RB-SiC
Properties & Application Areas
Silicon Carbide is the Outstanding Choice of High-Performance Materials
Silicon carbide possesses remarkable performance characteristics. It has an extremely high hardness and strong wear resistance. Its thermal conductivity is high, endowing it with excellent heat dissipation performance. Moreover, it exhibits good chemical stability and is resistant to corrosion.
RB-SiC
Reaction-Bonded Silicon Carbide
Properties
Physical Properties
High Temperature Resistance: The long-term service temperature in an oxidizing environment is ≤1400°C, and it can reach 1600°C in the short term (a SiO₂ protective film is formed after the oxidation of free silicon).
Thermal Shock Resistance: With a low thermal expansion coefficient (3.5-4.5×10⁻⁶/K), it can withstand the rapid cooling and heating cycle at 1000°C.
Near-Net-Shaping: SiC is directly generated through the reaction between silicon and carbon. Precise shapes (such as porous structures and irregular components) can be formed without complex machining processes.
Mechanical Strength: The flexural strength is 250-300 MPa, the compressive strength is 1800-2000 MPa, and the hardness is HV 18-22 GPa (Mohs hardness 9).
Economy
Low Cost: The production temperature (1400-1600°C) is lower than that of SiSiC (1600-1800°C), and the requirements for raw materials are low. The price is only 1/3 to 1/5 of that of SiSiC.
Process Characteristics
Near-Net-Shaping: SiC is directly generated through the reaction between silicon and carbon. Precise shapes (such as porous structures and irregular components) can be formed without complex machining processes.
High Porosity: It contains 10-15% pores inside, which are filled with free silicon (the content of free silicon is 10-15%). The density is only 2.5-2.7 g/cm³ (lower than 3.0-3.15 g/cm³ of SiSiC).
Chemical Stability
Corrosion Resistance: It has moderate resistance to acids (such as sulfuric acid and nitric acid) and alkaline solutions, but the free silicon is easily corroded by hydrofluoric acid.
Oxidation Resistance: When the temperature is above 1400°C, the free silicon is oxidized to form a SiO₂ glass layer, which inhibits further oxidation.
Typical Application Fields
Industrial Furnaces and Heat Treatment
Kiln Furniture: Push plates and saggars for ceramic sintering (resistant to high temperatures of 1300°C, with a service life of 8-12 months).
Heat Exchangers: High-temperature flue gas recovery devices (resistant to particle erosion and corrosion).
Wear-Resistant and Mechanical Components
Sandblasting Equipment: Silicon carbide sandblasting nozzles (with a service life more than 10 times that of steel products).
Pump and Valve Components: Impellers of slurry pumps and sealing rings (resisting the wear of solid particles).
Environmental Protection and Energy
Flue Gas Desulfurization (FGD): Linings of absorption towers and spray pipes (resistant to corrosive media with a pH value of 2-12).
Coal-Fired Power Plants: Elbows of coal powder conveying pipelines (resistant to wear and high-temperature oxidation).
Chemical Industry and Metallurgy
Reactor Linings: Lining materials for acid-resistant reactors (such as hydrochloric acid synthesis furnaces).
Zinc Smelting: Distillation pots (resistant to the corrosion of metal vapor and high temperatures).
Other Fields
Semiconductor Auxiliary Equipment: Quartz crucible supports (supporting the growth of wafers at high temperatures).
Military Industry and Aerospace: Thermal protective covers for missile seeker heads (resistant to aerodynamic heating at 1600°C in the short term).
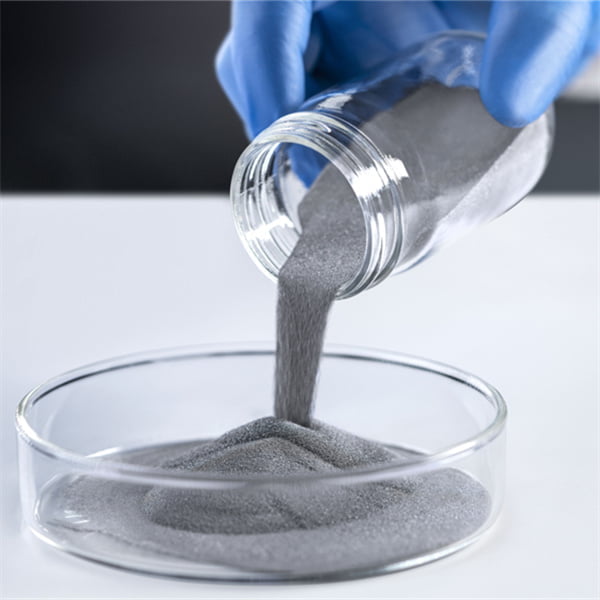
Advantages and Limitations
Advantages | Low-cost mass production of complex shapes |
Excellent thermal shock resistance, suitable for environments with temperature fluctuations | |
Moderate corrosion resistance, meeting most industrial requirements | |
Limitations | The free silicon leads to a decrease in strength at high temperatures (>1400°C, and the oxidation accelerates) |
The low density limits its application in high-pressure or high-purity scenarios | |
It is easily eroded by highly corrosive media such as hydrofluoric acid |
Application Cases
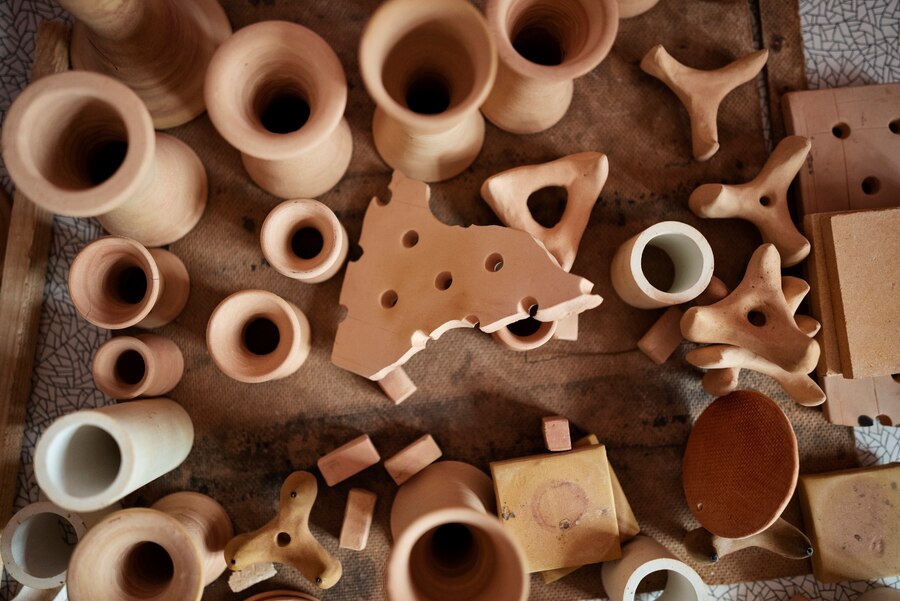
Ceramic Industry
A tile enterprise in China adopted RBSiC push plates to replace traditional corundum kiln furniture. The output per furnace increased by 20%, and the maintenance cost was reduced by 60%.
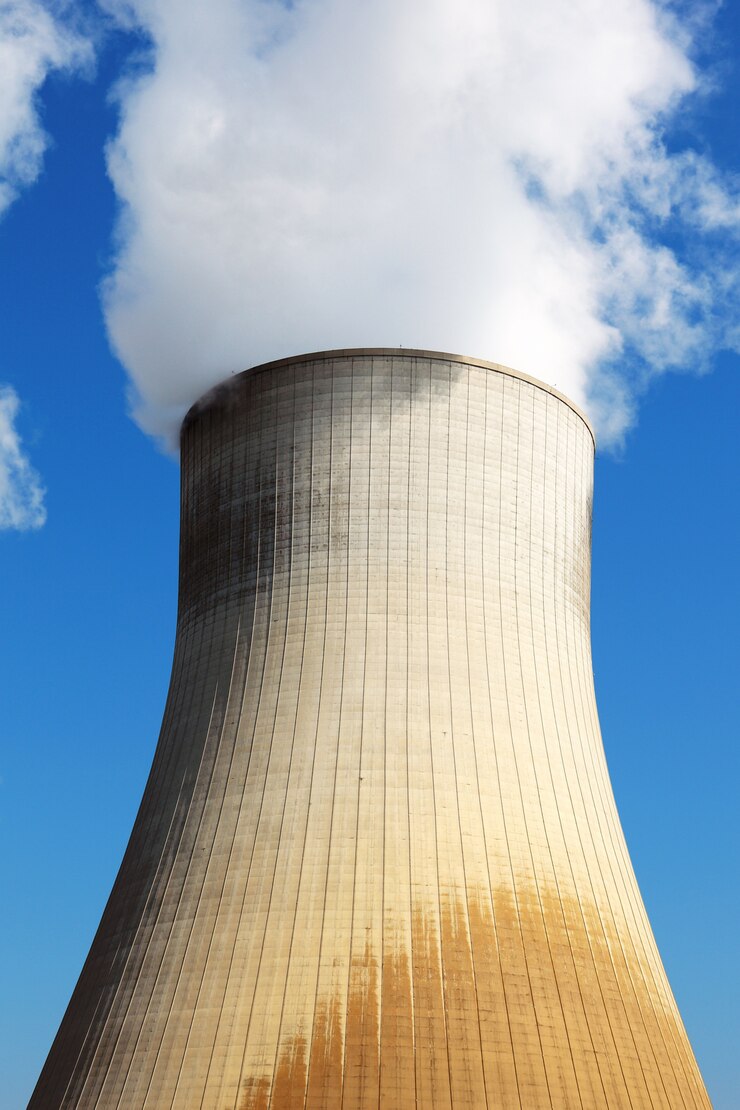
Environmental Protection
The FGD system of a coal-fired power plant in the United States used RBSiC spray pipes, with a service life of 5 years, which is much higher than the 1-2 years of stainless steel pipes.
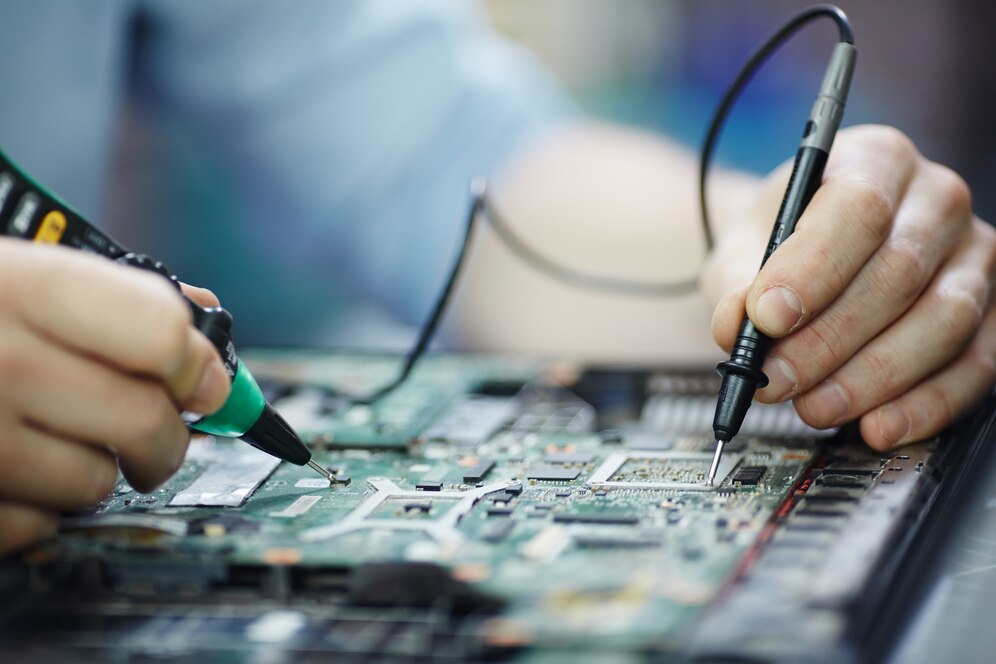
Semiconductor Manufacturing
A wafer factory in Japan used RBSiC quartz crucible supports, which ran continuously for 1000 hours without deformation at 1500°C, and the cost was only 40% of that of SiSiC supports.
Selection Suggestions
Applicable Scenarios | Sensitive to budget and requiring high-temperature oxidation resistance (≤1400°C) |
Needing complex shapes or porous structures (such as gas distributors) | |
Having moderate requirements for wear resistance and corrosion resistance | |
Alternative Solutions | If higher temperatures (>1600°C) or ultra-high purity is required, it is recommended to upgrade to Siliconized Silicon Carbide (SiSiC) or Sintered Silicon Carbide (S-SiC) |
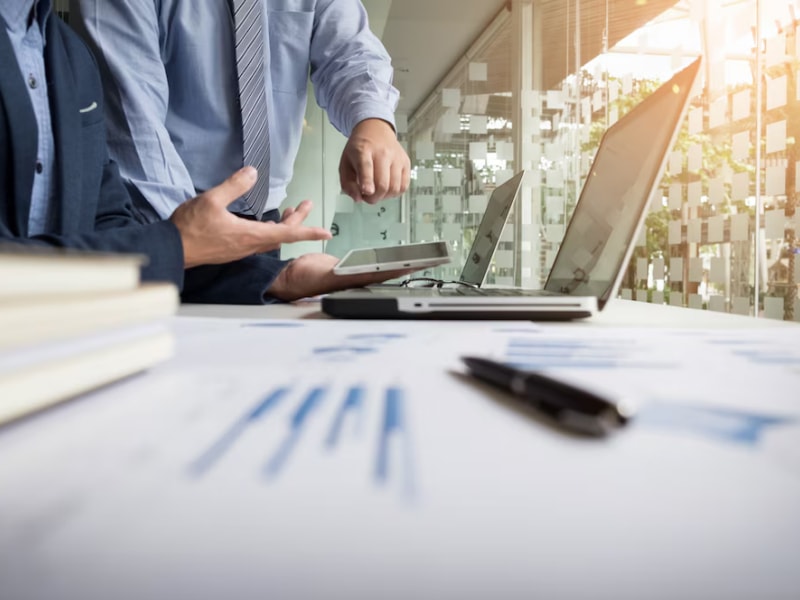
Product Examples
Customize Your Parts Today!
We possess the wide-ranging technologies for customizing silicon carbide products, such as material technology, processing technology, design technology, and integrated process technology from materials to products. Therefore, we are capable of handling various customization requirements. If you need further customizing solutions or to learn about other process types of silicon carbide products, please feel free to contact our engineering team first.