weifang City, backed by the technological capabilities of the Chinese Academy of Sciences (CAS), can provide invaluable design for manufacturability (DFM) support.
- Fluid Dynamics (for Liquid-Cooled Systems):
- Channel Design: For liquid-cooled SiC heat exchangers or cold plates, the design of internal channels (width, depth, path) is critical for optimizing fluid flow, heat transfer coefficients, and minimizing pressure drop.
- Flow Distribution: Ensure even distribution of the coolant across all heat transfer surfaces.
Engineering Tips for SiC Component Design:
- Simulate Performance: Utilize thermal modeling and simulation software (e.g., Finite Element Analysis – FEA, Computational Fluid Dynamics – CFD) to predict and optimize the thermal performance of the SiC component design before manufacturing.
- Iterative Prototyping: For complex applications, consider an iterative prototyping approach to test and refine the design.
- Wall Thickness: Maintain adequate wall thickness to ensure mechanical integrity, but avoid overly thick sections that could increase thermal resistance or material cost unnecessarily. Typical minimum wall thicknesses depend on the SiC grade and manufacturing process.
- Tolerances: Specify realistic and necessary tolerances. Overly tight tolerances can significantly increase manufacturing costs.
By carefully considering these design principles, engineers can create custom SiC components that deliver superior heat dissipation, contributing to the overall efficiency, reliability, and longevity of their thermal management systems. Collaborating with a supplier like CAS new materials (SicSino), who possesses deep material and process knowledge, ensures that these design considerations are expertly addressed, resulting in optimized OEM SiC parts and solutions.
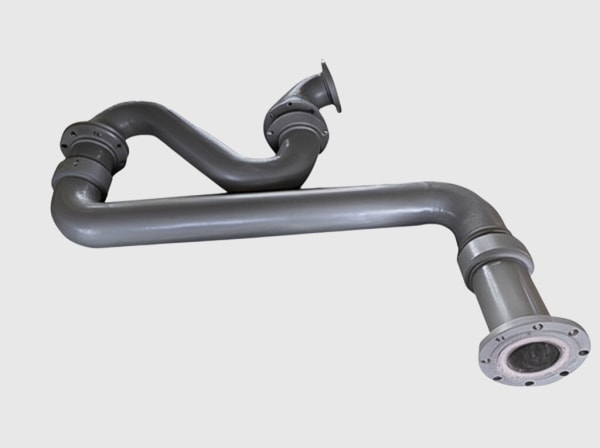
Achievable Tolerances, Surface Finishes, and Their Impact on Thermal Transfer
For precision SiC components intended for thermal management applications, dimensional accuracy, achievable tolerances, and surface finish are not merely cosmetic aspects; they significantly influence thermal performance, particularly at interfaces. Understanding the capabilities of SiC manufacturing processes and how these characteristics affect heat transfer is crucial for engineers and procurement professionals when specifying custom parts.
Tolerances: Silicon carbide is a very hard material, which makes it challenging to machine after sintering or reaction bonding. Therefore, achieving very tight tolerances often involves precision grinding, lapping, or other specialized finishing operations, which can add to the cost.
- As-Sintered/As-Fired Tolerances: Components in their “as-sintered” or “as-fired” state (i.e., after the high-temperature processing but before any significant machining) will have broader dimensional tolerances. These can typically range from ±0.5% to ±2% of the dimension, depending on the SiC grade, size, and complexity of the part. For many bulk thermal components where precise interfacing is not critical, these tolerances may be acceptable.
- Machined Tolerances: For applications requiring tighter control, such as substrates for direct bonding of semiconductor dies or surfaces forming part of a thermal interface, SiC components are typically ground or lapped.
- Grinding: Can achieve tolerances in the range of ±0.01 mm to ±0.05 mm ($ \pm 10 \mu m$ to $ \pm 50 \mu m$).
- Lapping/Polishing: For very flat and smooth surfaces, lapping and polishing can achieve dimensional tolerances down to a few microns ($ \mu m$) and flatness tolerances even better.
- Impact on Cost: Tighter tolerances invariably lead to higher manufacturing costs due to increased processing time, specialized equipment, and potentially lower yields. It’s essential to specify tolerances that are genuinely required for the application’s performance rather than over-specifying.
Surface Finish: The surface finish, often quantified by parameters like average roughness (Ra), directly impacts the thermal contact resistance when two solid surfaces are brought together. Air gaps present in rougher surfaces act as insulators, impeding heat flow.
- As-Sintered/As-Fired Surface: These surfaces will be relatively rough, with Ra values typically in the range of 1μm to 10μm or more, depending on the grain size and process.
- Ground Surfaces: Grinding can significantly improve the surface finish, typically achieving Ra values between 0.2μm and 0.8μm. This is often sufficient for many thermal interface applications, especially when used with a good thermal interface material (TIM).
- Lapped and Polished Surfaces: For the most demanding applications requiring minimal thermal interface resistance, such as direct die attachment or optical applications, lapping and polishing can achieve exceptionally smooth surfaces with Ra values below 0.05μm (50 nanometers), and even down to a few nanometers for super-polished finishes.
- Impact on Thermal Transfer: A smoother surface finish reduces the microscopic air gaps at an interface, leading to better solid-to-solid contact and lower thermal contact resistance. This allows for more efficient heat transfer between the SiC component and the adjacent material (e.g., a power device, a heat pipe, or another part of the heat sink assembly). When high-performance TIMs are used, they can help fill these microscopic voids, but a better initial surface finish will always yield superior results.
Dimensional Accuracy: Beyond tolerances on individual dimensions, overall dimensional accuracy, including flatness, parallelism, and perpendicularity, is critical for ensuring proper assembly and uniform contact pressure across thermal interfaces.
- Flatness: For heat sinks and substrates, flatness is paramount. Deviations from perfect flatness can create significant gaps, increasing thermal resistance. Lapping can achieve flatness values well below 1μm over considerable areas.
- Parallelism: Important for components that need to be assembled in stacks or have parallel mating surfaces.
The table below illustrates typical achievable surface finishes and their implications:
Finishing Process | Typical Ra Range (μm) | Typical Tolerances Achievable | Impact on Thermal Interface Resistance | Relative Cost |
---|---|---|---|---|
As-Sintered/Fired | 1.0 – 10.0+ | ±0.5% to ±2% | High (significant air gaps) | Low |
Grinding | 0.2 – 0.8 | ±0.01 to ±0.05 mm | Moderate (improved contact) | Medium |
Lapping | 0.05 – 0.2 | Down to few μm | Low (good solid contact) | High |
Polishing | < 0.05 | Down to few μm / sub- μm | Very Low (excellent contact) | Very High |
CAS new materials (SicSino), leveraging the advanced manufacturing capabilities within Weifang City and our own top-tier professional team, possesses the integrated process from materials to finished products, including precision machining and finishing technologies. We can advise on the optimal balance between achievable tolerances, surface finish requirements for your specific SiC thermal interface materials application, and overall cost to provide you with higher-quality, cost-competitive customized silicon carbide components. Our expertise ensures that your components meet the precise dimensional and surface specifications needed for maximum thermal efficiency.
Post-Processing and Coating Options for Enhanced SiC Thermal Performance
While the intrinsic properties of silicon carbide and careful design are foundational to effective thermal management, post-processing treatments and specialized coatings can further enhance performance, durability, and functionality of custom SiC components. These steps are often crucial for optimizing SiC parts for specific operating environments or enabling their integration with other materials.
Common Post-Processing Steps:
- Precision Grinding and Lapping:
- Purpose: As discussed previously, grinding and lapping are essential for achieving tight dimensional tolerances and smooth surface finishes. For thermal management, this reduces thermal contact resistance at interfaces.
- Benefits: Improved flatness, parallelism, and surface smoothness lead to more intimate contact with mating surfaces, maximizing heat transfer when used with or without Thermal Interface Materials (TIMs).
- Applications: Critical for SiC substrates for power electronics, heat spreaders in direct contact with heat sources, and any application requiring minimal thermal boundary resistance.
- Polishing:
- Purpose: Achieves an even smoother, mirror-like surface finish than lapping.
- Benefits: Further minimizes surface imperfections, which can be critical for applications like direct bonding or when very thin TIMs are used. Can also be important for optical components used in conjunction with thermal management (e.g., laser systems).
- Applications: High-performance semiconductor packaging, advanced optics.
- Edge Chamfering/Radiusing:
- Purpose: To remove sharp edges, which can be prone to chipping in brittle materials like SiC.
- Benefits: Improves handling safety, reduces the risk of crack initiation during assembly or operation due to stress concentrations, and can improve the reliability of coatings applied near edges.
- Applications: Standard practice for most precision SiC components.
- Cleaning:
- Purpose: To remove any contaminants, machining residues, or particulate matter from the SiC surface.
- Benefits: Ensures a clean surface for subsequent processes like coating, bonding, or assembly, which is critical for achieving strong adhesion and optimal interface properties.
- Applications: Essential before any coating or bonding step.
Coating Options for Enhanced Performance:
- Metallization:
- Purpose: Applying a thin metallic layer (e.g., nickel, gold, silver, copper, titanium) onto the SiC surface.
- Methods: Physical Vapor Deposition (PVD) like sputtering, Chemical Vapor Deposition (CVD), or plating techniques.
- Benefits:
- Solderability/Brazing: Enables SiC components to be soldered or brazed to other materials (e.g., copper baseplates, direct bonded copper (DBC) substrates, or metallic Kovar lids), creating robust, hermetic, and thermally conductive joints. This is crucial for creating SiC thermal interface materials and assemblies.
- Improved Electrical Contact: For SiC-based semiconductor devices, metallization provides low-resistance electrical contacts.
- Enhanced Thermal Spreading: Certain metallic layers can further aid in lateral heat spreading.
- Applications: Power electronic modules, hermetic packages, sensors, heat exchangers where tube-to-header joining is required.
- Dielectric Coatings (e.g., Silicon Nitride (Si3N4), Silicon Dioxide (SiO2)):
- Purpose: To provide electrical isolation while maintaining good thermal coupling, or to offer enhanced environmental protection.
- Benefits: Can prevent electrical shorting in high voltage applications, improve corrosion resistance in specific chemical environments, or act as a diffusion barrier.
- Applications: High-voltage power modules, sensors operating in harsh environments.
- Anti-Corrosion/Protective Coatings (e.g., CVD SiC, Diamond-Like Carbon – DLC):
- Purpose: To further enhance the already excellent corrosion resistance of SiC in extremely aggressive environments or to improve wear resistance.
- Benefits: Extends component lifetime in challenging chemical or abrasive conditions. CVD SiC coatings can seal porosity in some SiC grades like RBSiC, improving their chemical resistance.
- Applications: Chemical processing equipment, components exposed to abrasive slurries or high-temperature corrosive gases.
- Emissivity-Enhancing Coatings:
- Purpose: To increase the surface emissivity of SiC components, thereby improving radiative heat transfer.
- Benefits: In high-temperature applications where radiation is a significant mode of heat transfer, a high-emissivity coating can help dissipate heat more effectively.
- Applications: Radiative cooling components in space applications, high-temperature furnace elements.
The selection of appropriate post-processing and coating options depends heavily on the specific application requirements, the grade of SiC used, and the overall system design. CAS new materials (SicSino) offers comprehensive support in this area, drawing upon our wide array of material, process, design, measurement, and evaluation technologies. Our team can advise on the most suitable surface treatments and coatings to optimize your custom SiC products for thermal performance, reliability, and cost-effectiveness, ensuring they meet the rigorous demands of industries such as semiconductors, aerospace, and high-temperature processing.
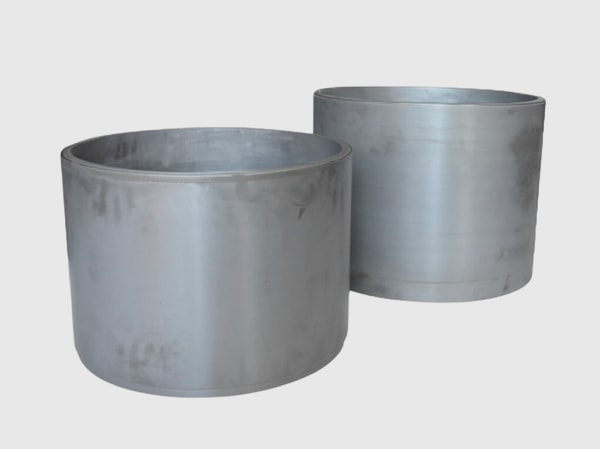
Frequently Asked Questions (FAQ) about SiC in Thermal Management
Engineers, procurement managers, and technical buyers often have specific questions when considering silicon carbide for their thermal management challenges. Here are some common queries with practical, concise answers:
Q1: How does silicon carbide (SiC) compare to traditional thermal management materials like aluminum, copper, or alumina in terms of performance?
A: SiC offers a unique combination of properties that often surpasses traditional materials in demanding applications:
- Vs. Aluminum (Al) & Copper (Cu):
- Thermal Conductivity: High-quality SiC (especially SSiC) can have thermal conductivity comparable to aluminum and in some cases approaching lower grades of copper, but it maintains this conductivity much better at elevated temperatures where Al and Cu soften and their performance degrades.
- Temperature Stability: SiC vastly outperforms Al and Cu at high temperatures (SiC can operate well above 1000∘C; Al is limited to below 200∘C, Cu below 300∘C for structural/thermal integrity).
- CTE Match: SiC has a much lower Coefficient of Thermal Expansion (CTE) than Al or Cu, making it more compatible with semiconductor materials like silicon, reducing thermal stress.
- Mechanical Properties: SiC is significantly harder, stiffer, and more wear-resistant.
- Weight: SiC is lighter than copper.
- Cost: Generally, SiC components are more expensive than bulk Al or Cu parts due to raw material and processing costs, but their superior performance and longevity in harsh conditions can lead to lower total cost of ownership.
- Vs. Alumina (Al2O3):
- Thermal Conductivity: SiC has significantly higher thermal conductivity (SiC: 120-270+ W/mK; Alumina: 20-30 W/mK). This is a key differentiator for heat dissipation.
- Mechanical Strength: Both are hard ceramics, but SiC generally offers better strength and thermal shock resistance.
- Cost: Alumina is typically less expensive than SiC.
- Applications: Alumina is widely used as an electrical insulator and for its good wear resistance, but for applications requiring high thermal conductivity, SiC is far superior.
In summary, SiC is chosen when high thermal conductivity is needed in conjunction with high-temperature capability, good CTE matching to semiconductors, excellent mechanical properties, or chemical inertness – a combination that metals and other ceramics often cannot provide.
Q2: What are the typical operating temperature ranges where silicon carbide excels for thermal management solutions?
A: Silicon carbide excels across a very broad range of temperatures, but its advantages become particularly pronounced in applications involving:
- Moderately High Temperatures (200∘C to 600∘C): In this range, traditional metals like aluminum and copper begin to lose their efficiency or mechanical integrity, or their CTE mismatch with semiconductors becomes problematic. SiC maintains excellent thermal conductivity and stability. This is common in power electronics, automotive applications, and some industrial processes.
- High Temperatures (600∘C to 1400∘C): This is where SiC truly shines. Reaction-Bonded SiC (RBSiC/SiSiC) can operate up to around 1350−1400∘C. Many industrial furnaces, heat treatment processes, and advanced energy systems operate in this range.
- Very High Temperatures (Above 1400∘C): Sintered Silicon Carbide (SSiC) can perform reliably at temperatures up to 1600∘C or even 1700∘C (and higher for short durations or in specific atmospheres). Applications include advanced kiln furniture, components for gas turbines, and research equipment.
Even at lower temperatures, SiC’s high thermal conductivity combined with other properties like electrical resistivity or stiffness can make it the material of choice. However, its high-temperature capabilities are a primary driver for its adoption in many thermal management systems.
Q3: Can CAS new materials (SicSino) assist with the design, material selection, and prototyping of custom SiC thermal solutions?
A: Absolutely. CAS new materials (SicSino) specializes in providing comprehensive support for custom silicon carbide products, from initial concept through to full-scale production. Here’s how we can assist:
- Material Selection: Leveraging our deep knowledge of various SiC grades (RBSiC, SSiC, etc.) and their specific properties, we guide you in selecting the optimal material that balances thermal performance, mechanical requirements, chemical resistance, and cost for your application. Our location in Weifang City, the hub of China’s SiC industry, and our ties to the Chinese Academy of Sciences (CAS) give us access to a wide array of material options and cutting-edge knowledge.
- Design Consultation & Optimization: Our domestic top-tier professional team, specializing in customized SiC production, can work with your engineering team to optimize component designs for manufacturability (DFM) and thermal efficiency. We can advise on geometry, tolerances, surface finishes, and integration strategies.
- Prototyping: We facilitate rapid prototyping to allow for testing and validation of your SiC thermal solutions. This iterative process helps refine designs and ensure they meet performance targets before committing to large-scale production.
- Custom Manufacturing: With our integrated process from materials to products, including advanced shaping, sintering, and precision machining capabilities, we can manufacture complex and high-precision custom SiC components tailored to your exact specifications.
- Technology Transfer & Turnkey Solutions: Beyond component supply, if you need to establish your own professional silicon carbide products manufacturing plant, CAS new materials (SicSino) can provide technology transfer for SiC production, along with full-range turnkey project services. This includes factory design, specialized equipment procurement, installation, commissioning, and trial production.
Our commitment is to provide you with not just components, but complete and effective advanced ceramic solutions for your thermal management challenges, ensuring higher quality, cost-competitiveness, and reliable supply.
This FAQ section aims to address initial key questions. For more detailed discussions regarding your specific project, we encourage you to reach out to our technical team at CAS new materials (SicSino).
Conclusion: The Unmatched Value of Custom Silicon Carbide in Demanding Thermal Environments
In the relentless pursuit of higher efficiency, power density, and operational reliability across industries ranging from semiconductors and power electronics to aerospace and high-temperature manufacturing, effective thermal management stands as a cornerstone of success. As we’ve explored, custom silicon carbide offers a compelling suite of properties – superior thermal conductivity, exceptional high-temperature stability, low thermal expansion, outstanding mechanical strength, and excellent chemical inertness – making it an indispensable material for tackling the most demanding thermal challenges.
The ability to tailor SiC components to specific application needs, from intricate heat sink geometries to precisely finished substrates, elevates its value proposition significantly. Generic solutions fall short where custom SiC manufacturing allows for optimized designs that maximize heat dissipation, enhance system longevity, and ultimately contribute to superior product performance and reliability. Whether it’s advanced ceramic heat sinks, robust industrial SiC components, or precision SiC parts for sensitive electronics, customization unlocks the full potential of this remarkable material.
Choosing the right supplier is paramount to harnessing these benefits. CAS new materials (SicSino), strategically positioned in Weifang City, the epicenter of China’s silicon carbide production, and backed by the formidable scientific and technological capabilities of the Chinese Academy of Sciences (CAS), is more than just a component provider. We are your partners in innovation. Our deep expertise in SiC materials science, custom design, advanced manufacturing processes, and quality assurance ensures that you receive higher-quality, cost-competitive customized silicon carbide components. Furthermore, our unique capability to offer technology transfer and turnkey plant solutions underscores our commitment to advancing the global SiC industry.
For engineers seeking to push performance boundaries, procurement managers sourcing reliable high-performance materials, and OEMs aiming to build next-generation systems, custom silicon carbide from a trusted partner like CAS new materials (SicSino) offers a pathway to achieve your objectives. We invite you to engage with our team to discuss how our custom silicon carbide products and comprehensive support can provide the optimal thermal management solution for your demanding industrial applications, ensuring you stay ahead in a competitive landscape.
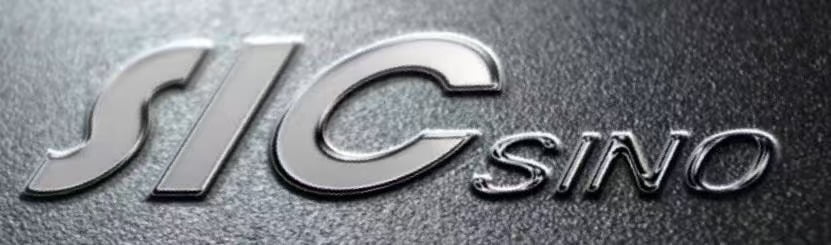
SicSino – CAS new materials
We, CAS new materials(SicSino), have been introducing and implementing silicon carbide production technology since the 2015, assisting the local enterprises in achieving large-scale production and technological advancements in product processes. We have been a witness to the emergence and ongoing development of the local silicon carbide industry.
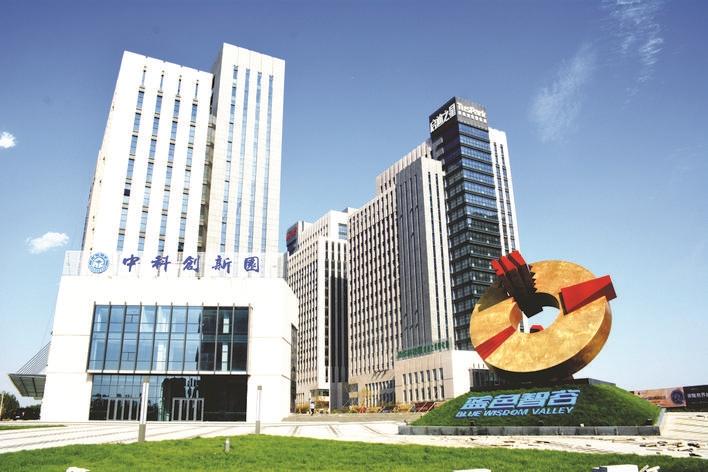