Silicon Carbide for Bearings: The Superior Choice for Demanding Industrial Applications
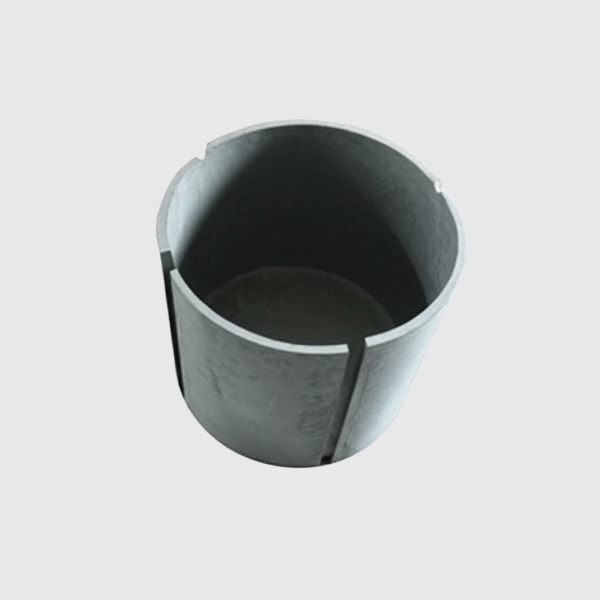
Share
In the realm of high-performance industrial applications, the choice of materials is paramount to ensuring longevity, efficiency, and reliability. Traditional bearing materials often fall short when faced with extreme temperatures, corrosive environments, high loads, and demanding wear conditions. This is where custom silicon carbide (SiC) bearings emerge as a transformative solution. Silicon carbide, a robust technical ceramic, offers an exceptional combination of properties that make it an ideal candidate for bearings operating in the toughest industrial settings. From semiconductor manufacturing to aerospace and chemical processing, SiC bearings are revolutionizing how engineers approach challenges related to friction, wear, and operational lifespan.
At CAS new materials (SicSino), we leverage our deep expertise in silicon carbide technology to provide bespoke SiC bearing solutions tailored to the unique requirements of our B2B clients, including wholesale buyers, technical procurement professionals, OEMs, and distributors. Situated in Weifang City, the heart of China’s silicon carbide manufacturing industry, which accounts for over 80% of the nation’s total SiC output, SicSino has been instrumental in advancing SiC production technology since 2015. Our affiliation with the CAS (Weifang) Innovation Park, a national-level innovation and entrepreneurship service platform backed by the Chinese Academy of Sciences (CAS), underscores our commitment to quality, innovation, and technological excellence. We empower industries by delivering higher-quality, cost-competitive custom silicon carbide components, backed by a domestic top-tier professional team and a comprehensive understanding of material science, process engineering, and design.
Key Advantages of Silicon Carbide Bearings
The decision to specify silicon carbide bearings for critical applications is driven by a host of compelling advantages over conventional materials like steel or even other ceramics. These benefits translate directly into improved performance, reduced downtime, and lower total cost of ownership in numerous industrial scenarios.
- Exceptional Hardness and Wear Resistance: Silicon carbide is one of the hardest commercially available materials, second only to diamond. This extreme hardness translates into outstanding wear resistance, meaning SiC bearings can withstand abrasive particles and high contact stresses without significant material loss. This leads to significantly longer service life, especially in applications with particulate contamination or insufficient lubrication.
- High-Temperature Stability: Unlike metallic bearings that soften and lose their mechanical properties at elevated temperatures, SiC bearings maintain their strength, hardness, and dimensional stability up to very high temperatures (often exceeding 1400∘C for certain grades). This makes them indispensable for applications like high-temperature furnaces, gas turbines, and exhaust systems.
- Superior Corrosion Resistance: SiC exhibits exceptional chemical inertness, resisting attack from a wide range of corrosive media, including strong acids, alkalis, and oxidizing agents. This makes industrial SiC bearings ideal for use in chemical pumps, mixers, and other equipment handling aggressive fluids where metallic bearings would quickly degrade.
- Low Coefficient of Friction: Silicon carbide can achieve a very low coefficient of friction, especially when paired with suitable lubricants or even in dry-running conditions for some designs. This reduces energy consumption, heat generation, and wear, further enhancing operational efficiency and bearing life.
- High Stiffness and Compressive Strength: The high elastic modulus (stiffness) of SiC ensures minimal deformation under load, leading to precise operation and consistent performance. Its excellent compressive strength allows SiC bearings to handle heavy loads without failure.
- Lower Density: Compared to steel, SiC is significantly lighter. This lower density reduces centrifugal forces in high-speed applications, allowing for higher operational speeds and reducing stress on associated components.
- Electrical Resistivity/Conductivity Options: Depending on the grade and manufacturing process, SiC can be an excellent electrical insulator or a semiconductor. This property is crucial in applications where electrical arcing or current flow through the bearing needs to be prevented or managed, such as in electric motors or generators.
- Good Thermal Shock Resistance: While ceramics are often perceived as brittle, certain grades of SiC offer good thermal shock resistance, allowing them to withstand rapid temperature changes without cracking.
These inherent material advantages make high-performance ceramic bearings made from silicon carbide a preferred choice for industries seeking to push the boundaries of operational capability and reliability. CAS new materials (SicSino) specializes in harnessing these properties to deliver custom SiC bearing solutions that meet the most demanding specifications.
Types of Silicon Carbide Used in Bearings and Their Properties
Not all silicon carbide is created equal. Different manufacturing processes result in various SiC grades with distinct microstructures and property profiles. Understanding these differences is crucial for selecting the optimal material for specific bearing applications. The most common types of SiC used for bearings include Sintered Silicon Carbide (SSC) and Reaction-Bonded Silicon Carbide (RBSC), also known as Silicon-Infiltrated Silicon Carbide (SiSiC).
Sintered Silicon Carbide (SSC) is produced by sintering fine SiC powder at high temperatures (typically above 2000∘C), often with non-oxide sintering aids. This process results in a dense, single-phase SiC material with very high purity.
- Properties: Extremely high hardness, excellent wear resistance, superior corrosion resistance across a wide pH range, high-temperature strength, and good thermal shock resistance. SSC generally offers the best all-around performance for the most demanding bearing applications.
- Best Suited For: Applications requiring maximum wear and corrosion resistance, high temperatures, and high purity environments, such as chemical pumps, semiconductor processing equipment, and high-performance seals.
Reaction-Bonded Silicon Carbide (RBSC or SiSiC) is manufactured by infiltrating a porous compact of SiC grains and carbon with molten silicon. The silicon reacts with the carbon to form new SiC, which bonds the original SiC grains. This process typically leaves some residual free silicon within the microstructure (usually 8-15%).
- Properties: High hardness and good wear resistance (though generally slightly lower than SSC), excellent thermal conductivity, good mechanical strength, and relatively lower manufacturing cost compared to SSC. The presence of free silicon can limit its use in certain highly corrosive environments or at extreme temperatures where the silicon might melt or react.
- Best Suited For: Applications where high thermal conductivity is beneficial, cost is a significant driver, and the operating environment is compatible with free silicon. Examples include bearings and components in pumps handling abrasive slurries, mechanical seals, and some high-temperature structural components.
Here’s a comparative overview:
Property | Sintered Silicon Carbide (SSC) | Reaction-Bonded SiC (RBSC/SiSiC) |
---|---|---|
Typical Density | >3.10 g/cm3 | 3.02−3.10 g/cm3 |
Hardness (Knoop) | 2500−2800 | 2200−2500 |
Flexural Strength | 400−550 MPa | 350−450 MPa |
Max. Use Temperature | 1600−1700∘C | 1350−1380∘C |
Thermal Conductivity | 80−120 W/mK | 100−150 W/mK |
Corrosion Resistance | Excellent | Good (limited by free silicon) |
Purity | Very High | Contains free silicon |
Relative Cost | Higher | Lower |
CAS new materials (SicSino) possesses the expertise to guide clients in selecting the most appropriate SiC grade for their bearing applications. Our understanding of the nuances between SSC, RBSC, and other specialized SiC formulations, combined with our robust manufacturing capabilities, allows us to deliver custom SiC bearing solutions optimized for performance and value. Our presence in Weifang, China’s SiC manufacturing hub, gives us access to a mature supply chain and a skilled workforce, further enhancing our ability to produce high-quality, cost-effective SiC components.
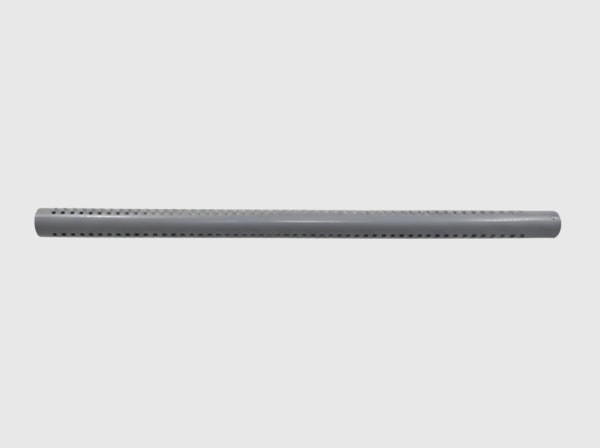
Applications of Silicon Carbide Bearings Across Industries
The exceptional properties of silicon carbide bearings make them indispensable in a wide array of industries where traditional bearings fail or offer suboptimal performance. Their ability to operate reliably under severe conditions translates into enhanced productivity, reduced maintenance, and improved safety.
1. Chemical Processing:
- Applications: Pumps (magnetic drive pumps, canned motor pumps), mixers, agitators, valves, and mechanical seals handling corrosive chemicals, acids, alkalis, and abrasive slurries.
- Benefits: Corrosion-resistant bearings made from SiC prevent chemical attack, extending the life of critical equipment. Their wear resistance is crucial when dealing with slurries containing hard particles. SicSino supplies custom SiC bearing components for leading chemical pump manufacturers.
2. Oil and Gas:
- Applications: Downhole drilling tools, mud motors, pumps for handling abrasive drilling fluids, and components in subsea equipment.
- Benefits: SiC bearings offer superior wear and erosion resistance in harsh downhole environments characterized by high pressures, abrasive media, and corrosive elements. Their reliability is critical for minimizing costly downtime in exploration and production.
3. Semiconductor Manufacturing:
- Applications: Vacuum pumps (turbomolecular pumps, dry pumps), wafer handling robots, chemical mechanical planarization (CMP) equipment, and other precision machinery operating in ultra-clean or aggressive chemical environments.
- Benefits: High purity grades of SiC prevent contamination. Their stiffness and wear resistance ensure precision movement crucial for semiconductor fabrication. Electrical insulation properties can also be vital.
4. Automotive and Electric Vehicles (EVs):
- Applications: Turbocharger bearings, water pump seals, components in high-performance braking systems, and potentially in electric motor bearings for EVs requiring high speed and electrical insulation.
- Benefits: High-temperature capability for turbochargers, wear resistance for water pumps, and lightweight properties for overall efficiency. In EVs, SiC’s electrical properties can prevent bearing damage from stray currents.
5. Aerospace and Defense:
- Applications: Auxiliary power units (APUs), actuators, gimbal systems, rocket engine turbopumps, and other components requiring high reliability in extreme temperatures and high-speed conditions.
- Benefits: Lightweight, high-temperature stability, and excellent stiffness-to-weight ratio are critical for aerospace applications. CAS new materials (SicSino) works with clients to develop specialized SiC components meeting stringent aerospace specifications.
6. Power Generation:
- Applications: Bearings in pumps for boiler feedwater, flue gas desulfurization (FGD) systems, and potentially in high-temperature turbine components.
- Benefits: Resistance to high temperatures, corrosive flue gases, and abrasive fly ash. SiC bearings can improve the reliability of critical power plant equipment.
7. Mining and Mineral Processing:
- Applications: Slurry pumps, hydrocyclones, and other equipment handling highly abrasive ores and minerals.
- Benefits: The extreme wear resistance of industrial SiC bearings significantly extends the operational life of machinery in these challenging environments, reducing maintenance frequency and costs.
8. Food and Pharmaceutical:
- Applications: Bearings in processing equipment where hygiene, corrosion resistance, and non-toxicity are paramount. SiC can be cleaned and sterilized effectively.
- Benefits: Resistance to cleaning agents and process fluids, non-contaminating, and long life.
The versatility of silicon carbide allows for tailored solutions across these diverse sectors. CAS new materials (SicSino), with its foundation in Weifang – a city home to over 40 SiC production enterprises – and its strong backing from the Chinese Academy of Sciences, is uniquely positioned to provide customized SiC bearing components that address the specific challenges of each industry. Our extensive process and design technologies enable us to meet varied customization needs for technical ceramic components.
Design and Manufacturing Considerations for Custom SiC Bearings
Designing and manufacturing custom silicon carbide bearings requires a specialized approach due to the unique properties of this advanced ceramic. Unlike metals, SiC is very hard and brittle, which influences design choices, machining processes, and achievable tolerances. Careful consideration of these factors is essential to harness the full potential of SiC and ensure reliable bearing performance.
Key Design Considerations:
- Load Capacity and Stress Concentration: While SiC has high compressive strength, its tensile strength is lower. Designs must carefully manage stress concentrations, avoiding sharp corners or abrupt changes in cross-section that could lead to fracture. Finite Element Analysis (FEA) is often employed to optimize designs and predict stress distributions.
- Speed Ratings (DN Value): The DN value (bearing bore in mm multiplied by RPM) is a critical parameter. SiC’s low density can allow for higher speeds than steel, but lubrication, heat dissipation, and dynamic stability must be carefully evaluated.
- Operating Environment:
- Temperature: Consider thermal expansion and potential for thermal shock. The design should accommodate differential expansion if SiC is paired with other materials.
- Chemical Exposure: While SiC offers broad corrosion resistance, specific grades perform differently. The choice between SSC and RBSC, for instance, can depend on the chemical environment.
- Lubrication: SiC bearings can run dry, with process fluid lubrication, or with conventional lubricants. The choice of lubrication (or lack thereof) significantly impacts design and performance. For dry running, surface finish and material pairing are critical.
- Precision Requirements:
- Tolerances: Achieving tight dimensional and geometric tolerances with SiC is challenging due to its hardness but is achievable with advanced grinding and lapping techniques. Typical tolerances for precision SiC bearings can be in the micron range.
- Surface Finish: A smooth surface finish (low Ra value) is crucial for minimizing friction and wear, especially in dry-running or marginally lubricated conditions. Polishing and lapping can achieve mirror-like finishes.
- Brittleness and Fracture Toughness: Designs should incorporate features that mitigate the risk of brittle fracture, such as chamfers, radii, and ensuring uniform load distribution. Assembly and handling procedures must also account for brittleness.
- Interference Fits and Mounting: Due to SiC’s high stiffness and low ductility, interference fits must be precisely calculated and controlled to avoid overstressing the ceramic components during assembly. Temperature differences during fitting can also be critical.
Manufacturing Challenges and Solutions:
- Machining: SiC’s extreme hardness makes it difficult and costly to machine using conventional methods. Diamond grinding, lapping, polishing, and Electrical Discharge Machining (EDM) for conductive grades are commonly used.
- Forming Complex Shapes: Near-net-shape forming techniques (e.g., pressing, slip casting, injection molding for green bodies) are preferred to minimize post-sintering machining.
- Joining: Joining SiC to other materials (e.g., metal shafts or housings) requires specialized techniques like brazing, shrink fitting, or adhesive bonding, each with its own design implications.
CAS new materials (SicSino) excels in navigating these design and manufacturing complexities. Our domestic top-tier professional team specializes in the customized production of silicon carbide products. We possess a wide array of technologies, including material, process, design, measurement, and evaluation technologies, along with an integrated process from materials to products. This enables us to meet diverse customization needs for SiC ceramic bearings and other technical ceramic components. We collaborate closely with our clients from the initial design phase, offering DFM (Design for Manufacturability) support to ensure that the final product is not only high-performing but also cost-effective to produce. Our experience, built upon assisting over 10 local enterprises with our technologies in the Weifang SiC hub, ensures reliable quality and supply assurance within China.
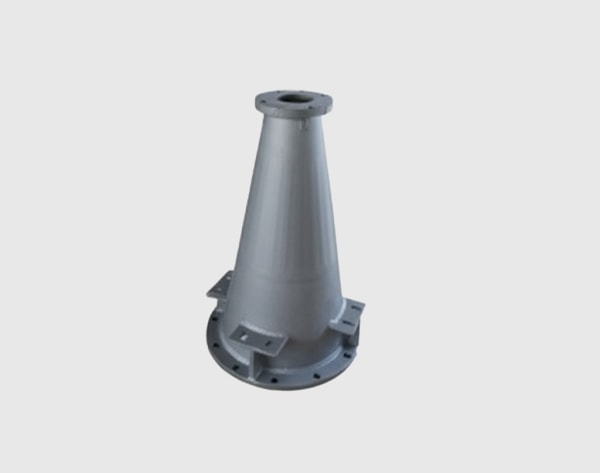
Performance and Durability: Silicon Carbide vs. Traditional Bearing Materials
When selecting bearings for demanding applications, a direct comparison of material performance and durability is essential. Silicon carbide (SiC) bearings offer a distinct set of advantages over traditional materials like bearing steels (e.g., 52100 chrome steel) and even other advanced ceramics like Zirconia (ZrO2) or Silicon Nitride (Si3N4) in specific contexts.
Feature | Bearing Steel (e.g., 52100) | Zirconia (ZrO2) | Silicon Nitride (Si3N4) | Silicon Carbide (SiC) |
---|---|---|---|---|
Hardness | High | Very High | Extremely High | Exceptionally High |
Wear Resistance | Good | Excellent | Excellent | Superior |
Corrosion Resistance | Poor to Moderate | Excellent (to most chemicals) | Very Good | Superior (especially SSC) |
Max. Temperature | ∼120−250∘C | ∼400−500∘C | ∼800−1000∘C | ∼1350−1700∘C (grade dependent) |
Fracture Toughness | Excellent | Good | Very Good | Moderate |
Density | High (∼7.8 g/cm3) | Moderate (∼6.0 g/cm3) | Low (∼3.2 g/cm3) | Low (∼3.1−3.2 g/cm3) |
Thermal Expansion | Moderate | High | Low | Low |
Electrical Property | Conductive | Insulator | Insulator | Insulator or Semiconductor |
Lubrication Needs | High | Can run dry (limited) | Can run dry (good) | Can run dry (excellent) |
Relative Cost | Low | High | Very High | High |
Key Performance and Durability Insights:
- Extreme Environments: SiC significantly outperforms steel in corrosive, high-temperature, and abrasive environments. While Si3N4 is also a strong contender, SiC (especially SSC) often has an edge in aggressive chemical resistance and higher temperature ceilings.
- Lifespan: In suitable applications, SiC ceramic bearings can offer a lifespan many times that of steel bearings, leading to drastically reduced maintenance intervals and lower lifecycle costs. This is particularly true in unlubricated or marginally lubricated conditions where steel would fail rapidly.
- High-Speed Operation: The lower density of SiC and Si3N4 compared to steel reduces centrifugal forces, making them suitable for higher speed applications. SiC’s high stiffness also contributes to stability at speed.
- Non-Magnetic and Electrically Insulating: Unlike steel, SiC bearings are non-magnetic and can be excellent electrical insulators. This is crucial for applications like electric motors to prevent electrical discharge machining (EDM) damage to the bearing surfaces.
- Dry Running Capability: SiC bearings, particularly those with highly polished surfaces, exhibit excellent performance in dry-running or process-fluid-lubricated conditions where conventional lubricants cannot be used or would contaminate the process. This is a significant advantage over steel bearings which typically require continuous lubrication.
- Brittleness Consideration: The primary drawback of ceramics, including SiC, is their lower fracture toughness compared to steel. This means they are more susceptible to catastrophic failure from shock loads or high tensile stresses. Careful design, handling, and installation are essential to mitigate this risk. Zirconia offers better fracture toughness among ceramics but compromises on hardness and temperature resistance compared to SiC and Si3N4.
For engineers and procurement managers evaluating extreme environment bearings, the decision often comes down to a trade-off between initial cost and long-term performance and reliability. While SiC bearings may have a higher upfront cost than steel, their extended service life and reduced need for maintenance in harsh conditions frequently result in a lower total cost of ownership.
CAS new materials (SicSino) helps clients make these informed decisions by providing detailed material data and application-specific expertise. Our ability to customize SiC grades and designs ensures that the selected bearing solution offers the optimal balance of performance, durability, and cost for your industrial SiC bearing needs.
Choosing the Right Silicon Carbide Bearing Supplier: Why CAS new materials (SicSino) is Your Ideal Partner
Selecting the right supplier for custom silicon carbide bearings is as critical as choosing the material itself. The supplier’s technical capabilities, material expertise, quality control systems, and customer support play a pivotal role in the success of your application. When evaluating potential partners for technical ceramic components, consider the following factors:
- Material Expertise and Range: Does the supplier have in-depth knowledge of different SiC grades (SSC, RBSC, etc.) and their suitability for various applications? Can they offer or source specialized formulations if needed?
- Customization Capabilities: Can the supplier manufacture bearings to your precise design specifications, including complex geometries, tight tolerances, and specific surface finishes? Do they offer design support or DFM (Design for Manufacturability) services?
- Manufacturing Prowess: What are their manufacturing capabilities? Do they have advanced forming, sintering, grinding, and lapping equipment? What is their capacity for small and large volume orders?
- Quality Control and Certifications: What quality management systems (e.g., ISO 9001) are in place? What testing and inspection methods are used to ensure material properties and dimensional accuracy (e.g., density, hardness, strength testing, CMM inspection)?
- Technical Support and Collaboration: Does the supplier offer engineering support throughout the design, prototyping, and production phases? Are they willing to collaborate on challenging applications?
- Track Record and Experience: Do they have a proven history of supplying high-quality SiC components to your industry or for similar applications? Can they provide case studies or references?
- Lead Time and Supply Chain Reliability: What are their typical lead times for custom orders? How robust is their supply chain for raw materials and manufacturing?
- Cost-Effectiveness: While quality is paramount, the supplier should offer competitive pricing without compromising on material or manufacturing standards.
Why CAS new materials (SicSino) Stands Out:
CAS new materials (SicSino) is uniquely positioned to be your preferred partner for custom silicon carbide bearings and components.
- Strategic Location and Industry Immersion: We are based in Weifang City, the recognized hub of China’s silicon carbide customizable parts manufacturing. This region hosts over 40 SiC enterprises, accounting for more than 80% of China’s SiC output. SicSino has been a key player since 2015, fostering technological advancements and large-scale production within this ecosystem.
- Strong Technological Backing: As part of the CAS (Weifang) Innovation Park, SicSino leverages the formidable scientific and technological capabilities of the Chinese Academy of Sciences (CAS). Our foundation on the national technology transfer center of CAS ensures access to cutting-edge research, materials science, and process innovations.
- Comprehensive In-House Expertise: We boast a domestic top-tier professional team specializing in customized SiC production. Our capabilities span the entire spectrum:
- Material Technology: Deep understanding of SiC grades and their properties.
- Process Technology: Expertise in forming, sintering, and precision finishing.
- Design Technology: Advanced design support and FEA capabilities.
- Measurement & Evaluation Technology: Rigorous quality control and testing.
- Integrated Process: Seamless management from raw materials to finished products.
- Proven Track Record: We have successfully supported over 10 local enterprises with our advanced SiC technologies, demonstrating our ability to deliver tangible results and drive industry growth.
- Commitment to Quality and Cost-Effectiveness: Our integrated approach and strategic location allow us to offer higher-quality, cost-competitive customized silicon carbide components within China. We ensure reliable quality and supply assurance.
- Turnkey Solutions and Technology Transfer: Beyond component supply, CAS new materials (SicSino) is committed to fostering global SiC capabilities. If you are looking to establish a professional silicon carbide products manufacturing plant in your country, we can provide technology transfer for professional SiC production. This includes a full range of “turnkey project” services: factory design, procurement of specialized equipment, installation and commissioning, and trial production. This unique offering ensures effective investment, reliable technology transformation, and a guaranteed input-output ratio.
Choosing CAS new materials (SicSino) means partnering with a knowledgeable and reliable silicon carbide bearing manufacturer that is deeply embedded in the industry’s core, backed by national-level scientific resources, and committed to providing comprehensive solutions from custom components to complete factory setups.
Cost Drivers and Lead Time Considerations for SiC Bearings
Understanding the factors that influence the cost and lead time of custom silicon carbide bearings is crucial for effective budgeting, project planning, and procurement. Due to the specialized nature of SiC materials and manufacturing processes, these components typically involve different cost structures and timelines compared to conventional metallic bearings.
Key Cost Drivers:
- Material Grade:
- Sintered Silicon Carbide (SSC): Generally more expensive due to higher purity raw materials, more complex sintering processes, and higher energy consumption.
- Reaction-Bonded Silicon Carbide (RBSC/SiSiC): Often more cost-effective due to lower processing temperatures and the use of less refined raw SiC. However, the cost of high-purity silicon for infiltration can be a factor.
- Raw Material Purity and Powder Characteristics: Finer, high-purity SiC powders required for high-performance bearings contribute to higher costs.
- Complexity of Design and Geometry:
- Intricate Shapes: Complex geometries with internal features, thin walls, or non-standard shapes require more sophisticated tooling and forming techniques, increasing costs.
- Size: Larger components consume more material and may require larger, specialized processing equipment, impacting cost. Smaller, highly precise parts can also be costly due to handling and machining challenges.
- Tolerances and Surface Finish:
- Tight Tolerances: Achieving micron-level dimensional and geometric tolerances necessitates extensive precision grinding, lapping, and metrology, which are time-consuming and add to the cost.
- Surface Finish Requirements: Highly polished or superfinished surfaces (low Ra values) for low friction and wear require multiple finishing steps, significantly impacting labor and machining time.
- Manufacturing Processes:
- Near-Net Shaping: Processes that produce parts closer to the final shape (e.g., injection molding for green parts) can reduce costly and time-consuming machining later on.
- Machining Intensity: The amount of diamond grinding, lapping, or EDM required directly correlates with cost.
- Order Volume (Quantity):
- Economies of Scale: Larger production runs generally allow for better amortization of tooling and setup costs, leading to lower per-unit prices.
- Prototyping and Small Batches: These tend to have higher per-unit costs due to setup, custom tooling, and intensive engineering involvement.
- Quality Assurance and Testing:
- Stringent Inspection: Extensive NDT (Non-Destructive Testing), material characterization, and dimensional inspection add to the overall cost but are crucial for ensuring reliability in critical applications.
Lead Time Considerations:
- Raw Material Availability: Sourcing specific SiC powders or other precursor materials can sometimes impact lead times.
- Tooling Design and Fabrication: For custom designs, creating molds, dies, or fixtures can take several weeks.
- Manufacturing Processes:
- Green body forming: days to weeks depending on complexity and method.
- Sintering/Reaction Bonding: Can take several days per cycle, including controlled heating and cooling.
- Machining and Finishing: This is often the most time-consuming stage for high-precision SiC bearings, potentially taking weeks depending on the complexity and tolerances.
- Order Backlog and Capacity: Supplier workload and available capacity will influence lead times.
- Prototyping vs. Production: Prototypes may have shorter lead times if processes can be expedited, while full production runs will be scheduled based on overall capacity and complexity.
- Quality Control and Shipping: Final inspection and international shipping (if applicable) also add to the total lead time.
Typical lead times for custom SiC bearings can range from a few weeks for simpler, repeat orders to several months for highly complex, new designs, or large volume production.
CAS new materials (SicSino) works transparently with clients to provide realistic cost estimates and lead time projections. Our integrated process, from material sourcing within the Weifang SiC hub to advanced manufacturing and quality control, is optimized for efficiency. We strive to offer competitive pricing for high-performance ceramic bearings without compromising the quality and reliability that our customers expect. Early engagement with our technical team during the design phase can often help identify opportunities for cost optimization and lead time reduction.
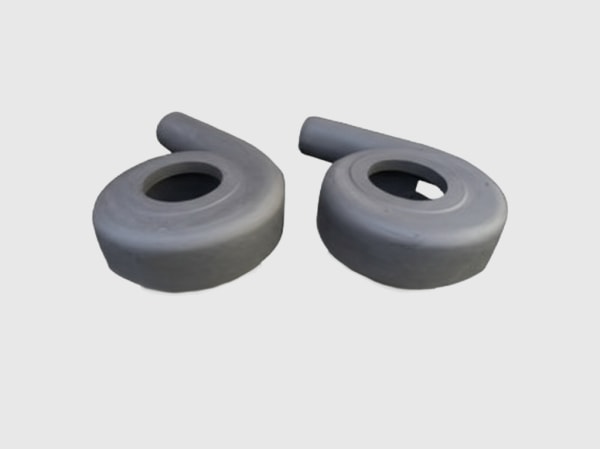
FAQ (Frequently Asked Questions)
Q1: Are silicon carbide bearings significantly more expensive than steel bearings? A: Yes, the initial procurement cost of silicon carbide bearings is generally higher than that of standard steel bearings. This is due to the more complex and energy-intensive manufacturing processes for SiC, the cost of high-purity raw materials, and the specialized machining (diamond grinding) required. However, for applications involving extreme temperatures, corrosive media, high wear, or where lubrication is problematic, SiC bearings can offer a significantly longer service life and reduced maintenance, leading to a lower Total Cost of Ownership (TCO) over time. The enhanced reliability can also prevent costly unscheduled downtime.
Q2: Do SiC bearings require special handling or installation procedures? A: Yes, due to the inherent brittleness of ceramic materials like silicon carbide, special care is required during handling and installation. SiC bearings are less forgiving of shock loads, impact, or misalignment compared to ductile steel bearings. Key considerations include: * Avoiding dropping or striking the bearings. * Using appropriate tools and methods for mounting (e.g., press fitting with precise control, thermal fitting). * Ensuring proper alignment of shafts and housings to prevent stress concentrations. * Carefully calculating interference fits to avoid cracking. CAS new materials (SicSino) can provide guidance on best practices for handling and installing your custom SiC bearings to ensure optimal performance and longevity.
Q3: Can silicon carbide bearings run completely dry without any lubrication? A: Yes, one of the significant advantages of certain types of SiC ceramic bearings, particularly those made from Sintered Silicon Carbide (SSC) with highly polished surfaces, is their ability to run dry or with minimal process fluid lubrication. SiC has a low coefficient of friction and excellent wear resistance, which allows for self-lubricating behavior in some pairings or through the formation of a tribofilm. This makes them ideal for applications where conventional lubricants would contaminate the product (e.g., food processing, semiconductor manufacturing) or cannot survive the operating conditions (e.g., very high temperatures, vacuum). However, the load, speed, and environmental conditions will determine the suitability for completely dry operation.
Q4: What industries benefit most from using custom SiC bearings? A: Industries that regularly encounter harsh operating conditions see the most significant benefits from industrial SiC bearings. These include: * Chemical Processing: For pumps and mixers handling corrosive fluids and abrasive slurries. * Oil & Gas: For downhole tools and pumps in abrasive and corrosive environments. * Semiconductor Manufacturing: For vacuum pumps and precision equipment requiring high purity and wear resistance. * Aerospace & Defense: For components needing high-temperature stability and lightweight properties. * Power Generation: For equipment exposed to high temperatures and corrosive byproducts. * Any application where traditional bearings fail prematurely due to wear, corrosion, high temperatures, or lack of lubrication will benefit from the superior properties of custom SiC bearings. CAS new materials (SicSino) specializes in tailoring SiC bearing solutions for such demanding sectors.
Conclusion: The Unparalleled Value of Custom Silicon Carbide Bearings in Demanding Environments
In the landscape of advanced materials, custom silicon carbide bearings stand out for their exceptional ability to perform under conditions that would lead to the rapid failure of conventional alternatives. Their unparalleled combination of hardness, wear resistance, high-temperature stability, and corrosion inertness makes them the material of choice for engineers and procurement professionals tackling the most demanding industrial challenges. From enhancing the reliability of chemical pumps to enabling precision in semiconductor manufacturing and ensuring durability in aerospace applications, SiC bearings offer a pathway to improved efficiency, extended service life, and reduced operational costs.
Choosing the right material and, equally importantly, the right supplier is critical to unlocking these benefits. CAS new materials (SicSino), strategically located in Weifang, the nucleus of China’s SiC industry, and backed by the prestigious Chinese Academy of Sciences, offers not just components but comprehensive solutions. Our deep expertise in SiC material science, custom design, precision manufacturing, and quality assurance ensures that our clients receive SiC ceramic bearings optimized for their specific needs. Whether you require bespoke bearing components or are exploring the potential of establishing your own SiC production capabilities through our turnkey technology transfer programs, SicSino is your trusted partner.
By investing in high-quality, custom-engineered silicon carbide bearings, industries can push the boundaries of performance, achieve greater reliability, and ultimately gain a competitive edge in an increasingly demanding global market. We invite you to engage with CAS new materials (SicSino) to explore how our advanced silicon carbide solutions can elevate your applications.
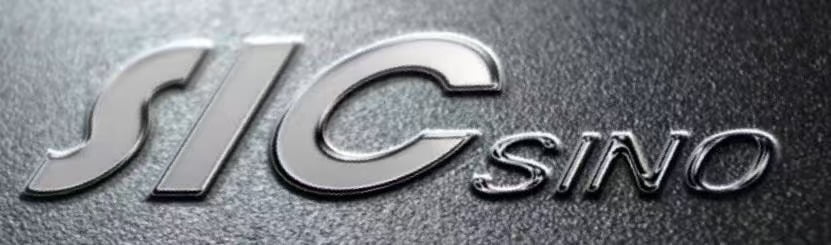
SicSino – CAS new materials
We, CAS new materials(SicSino), have been introducing and implementing silicon carbide production technology since the 2015, assisting the local enterprises in achieving large-scale production and technological advancements in product processes. We have been a witness to the emergence and ongoing development of the local silicon carbide industry.
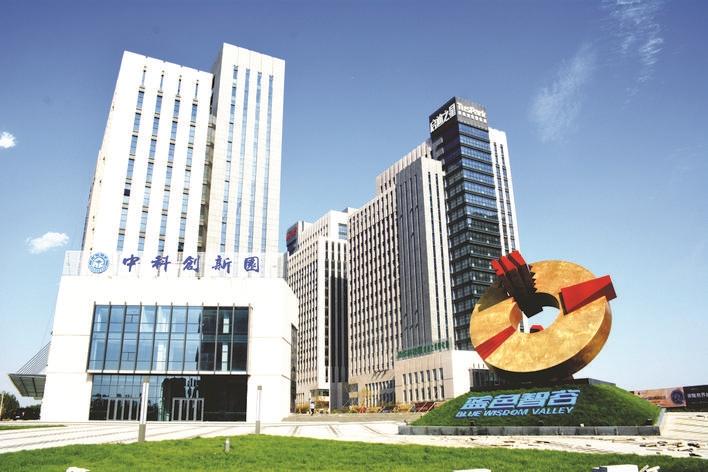