Unyielding Under Fire: The Power of Custom Silicon Carbide for High-Temperature Components
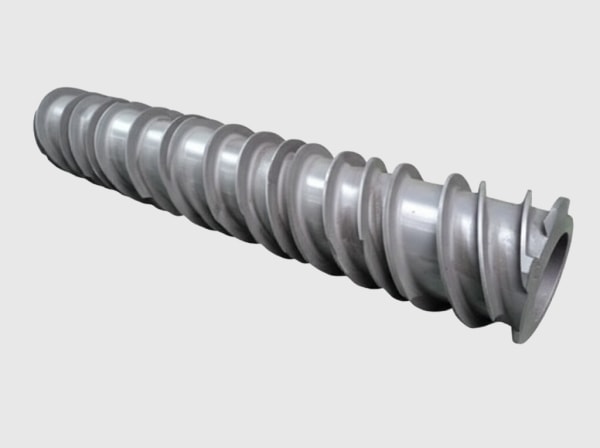
Share
In the demanding realm of industrial applications where extreme temperatures are the norm, material selection is paramount. Components must not only withstand intense heat but also maintain their structural integrity, performance, and lifespan. Among the advanced technical ceramics, custom silicon carbide (SiC) emerges as a frontrunner, offering an exceptional combination of properties that make it indispensable for high-temperature components. This blog post delves into the world of custom SiC, exploring its critical role, diverse applications, inherent advantages, and the considerations necessary for harnessing its full potential in high-thermal environments. We will also shed light on how partnering with a knowledgeable supplier, like CAS new materials (SicSino), rooted in the heart of China’s SiC manufacturing hub, can elevate your high-temperature applications.
Introduction: The Critical Role of Custom Silicon Carbide in High-Temperature Environments
Custom silicon carbide products are engineered ceramic components specifically designed and manufactured to meet the precise requirements of high-performance industrial applications, particularly those involving extreme temperatures. Unlike standard, off-the-shelf ceramic parts, custom SiC components are tailored in terms of composition, shape, size, and surface finish to deliver optimal performance under specific operating conditions. This customization is crucial because, in high-temperature environments, even slight variations in material properties or design can significantly impact efficiency, reliability, and safety.
The indispensability of SiC in these settings stems from its intrinsic material characteristics. Silicon carbide is a covalently bonded material, giving it exceptional strength and hardness, which it retains even at temperatures exceeding 1500circC (2732circF). Its high thermal conductivity, coupled with low thermal expansion, results in excellent thermal shock resistance, allowing SiC components to endure rapid temperature fluctuations without cracking or failing. Furthermore, its superior chemical inertness ensures resistance to corrosion and oxidation, even in aggressive, high-temperature atmospheres. These properties make custom SiC components essential for applications where other materials would degrade, melt, or lose their critical functionalities. Industries rely on engineered SiC parts for everything from furnace linings and kiln furniture to heat exchangers and semiconductor processing equipment, where unwavering performance under thermal stress is non-negotiable.
Key Industries Benefiting from High-Temperature Silicon Carbide Components
The exceptional thermal stability and mechanical robustness of silicon carbide make it a preferred material for components operating under extreme heat across a multitude of sectors. The ability to customize SiC parts further enhances its applicability, allowing engineers to design solutions for specific high-temperature challenges.
Semiconductor Manufacturing: The semiconductor industry relies heavily on SiC for components used in thermal processing equipment, such as wafer handling systems, chemical vapor deposition (CVD) chamber parts, and etching equipment.
- High Purity Requirements: Sintered Silicon Carbide (SSiC) is particularly favored for its high purity, preventing contamination of semiconductor wafers.
- Thermal Uniformity: The high thermal conductivity of SiC ensures uniform temperature distribution, critical for consistent wafer processing.
- Plasma Resistance: SiC components exhibit excellent resistance to the corrosive plasma environments common in semiconductor fabrication. Custom SiC wafer chucks, susceptors, and edge rings are vital for achieving the precision and cleanliness demanded.
Aerospace and Defense: In aerospace, SiC is utilized for components in propulsion systems, thermal protection systems, and high-performance braking systems.
- Lightweight Strength: SiC offers a high strength-to-weight ratio, crucial for aerospace applications where weight reduction is paramount.
- Extreme Temperature Tolerance: Components like rocket nozzles, turbine blades, and leading edges for hypersonic vehicles benefit from SiC’s ability to withstand extreme thermal cycling and oxidative environments. Custom SiC ceramic matrix composites (CMCs) are increasingly explored for these demanding roles.
Industrial Furnaces and Kilns: SiC is a staple material for constructing robust and energy-efficient industrial heating equipment.
- Kiln Furniture: Beams, rollers, plates, and supports made from Reaction-Bonded Silicon Carbide (RBSiC or SiSiC) and Nitride-Bonded Silicon Carbide (NBSC) offer long service life due to their excellent load-bearing capacity at high temperatures and resistance to creep.
- Burner Nozzles and Radiant Tubes: SiC’s thermal shock resistance and high emissivity make it ideal for these components, leading to improved energy efficiency and longevity. Custom SiC heating elements and SiC recuperator tubes significantly enhance furnace performance.
Energy Production and Conversion: The energy sector, including power generation and renewable energy systems, leverages SiC for its thermal and mechanical properties.
- Heat Exchangers: SiC’s high thermal conductivity and corrosion resistance are beneficial for heat exchangers operating with aggressive fluids or at high temperatures, such as those in concentrated solar power (CSP) systems or advanced nuclear reactors.
- Power Electronics: While a different application of SiC (as a semiconductor material), it’s worth noting that SiC power devices operate at higher temperatures, voltages, and frequencies than silicon-based devices, leading to more efficient power conversion. This indirectly drives demand for thermally stable packaging and substrate materials.
Chemical Processing and Metallurgy: The harsh chemical and thermal environments in these industries necessitate materials like SiC.
- Pump Components: Seals, bearings, and liners in pumps handling hot, corrosive, or abrasive media benefit from SiC’s wear and chemical resistance.
- Thermocouple Protection Tubes: SiC tubes protect temperature sensors in aggressive melts and atmospheres, ensuring accurate readings and long sensor life. Custom SiC crucibles and linings are also widely used.
The versatility of custom silicon carbide components allows for tailored solutions within these and other emerging high-temperature fields. As industries push the boundaries of temperature and performance, the demand for reliable, custom-engineered SiC solutions, such as those facilitated by CAS new materials (SicSino) through their extensive network and technological expertise, will only continue to grow.
Unlocking Performance: Advantages of Custom SiC for High-Temperature Applications
Choosing custom silicon carbide for high-temperature applications isn’t merely a material selection; it’s an investment in performance, longevity, and operational efficiency. The unique combination of inherent SiC properties, enhanced by the ability to tailor components to specific needs, provides a compelling set of advantages.
- Exceptional Thermal Stability and Strength at High Temperatures: Silicon carbide maintains its mechanical strength and structural integrity at very high temperatures, often exceeding 1500circC (2732circF), where many metals would soften or melt. This high-temperature strength is critical for load-bearing components in furnaces, engines, and reactors. Unlike some ceramics that become brittle or deform, SiC exhibits remarkable stability.
- Benefit: Longer component life, reduced deformation under load, and reliable operation in extreme thermal conditions.
- Superior Thermal Conductivity: SiC possesses high thermal conductivity, meaning it can efficiently dissipate heat. This is advantageous in applications requiring uniform temperature distribution (e.g., semiconductor wafer processing) or rapid heat transfer (e.g., heat exchangers).
- Benefit: Improved thermal management, prevention of hot spots, enhanced energy efficiency in heating and cooling processes, and faster response times in thermal cycling.
- Excellent Thermal Shock Resistance: The combination of high thermal conductivity, low coefficient of thermal expansion, and high tensile strength gives SiC outstanding resistance to thermal shock. It can withstand rapid changes in temperature without cracking or catastrophic failure.
- Benefit: Increased reliability in applications with frequent heating and cooling cycles, such as kiln furniture, burner nozzles, or components in aerospace propulsion.
- Low Coefficient of Thermal Expansion: SiC expands and contracts minimally with temperature changes. This dimensional stability is crucial for maintaining tight tolerances and precise alignments in assemblies operating across a wide temperature range.
- Benefit: Reduced thermal stresses, improved dimensional control, and better fit and performance of complex assemblies at high temperatures.
- High Hardness and Wear Resistance: Silicon carbide is one of the hardest commercially available ceramic materials, second only to diamond and boron carbide. This makes it extremely resistant to abrasion, erosion, and wear, even at elevated temperatures.
- Benefit: Extended service life for components exposed to abrasive particles, high-velocity flows, or sliding contact, such as nozzles, pump seals, and bearings.
- Chemical Inertness and Corrosion Resistance: SiC exhibits excellent resistance to a wide range of corrosive chemicals, including strong acids and bases, even at high temperatures. It also shows good resistance to oxidation, particularly the dense Sintered SiC grades.
- Benefit: Suitability for use in aggressive chemical environments, such as chemical reactors, flue gas desulfurization systems, and components handling molten metals. This leads to reduced maintenance and replacement costs.
- Customization for Optimized Performance: The ability to create custom SiC parts means that designs can be optimized for specific thermal profiles, mechanical loads, and chemical environments. This includes complex geometries, specific surface finishes, and integration with other components. CAS new materials (SicSino), with its deep understanding of SiC processing and application, supports businesses in developing these tailored solutions, leveraging the rich manufacturing ecosystem of Weifang City.
The table below summarizes these key advantages:
Property | Advantage for High-Temperature Applications | Impact on Performance |
---|---|---|
Thermal Stability | Maintains strength and form at extreme temperatures | Reliable operation, extended component life |
Thermal Conductivity | Efficient heat dissipation and transfer | Temperature uniformity, energy efficiency, faster cycling |
Thermal Shock Resistance | Withstands rapid temperature changes without cracking | Durability in cyclic thermal conditions, reduced failure rates |
Low Thermal Expansion | Minimal dimensional change with temperature | Dimensional stability, reduced stress, precision |
Hardness & Wear Resistance | Resists abrasion, erosion, and wear | Longer service life in abrasive environments |
Chemical Inertness | Resists corrosion and chemical attack | Suitability for harsh chemical environments, less degradation |
Customizability | Tailored design for specific operational needs | Optimized performance, enhanced system efficiency |
By leveraging these advantages, industries can significantly enhance the reliability and efficiency of their high-temperature processes, making custom silicon carbide a cornerstone material for innovation in extreme environments.

Selecting the Right Material: SiC Grades Optimized for Extreme Heat
Not all silicon carbide is created equal, especially when it comes to performance in extreme thermal environments. Different manufacturing processes yield SiC grades with varying microstructures, densities, and impurity levels, all of which influence their high-temperature behavior. Choosing the optimal SiC grade is crucial for ensuring component longevity and operational success. CAS new materials (SicSino) possesses extensive knowledge of these materials and can guide you in selecting the most suitable grade, leveraging their access to a wide array of technologies from the CAS (Chinese Academy of Sciences) and the specialized production capabilities within Weifang, China’s SiC hub.
Here are some common SiC grades and their suitability for high-temperature components:
Reaction-Bonded Silicon Carbide (RBSiC or SiSiC – Silicon Infiltrated SiC):
- Manufacturing: Produced by infiltrating a porous preform of SiC grains and carbon with molten silicon. The silicon reacts with the carbon to form new SiC, which bonds the original grains. Typically contains 8-15% free silicon.
- High-Temperature Properties:
- Maximum service temperature is limited by the melting point of silicon (around 1410circC or 2570circF). Above this, strength decreases significantly.
- Good thermal shock resistance due to relatively high thermal conductivity.
- Excellent wear and corrosion resistance.
- Can be formed into complex shapes with relative ease and lower cost compared to SSiC.
- Best Suited For: Kiln furniture (beams, setters, rollers), burner nozzles, radiant heater tubes, wear-resistant liners, and applications where cost and complex shapes are primary concerns, and the operating temperature remains below the silicon melting point.
- CAS new materials (SicSino) Advantage: Leveraging the extensive SiC production in Weifang, SicSino can facilitate cost-effective sourcing and customization of RBSiC components for various furnace and industrial applications.
Sintered Silicon Carbide (SSiC or S-SiC):
- Manufacturing: Produced by sintering fine SiC powder at very high temperatures (typically above 2000circC or 3632circF) with sintering aids (e.g., boron and carbon). This results in a dense, single-phase SiC material with minimal or no free silicon.
- High-Temperature Properties:
- Excellent high-temperature strength and creep resistance, maintaining properties well above 1600circC (2912circF).
- Superior chemical resistance, including resistance to oxidation at high temperatures.
- Very high hardness and good wear resistance.
- High thermal conductivity.
- Best Suited For: The most demanding high-temperature applications requiring maximum strength, purity, and corrosion resistance. Examples include advanced heat exchanger tubes, semiconductor processing components (susceptors, chamber parts), chemical pump seals and bearings operating at high temperatures, and components for waste incineration.
- CAS new materials (SicSino) Advantage: SicSino’s connection to the CAS National Technology Transfer Center provides access to advanced SSiC processing technologies, ensuring high-purity and high-performance components for critical applications.
Nitride-Bonded Silicon Carbide (NBSC):
- Manufacturing: SiC grains are bonded by a silicon nitride (Si_3N_4) phase. This is often achieved by nitriding a mixture of SiC and silicon powder.
- High-Temperature Properties:
- Good thermal shock resistance and moderate strength at high temperatures.
- Excellent resistance to molten non-ferrous metals like aluminum.
- Good wear resistance.
- Best Suited For: Applications in the non-ferrous metals industry, such as thermocouple protection tubes, riser stalks for low-pressure die casting, and furnace linings in contact with molten aluminum. Also used for some types of kiln furniture.
Other Specialized Grades:
- Graphite-Loaded SiC: Incorporates graphite to improve thermal shock resistance and machinability, sometimes at the expense of maximum operating temperature or strength.
- Porous SiC: Designed for applications like diesel particulate filters (DPFs) or hot gas filtration, offering controlled porosity while retaining high-temperature stability.
The selection process involves a careful analysis of the operating temperature, thermal cycling conditions, mechanical loads, chemical environment, and cost considerations.
SiC Grade | Max. Service Temp. (approx.) | Key High-Temp Strengths | Common High-Temp Applications |
---|---|---|---|
RBSiC (SiSiC) | sim1380circC | Good thermal shock resistance, complex shapes, cost-effective | Kiln furniture, burner nozzles, radiant tubes, wear parts |
SSiC (S-SiC) | 1600circC | Highest strength & creep resistance at high temp, high purity, excellent corrosion resistance | Semiconductor parts, heat exchangers, advanced chemical processing |
NBSC | sim1400circC−1550circC | Excellent resistance to molten non-ferrous metals, good thermal shock | Aluminum industry components (riser tubes, protection tubes), kiln furniture |
Working with a supplier like CAS new materials (SicSino) provides access to expert guidance in navigating these choices. Their team, backed by the scientific prowess of the Chinese Academy of Sciences and the vast manufacturing capabilities of the Weifang SiC cluster, can help identify or develop the precise custom SiC grade required to optimize performance and longevity in your specific high-temperature application. Their focus on material, process, and design technologies ensures that the selected grade will be manufactured to the highest quality standards.
Engineering for Endurance: Design and Manufacturing Considerations for High-Temperature SiC Parts
Creating silicon carbide components that reliably endure extreme temperatures requires more than just selecting the right SiC grade; it demands careful engineering and sophisticated manufacturing practices. The inherent brittleness of ceramics, coupled with the severe stresses induced by high-temperature operations, necessitates a design philosophy that accommodates these challenges. CAS new materials (SicSino), with its access to a domestic top-tier professional team specializing in customized SiC production and an integrated process from materials to products, plays a crucial role in guiding clients through these complexities.
Key Design Considerations for High-Temperature SiC Components:
- Thermal Stress Management:
- Uniform Heating/Cooling: Design the component and the system it operates in to promote uniform temperature distribution. Avoid sharp temperature gradients that can induce high thermal stresses.
- Radii and Fillets: Incorporate generous radii in corners and avoid sharp edges, which act as stress concentrators. Smooth transitions in geometry are crucial.
- Wall Thickness Uniformity: Aim for consistent wall thicknesses to prevent differential heating and expansion, which can lead to cracking. If variations are necessary, ensure gradual transitions.
- Thermal Expansion Mismatch: When SiC is joined to other materials (e.g., metals), carefully consider the differences in coefficients of thermal expansion (CTE). Design flexible joints or intermediate layers to accommodate differential expansion and prevent stress buildup.
- Mechanical Load Distribution:
- Avoid Point Loads: Distribute mechanical loads over larger areas to reduce localized stress.
- Minimize Tensile Stresses: SiC, like other ceramics, is much stronger in compression than in tension. Designs should aim to keep SiC components under compressive loads where possible.
- Creep Considerations: For components under sustained load at very high temperatures (especially above 1200circC), factor in the potential for creep deformation, particularly with RBSiC. SSiC offers superior creep resistance.
- Geometric Complexity and Manufacturability:
- While advanced forming techniques allow for complex SiC shapes, simpler designs are generally more robust and cost-effective to manufacture.
- Understand the limitations of the chosen manufacturing process (e.g., pressing, slip casting, extrusion, additive manufacturing). CAS new materials (SicSino) can advise on manufacturable designs based on their wide array of process technologies.
- Consider features for handling and installation, especially for large or delicate components.
- Joining and Assembly:
- Joining SiC to SiC or SiC to other materials for high-temperature service is challenging. Techniques include brazing, diffusion bonding, or mechanical clamping. The joint design must accommodate thermal stresses and the operational environment.
- For mechanical joints, consider the use of SiC fasteners or designs that minimize stress on the ceramic parts.
Manufacturing Complexities:
- Powder Processing: The quality and consistency of the initial SiC powder are critical for the final properties of the component.
- Forming: Various techniques are used, each with its pros and cons regarding shape complexity, tolerances, and cost.
- Dry Pressing: Suitable for simple shapes and high volumes.
- Isostatic Pressing: Good for more complex shapes and uniform density.
- Slip Casting & Extrusion: Used for hollow or elongated shapes.
- Additive Manufacturing (3D Printing): Emerging technology for highly complex geometries and rapid prototyping.
- Sintering/Reaction Bonding: These high-temperature processes are crucial for densification and achieving the desired microstructure. Precise control of temperature, atmosphere, and time is essential.
- Machining (Grinding): Due to its extreme hardness, SiC is typically machined in its green (pre-sintered) state or, more commonly, diamond ground after sintering. This is a slow and costly process, so designs should aim to minimize machining requirements. CAS new materials (SicSino)’s measurement and evaluation technologies ensure precision throughout the manufacturing and finishing stages.
CAS new materials (SicSino) offers comprehensive support, from initial design consultation to final product delivery. Their expertise, built upon the technological foundation of the Chinese Academy of Sciences and extensive experience within Weifang’s SiC industry, allows them to assist clients in optimizing designs for manufacturability and high-temperature performance. They understand the nuances of different SiC grades and manufacturing routes, ensuring that custom SiC components are engineered for endurance in the most demanding thermal environments. Their commitment extends to even helping clients establish their own specialized SiC production facilities if desired, showcasing their deep process knowledge.
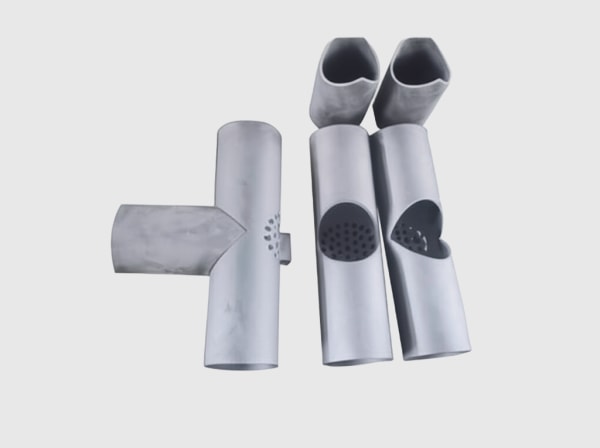
Maximizing Lifespan and Performance: Post-Processing and Surface Treatments for High-Temperature SiC
Once a silicon carbide component has been formed and sintered (or reaction-bonded), various post-processing steps may be necessary to meet the precise dimensional tolerances, surface finish requirements, and enhanced performance characteristics demanded by high-temperature applications. These final touches are critical for maximizing the lifespan and operational efficiency of custom SiC parts. CAS new materials (SicSino), with its integrated process from materials to products and advanced measurement and evaluation technologies, ensures that these post-processing steps are executed with precision.
Common Post-Processing Techniques for SiC Components:
- Grinding:
- Purpose: Due to the extreme hardness of SiC, diamond grinding is the primary method for achieving tight dimensional tolerances and specific geometric features after sintering. It’s used to shape flat surfaces, cylindrical features, and complex contours.
- Considerations for High-Temp Applications: Grinding can introduce microscopic surface flaws that might act as crack initiation sites, especially under thermal stress. Controlled grinding processes that minimize subsurface damage are crucial. The surface finish achieved can also influence emissivity and reactivity at high temperatures.
- Lapping and Polishing:
- Purpose: To achieve exceptionally smooth surface finishes (low Ra values) and high degrees of flatness or parallelism. This is critical for applications like seals, bearings, mirrors for high-temperature optical systems, and semiconductor wafer chucks where surface quality impacts performance and wear.
- Considerations for High-Temp Applications: A highly polished surface can sometimes improve resistance to chemical attack and reduce friction at elevated temperatures. However, the effect on emissivity and thermal shock behavior needs to be considered for specific applications.
- Edge Chamfering and Radiusing:
- Purpose: To remove sharp edges that can be prone to chipping during handling or act as stress concentrators during thermal cycling. Introducing small chamfers or radii can significantly improve the robustness of the component.
- Considerations for High-Temp Applications: This is a vital step for mitigating the risk of crack initiation at edges when components are subjected to thermal shock or mechanical loads at high temperatures.
Surface Treatments and Coatings (Less Common for Bulk SiC but sometimes considered):
While bulk SiC itself offers excellent high-temperature properties, specific surface treatments or coatings might be explored for unique circumstances, though these are more prevalent in SiC fiber composites or thin-film applications.
- Sealing (for RBSiC/SiSiC):
- Purpose: In some Reaction-Bonded SiC grades, if any surface-connected porosity or residual silicon needs to be addressed for specific chemical environments, sealing treatments might be applied. However, for high-temperature use, the sealant material itself must be stable.
- Considerations for High-Temp Applications: The sealant’s thermal stability and compatibility with the SiC and the operating environment are paramount. Often, using a denser grade like SSiC is preferred over relying on sealants for very high-temperature corrosive environments.
- Oxidation Protective Coatings (Environmental Barrier Coatings – EBCs):
- Purpose: Although SiC forms a passive silica (SiO_2) layer that provides good oxidation protection up to around 1600circC, in extremely aggressive oxidative or water vapor environments at ultra-high temperatures (more relevant for SiC/SiC CMCs in gas turbines), specialized EBCs are developed.
- Considerations for High-Temp Applications: For monolithic SiC components in most industrial heating applications, the inherent SiO_2 layer is sufficient. EBCs add complexity and cost and are typically reserved for cutting-edge aerospace or energy applications.
- Glazing (for some Porous or Lower-Grade SiC):
- Purpose: To reduce porosity and improve resistance to chemical attack or gas permeability in certain types of SiC refractories.
- Considerations for High-Temp Applications: The glaze must have a CTE matched to the SiC substrate and be stable at the operating temperature.
Quality Control and Metrology: Throughout these post-processing steps, rigorous quality control is essential.
- Dimensional Verification: Using advanced metrology tools (CMMs, optical comparators, laser scanners) to ensure all dimensions are within the specified tolerances.
- Surface Finish Measurement: Profilometers and other surface metrology tools to verify surface roughness and waviness.
- Non-Destructive Testing (NDT): Techniques like ultrasonic testing or fluorescent penetrant inspection may be used to detect any surface or subsurface flaws introduced during manufacturing or post-processing.
CAS new materials (SicSino) emphasizes the importance of these finishing steps. Their commitment to “measurement & evaluation technologies” as part of their integrated process ensures that custom SiC high-temperature components not only meet the bulk material property requirements but also the critical surface and dimensional specifications necessary for optimal performance and longevity. Their support helps clients achieve the necessary precision for even the most demanding applications, leveraging the skilled workforce and specialized equipment available within the Weifang SiC industrial cluster.
Navigating the Challenges: Optimizing Silicon Carbide for Demanding High-Temperature Operations
While silicon carbide is a remarkable material for high-temperature applications, engineers and procurement managers must be aware of certain challenges and limitations to ensure optimal performance and prevent premature failure. Addressing these proactively through careful design, material selection, and operational protocols is key to harnessing the full potential of custom SiC components. CAS new materials (SicSino), with its deep technological expertise derived from the Chinese Academy of Sciences and its practical experience within the Weifang SiC industry, can provide invaluable assistance in mitigating these challenges.
Common Challenges and Mitigation Strategies:
- Brittleness and Fracture Toughness:
- Challenge: Like most ceramics, SiC is inherently brittle, meaning it has low fracture toughness. It does not yield plastically like metals and can fail catastrophically if subjected to impact loads or excessive tensile stress.
- Mitigation:
- Design: Incorporate generous radii, avoid stress concentrators (sharp corners, notches), and design for compressive loading where possible.
- Material Selection: While all SiC is brittle, some microstructures or composite forms (like SiC/SiC CMCs, though these are a distinct class) can offer improved toughness.
- Handling & Installation: Implement careful handling and installation procedures to avoid mechanical shock or chipping.
- Proof Testing: For critical components, proof testing under conditions exceeding expected operational loads can help weed out parts with critical flaws.
- Oxidation at Very High Temperatures (especially in the presence of water vapor):
- Challenge: SiC forms a protective silicon dioxide (SiO_2) layer upon heating in an oxidizing atmosphere, which is stable and effective up to around 1600circC. However, at even higher temperatures, or in atmospheres containing significant water vapor (“steam oxidation” or “active oxidation”), the SiO_2 layer can become less stable, or volatile silicon monoxide (SiO) can form, leading to material loss.
- Mitigation:
- Grade Selection: Dense Sintered SiC (SSiC) generally offers better oxidation resistance than RBSiC due to the absence of free silicon, which can oxidize preferentially.
- Atmosphere Control: If possible, control the operating atmosphere to minimize water vapor or highly reducing conditions at extreme temperatures.
- Temperature Limits: Operate within the recommended temperature limits for the specific SiC grade and environment.
- Environmental Barrier Coatings (EBCs): For ultra-high temperature applications (e.g., >1600−1700circC in aggressive environments), EBCs may be necessary, though this is typically for advanced aerospace components.
- Slow Crack Growth (Subcritical Crack Growth):
- Challenge: Existing microscopic flaws in a ceramic component can slowly grow under sustained stress, even if that stress is below the material’s short-term fracture strength. This is exacerbated at high temperatures and in certain chemical environments.
- Mitigation:
- High-Quality Material: Use high-quality SiC with minimal inherent flaws. This is where CAS new materials (SicSino)’s commitment to quality from material sourcing to final product becomes crucial.
- Surface Finish: Ensure smooth surface finishes, as surface flaws are often the origin of crack growth. Careful grinding and polishing are important.
- Design for Lower Stress: Maintain operational stresses well below the material’s threshold for slow crack growth.
- Periodic Inspection: For critical applications, non-destructive inspection may be scheduled to monitor for crack development.
- Joining SiC to Other Materials (especially Metals):
- Challenge: The significant difference in Coefficient of Thermal Expansion (CTE) between SiC and most metals creates large stresses at joints when subjected to temperature changes. This can lead to joint failure or fracture of the SiC.
- Mitigation:
- Graded Joints: Use intermediate materials with CTEs between that of SiC and the metal to create a more gradual transition.
- Brazing: Select braze alloys that can wet SiC and accommodate some stress. Active braze alloys containing titanium are often used. The braze joint design is critical.
- Mechanical Clamping: Design compliant mechanical joints that allow for some differential movement.
- Finite Element Analysis (FEA): Use FEA to model and optimize joint designs to minimize stress concentrations. CAS new materials (SicSino)’s design support can incorporate such advanced analysis.
- Machining Complexity and Cost:
- Challenge: The extreme hardness of SiC makes it difficult and expensive to machine. Diamond grinding is typically required, which is a slow process.
- Mitigation:
- Near-Net Shape Forming: Design components and select manufacturing processes (e.g., slip casting, injection molding, additive manufacturing) that produce parts as close to the final dimensions as possible, minimizing the need for extensive grinding.
- Green Machining: Perform some machining when the SiC is in its “green” (unfired) state, when it is much softer, though this provides less precision.
- Optimize Design for Machining: If machining is unavoidable, design features that are easier to grind (e.g., accessible surfaces, simple geometries).
The table below highlights key challenges and common approaches:
Challenge | Primary Concern | Key Mitigation Strategies |
---|---|---|
Brittleness | Catastrophic failure under impact or tensile stress | Design for compression, avoid stress concentrators, careful handling, proof testing |
High-Temp Oxidation/Volatilization | Material loss in aggressive atmospheres | Grade selection (SSiC > RBSiC), atmosphere control, operate within temperature limits |
Slow Crack Growth | Failure under sustained stress over time | High-quality material, smooth surface finish, design for lower stress |
Joining to Dissimilar Materials | CTE mismatch leading to stress and failure | Graded joints, specialized brazing, compliant mechanical designs, FEA analysis |
Machining Complexity & Cost | Difficult and expensive to achieve tight tolerances | Near-net shape forming, green machining, design optimization for machining |
By understanding these challenges and working with experienced suppliers like CAS new materials (SicSino), who can provide insights into material selection, design optimization, and advanced manufacturing techniques, businesses can successfully implement custom silicon carbide components for reliable and long-lasting performance in the most demanding high-temperature industrial operations. Their connection to the comprehensive service ecosystem for technology transfer and commercialization via the CAS National Technology Transfer Center ensures access to cutting-edge solutions.
How to Choose the Right SiC Supplier for High-Temperature Components
Selecting the right supplier for your custom silicon carbide high-temperature components is as critical as choosing the right material grade or design. A capable supplier does more than just manufacture parts; they act as a partner, offering technical expertise, material guidance, quality assurance, and reliable delivery. Given the demanding nature of high-temperature applications, this choice significantly impacts the performance, longevity, and overall success of your project.
Here are key factors to consider when evaluating a potential SiC supplier:
- Technical Expertise and Experience in High-Temperature Applications:
- Depth of Knowledge: Does the supplier have a deep understanding of SiC material science, including the nuances of different grades (RBSiC, SSiC, NBSC, etc.) and their behavior at elevated temperatures?
- Application-Specific Experience: Have they successfully supplied components for applications similar to yours? Can they provide case studies or references?
- Problem-Solving Capabilities: Are they equipped to discuss your specific challenges (e.g., thermal shock, chemical attack, mechanical stress at high temperatures) and recommend or develop tailored solutions?
- CAS new materials (SicSino) Strength: SicSino stands out due to its foundation on the robust scientific and technological capabilities of the Chinese Academy of Sciences (CAS). Their team is described as a “domestic top-tier professional team specializing in customized production of silicon carbide products,” bringing a high level of technical acumen.
- Material Quality and Sourcing:
- Raw Material Control: Where do they source their SiC powders, and what quality control measures are in place for raw materials? The purity and consistency of the starting powder significantly impact the final product.
- Grade Availability: Can they offer a range of SiC grades suitable for various high-temperature requirements, or are they limited to one or two types?
- Traceability: Can they provide material certifications and ensure traceability throughout the manufacturing process?
- Customization and Design Support Capabilities:
- Engineering Collaboration: Are they willing and able to work with your engineering team to optimize designs for manufacturability, performance, and cost-effectiveness in high-temperature environments?
- Range of Technologies: Do they possess a wide array of technologies, covering material development, various forming processes (pressing, casting, etc.), precision machining (grinding), and finishing? CAS new materials (SicSino) explicitly states they possess “material, process, design, measurement & evaluation technologies, along with the integrated process from materials to products.”
- Complexity Handling: Can they manufacture complex geometries and achieve tight tolerances as required by your designs?
- Manufacturing Capabilities and Quality Management Systems:
- Production Facilities: What is the state of their manufacturing equipment and facilities?
- Quality Certifications: Do they hold relevant quality certifications (e.g., ISO 9001)?
- In-Process Quality Control: What quality checks are performed during the manufacturing process, from powder preparation to final inspection?
- Measurement and Evaluation: Do they have advanced metrology equipment to verify dimensions, surface finish, and detect flaws? SicSino highlights their “measurement & evaluation technologies.”
- Location and Supply Chain Reliability:
- Proximity and Logistics: While global sourcing is common, consider the implications for lead times, shipping costs, and communication.
- Hub Advantage: CAS new materials (SicSino) is strategically located in Weifang City, described as “the hub of China’s silicon carbide customizable parts manufacturing,” which accounts for over 80% of China’s total SiC output. This provides access to a mature supply chain and a skilled workforce.
- Supply Assurance: What measures are in place to ensure consistent supply and mitigate disruptions? SicSino’s support for over 10 local enterprises suggests a robust network and influence within this hub, contributing to “more reliable quality and supply assurance within China.”
- Cost-Effectiveness and Lead Times:
- Transparent Pricing: Is the pricing structure clear, and do they offer competitive rates for the quality and customization provided? SicSino aims to offer “higher-quality, cost-competitive customized silicon carbide components in China.”
- Realistic Lead Times: Can they provide and adhere to realistic lead times for prototypes and production volumes?
- Value beyond Price: Consider the total cost of ownership, including component lifespan, performance, and the supplier’s support, rather than just the initial purchase price.
- Commitment to Innovation and Partnership:
- Technology Transfer Capabilities: Is the supplier involved in ongoing research and development? Are they open to technology transfer or collaborative development for unique needs? CAS new materials (SicSino) uniquely offers “technology transfer for professional silicon carbide production, along with a full-range of services (turnkey project)” for clients wishing to establish their own SiC plants, demonstrating profound technological depth.
- Long-Term Relationship: Look for a supplier interested in building a long-term partnership rather than just a transactional relationship.
Evaluating CAS new materials (SicSino) as a Supplier: Based on their provided information, CAS new materials (SicSino) presents a compelling case:
- Strong Technical Backing: Affiliation with the Chinese Academy of Sciences and the National Technology Transfer Center.
- Industry Hub Location: Situated in Weifang, the heart of China’s SiC production.
- Comprehensive Capabilities: Offering an integrated process from materials to design, manufacturing, and evaluation.
- Customization Focus: Specializing in customized SiC products to meet diverse needs.
- Quality and Cost Focus: Aiming for higher quality and cost-competitiveness.
- Unique Offering: Providing technology transfer for establishing SiC production plants.
When choosing a supplier, conduct thorough due diligence. Request samples, visit facilities if possible, and have detailed technical discussions. For high-temperature SiC components, a supplier that combines material expertise, manufacturing excellence, and a collaborative approach, like CAS new materials (SicSino), is invaluable.
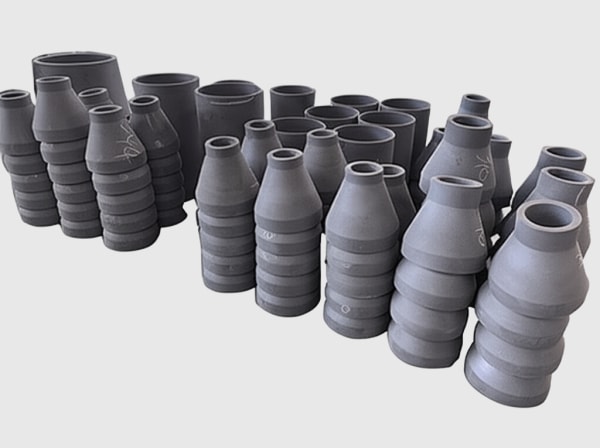
Frequently Asked Questions (FAQ) about Silicon Carbide for High-Temperature Components
Engineers, procurement managers, and technical buyers often have specific questions when considering silicon carbide for their high-temperature needs. Here are some common queries with concise, practical answers.
Q1: What is the maximum operating temperature for silicon carbide components? A: The maximum operating temperature for silicon carbide components significantly depends on the specific grade of SiC and the operating atmosphere. * Reaction-Bonded Silicon Carbide (RBSiC or SiSiC), which contains free silicon, is generally limited to around 1380circC (2516circF). Above this temperature, the free silicon can melt, leading to a loss of strength. * Sintered Silicon Carbide (SSiC), being nearly pure SiC, can operate at much higher temperatures, often up to 1600circC (2912circF) or even higher in inert atmospheres for short durations. Some sources cite usability up to 1700circC (3092circF). * Oxidizing atmospheres can lead to the formation of a protective silica (SiO_2) layer, but at extremely high temperatures (above 1600−1700circC) or in the presence of water vapor, active oxidation or volatilization can occur. * Always consult the supplier’s specifications for the particular grade and consider the specific application environment. CAS new materials (SicSino) can provide detailed guidance on temperature limits for their custom SiC products.
Q2: How does the thermal shock resistance of SiC compare to other ceramics used at high temperatures, like alumina or zirconia? A: Silicon carbide generally exhibits superior thermal shock resistance compared to many other traditional high-temperature ceramics like alumina (Al_2O_3) and zirconia (ZrO_2). This is due to its favorable combination of: * High thermal conductivity: Allows SiC to dissipate heat quickly, reducing internal temperature gradients. * Low coefficient of thermal expansion: Means it expands and contracts less with temperature changes, reducing internal stresses. * High tensile strength: Enables it to withstand higher internal stresses before fracturing.
While alumina is a cost-effective refractory, it has lower thermal conductivity and higher thermal expansion than SiC, making it more susceptible to thermal shock. Zirconia has very low thermal conductivity (making it a good thermal barrier) but also a relatively high thermal expansion, which can be a challenge. Therefore, for applications involving rapid temperature cycling, **custom SiC components** are often the preferred choice.
Q3: Can silicon carbide components be easily machined to complex shapes for high-temperature applications? What are the alternatives if machining is too costly? A: Machining fully sintered silicon carbide is challenging and costly due to its extreme hardness. It typically requires specialized diamond grinding tools and is a slow process. * Machining Limitations: While complex shapes can be achieved through grinding, it significantly adds to the component’s cost and lead time. Design considerations should aim to minimize the amount of post-sintering machining. * Alternatives to Extensive Machining: * Near-Net Shape Forming: Utilizing manufacturing processes that produce parts very close to the final desired shape and dimensions is highly recommended. These include: * Pressing (Dry, Isostatic): For simpler to moderately complex shapes. * Slip Casting & Extrusion: For hollow or elongated uniform cross-section parts. * Injection Molding (SiC-PIM): For smaller, highly complex parts in larger volumes. * Additive Manufacturing (3D Printing of SiC): An emerging technology for creating highly intricate geometries directly, which can significantly reduce or eliminate the need for traditional machining. * Green Machining: Machining the SiC component in its “green” or “bisque” (pre-sintered or partially sintered) state when it is much softer. However, allowances must be made for shrinkage during final sintering, and the achievable tolerances are not as tight as with diamond grinding. * Consultation with Supplier: It’s crucial to discuss design complexity and forming options with your supplier early in the design phase. CAS new materials (SicSino), with their expertise in “material, process, design, measurement & evaluation technologies,” can advise on the most cost-effective manufacturing route for your custom high-temperature SiC components, balancing complexity with manufacturability. They can leverage Weifang’s diverse SiC production capabilities to find optimal solutions.
Conclusion: The Enduring Value of Custom Silicon Carbide in Demanding Industrial Environments
In the relentless pursuit of efficiency, durability, and performance in high-temperature industrial applications, custom silicon carbide stands out as a material of exceptional value. Its unique combination of high-temperature strength, superior thermal conductivity, outstanding thermal shock resistance, and chemical inertness makes it an indispensable solution for components operating in the most challenging thermal environments. From the heart of semiconductor processing equipment to the fiery interiors of industrial furnaces and the cutting edge of aerospace technology, custom SiC parts deliver reliability where other materials falter.
The ability to tailor SiC components to precise specifications—optimizing geometry, material grade, and surface characteristics—further amplifies its benefits, allowing engineers to push operational boundaries and achieve new levels of performance. However, realizing this potential requires not only an understanding of SiC’s properties but also a strategic partnership with a knowledgeable and capable supplier.
CAS new materials (SicSino), rooted in Weifang City, the epicenter of China’s silicon carbide industry, and backed by the formidable scientific and technological resources of the Chinese Academy of Sciences, embodies such a partner. Their comprehensive expertise, spanning material science, advanced process technologies, custom design, and meticulous quality control, empowers businesses to leverage the full advantages of custom SiC. By offering higher-quality, cost-competitive components and even facilitating technology transfer for establishing specialized production facilities, SicSino demonstrates a profound commitment to advancing the application of silicon carbide globally.
Investing in custom silicon carbide components is an investment in operational resilience, extended service life, and enhanced productivity. As industries continue to innovate and demand ever-higher performance from their equipment, the role of advanced ceramics like SiC, supplied by expert partners such as CAS new materials (SicSino), will only become more critical in shaping a future of high-efficiency, high-temperature manufacturing and technology.
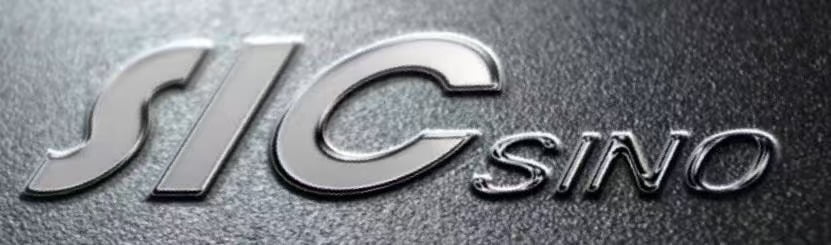
SicSino – CAS new materials
We, CAS new materials(SicSino), have been introducing and implementing silicon carbide production technology since the 2015, assisting the local enterprises in achieving large-scale production and technological advancements in product processes. We have been a witness to the emergence and ongoing development of the local silicon carbide industry.
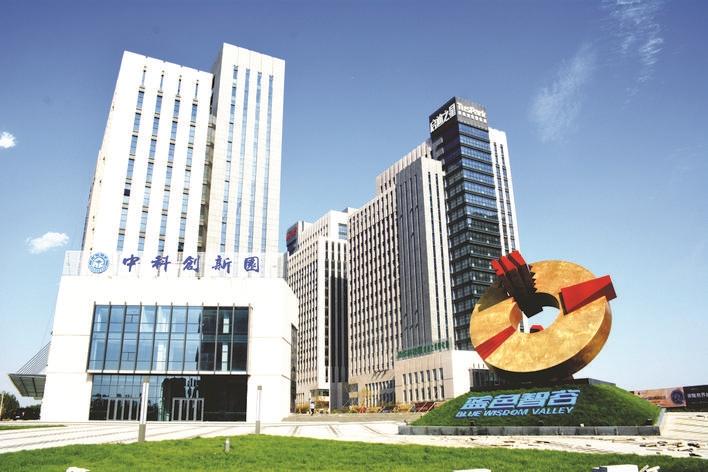