S-SiC
Properties & Application Areas
Silicon Carbide is the Outstanding Choice of High-Performance Materials
Silicon carbide possesses remarkable performance characteristics. It has an extremely high hardness and strong wear resistance. Its thermal conductivity is high, endowing it with excellent heat dissipation performance. Moreover, it exhibits good chemical stability and is resistant to corrosion.
S-SiC
Sintered Silicon Carbide
Usually, the pressureless sintering process is adopted. High-purity silicon carbide powder is mixed with a small amount of additives, and then heated to around 1800°C to 2000°C in a high-temperature furnace for sintering. A dense ceramic structure is formed through the diffusion and fusion of particles.
Properties
Extreme Hardness and Wear Resistance
High-Temperature Stability
Chemical Inertness and Corrosion Resistance
High Thermal Conductivity and Low Expansion
High Purity and Uniform Structure
Application Areas
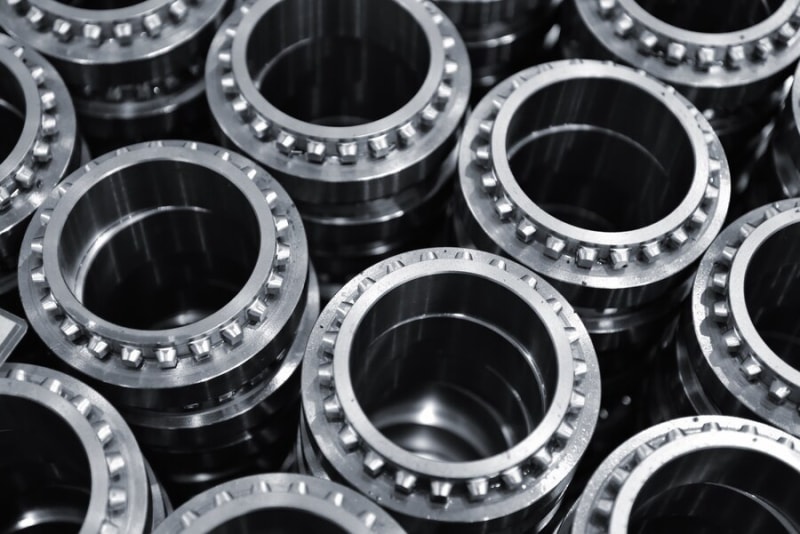
Industrial Manufacturing & Mechanical Engineering
Sealing & Bearing Systems
Mechanical seals for centrifugal pumps/compressors maintain long-term stability under high pressure, temperature, and corrosive media.
Example: SSiC pump seals last 5x longer than traditional materials.
Wear-Resistant Components
Slurry pump impellers in mining and drill bit nozzles in oil drilling resist abrasive and chemical erosion.
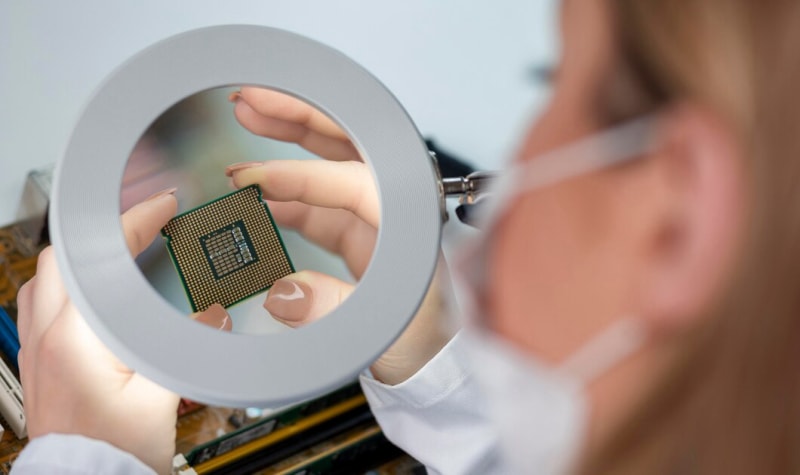
Electronics & Semiconductors
Wafer Processing Equipment
Wafer carriers and etching fixtures in semiconductor manufacturing withstand 1400°C and plasma exposure.
Example: SSiC vacuum chucks ensure nanometer-level precision during wafer processing.
Thermal Management
High-power chip packaging substrates efficiently dissipate heat to extend device lifespan.
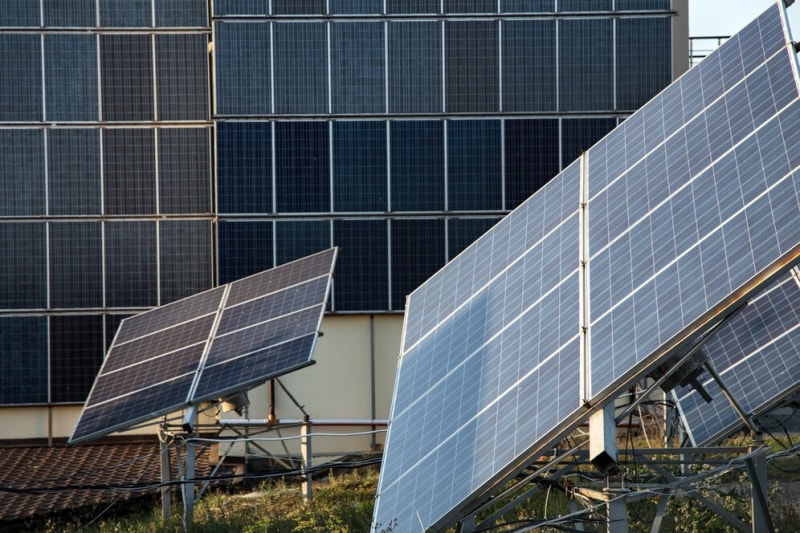
Energy & Environmental Protection
Solar Photovoltaics
Silicon wafer cutting wheels and polysilicon reduction furnace liners resist 1600°C and corrosive gases (e.g., HCl).
Nuclear Energy
Control rod cladding and heat exchanger components in reactors resist radiation and high-temperature fission products.
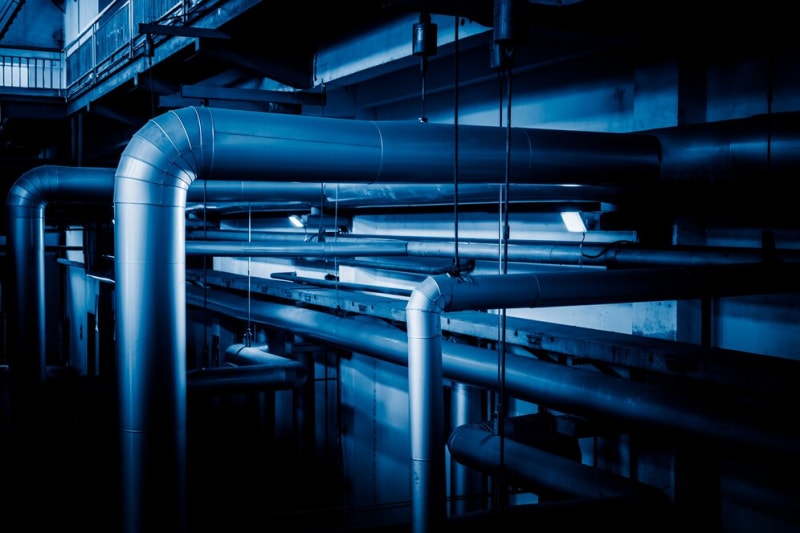
Chemical & Environmental Engineering
Corrosion-Resistant Piping
Pipelines for sulfuric acid/caustic soda transport eliminate rapid metal corrosion.
Filtration Systems
High-temperature gas purification filters for power plants/steel mills withstand 1000°C and particle abrasion.
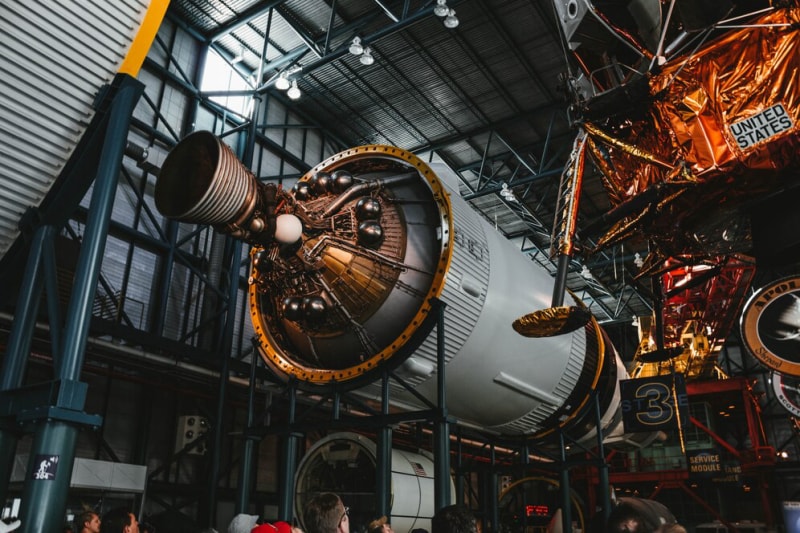
Specialized Fields
Ballistic Armor
Lightweight armor plates (density: 3.1 g/cm³), lighter than aluminum but stronger, used in vehicles and personal protection.
Aerospace
Rocket engine nozzles and satellite structures maintain integrity in extreme temperatures and radiation.
Comparison of Technological Advantages
Property | SSiC | RBSiC (Reaction-Bonded SiC) | HPSiC (Hot-Pressed SiC) |
Purity | >99% | Contains 10-15% free silicon | >99% |
Max Operating Temp | 1800°C (inert) | 1400°C | 1600°C |
Cost | Moderate | Low | High |
Typical Uses | High-temperature structures, semiconductor tools | Wear parts, kiln furniture | Precision molds, optics |
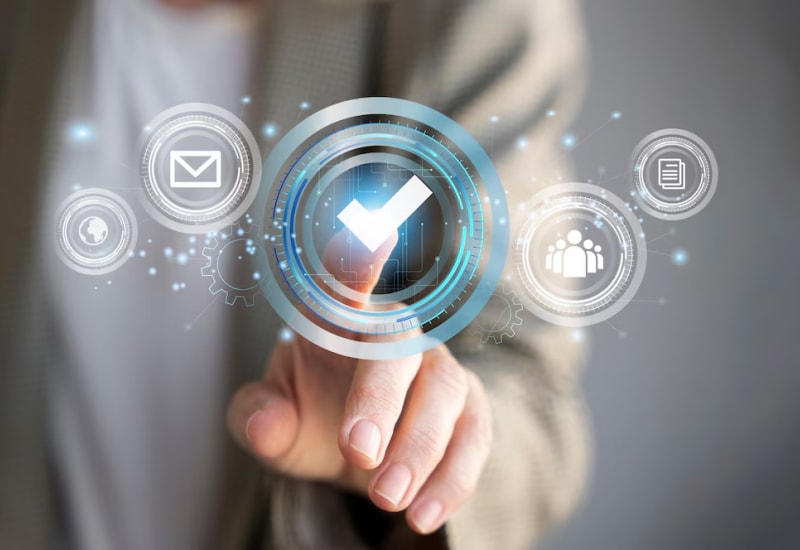
Process & Customization
SSiC is produced via pressureless sintering
High-purity SiC powder (1-10 μm) mixed with trace sintering aids (e.g., B₄C, Al₂O₃-Y₂O₃) is sintered at 1800-2150°C, forming dense structures through particle diffusion.
Customization Capabilities
Complex shapes (e.g., helical pipes, porous filters) with ±0.05 mm dimensional accuracy.
Surface treatments (coating, lapping) for specialized needs (e.g., anti-adhesion, optical flatness).
Case Studies
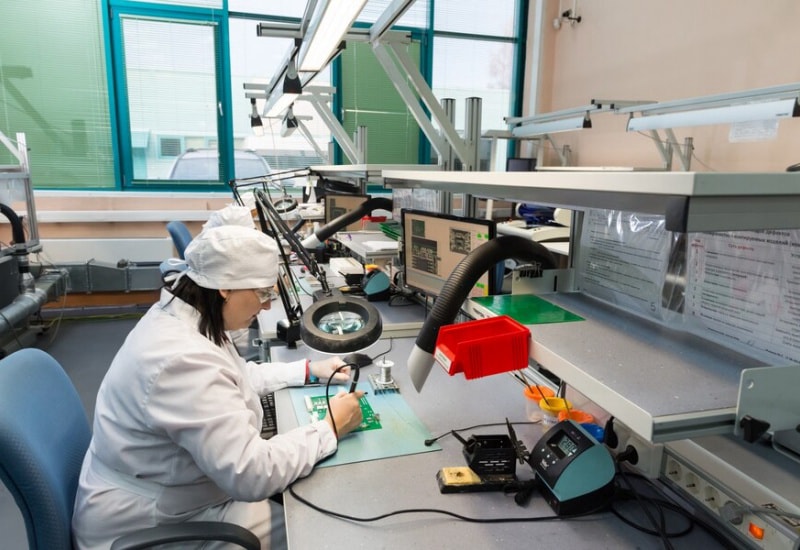
Semiconductor Industry
Leading chip manufacturers use SSiC wafer fixtures, extending tool life to 10x that of traditional quartz in 200mm/300mm wafer annealing.
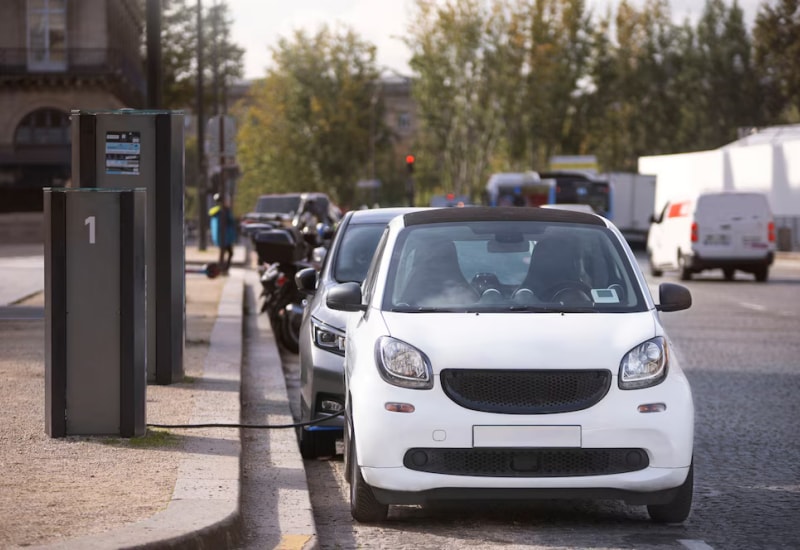
Electric Vehicles
SSiC inverter heat sinks improve motor efficiency by 5%, increasing EV range by 10%.
Product Examples
Customize Your Parts Today!
We possess the wide-ranging technologies for customizing silicon carbide products, such as material technology, processing technology, design technology, and integrated process technology from materials to products. Therefore, we are capable of handling various customization requirements. If you need further customizing solutions or to learn about other process types of silicon carbide products, please feel free to contact our engineering team first.