Mastering Extreme Conditions: Why Custom Silicon Carbide is Revolutionizing Fluid Handling
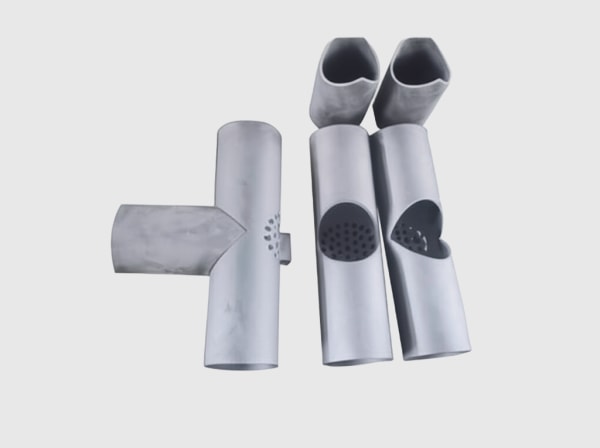
Share
In the demanding world of industrial fluid handling, equipment is constantly under siege from corrosive chemicals, abrasive slurries, high temperatures, and extreme pressures. Traditional materials often fall short, leading to frequent downtime, costly maintenance, and compromised operational efficiency. Enter custom silicon carbide (SiC), a high-performance technical ceramic that is rapidly becoming the material of choice for critical fluid handling components. Its exceptional properties offer unparalleled reliability and longevity in applications where others fail. This blog post delves into the world of custom SiC for fluid handling, exploring its applications, advantages, design considerations, and how choosing the right supplier, like CAS new materials (SicSino), can be a game-changer for your operations.
Introduction to Custom Silicon Carbide in Demanding Fluid Handling Applications
Silicon Carbide (SiC) is an advanced synthetic ceramic material renowned for its remarkable hardness, strength, and thermal stability. Formed by a compound of silicon and carbon, SiC boasts a unique combination of properties that make it exceptionally suited for high-performance industrial applications. While standard SiC components offer significant benefits, custom silicon carbide products take this a step further by tailoring these properties to the precise requirements of specific, often extreme, fluid handling environments.
Fluid handling systems are the lifeblood of many industries, from chemical processing and energy production to semiconductor manufacturing and pharmaceuticals. The fluids transported can range from ultrapure water to highly corrosive acids, abrasive slurries, and high-temperature liquids and gases. The challenges are immense:
- Corrosion: Aggressive chemicals can rapidly degrade metallic components.
- Abrasion & Erosion: Solids-laden fluids can wear down parts quickly.
- High Temperatures & Pressures: Many processes operate under conditions that exceed the limits of conventional materials.
- Thermal Shock: Rapid temperature fluctuations can cause materials to crack or fail.
- Purity Requirements: In industries like semiconductors and pharmaceuticals, material inertness is crucial to prevent contamination.
Custom SiC components, such as seals, bearings, pump volutes, impellers, valve seats, and nozzles, are engineered to withstand these harsh conditions. By customizing the SiC grade, design, and manufacturing process, engineers can achieve optimal performance, minimize wear and tear, extend service life, and reduce the total cost of ownership. The ability to precisely engineer a component for a specific fluid, temperature range, and mechanical load is what makes custom SiC an indispensable solution in modern industry. This is where the expertise of specialized manufacturers becomes critical, ensuring that the unique potential of SiC is fully harnessed for each application.
Key Industrial Applications of SiC in Fluid Handling Systems
The versatility and robustness of silicon carbide make it suitable for a wide array of critical components within fluid handling systems across diverse industries. Its adoption is driven by the need for enhanced reliability and performance where traditional materials like stainless steel, superalloys, or even other ceramics like alumina, reach their operational limits.
Pumps: SiC is extensively used in various pump components, especially those handling abrasive slurries, corrosive chemicals, or operating at high temperatures.
- Impellers and Volutes/Casings: Reaction-Bonded Silicon Carbide (RBSiC or SiSiC) and Sintered Silicon Carbide (SSiC) offer superior resistance to wear from abrasive particles and corrosion from aggressive chemicals, significantly outlasting metal or rubber-lined parts. Custom-designed SiC pump components maintain their profile for longer, ensuring consistent pump performance.
- Shafts and Shaft Sleeves: The high stiffness and wear resistance of SiC protect shafts from abrasive wear and chemical attack, preventing premature failure and reducing maintenance for industrial SiC pump parts.
- Bearings (Journal and Thrust): SiC bearings, particularly SSiC, can operate in process fluids (product-lubricated bearings), even those that are corrosive or contain abrasive particles. Their low friction and high hardness lead to extended life in applications like SiC bearings for pumps in chemical or slurry services.
Valves: Valves controlling the flow of harsh fluids benefit immensely from SiC’s properties.
- Seats, Discs, Balls, and Plugs: Custom SiC valve components provide exceptional sealing and longevity in highly erosive or corrosive environments. SiC ball valve parts and seats maintain their tight shut-off capabilities far longer than metallic equivalents.
- Liners: For valve bodies exposed to severe conditions, SiC liners offer a robust barrier against wear and chemical attack.
Mechanical Seals: Perhaps one of the most well-established applications for SiC in fluid handling is in mechanical seals.
- Seal Faces/Rings: SiC, often paired with itself or carbon-graphite, provides an ideal combination of hardness, high thermal conductivity (to dissipate frictional heat), excellent corrosion resistance, and low wear rates. SiC mechanical seal faces are standard in demanding applications such as chemical pumps, high-pressure pumps, and hot water services. SSiC and graphite-loaded SiC are popular choices here.
Other Fluid Handling Equipment:
- Nozzles: SiC spray nozzles are used for injecting chemicals, cooling, or cleaning in corrosive or erosive streams due to their ability to maintain orifice geometry and spray patterns.
- Liners for Pipes and Cyclones: In mining and mineral processing, SiC liners protect equipment from extreme abrasive wear.
- Flow Meters: Components within flow meters that come into contact with aggressive fluids can be made from SiC to ensure accuracy and longevity.
- Heat Exchanger Tubes: For very specific aggressive media or high-temperature applications, SiC tubes offer excellent thermal conductivity and corrosion resistance.
The table below highlights key industries and the benefits SiC brings to their fluid handling applications:
Industry Sector | Common SiC Components Used | Key SiC Benefits Leveraged |
---|---|---|
Chemical Processing | Pump parts (impellers, casings, bearings), Valve trims (seats, balls), Mechanical seal faces, Nozzles | Superior corrosion resistance, wear resistance, high-temperature stability |
Petrochemical | Pump components, Mechanical seals, Valve parts for sour gas or abrasive crudes | Chemical inertness, wear resistance, thermal shock resistance |
Mining & Mineral Processing | Slurry pump parts, Cyclone liners, Pipe liners, Chute liners | Extreme abrasion resistance, erosion resistance |
Oil & Gas (Upstream/Downstream) | Pump bearings, Mechanical seals, Choke valve components | Wear resistance in sandy conditions, corrosion resistance (H2S) |
Power Generation | Boiler feedwater pump seals, Flue Gas Desulfurization (FGD) pump parts & nozzles | High-temperature strength, abrasion and corrosion resistance |
Semiconductor Manufacturing | Ultrapure water pump components, Wafer handling parts, CMP slurry components | High purity, chemical inertness, wear resistance |
Pharmaceuticals & Food | Pump seals, Homogenizer parts, Bearings for process fluids | FDA compliance (for certain grades), cleanability, wear resistance, chemical inertness |
Pulp & Paper | Pump components for abrasive/corrosive media, Mechanical seals, Doctor blades | Wear resistance against fibers and fillers, chemical resistance |
The widespread adoption of technical ceramics for industrial use, particularly SiC, in these applications underscores its critical role in enhancing operational efficiency and reducing maintenance costs in challenging fluid environments.
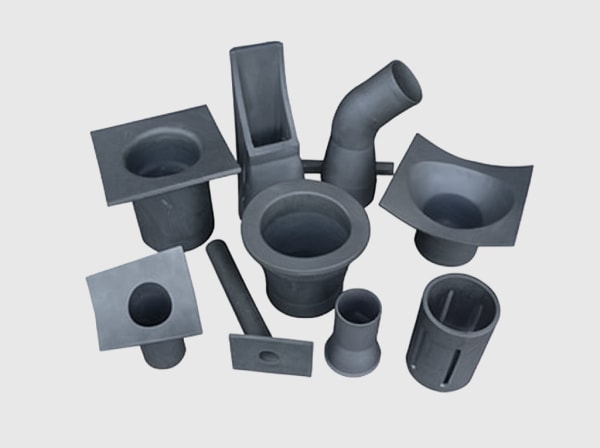
Why Choose Custom Silicon Carbide for Fluid Handling?
While off-the-shelf SiC components can offer significant advantages, custom silicon carbide solutions provide an even higher level of performance and reliability by precisely matching the material and design to the specific demands of your fluid handling application. Opting for customization unlocks a range of benefits that directly impact operational efficiency, component lifespan, and overall system integrity.
- Superior Wear and Abrasion Resistance: Fluids containing hard particles, such as slurries in mining, pigments in chemical processing, or catalysts, can wreak havoc on conventional materials. Custom SiC components, engineered from grades like Sintered Silicon Carbide (SSiC) or specialized Reaction-Bonded Silicon Carbide (RBSiC), offer hardness second only to diamond. This translates into significantly extended service life for parts like pump impellers, liners, and valve seats, even when handling the most abrasive slurries. This drastically reduces downtime associated with parts replacement.
- Unmatched Corrosion Resistance: Silicon carbide is virtually inert to a vast spectrum of chemicals, including strong acids (e.g., sulfuric, nitric, hydrochloric, hydrofluoric acid), bases, solvents, and oxidizing agents, even at elevated temperatures. Customization allows for the selection of the purest SiC grades (like SSiC with no free silicon) for applications involving extremely corrosive media, ensuring that corrosion-resistant ceramic parts maintain their structural integrity and prevent product contamination.
- Exceptional High-Temperature Stability: Many fluid handling processes occur at elevated temperatures where metals may soften, creep, or corrode rapidly. SiC maintains its excellent mechanical strength, hardness, and chemical resistance at temperatures exceeding 1400∘C (and some grades even higher). Custom designs can account for thermal expansion and ensure components like high-temperature SiC valves or pump parts operate reliably.
- Excellent Thermal Shock Resistance: Industrial processes can involve rapid temperature changes, which can cause brittle materials to fracture. Certain grades of SiC, particularly Nitride-Bonded Silicon Carbide (NBSC) or specifically engineered RBSiC, offer good thermal shock resistance. Custom design further optimizes the component’s geometry to minimize stress concentrations during thermal cycling.
- High Thermal Conductivity: For applications like mechanical seal faces or bearings, the ability to dissipate frictional heat is crucial. SiC possesses significantly higher thermal conductivity than other ceramics like alumina or zirconia. This property helps prevent overheating, reduces thermal distortions, and extends the life of dynamic components. Customizing the SiC grade can fine-tune this property.
- Low Coefficient of Friction and Self-Lubricating Properties: In dynamic applications such as SiC mechanical seals for chemical pumps or custom SiC bearings, SiC (especially when paired with itself or graphite) exhibits a low coefficient of friction. This reduces energy consumption, minimizes wear, and allows for operation with poor lubricants or even dry running for short periods in some cases.
- Chemical Inertness and Purity: For industries like semiconductor manufacturing (ultrapure water systems) or pharmaceuticals, preventing contamination of the process fluid is paramount. High-purity SSiC is exceptionally inert and does not leach ions into the fluid, ensuring product quality.
- Extended Service Life and Reduced Total Cost of Ownership (TCO): While the initial investment for custom SiC components might be higher than for parts made from conventional materials, their significantly longer operational life, reduced maintenance requirements, and minimized downtime lead to a substantially lower TCO. The extended mean time between failures (MTBF) translates directly into increased productivity and profitability.
Choosing custom SiC means partnering with a supplier who understands the nuances of both the material and the application. CAS new materials (SicSino), located in Weifang City, the heart of China’s silicon carbide manufacturing hub, leverages its deep expertise and connection with the Chinese Academy of Sciences (CAS) to provide precisely tailored SiC solutions. Their assistance to over 40 local SiC enterprises has fostered an environment of technological advancement, ensuring that custom components deliver maximum performance.
Recommended SiC Grades and Compositions for Fluid Handling
Selecting the appropriate grade of silicon carbide is crucial for optimizing performance and cost-effectiveness in fluid handling applications. Different manufacturing processes result in SiC materials with varying microstructures and properties. Here are some of the most common SiC grades and their typical suitability for fluid handling:
- Reaction-Bonded Silicon Carbide (RBSiC or SiSiC – Silicon Infiltrated Silicon Carbide):
- Manufacturing: Produced by infiltrating a porous carbon-SiC preform with molten silicon. The silicon reacts with some of the carbon to form more SiC, and the remaining pores are filled with metallic silicon (typically 8-20% free silicon).
- Properties: Good wear resistance, high hardness, excellent thermal conductivity, good dimensional control, and relatively lower manufacturing cost. Can be formed into complex shapes.
- Fluid Handling Suitability: Widely used for pump components (impellers, volutes, shaft sleeves), valve trims, cyclone liners, and nozzles in moderately corrosive and abrasive environments. It’s a workhorse material for many industrial SiC components.
- Limitations: The presence of free silicon makes it susceptible to attack by strong alkalis, hydrofluoric acid, and certain high-temperature oxidizing environments. Not ideal for ultra-high purity applications.
- Sintered Silicon Carbide (SSiC or S-SiC):
- Manufacturing: Produced by sintering fine, high-purity SiC powder at very high temperatures (typically > 2000∘C) with non-oxide sintering aids (e.g., boron and carbon). This results in a dense, fine-grained, single-phase SiC material.
- Properties: Highest purity (typically >99% SiC), exceptional corrosion resistance across the full pH range, superior wear and erosion resistance, excellent high-temperature strength, and good thermal shock resistance.
- Fluid Handling Suitability: The premium choice for the most demanding applications, including mechanical seal faces in highly corrosive chemical pumps, bearings operating in aggressive media, valve components for severe service, and parts for ultrapure water systems. Often specified for advanced ceramic solutions in critical applications.
- Limitations: Generally more expensive than RBSiC and can be more challenging to produce in very large or highly complex shapes.
- Nitride-Bonded Silicon Carbide (NBSC):
- Manufacturing: SiC grains are bonded by a silicon nitride (Si3N4) matrix.
- Properties: Good mechanical strength, excellent thermal shock resistance, and good resistance to wetting by molten metals.
- Fluid Handling Suitability: Less common as a primary material for direct fluid contact components compared to RBSiC or SSiC, but can be used in applications where extreme thermal cycling is a major concern, or as refractory components associated with high-temperature fluid processes.
- Graphite-Loaded Silicon Carbide (SiC-C):
- Manufacturing: Typically SSiC or RBSiC with fine graphite particles dispersed within the SiC matrix.
- Properties: Enhanced tribological properties, including lower coefficient of friction and improved dry-running capabilities. The graphite acts as a solid lubricant.
- Fluid Handling Suitability: Primarily used for mechanical seal faces and bearings where improved lubricity is critical, especially in applications with marginal lubrication or risk of intermittent dry running. Essential for high-performance mechanical seals.
- Porous Silicon Carbide:
- Properties: Controlled porosity, high surface area, good thermal and chemical stability.
- Fluid Handling Suitability: Used in specialized applications such as filters for hot gases or corrosive liquids, diffusers, membranes, and catalyst supports.
The following table provides a comparative overview of key SiC grades for fluid handling:
SiC Grade | Key Characteristics | Typical Fluid Handling Applications | Relative Cost | Corrosion Resistance | Abrasion Resistance | Max. Use Temp. (approx.) |
---|---|---|---|---|---|---|
RBSiC (SiSiC) | Good overall properties, complex shapes, moderate cost, contains free silicon | Pump impellers & casings, valve parts, nozzles, wear liners for moderate corrosion/abrasion | Medium | Good (except strong alkalis, HF) | Very Good | 1350∘C |
SSiC (Sintered SiC) | Highest purity, excellent corrosion & wear resistance, high strength at temperature | Mechanical seal faces, bearings, valve components for severe chemical & abrasive service, ultrapure water | High | Excellent | Excellent | 1600∘C |
Nitride-Bonded SiC (NBSC) | Excellent thermal shock resistance, good strength | Applications with severe thermal cycling, refractory components | Medium-High | Good | Good | 1550∘C |
Graphite-Loaded SiC (e.g., SSiC+C) | Improved lubricity, lower friction, good dry-run capability | Mechanical seal faces, bearings requiring enhanced tribological performance | High | Excellent (base SiC) | Very Good | 1600∘C (base SiC) |
Choosing the correct SiC grade is a critical step. CAS new materials (SicSino), with its extensive experience and support from the Chinese Academy of Sciences, provides invaluable assistance in this selection process. Their deep understanding of material science and manufacturing processes, honed by assisting numerous enterprises in Weifang’s SiC industrial cluster, ensures that clients receive custom SiC components perfectly optimized for their specific fluid handling challenges.
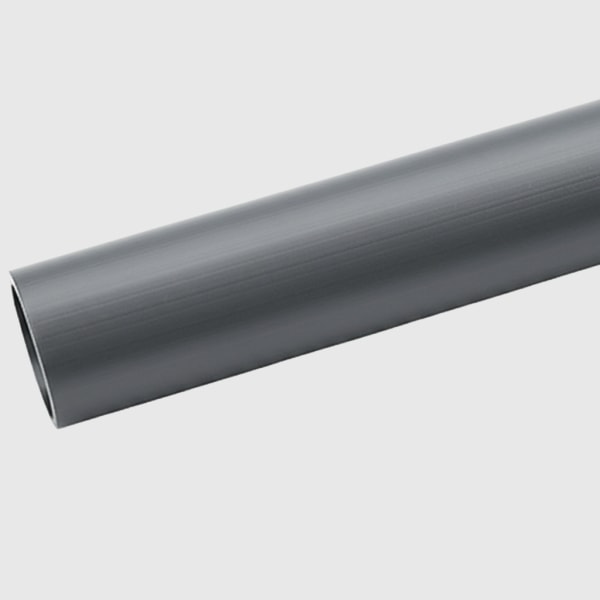
Critical Design and Manufacturability Considerations for Custom SiC Fluid Handling Components
Designing components with silicon carbide requires a different approach than with metals or plastics due to its inherent hardness and brittleness. While SiC offers exceptional performance, careful design considerations are essential to ensure manufacturability, structural integrity, and optimal functionality in fluid handling systems. Collaborating with an experienced SiC manufacturer like CAS new materials (SicSino) early in the design phase is highly recommended to leverage their specialized knowledge.
Key Design Principles for SiC Components:
- Simplicity and Geometry:
- Avoid Sharp Corners and Edges: These create stress concentrations that can lead to chipping or fracture. Generous radii and chamfers should be incorporated.
- Uniform Wall Thickness: Helps prevent stress during sintering and thermal cycling. Avoid abrupt changes in cross-section.
- Minimize Complex Internal Features: While possible, intricate internal cavities or undercuts can significantly increase manufacturing complexity and cost. Design for ease of demolding or green machining.
- Aspect Ratios: Very long, thin parts can be challenging to manufacture and handle without breakage.
- Managing Brittleness:
- Tensile vs. Compressive Loads: SiC is much stronger in compression than in tension. Designs should aim to load SiC components compressively wherever possible.
- Stress Analysis: For critical components, Finite Element Analysis (FEA) can identify high-stress areas and allow for design optimization before manufacturing.
- Impact Resistance: Design housings or surrounding structures to protect SiC parts from direct impact.
- Joining SiC to Other Materials:
- Fluid handling systems often require SiC components to be integrated with metallic housings or other parts.
- Differential Thermal Expansion: SiC generally has a lower coefficient of thermal expansion than metals. This difference must be accommodated in the design to prevent stress build-up during temperature changes. Techniques include using compliant interlayers, specific brazing alloys, or mechanical attachment methods like shrink-fitting (with careful interference calculations) or bolting with appropriate gasket materials.
- Brazing and Bonding: Specialized active brazing alloys or adhesive bonding techniques can be used, but require careful surface preparation and process control.
- Sealing Surfaces:
- For components like mechanical seal faces or valve seats, the design of the sealing surface is paramount.
- Flatness and Surface Finish: Specify appropriate flatness and surface finish requirements to ensure effective sealing and minimize friction/wear.
- Contact Pressure: Ensure the design allows for uniform contact pressure across the sealing interface.
- Designing for Manufacturability (DFM):
- Forming Process Limitations: The chosen forming method (e.g., dry pressing, isostatic pressing, slip casting, extrusion, injection molding, or newer additive manufacturing techniques) will influence design possibilities. For example, pressing is suitable for simpler shapes, while slip casting or additive manufacturing can produce more complex geometries.
- Sintering Shrinkage: SiC parts shrink significantly during sintering (typically 15-20% for SSiC). This must be accounted for in the green (pre-sintered) stage design to achieve final dimensions.
- Machining Allowances: If tight tolerances require post-sinter diamond grinding, sufficient material allowance must be included in the as-sintered design.
Engineering Tips for Success:
- Early Supplier Involvement: Engage with your SiC supplier, such as CAS new materials (SicSino), at the earliest stages of design. Their expertise in custom SiC manufacturing and materials science can save significant time and cost by optimizing the design for performance and manufacturability. CAS new materials (SicSino), with its foundation in the CAS (Weifang) Innovation Park and extensive experience assisting the local Weifang SiC industry, possesses a deep understanding of design, material, process, and evaluation technologies.
- Provide Comprehensive Application Details: Clearly define the operating conditions: fluid composition, temperature range, pressure, flow rates, presence and nature of abrasives, and expected component lifetime.
- Iterative Prototyping: For complex or critical parts, consider a prototyping phase to validate the design and performance before committing to large-scale production.
By adhering to these design principles and collaborating closely with experts, engineers can fully harness the exceptional properties of silicon carbide for robust and long-lasting fluid handling solutions.
Achieving Precision: Tolerances, Surface Finish, and Dimensional Control for SiC Fluid Parts
The performance of silicon carbide components in demanding fluid handling applications, particularly for parts like mechanical seal faces, bearings, valve seats, and precision nozzles, is critically dependent on achieving tight dimensional tolerances and specific surface finishes. The inherent hardness of SiC makes machining challenging, requiring specialized diamond tooling and techniques. Understanding the achievable precision is vital for both design engineers and procurement professionals.
Dimensional Tolerances:
- As-Sintered Tolerances: Components directly from the sintering furnace (as-sintered) will have wider dimensional tolerances. These are influenced by the forming method, powder characteristics, and sintering cycle. Typical as-sintered tolerances for SiC might range from ±0.5% to ±2% of the dimension, depending on size and complexity. For applications where these tolerances are acceptable, costs can be lower as post-sintering machining is minimized or eliminated.
- Machined Tolerances: For applications requiring high precision, SiC components undergo diamond grinding after sintering. This allows for much tighter tolerances.
- Standard Machined Tolerances: Typically in the range of ±0.025 mm to ±0.1 mm (±0.001″ to ±0.004″).
- Precision Machined Tolerances: For critical features, tolerances as tight as ±0.005 mm to ±0.01 mm (±0.0002″ to ±0.0004″) can be achieved with advanced grinding and lapping processes. However, striving for unnecessarily tight tolerances significantly increases cost.
Surface Finish (Roughness):
The surface finish of SiC components is crucial, especially for dynamic sealing surfaces and bearings, as it directly impacts friction, wear, and sealing efficiency.
- As-Sintered Surface: The surface finish of as-sintered parts is generally rougher, often in the range of Ra=1.0 to 3.0 μm.
- Ground Surface: Diamond grinding can achieve smoother surfaces, typically Ra=0.2 to 0.8 μm. This is suitable for many general-purpose fluid handling components.
- Lapped and Polished Surfaces: For high-performance applications like mechanical seal faces or precision bearings, lapping and polishing are employed to achieve very fine surface finishes.
- Lapped: Ra=0.05 to 0.2 μm.
- Polished: Ra<0.025 μm (mirror finish) can be achieved, resulting in extremely low friction and excellent sealing capabilities. Such finishes are essential for high-performance SiC mechanical seals.
The table below illustrates typical surface finish values for different processing stages:
Processing Stage | Typical Surface Roughness (Ra) | Common Applications |
---|---|---|
As-Sintered | 1.0−3.0 μm | Liners, non-critical structural parts |
Ground | 0.2−0.8 μm | General purpose pump parts, valve bodies |
Lapped | 0.05−0.2 μm | Standard mechanical seal faces, less critical bearings |
Polished (Fine Lapped) | <0.05 μm | High-performance mechanical seal faces, precision bearings |
Dimensional Accuracy and Stability:
Silicon carbide exhibits excellent dimensional stability over a wide range of temperatures and does not suffer from creep at typical industrial operating temperatures (unlike some metals or plastics). This means that once a component is manufactured to the required precision, it will maintain its dimensions and shape throughout its service life, contributing to consistent performance.
Impact on Performance and Cost:
- Tighter tolerances and finer surface finishes invariably lead to higher manufacturing costs due to the additional machining steps (grinding, lapping, polishing) and increased inspection requirements.
- However, for critical applications, the improved performance (e.g., reduced leakage in seals, lower friction in bearings, extended life) often justifies the investment.
- It is crucial to specify only the level of precision truly required by the application to achieve a balance between performance and cost.
CAS new materials (SicSino), leveraging its position in Weifang, the hub of China’s SiC industry, and its access to the advanced technological capabilities of the Chinese Academy of Sciences, is well-equipped to meet stringent tolerance and surface finish requirements. Their integrated processes, from material development to final product evaluation, ensure that custom SiC fluid handling parts meet the demanding specifications of wholesale buyers, technical procurement professionals, and OEMs. Their domestic top-tier professional team specializes in customized production, benefiting from a wide array of technologies including advanced measurement and evaluation techniques.
Navigating Challenges and Post-Processing for Peak Performance in SiC Fluid Components
While silicon carbide offers a formidable array of benefits for fluid handling, it also presents certain challenges in manufacturing and application. Understanding these challenges and the necessary post-processing steps is key to unlocking the material’s full potential and ensuring reliable, long-term performance. This is where the expertise of a seasoned industrial SiC supplier becomes invaluable.
Common Challenges with Silicon Carbide:
- Brittleness: Like most ceramics, SiC is a brittle material with low fracture toughness compared to metals. This means it is susceptible to catastrophic failure if subjected to high impact loads or excessive tensile stresses.
- Mitigation: Careful design (avoiding stress concentrators, using compressive loading), proper handling during assembly and maintenance, and protecting components from mechanical shock are crucial. Material selection (e.g., tougher grades or composites for specific impact scenarios, though this can compromise other properties) can also play a role.
- Machining Complexity and Cost: The extreme hardness of SiC means that any shaping or finishing after sintering must be done using diamond tooling. This is a slower and more expensive process than machining metals.
- Mitigation: Designs should aim to achieve near-net shape during the initial forming and sintering stages to minimize the amount of post-sinter grinding. Early collaboration with manufacturers like CAS new materials (SicSino) helps optimize designs for manufacturability.
- Thermal Shock Sensitivity (for some grades/designs): While SiC generally has good thermal shock resistance, rapid and extreme temperature changes can still induce stresses leading to cracking, especially in complex shapes or constrained designs.
- Mitigation: Selecting appropriate SiC grades (e.g., NBSC or SSiC with fine grain structure), designing for uniform heating/cooling, and understanding the application’s thermal cycling parameters are important.
- Joining to Other Materials: As mentioned in design considerations, effectively joining SiC to metallic components can be complex due to differences in thermal expansion coefficients.
- Mitigation: Employing specialized joining techniques (e.g., active metal brazing, shrink fitting with careful design, mechanical clamping with compliant interlayers) requires expertise.
Essential Post-Processing Steps for SiC Fluid Components:
After the initial sintering process, several post-processing steps are often necessary to meet the dimensional and surface finish requirements for high-performance fluid handling components:
- Precision Grinding: This is the most common post-processing step, using diamond grinding wheels to achieve tight dimensional tolerances, specific profiles, and improved surface finishes on critical areas such as shafts, bearing races, and sealing surfaces.
- Lapping and Polishing: For applications demanding exceptionally smooth and flat surfaces, such as SiC mechanical seal faces or high-precision valve seats, lapping and polishing are employed. These processes use progressively finer diamond abrasives to achieve mirror-like finishes (Ra<0.05μm), minimizing friction and leakage.
- Edge Preparation (Chamfering/Radiusing): To reduce the risk of chipping on sharp edges, which can act as crack initiation sites, edges are often chamfered or radiused. This is particularly important for parts that are handled frequently or subjected to contact stresses.
- Cleaning: Thorough cleaning is essential to remove any contaminants, machining residues, or loose particles before the components are assembled into fluid handling systems, especially for high-purity applications.
- Sealing (less common for dense SiC): While SSiC is inherently dense, some RBSiC grades might have slight residual porosity. For specific applications requiring absolute impermeability, or if porous SiC is used for filtration, impregnation with resins or other sealants might be performed. However, for most corrosion and wear-resistant fluid handling applications, dense SSiC or RBSiC without post-sealing is preferred.
- Inspection and Quality Control: Rigorous inspection using advanced metrology equipment (CMMs, surface profilometers, interferometers) is vital to ensure that all specifications for dimensions, tolerances, and surface finish are met.
Overcoming these challenges and implementing appropriate post-processing requires significant expertise and specialized equipment. CAS new materials (SicSino) excels in this domain. Their comprehensive technological capabilities, encompassing material science, process engineering, design optimization, and meticulous measurement and evaluation, enable them to produce high-quality, cost-competitive custom silicon carbide components. Their support for local enterprises in Weifang has driven technological advancements across the SiC production chain, ensuring that customers benefit from cutting-edge manufacturing practices. This integrated approach allows them to effectively mitigate common SiC challenges and deliver parts ready for peak performance.
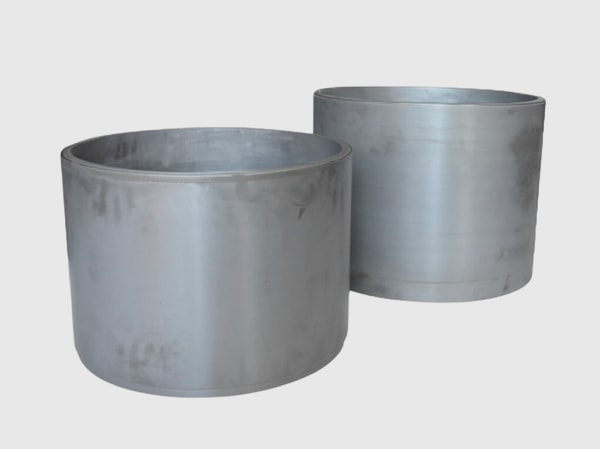
Frequently Asked Questions (FAQ) about Silicon Carbide in Fluid Handling
Procurement managers, engineers, and technical buyers often have questions when considering silicon carbide for their fluid handling applications. Here are answers to some common queries:
Q1: What are the main advantages of SiC over traditional materials like stainless steel or other ceramics (e.g., alumina) in corrosive fluid handling?
A1: Silicon Carbide (SiC) offers several distinct advantages: * Superior Corrosion Resistance: SiC (especially SSiC) is virtually inert to a much wider range of aggressive chemicals, including strong acids and bases, over a broader temperature range than most stainless steels and even alumina. Alumina, for example, is susceptible to attack by strong alkalis and hydrofluoric acid. * Exceptional Wear and Abrasion Resistance: SiC is significantly harder than stainless steel and alumina. This makes it far more resistant to wear from abrasive slurries, extending component life dramatically. * High-Temperature Capability: SiC maintains its mechanical properties and corrosion resistance at much higher temperatures than stainless steels and most other industrial ceramics. * Thermal Conductivity: SiC generally has higher thermal conductivity than alumina, which is beneficial for dissipating heat in applications like mechanical seals. * Hardness & Stiffness: SiC’s high hardness and stiffness contribute to dimensional stability and resistance to deformation under load.
While stainless steel offers good general corrosion resistance and toughness, and alumina is a cost-effective ceramic for moderate wear and corrosion, SiC excels in the most extreme conditions where these materials would fail prematurely.
Q2: How does the cost of custom SiC components compare to mass-produced metal or plastic parts?
A2: The initial procurement cost of custom SiC components is typically higher than for mass-produced parts made from common metals (like stainless steel) or plastics. This is due to the cost of raw materials, energy-intensive manufacturing processes (sintering at high temperatures), and precision diamond machining.
However, it’s crucial to consider the Total Cost of Ownership (TCO). SiC components offer: * Significantly longer service life: Reducing replacement frequency. * Reduced downtime: Leading to higher productivity. * Lower maintenance costs: Fewer repairs and replacements. * Improved process efficiency: Consistent performance due to wear resistance. In many demanding applications, the extended lifespan and reliability of SiC parts result in a lower TCO compared to cheaper alternatives that require frequent replacement. OEM SiC components are often specified for critical applications where long-term reliability is paramount.
Q3: What information do I need to provide to get an accurate quote for custom SiC fluid handling components from a supplier like CAS new materials (SicSino)?
A3: To receive an accurate and timely quotation, please provide as much of the following information as possible: * Detailed Drawings or CAD Models: Including all dimensions, critical tolerances, and surface finish requirements. * Material Grade: Specify the desired SiC grade (e.g., SSiC, RBSiC) or describe the application to allow the supplier to recommend a suitable grade. * Operating Conditions: * Fluid Composition: Specific chemicals, concentrations, pH. * Presence of Abrasives: Type, size, and concentration of solids. * Temperature Range: Minimum, maximum, and normal operating temperatures. * Pressure: Operating pressure and any pressure fluctuations. * Flow Rate: If relevant to wear or erosion. * Quantity Required: Including anticipated annual usage if applicable. * Application Description: Briefly explain how and where the component will be used. * Any Specific Testing or Certification Requirements.
Providing comprehensive information enables suppliers like CAS new materials (SicSino) to understand your needs thoroughly and offer the most appropriate and cost-effective solution. Their team is experienced in working with wholesale buyers and technical procurement professionals to define specifications accurately.
Q4: Can SiC components be repaired, or are they typically replaced?
A4: Generally, due to their extreme hardness and brittle nature, repairing damaged SiC components is very difficult and often not economically viable. Attempting to weld or patch SiC can introduce flaws or fail to restore original properties. Minor surface rework like re-lapping of a seal face might be possible in some limited cases if sufficient material stock exists and the damage is superficial. However, for most types of damage (cracks, significant chips, or wear beyond tolerance), replacement is the standard approach. The design philosophy for SiC components focuses on maximizing their initial service life to minimize the need for intervention.
Q5: What is the typical lead time for custom SiC fluid handling parts?
A5: Lead times for custom SiC fluid handling parts can vary significantly based on several factors: * Complexity of the Part: More intricate designs require more complex tooling and longer manufacturing times. * Material Grade: Some specialized grades may have longer production cycles. * Quantity Ordered: Larger quantities may have longer overall lead times but can sometimes benefit from production efficiencies. Small, highly custom orders might require dedicated setups. * Tolerance and Surface Finish Requirements: Tighter specifications necessitate more extensive machining and inspection, adding to the time. * Tooling Requirements: If new molds or specialized tooling are needed, this will add to the initial lead time. * Current Supplier Workload: Peak demand periods can affect lead times.
Typical lead times can range from a few weeks for simpler, repeat-order parts to several months for highly complex, first-time components requiring new tooling. It’s always best to discuss lead time requirements with your supplier. CAS new materials (SicSino), with its integrated processes and commitment to efficient production, strives to offer competitive lead times for its high-quality customized silicon carbide components within China and for global clients.
Conclusion: The Enduring Value of Custom Silicon Carbide in Demanding Industrial Environments
In the relentless pursuit of operational excellence and reliability in industrial fluid handling, the choice of materials for critical components is paramount. Custom silicon carbide has unequivocally demonstrated its superior capabilities in environments where corrosion, abrasion, high temperatures, and extreme pressures push conventional materials beyond their limits. The intrinsic properties of SiC – its exceptional hardness, chemical inertness, thermal stability, and wear resistance – translate directly into tangible benefits: significantly extended component lifespan, drastically reduced maintenance intervals and downtime, and enhanced process consistency.
Opting for custom SiC solutions allows engineers and procurement professionals to move beyond standard offerings and acquire components precisely engineered for their specific application challenges. This tailored approach ensures optimal performance and maximizes the return on investment, particularly when considering the total cost of ownership. From pump impellers and mechanical seals to valve trims and specialized nozzles, customized silicon carbide parts are pivotal in enhancing the efficiency and safety of fluid handling systems across a multitude of industries, including chemical processing, energy, aerospace, and manufacturing.
Choosing the right supplier is as critical as choosing the right material. A partner like CAS new materials (SicSino) offers more than just components; they provide comprehensive expertise rooted in the heart of China’s SiC manufacturing hub, Weifang City. Backed by the formidable scientific and technological capabilities of the Chinese Academy of Sciences (CAS) and its National Technology Transfer Center, SicSino delivers not only higher-quality, cost-competitive custom SiC components but also a wealth of knowledge in material selection, design optimization, and process integration. Their proven track record in assisting numerous local enterprises achieve technological advancements underscores their commitment to quality and innovation.
Furthermore, for organizations looking to establish their own specialized SiC production, CAS new materials (SicSino) offers unparalleled technology transfer services, providing turnkey solutions from factory design to trial production. This unique capability positions them as a strategic partner for businesses aiming for self-sufficiency and technological leadership in advanced ceramics.
In conclusion, embracing custom silicon carbide is an investment in resilience, efficiency, and long-term performance. For technical buyers, engineers, and OEMs seeking to conquer the most demanding fluid handling challenges, partnering with a knowledgeable and capable supplier like CAS new materials (SicSino) ensures access to world-class SiC solutions and a pathway to enhanced industrial productivity and a superior competitive edge.
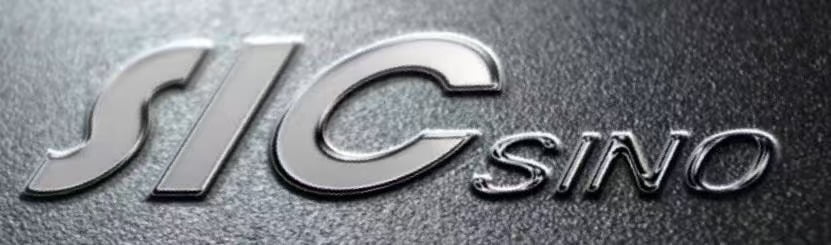
SicSino – CAS new materials
We, CAS new materials(SicSino), have been introducing and implementing silicon carbide production technology since the 2015, assisting the local enterprises in achieving large-scale production and technological advancements in product processes. We have been a witness to the emergence and ongoing development of the local silicon carbide industry.
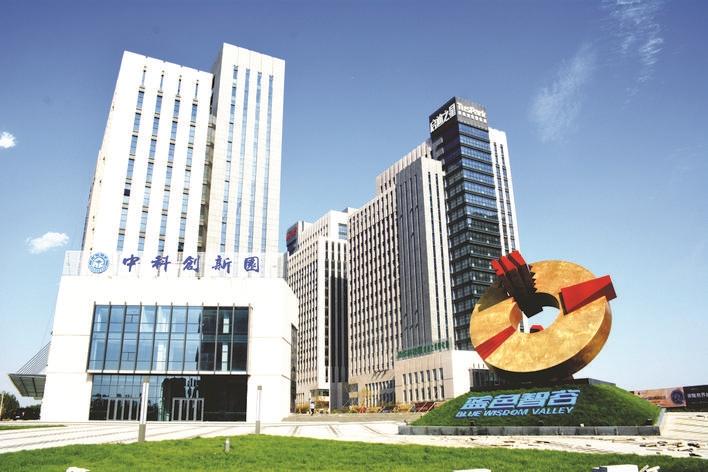