R-SiC
Properties & Application Areas
Silicon Carbide is the Outstanding Choice of High-Performance Materials
Silicon carbide possesses remarkable performance characteristics. It has an extremely high hardness and strong wear resistance. Its thermal conductivity is high, endowing it with excellent heat dissipation performance. Moreover, it exhibits good chemical stability and is resistant to corrosion.
R-SiC
Recrystallized Silicon Carbide
Recrystallized silicon carbide (R-SiC) is a high-performance material formed at a high temperature above 2000°C, second only to diamond in hardness, which retains many excellent properties of SiC, such as high temperature strength, strong corrosion resistance, excellent oxidation resistance, good thermal shock resistance, etc.
Properties
High Hardness
Mohs hardness of 9.2–9.5, second only to diamond and cubic boron nitride, making it suitable for manufacturing wear-resistant components.
High Strength
Maintains high strength at elevated temperatures, with flexural strength at 1000°C reaching 80%–90% of its room-temperature value.
High Thermal Conductivity
Excellent heat dissipation with thermal conductivity of 170–220 W/(m·K) at 20°C, ideal for components requiring efficient heat transfer.
Low Thermal Expansion Coefficient
Thermal expansion coefficient of 4.0×10⁻⁶–4.5×10⁻⁶/°C (20–1000°C), ensuring excellent thermal shock resistance and dimensional stability under rapid temperature changes.
Chemical Stability
Chemically inert to most acids and alkalis at room temperature, only reacting with strong oxidizing agents at high temperatures, suitable for harsh chemical environments.
Corrosion Resistance
Resistant to molten metals and salts, widely applied in metallurgical and chemical industries.
Superior Electrical Properties
High resistivity (1.0×10⁻³–1.5×10⁻³ Ω·m at 1600°C) for use as high-temperature furnace heating elements, with semiconductor characteristics enabling applications in electronic devices.
Application Areas
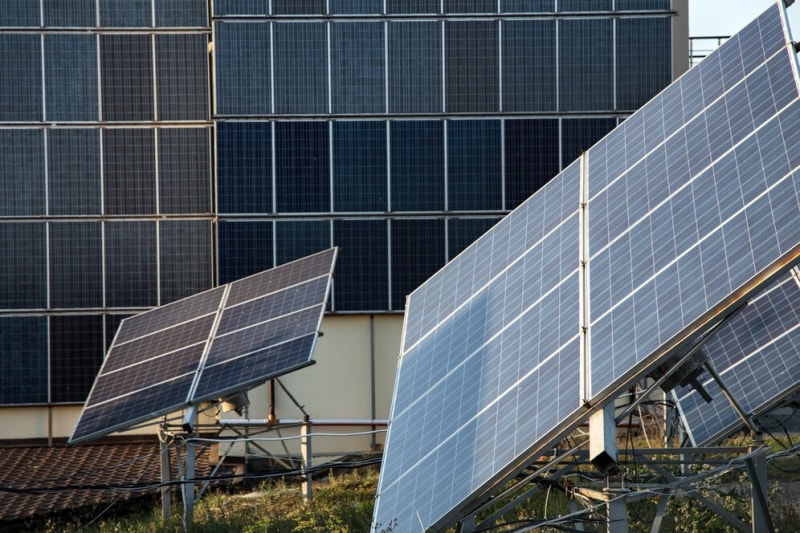
Semiconductor & Photovoltaic Industries
Silicon/SiC Single Crystal Growth
Quartz Crucible Supports: Sustain silicon ingot growth at 1500°C without carbon contamination (0% free silicon).
SiC Crystal Growth Furnace Components: Reduce defect density (e.g., dislocations) in 4H-SiC epitaxial wafer production.
Epitaxy Process Equipment
CVD Chamber Susceptors: Withstand 1600°C to ensure uniform deposition on wafer surfaces.
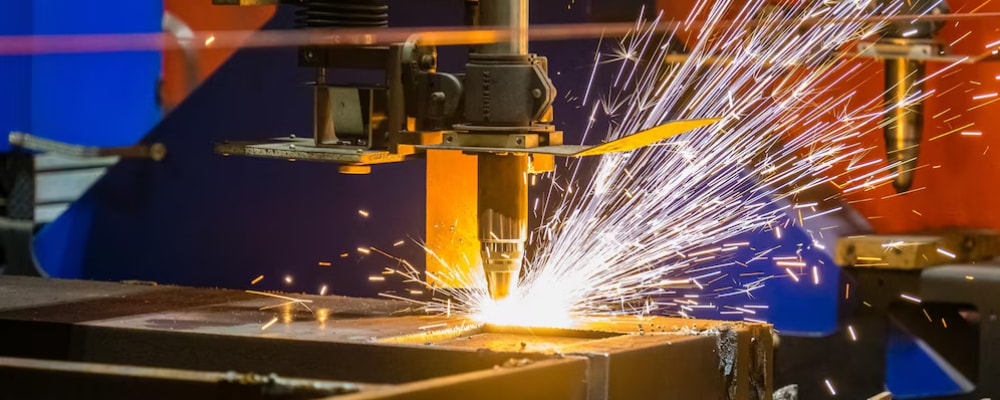
High-Temperature Industrial Equipment
Vacuum Furnace Heating Elements
Replace graphite elements in inert atmospheres up to 2000°C, avoiding carbon contamination (e.g., sapphire single crystal furnaces).
Radiant Tubes & Heat Exchangers
Carburizing furnace radiant tubes last 8 years (vs. 1–2 years for metal tubes); flue gas waste heat recovery units resist particle abrasion.
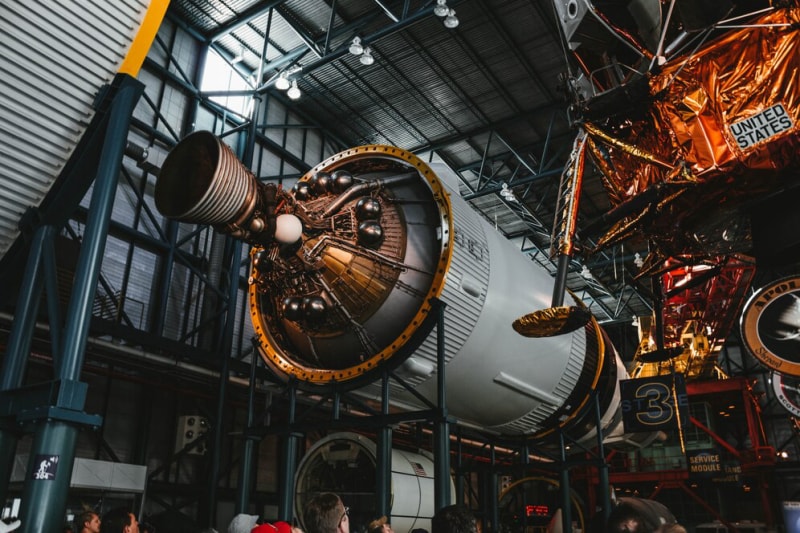
Nuclear Energy & Aerospace
Nuclear Reactor Components
Fuel cladding for high-temperature gas-cooled reactors, resisting neutron irradiation and CO₂ corrosion (≤1600°C).
Spacecraft Thermal Protection
Thermal barrier coating substrates for reentry vehicles, tolerating 1800°C aerodynamic heating (e.g., China’s Chang’e lunar probes).
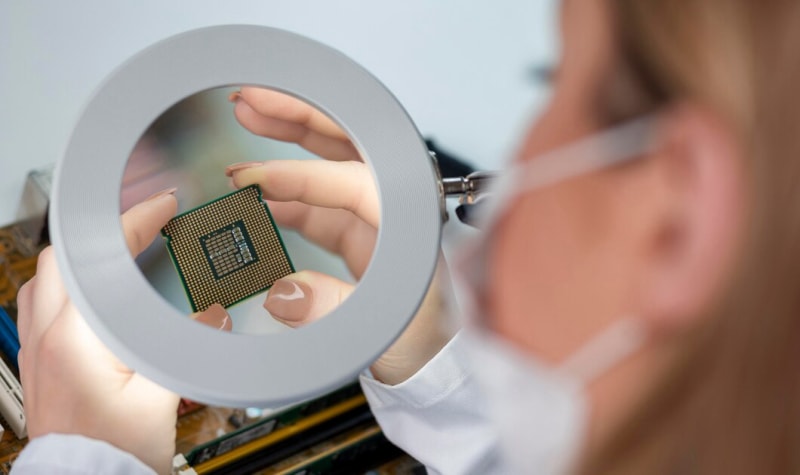
Electronic Device Thermal Management
High-Power Chip Substrates
5G base station amplifier module substrates with 170–220 W/(m·K) thermal conductivity, 3x more efficient than aluminum.
LED Heat Sinks
Replace metals in high-brightness LED packaging to eliminate thermal expansion mismatch.
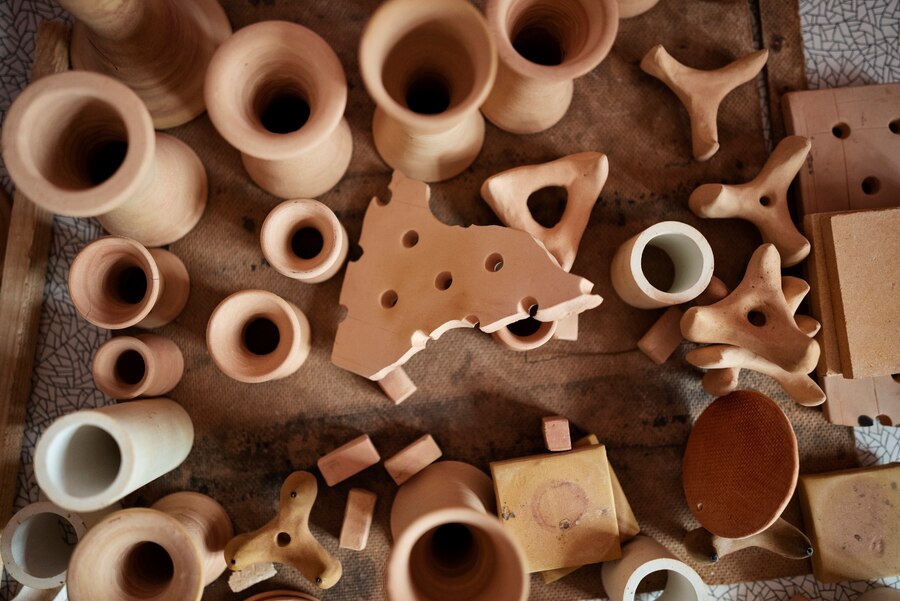
Specialty Ceramics & Optics
Laser Windows & Lenses
CO₂ laser output windows with >95% transmittance, resisting 200W/cm² heat flux.
High-Frequency Device Packaging
Radar radome materials combining high thermal conductivity and low dielectric loss (ε≈4.5).
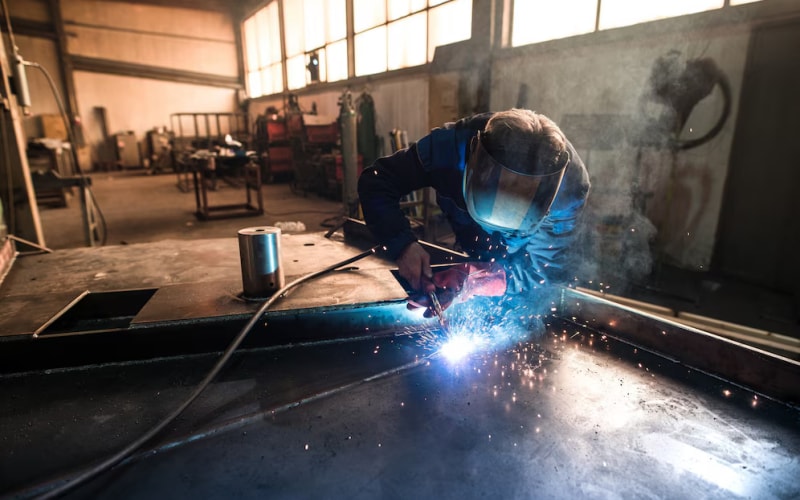
Chemical & Metallurgical Industries
Molten Metal Handling Equipment
Zinc smelting distillation pots resistant to 1000°C zinc vapor corrosion (3x longer lifespan than graphite).
Corrosion-Resistant Reactor Liners
Hydrochloric acid synthesis furnace liners resisting Cl₂ and HCl gas erosion.
Selection Recommendations
Ideal for
① Ultra-high temperatures (>1600°C) or high-purity environments.
② Critical requirements for thermal conductivity and chemical stability.
③ Long-term exposure to extreme thermal cycles (e.g., nuclear reactors).
Alternatives
SiSiC(Siliconized Silicon Carbide) for budgets <1600°C; RBSiC (Reaction-Bonded Silicon Carbide) for complex shapes with cost sensitivity.”
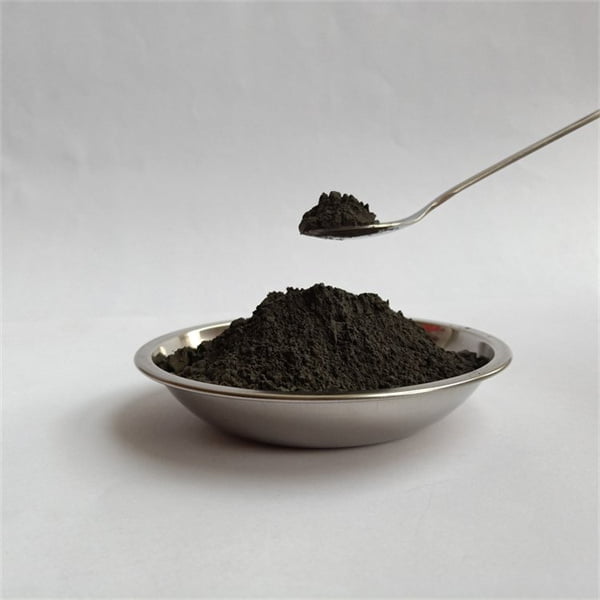
Product Examples
Customize Your Parts Today!
We possess the wide-ranging technologies for customizing silicon carbide products, such as material technology, processing technology, design technology, and integrated process technology from materials to products. Therefore, we are capable of handling various customization requirements. If you need further customizing solutions or to learn about other process types of silicon carbide products, please feel free to contact our engineering team first.