Silicon Carbide (SiC) for the Nuclear Industry: Powering the Next Generation of Nuclear Technology
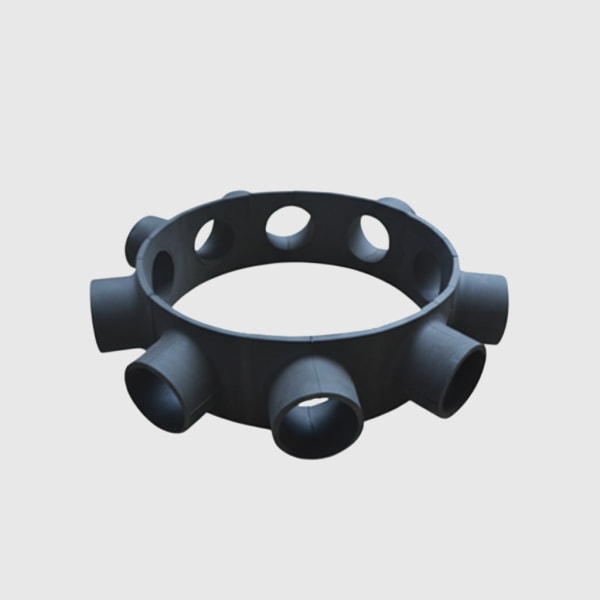
Share
The nuclear industry stands at the cusp of a new era, driven by the urgent need for clean, reliable, and inherently safe energy solutions. As reactor designs evolve towards higher efficiencies, enhanced safety margins, and extended operational lifetimes, the demand for materials capable of withstanding extreme environments has never been more critical. Among the frontrunners in this materials revolution is silicon carbide (SiC), a high-performance technical ceramic offering a unique combination of properties that make it exceptionally well-suited for the demanding conditions within a nuclear reactor. Custom silicon carbide components are rapidly becoming indispensable for a wide array of nuclear applications, promising to unlock new levels of performance and safety. This blog post will delve into the world of custom SiC for the nuclear industry, exploring its applications, advantages, material considerations, and the critical factors in sourcing these advanced ceramics.
At the heart of China’s burgeoning silicon carbide manufacturing capabilities is Weifang City, a region accounting for over 80% of the nation’s total SiC output. CAS new materials (SicSino) has been a pivotal force in this development since 2015, introducing advanced SiC production technology and fostering large-scale production and technological innovation among local enterprises. As part of the CAS (Weifang) Innovation Park and backed by the formidable scientific and technological prowess of the Chinese Academy of Sciences (CAS) through its National Technology Transfer Center, SicSino is more than just a supplier; we are an innovation partner, committed to delivering superior quality and cost-effective custom silicon carbide solutions.
Introduction: The Indispensable Role of Custom Silicon Carbide in Advancing Nuclear Technology
Silicon carbide is a ceramic compound of silicon and carbon (SiC) renowned for its exceptional hardness, high thermal conductivity, excellent resistance to wear and corrosion, and remarkable stability at extreme temperatures and under intense radiation. Unlike traditional metallic materials used in nuclear reactors, such as Zirconium alloys or stainless steels, SiC maintains its structural integrity and desirable properties under conditions that would cause metals to degrade, corrode, or even melt.
The essence of “custom” silicon carbide products lies in the ability to tailor these components to the highly specific and often unique requirements of advanced nuclear reactor designs. This includes fabricating complex geometries, achieving precise material compositions, and ensuring microstructural characteristics optimized for specific operational demands. In an industry where safety and reliability are paramount, the ability to customize components translates directly into enhanced performance, extended component life, and improved overall reactor safety. The move towards Generation IV reactors, small modular reactors (SMRs), and fusion concepts further amplifies the need for materials like SiC that push the boundaries of performance. Custom SiC fabrication for nuclear applications is therefore not just a manufacturing capability but a critical enabler of future nuclear technologies.
Pioneering Applications: Custom SiC in Next-Generation Nuclear Systems
The versatility and exceptional properties of silicon carbide have paved the way for its use in a multitude of critical nuclear applications, both in existing reactors and, more significantly, in advanced reactor designs. Procurement managers and engineers in the nuclear sector are increasingly specifying advanced ceramic materials for nuclear reactors, with SiC at the forefront.
Key applications include:
- Accident Tolerant Fuel (ATF) Cladding: This is arguably one of the most impactful applications. SiC and SiC-matrix composites (CMCs) are leading candidates to replace traditional Zircaloy cladding. SiC offers significantly higher oxidation resistance in steam environments, reducing the risk of hydrogen generation during loss-of-coolant accidents (LOCA). This enhances reactor safety by providing more coping time and reducing the severity of accident scenarios. Custom SiC fuel cladding can be designed for optimal neutron economy and fission product retention.
- Reactor Core Structural Components: SiC’s high strength at elevated temperatures and radiation stability make it suitable for various in-core structures. These include support grids, control rod guide tubes, neutron reflectors, and core barrel components. SiC nuclear components in these roles contribute to core stability, improved neutron efficiency, and longer operational cycles.
- Heat Exchangers and Recuperators: In high-temperature gas-cooled reactors (HTGRs) and molten salt reactors (MSRs), SiC’s excellent thermal conductivity, high-temperature strength, and corrosion resistance are invaluable for compact and efficient heat exchangers. Custom-designed SiC tubes and plates can handle aggressive coolants and high thermal fluxes.
- Control Rods and Shutdown Systems: The ability of SiC to withstand high temperatures and radiation without significant degradation makes it a candidate material for control rod elements or their protective sleeves, ensuring reliable reactor control and shutdown capabilities.
- Plasma Facing Components in Fusion Reactors: For future fusion energy systems, SiC and particularly SiC-SiC composites for nuclear applications are being explored for first wall and blanket structures due to their low activation characteristics, high-temperature capability, and resistance to plasma-induced erosion and neutron bombardment.
- Nuclear Waste Immobilization and Storage: The chemical durability and radiation resistance of SiC make it a promising material for matrices to immobilize high-level nuclear waste, ensuring long-term stability and containment. Custom SiC canisters could offer enhanced safety for spent fuel storage and geological disposal.
- Instrumentation and Sensors: SiC-based sensors can operate reliably in the harsh temperature and radiation environments within a reactor core, providing critical data for monitoring and control where traditional sensors would fail.
The development and deployment of these applications rely heavily on the ability to produce custom silicon carbide components nuclear grade, meeting stringent quality and performance criteria. SicSino, with its deep understanding of SiC materials and processing, coupled with its robust R&D background via the Chinese Academy of Sciences, is well-positioned to support these pioneering efforts.
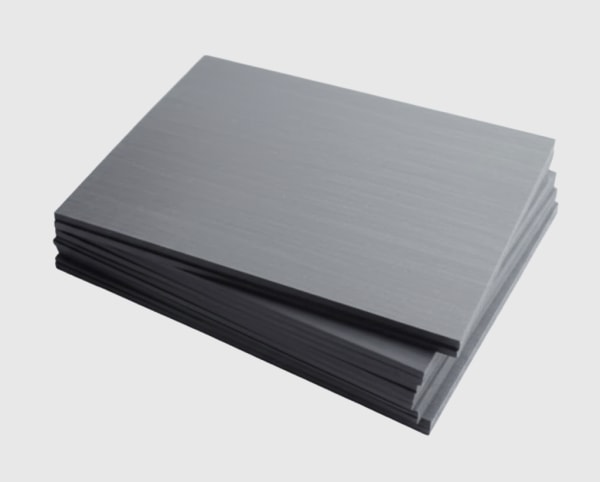
The Custom Advantage: Why Tailored Silicon Carbide Excels in Nuclear Environments
Choosing custom silicon carbide for nuclear applications isn’t just about leveraging a superior material; it’s about harnessing the full potential of that material through tailored design and manufacturing. The unique operating conditions of nuclear reactors – intense radiation fields, high temperatures, corrosive coolants, and demanding mechanical stresses – necessitate components that are precisely engineered for their specific roles.
The key benefits of using custom SiC fabrication nuclear components include:
- Superior Radiation Resistance: SiC exhibits remarkable stability under neutron and gamma irradiation. It maintains its dimensional stability and mechanical properties to much higher doses than most metals. This leads to longer component lifetimes and reduced material swelling or embrittlement, critical for radiation-hardened SiC parts. Its low neutron absorption cross-section also contributes to better neutron economy in the reactor core.
- Exceptional High-Temperature Performance: Many advanced reactor concepts operate at significantly higher temperatures than current light-water reactors to achieve greater thermal efficiency. High-temperature SiC ceramics retain their strength and creep resistance at temperatures exceeding 1600∘C, where conventional alloys would fail. This allows for higher operating temperatures, improving energy conversion efficiency and overall plant economics.
- Outstanding Chemical Inertness and Corrosion Resistance: SiC is highly resistant to oxidation and corrosion by various coolants, including water/steam (crucial for ATF), helium, liquid metals (like sodium or lead), and molten fluoride or chloride salts. This corrosion-resistant ceramics nuclear property prevents degradation of components and reduces the release of corrosion products into the coolant, minimizing system contamination and maintenance.
- Enhanced Safety Margins: The combination of high-temperature stability, oxidation resistance (especially in steam), and radiation tolerance provides significantly wider safety margins during normal operation and, crucially, under accident conditions. For instance, SiC fuel cladding can withstand much higher temperatures before failure compared to Zircaloy, greatly reducing the risk of core damage.
- Wear and Abrasion Resistance: For components subjected to fluid flow or mechanical interaction, SiC’s inherent hardness provides excellent wear resistance, leading to longer operational life and reduced particulate generation.
- Design Flexibility for Optimized Performance: Customization allows engineers to design SiC components with complex geometries optimized for specific functions, such as enhanced heat transfer surfaces or intricate flow channels. This can lead to more compact and efficient reactor systems.
Below is a comparison highlighting some advantages of SiC over traditional Zircaloy for fuel cladding:
Property | Silicon Carbide (SiC) | Zircaloy | Implication for Nuclear Applications (SiC Advantage) |
---|---|---|---|
Max Operating Temp. | > 1600∘C (retains strength) | ~350∘C (LWRs); Rapid degradation > 800∘C | Higher efficiency in advanced reactors; Significantly increased accident tolerance. |
Steam Oxidation | Very slow, protective SiO2 layer | Rapid at high temp. (> 800∘C), H$_2$ generation | Drastically reduced hydrogen production during LOCA, mitigating explosion risk; Preserves cladding integrity longer. |
Radiation Stability | Good dimensional stability, low swelling | Susceptible to irradiation growth, creep, embrittlement | Longer fuel life, predictable behavior under high neutron fluence. |
Chemical Inertness | Excellent in various coolants (He, molten salts) | Reactive with steam at high temperatures | Suitable for diverse advanced reactor coolants; Reduced corrosion product transport. |
Neutron Absorption | Low | Low, but higher than pure SiC | Improved neutron economy. |
Mechanical Properties | High strength, high modulus (brittle without toughening) | Ductile, good strength at operating temp. | Requires composite approach (e.g., SiC-SiC CMC) for toughness, but offers superior high-temp strength. |
This table underscores why technical ceramics for nuclear energy, particularly SiC, are pivotal for next-generation reactor safety and performance. CAS new materials (SicSino) leverages its expertise to provide custom SiC solutions that embody these advantages, supporting OEMs and technical procurement professionals in achieving their demanding performance targets.
Selecting the Shield: Recommended SiC Grades and Composites for Nuclear Integrity
Not all silicon carbide is created equal, especially when destined for the rigors of a nuclear environment. The manufacturing process and resulting microstructure significantly influence the material’s properties. Selecting the appropriate SiC grade or composite is crucial for ensuring the integrity and longevity of nuclear components. Procurement managers and OEM SiC parts nuclear specifiers must work closely with knowledgeable suppliers.
Common and emerging SiC grades relevant to nuclear applications include:
- Chemical Vapor Deposited Silicon Carbide (CVD-SiC):
- Description: Produced by chemical reactions of gaseous precursors at high temperatures, resulting in an ultra-high purity (>99.9995%) and theoretically dense SiC layer.
- Key Properties: Exceptional purity, high thermal conductivity, excellent corrosion and oxidation resistance, good radiation stability, very smooth surface finish possible.
- Nuclear Applications: Often used as coatings on SiC fibers in CMCs, as protective layers on other materials, or for monolithic components where extreme purity and chemical resistance are paramount (e.g., TRISO fuel particle coatings, certain sensor components).
- Sintered Silicon Carbide (S-SiC):
- Description: Made by sintering fine SiC powders, often with non-oxide sintering aids (like boron and carbon) at high temperatures (typically >2000∘C). Can be pressureless sintered or pressure-assisted (e.g., hot pressing, HIP).
- Key Properties: High density (typically >98%), good mechanical strength, high hardness, good thermal conductivity, and excellent wear and corrosion resistance.
- Nuclear Applications: Structural components, heat exchanger tubes, seals, bearings, and parts requiring high strength and wear resistance. Its radiation stability is generally good.
- Reaction-Bonded Silicon Carbide (RBSiC or SiSiC – Silicon-Infiltrated SiC):
- Description: Manufactured by infiltrating a porous preform of SiC particles and carbon with molten silicon. The silicon reacts with the carbon to form new SiC, which bonds the original particles. Typically contains 8-15% free silicon.
- Key Properties: Near-net shape capability, good dimensional stability, good thermal conductivity, and moderate strength. Generally more cost-effective than S-SiC or CVD-SiC for complex shapes.
- Nuclear Applications: While the presence of free silicon can be a concern for some very high-radiation or high-temperature applications (due to lower melting point of Si and potential reactions), it can be suitable for components where these extremes are not met, or where cost is a major driver for large, complex parts. Careful evaluation is needed for specific nuclear environments.
- Silicon Carbide Fiber-Reinforced Silicon Carbide Matrix Composites (SiC/SiC CMCs):
- Description: Consist of SiC fibers (e.g., Nicalon™, Tyranno™, Hi-Nicalon™ S) embedded in a SiC matrix. The matrix is often applied via Chemical Vapor Infiltration (CVI), Polymer Impregnation and Pyrolysis (PIP), or other methods like melt infiltration. A crucial element is the fiber-matrix interphase (often pyrolytic carbon or boron nitride) that allows for fiber pull-out, providing toughness.
- Key Properties: Significantly enhanced fracture toughness (“graceful failure” rather than brittle fracture), pseudo-ductility, excellent high-temperature strength retention, good thermal shock resistance, and radiation stability comparable to monolithic SiC.
- Nuclear Applications: This is a game-changing material for safety-critical components such as SiC fuel cladding, channel boxes, flow shrouds, and structural elements in both fission and fusion reactors. The ability to withstand thermal and mechanical shocks without catastrophic failure is a major advantage. SiC-SiC composites nuclear applications are a key area of R&D and deployment.
Table: Key Properties of Nuclear-Relevant SiC Grades
Material Type | Density (g/cm³) | Flexural Strength (MPa, RT) | Max Use Temp. (°C) | Thermal Conductivity (W/mK, RT) | Fracture Toughness (MPa·m½) | Relative Cost | Radiation Stability |
---|---|---|---|---|---|---|---|
CVD-SiC | ~3.21 | 400-600 | 1600+ | 150-300 | 3-4 | High | Excellent |
Sintered SiC (S-SiC) | >3.10 | 450-650 | 1600+ | 80-150 | 4-6 | Med-High | Good |
Reaction-Bonded (RBSiC) | ~3.05-3.15 | 250-400 | 1350-1380 | 100-150 | 3-5 | Med | Fair-Good |
SiC/SiC CMC | ~2.5-3.0 | 200-400 (tensile) | 1600+ | 15-60 | 10-25 | Very High | Excellent |
Note: Properties can vary significantly based on specific composition, microstructure, and manufacturing process.
CAS new materials (SicSino), leveraging its location in Weifang – the hub of China’s silicon carbide customizable parts factories – and its strong ties with the Chinese Academy of Sciences, possesses a domestic top-tier professional team specializing in the customized production of a wide array of SiC products. We offer expertise in material selection, helping clients choose the optimal SiC grade or composite, including S-SiC and RBSiC, to meet diverse customization needs for demanding nuclear applications. Our focus is on delivering higher-quality, cost-competitive customized silicon carbide components in China.
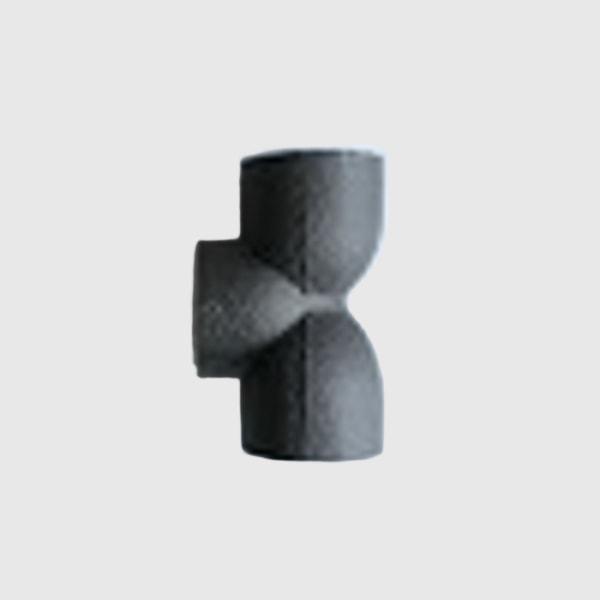
Blueprint for Resilience: Critical Design Considerations for SiC Nuclear Components
Designing components with advanced ceramics like silicon carbide requires a different mindset than designing with ductile metals. SiC’s inherent brittleness (in its monolithic form) and its specific manufacturing constraints must be considered from the outset to ensure robust, reliable, and manufacturable parts. Engineers specializing in custom SiC components nuclear design must account for the unique behavior of these materials under operational stresses.
Key design considerations include:
- Designing for Manufacturability (DfM):
- Geometric Complexity: While SiC can be formed into complex shapes, intricate features, sharp internal corners, and sudden changes in cross-section can create stress concentrations and manufacturing challenges. Generous radii and fillets are recommended.
- Wall Thickness: Minimum and maximum wall thicknesses are process-dependent. Thin walls can be fragile, while overly thick sections can lead to issues during sintering or infiltration (e.g., uniform density, internal stresses).
- Aspect Ratios: Very high aspect ratios (length to diameter/width) can be difficult to manufacture and handle.
- Draft Angles: For processes involving molds (e.g., some types of green forming before sintering), draft angles may be necessary.
- Managing Brittleness:
- Stress Concentrations: Avoid notches, sharp edges, and point loads that can act as crack initiators. Distribute loads over larger areas.
- Tensile Stresses: SiC is much stronger in compression than in tension. Designs should aim to keep SiC components under compressive loads where possible.
- Component Mounting and Interfaces: Design mounting fixtures and interfaces to accommodate thermal expansion differences with mating metallic parts and to avoid inducing localized stresses. Compliant layers or carefully designed mechanical attachments may be needed.
- Joining of SiC Components:
- For large or highly complex structures, joining SiC to SiC or SiC to other materials (like metals) may be necessary. Specialized joining techniques (e.g., diffusion bonding, brazing with active filler metals, reaction forming joints, mechanical fastening) are required. These joints must also withstand the nuclear environment. The hermeticity and strength of such joints are critical for applications like fuel cladding.
- Thermal Management:
- SiC has high thermal conductivity, which is often an advantage. However, thermal gradients can induce stresses. Designs should consider thermal expansion and thermal shock resistance.
- For SiC/SiC CMCs, the anisotropic nature of thermal conductivity (different along fiber directions vs. through-thickness) must be accounted for in thermal analyses.
- Modeling and Simulation:
- Finite Element Analysis (FEA) is crucial for predicting stress distributions, temperature profiles, and deformation under operational loads, including thermal, mechanical, and irradiation-induced effects. Probabilistic design approaches (e.g., Weibull statistics) are often used to account for the statistical nature of ceramic strength.
- Integration with System Design:
- The SiC component must be designed as an integral part of the larger nuclear system. Interactions with coolants, surrounding structures, and the overall neutronics of the reactor core must be considered.
Engineering Tips for SiC Component Design:
- Simplify geometry wherever possible without compromising function.
- Use generous radii on all internal and external corners.
- Aim for uniform wall thicknesses to minimize stress during processing and operation.
- Design features that can be net-shape formed or require minimal post-sinter machining.
- Consider modular designs that utilize smaller, easier-to-manufacture SiC components joined together.
- Consult with experienced silicon carbide manufacturers nuclear grade like SicSino early in the design process. Our team, backed by the robust scientific and technological capabilities of the CAS National Technology Transfer Center, can provide invaluable input on design for manufacturability and material optimization.
CAS new materials (SicSino) offers comprehensive customizing support, including material, process, and design technologies. Our integrated process from materials to products enables us to meet diverse customization needs effectively.
Precision Under Pressure: Tolerance, Surface Finish, and Dimensional Control for Nuclear-Grade SiC
In the nuclear industry, precision is not just a goal; it’s a fundamental requirement for safety and performance. Custom silicon carbide components nuclear applications demand exceptionally tight dimensional tolerances, specific surface finishes, and rigorous quality control to ensure they fit correctly, function as intended, and maintain their integrity over long operational periods.
- Achievable Tolerances:
- The achievable tolerances for SiC components depend on the manufacturing method (e.g., sintering, reaction bonding, CVD) and the extent of post-processing (e.g., grinding, lapping).
- As-sintered or as-reacted parts: Tolerances are generally looser, often in the range of ±0.5% to ±1% of the dimension, or even wider for very large or complex parts. However, near-net-shape processing aims to minimize machining.
- Machined (Ground/Lapped) parts: For critical dimensions, SiC can be diamond ground, lapped, and polished to very tight tolerances, often in the range of ±0.005 mm to ±0.025 mm ($ \pm 5 \text{ } \mu\text{m}$ to ±25 μm), or even tighter for specialized applications.
- Achieving such precision on hard ceramics like SiC requires specialized equipment and expertise, contributing to the component’s cost.
- Surface Finish:
- The surface finish (roughness, Ra) of SiC components is critical for various reasons:
- Fluid Dynamics: Smooth surfaces are often required in flow channels to minimize pressure drop and prevent turbulence (e.g., fuel cladding, heat exchanger tubes).
- Wear Resistance: Smoother surfaces generally exhibit lower friction and wear rates in sliding contact applications.
- Hermeticity: For sealing applications, a very smooth surface is essential.
- Corrosion Resistance: A smoother surface can sometimes offer better corrosion resistance by reducing sites for corrosive attack.
- Joining: Surface preparation is critical for achieving strong and reliable joints.
- Typical achievable surface finishes:
- As-fired/sintered: Ra can range from 1 μm to 10 μm or more, depending on the process and green forming technique. CVD-SiC can achieve very smooth as-deposited surfaces (e.g., Ra < 1 μm).
- Ground: Ra 0.2 μm to 0.8 μm is common.
- Lapped/Polished: Ra < 0.1 μm can be achieved, with optical-quality finishes possible for specific applications.
- The surface finish (roughness, Ra) of SiC components is critical for various reasons:
- Dimensional Control and Inspection:
- Rigorous dimensional inspection is mandatory for nuclear-grade components. This involves:
- Contact Metrology: Coordinate Measuring Machines (CMMs) with touch probes.
- Non-Contact Metrology: Laser scanners, optical profilometers, white light interferometry for surface roughness and form.
- Specialized Gauging: Custom gauges for specific features.
- Statistical Process Control (SPC) should be implemented throughout the manufacturing process to ensure consistency and identify potential deviations early.
- Traceability of materials and processing parameters is essential.
- Rigorous dimensional inspection is mandatory for nuclear-grade components. This involves:
CAS new materials (SicSino) understands the critical importance of precision. We possess advanced measurement and evaluation technologies as part of our comprehensive service ecosystem. This allows us to ensure that the customized silicon carbide components we deliver from Weifang meet the stringent dimensional and surface finish requirements of our clients in the nuclear and other high-tech industries. Our commitment to quality is backed by the expertise derived from the Chinese Academy of Sciences, ensuring reliable and consistent production.
Beyond Fabrication: Post-Processing, Qualification, and Overcoming Challenges with SiC in Nuclear Applications
Manufacturing a silicon carbide component to the correct shape and dimension is only part of the journey, especially for demanding nuclear applications. Post-processing steps are often necessary to achieve the final required properties and surface conditions. Furthermore, rigorous qualification is essential to demonstrate that the component will perform reliably and safely in the intended nuclear environment. Despite its many advantages, SiC also presents certain challenges that need to be addressed through careful material selection, design, and manufacturing control.
Post-Processing Needs:
- Precision Grinding and Lapping: As SiC is an extremely hard material, diamond tooling is required for any machining operations. Grinding is used to achieve tight dimensional tolerances and improve surface finish after sintering or reaction bonding. Lapping and polishing can further refine the surface to meet very low roughness requirements.
- Cleaning: Thorough cleaning is essential to remove any contaminants from machining or handling before installation or further processing (like coating).
- Edge Chamfering/Radiusing: To mitigate stress concentrations and prevent chipping, sharp edges are often chamfered or radiused.
- Coatings: In some cases, additional coatings might be applied to SiC components. For example, environmental barrier coatings (EBCs) can be used on SiC/SiC CMCs in certain high-temperature, corrosive environments to further enhance durability, or specific coatings might be needed for joining purposes.
- Joining and Assembly: If the final component is an assembly of multiple SiC parts or SiC and metallic parts, specialized joining processes (discussed earlier) are performed as a post-fabrication step.
Qualification for Nuclear Service:
This is a critical and often lengthy process. Wholesale silicon carbide nuclear components must meet the highest standards.
- Non-Destructive Evaluation (NDE): Various NDE techniques are employed to inspect for internal flaws, cracks, porosity, or density variations without damaging the component. These include:
- X-ray Radiography and Computed Tomography (CT)
- Ultrasonic Testing (UT)
- Fluorescent Penetrant Inspection (FPI) for surface-breaking cracks
- Material Characterization: Extensive testing to verify mechanical properties (strength, toughness, hardness, creep), thermal properties (conductivity, expansion), and microstructure.
- Performance Testing under Simulated Conditions: This may involve exposing sample components or coupons to:
- High temperatures and relevant atmospheric/coolant conditions.
- Irradiation testing in research reactors to assess behavior under neutron and gamma flux (swelling, changes in mechanical properties, thermal conductivity degradation).
- Thermal shock testing.
- Corrosion testing in representative coolants.
- Adherence to Nuclear Codes and Standards: Components must often be manufactured and qualified in accordance with established nuclear codes and standards (e.g., ASME, RCC-MRx, or specific utility/regulator requirements). This involves rigorous documentation, quality assurance programs, and often third-party certification.
Common Challenges and How to Overcome Them:
- Brittleness (Monolithic SiC):
- Challenge: Monolithic SiC has low fracture toughness, meaning it can fracture catastrophically if a critical flaw is present and subjected to sufficient stress.
- Mitigation: Use of SiC/SiC CMCs which offer pseudo-ductility; designing for compressive stress states; careful handling; rigorous NDE to eliminate flawed parts; proof testing.
- Machining Complexity and Cost:
- Challenge: SiC’s extreme hardness makes it difficult and expensive to machine.
- Mitigation: Near-net-shape forming techniques to minimize machining; utilizing experienced fabricators with specialized diamond grinding equipment; optimizing designs for easier machining. CAS new materials (SicSino) focuses on cost-competitive solutions by optimizing manufacturing processes.
- Irradiation-Induced Degradation:
- Challenge: While generally radiation-stable, very high neutron fluences can lead to some swelling, a decrease in thermal conductivity, and changes in mechanical properties.
- Mitigation: Selection of high-purity, crystalline SiC grades (like high-quality CVD-SiC or S-SiC); use of SiC/SiC CMCs designed for radiation stability; accounting for these changes in component design and lifetime assessments.
- Joining Reliability:
- Challenge: Creating strong, hermetic, and durable joints between SiC parts or SiC and metals that can withstand nuclear conditions is technically challenging.
- Mitigation: Development and qualification of advanced joining techniques; careful joint design to minimize stress and accommodate thermal expansion mismatches; rigorous NDE of joints.
- Cost and Scalability:
- Challenge: Custom, high-quality SiC components, especially CMCs, can be more expensive than traditional metallic parts. Scaling up production for large reactor fleets is also a consideration.
- Mitigation: Ongoing R&D to reduce manufacturing costs (e.g., more efficient fiber and matrix production for CMCs); standardization of components where possible; strategic partnerships with capable suppliers like SicSino, located in the Weifang SiC hub, which benefits from economies of scale and an established supply chain. SicSino’s technology transfer services also aim to facilitate broader access to SiC manufacturing capabilities.
By understanding these challenges and proactively addressing them through advanced materials science, robust engineering design, and meticulous manufacturing and qualification processes, the full potential of silicon carbide in the nuclear industry can be realized.

Frequently Asked Questions (FAQ)
- Q1: What makes custom silicon carbide a superior choice over traditional materials like Zircaloy for nuclear fuel cladding? A1: Custom silicon carbide, particularly SiC/SiC composites, offers significantly enhanced accident tolerance. It can withstand much higher temperatures (over 1600∘C) without melting or reacting aggressively with steam, which drastically reduces hydrogen production during loss-of-coolant accidents (LOCAs) compared to Zircaloy (which degrades rapidly above 800∘C and produces significant hydrogen). SiC also has excellent radiation stability, corrosion resistance to various coolants, and can lead to improved fuel cycle economics through higher burnup potential.
- Q2: How does the cost of custom SiC components for nuclear applications compare to other options? A2: Initially, custom SiC components, especially advanced forms like SiC/SiC CMCs, can have a higher upfront manufacturing cost than traditional metallic components. However, a true cost assessment should consider the total lifecycle cost. The superior durability, longer component lifetimes, enhanced safety (potentially reducing the need for complex auxiliary safety systems or mitigating accident consequences), and improved thermal efficiency offered by SiC can lead to significant long-term savings and overall economic benefits. CAS new materials (SicSino) strives to provide cost-competitive customized SiC components by leveraging the manufacturing ecosystem in Weifang and optimizing production processes.
- Q3: What is the typical lead time for custom SiC nuclear components from a supplier like CAS new materials (SicSino)? A3: Lead times for custom SiC nuclear components can vary significantly based on several factors, including the complexity of the design, the specific SiC grade required (e.g., monolithic vs. CMC), the quantity ordered, the stringency of qualification requirements, and current production schedules. Simple prototypes might take several weeks, while complex, qualified components could take several months or longer. It’s crucial to discuss specific project timelines directly with SicSino. Our team is committed to efficient project management from inquiry to delivery, supported by our integrated processes.
- Q4: Can CAS new materials (SicSino) assist with the design and material selection for highly specific or novel nuclear requirements? A4: Yes, absolutely. CAS new materials (SicSino) prides itself on its technical expertise, backed by the Chinese Academy of Sciences. We have a domestic top-tier professional team specializing in customized production of silicon carbide products, encompassing material science, process engineering, design optimization, and measurement/evaluation technologies. We work closely with our clients, including OEMs and technical procurement professionals, to understand their unique challenges and help them select or develop the optimal SiC material and component design for their specific nuclear applications. We can offer guidance on manufacturability, performance trade-offs, and material characterization.
- Q5: What are the primary challenges in scaling up SiC component production to meet the demands of future, potentially larger, fleets of advanced nuclear reactors? A5: Key challenges include the current cost of some SiC materials (especially high-purity fibers for CMCs), the complexity and length of some manufacturing processes (like CVI for CMCs), the need for specialized manufacturing equipment, and ensuring a robust supply chain for raw materials and precursor gases. Further R&D is focused on developing more cost-effective and scalable manufacturing techniques. Additionally, standardizing component designs where feasible and fostering global collaboration and technology transfer, such as the services offered by CAS new materials (SicSino) to help establish local SiC production plants, will be crucial for meeting future large-scale demands.
Conclusion: Embracing Custom Silicon Carbide for a Safer and More Efficient Nuclear Future
Custom silicon carbide represents a transformative material technology for the nuclear industry. Its exceptional performance under the extreme conditions of temperature, radiation, and corrosive environments found within nuclear reactors offers pathways to enhanced safety, improved thermal efficiency, extended component lifetimes, and the realization of advanced reactor designs. From accident-tolerant fuel cladding that significantly mitigates accident risks to durable core structures and efficient heat exchangers, custom SiC components are enabling engineers to push the boundaries of nuclear performance.
Choosing the right partner for the design, development, and supply of these critical components is paramount. CAS new materials (SicSino), strategically located in Weifang, the epicenter of China’s silicon carbide production, stands as a testament to innovation and quality in this field. Our deep roots within the Chinese Academy of Sciences provide an unparalleled foundation of scientific and technological expertise. We offer a comprehensive suite of services, from material selection and custom design to high-precision manufacturing and rigorous quality assurance, ensuring that our clients receive SiC components that meet the most demanding nuclear-grade specifications.
Furthermore, SicSino is committed to fostering the growth of the global SiC industry through technology transfer, empowering nations to build their own specialized SiC manufacturing capabilities. As the nuclear industry continues its vital role in providing clean and sustainable energy, custom silicon carbide, supplied by experienced and reliable partners like CAS new materials (SicSino), will be an indispensable element in building a safer, more efficient, and more resilient nuclear future. We invite engineers, procurement managers, and technical buyers to engage with us to explore how our advanced SiC solutions can meet your most demanding industrial challenges.
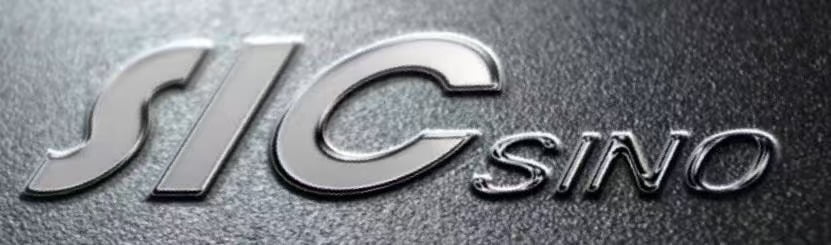
SicSino – CAS new materials
We, CAS new materials(SicSino), have been introducing and implementing silicon carbide production technology since the 2015, assisting the local enterprises in achieving large-scale production and technological advancements in product processes. We have been a witness to the emergence and ongoing development of the local silicon carbide industry.
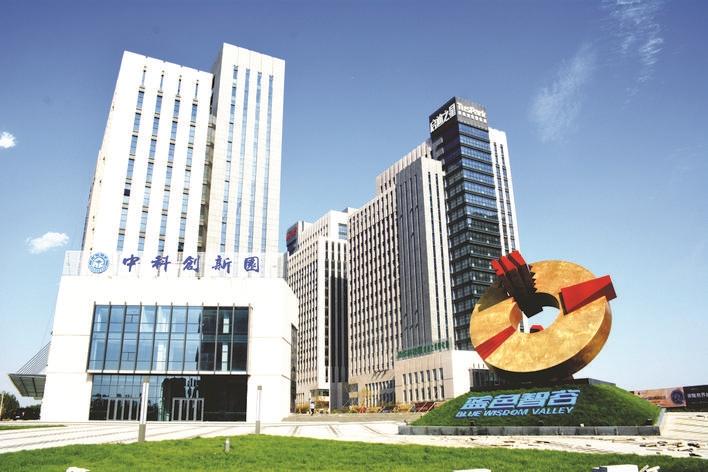