カスタム炭化ケイ素による優れた熱管理の実現
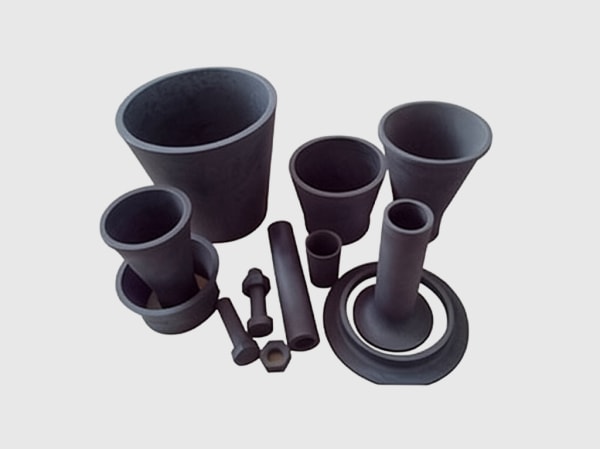
シェア
今日の技術的に高度な産業界では、極限条件下で性能を発揮できる材料への需要がかつてないほど高まっています。電子デバイスが小型化、高性能化し、より高い周波数で動作するにつれて、効率的な熱管理はもはや贅沢品ではなく、不可欠なものとなっています。放熱不良は、性能の低下、信頼性の低下、さらにはコンポーネントやシステムの壊滅的な故障につながる可能性があります。そこで、 カスタム炭化ケイ素(SiC) は、最も要求の厳しいアプリケーションに対して、比類のない熱伝導率、安定性、および機械的堅牢性を提供する、優れた材料として登場します。このブログ記事では、熱管理のためのシリコンカーバイドの世界を掘り下げ、そのアプリケーション、利点、設計上の考慮事項、および CAS新素材(SicSino)のような適切なサプライヤーの選択が、高性能な産業ニーズにとっていかに革新的であるかを探ります。
シリコンカーバイドの優れた熱管理能力の紹介
炭化ケイ素(SiC)は、高度な セラミック 材料であり、物理的および化学的特性の卓越した組み合わせで知られています。シリコンと炭素で構成されるSiCは、非常に強力な共有結合を持ち、高い硬度、強度、そして熱管理にとって重要な優れた熱伝導率を生み出します。銅やアルミニウムのような従来のヒートシンク材料とは異なり、炭化ケイ素は高温でも優れた熱特性を維持するため、他の材料が機能しない環境では不可欠です。
SiCが熱管理に有利な主な理由は、重要なコンポーネントから効率的に熱を伝導する能力があるためです。 その熱伝導率は、特に高い動作温度では、多くの金属よりも大幅に高くなる可能性があります。 この放熱効率は、敏感な電子機器や産業機器の最適な動作温度を維持するのに役立ち、それによって寿命と性能を向上させます。 さらに カスタム炭化ケイ素熱管理ソリューション は、特定のアプリケーション要件に合わせて設計を調整し、複雑なシステムで熱効率を最大化することを可能にします。産業界はますます 高度なセラミックソリューション SiCのような材料に目を向け、性能と信頼性の限界を押し広げています。
で CAS新素材(SicSino)中国の炭化ケイ素製造の中心地である濰坊市に拠点を置く当社は、SiCの変革的な影響を直接目撃してきました。2015年以来、当社はSiCの生産技術の進歩に貢献し、地元企業の大量生産と技術的ブレークスルーの達成を支援してきました。SiC材料科学と製造プロセスに関する当社の深い理解は、高品質な製品を提供する上で独自の立場を確立しており、 カスタムSiC部品 優れた熱管理のために最適化されています。
最適な熱性能のためにSiCを活用する主要なアプリケーション
炭化ケイ素の優れた熱特性は、効率的な放熱が最も重要な幅広い用途に最適な材料となっています。 産業界が高出力密度と運用効率を追求するにつれて、 産業用SiC部品 そして 高温SiC部品 の役割は拡大し続けています。
熱管理におけるSiCの最も重要な応用分野の1つは、 パワーエレクトロニクス. SiC製のMOSFET、SBD、IGBTなどのデバイスは、シリコンベースのデバイスよりも高い電圧、温度、スイッチング周波数で動作できます。 この性能向上により、より多くの熱が発生するため、高度な冷却ソリューションが必要です。SiC基板とヒートスプレッダは、これらの強力なデバイスを最適な動作温度内に維持するために必要な熱経路を提供し、信頼性と寿命を保証します。用途には以下が含まれます。
- 再生可能エネルギーシステム(太陽光、風力)用インバータおよびコンバータ
- 電気自動車(EV)パワーモジュールおよび充電ステーション
- 産業用モータドライブ
- 無停電電源装置(UPS)
熱交換器 は、もう1つの重要な用途を表しています。 化学処理、廃熱回収、金属処理などの高温産業プロセスでは、SiC熱交換器は、高い熱伝導率、優れた耐食性、および極端な温度と熱衝撃に耐える能力により、優れた性能を発揮します。 これにより、金属製の代替品と比較して、より効率的なエネルギー利用とより長い耐用年数が実現します。
の分野では、 LED照明、特に産業用、自動車用、および大規模会場照明で使用される高出力LEDの場合、SiCは優れた基板材料として機能します。 LEDチップによって生成される熱を効率的に放散することは、光出力、色の均一性を維持し、照明システムの寿命を延ばすために不可欠です。 SiCヒートスプレッダ は、ここで重要な役割を果たします。
について 航空宇宙および防衛産業 も、要求の厳しい用途で熱管理のためにSiCに依存しています。 航空電子機器の冷却から宇宙船やミサイルの熱保護システムまで、SiCの軽量性(一部の高温金属と比較して)、高い熱安定性、および機械的強度が非常に高く評価されています。
その他の注目すべき用途には以下が含まれます。
- 半導体製造装置: 正確な温度制御が必要なウェハチャックや処理チャンバー部品などのコンポーネント。
- 高温炉: 熱安定性と耐衝撃性が重要なライニング、窯道具、および発熱体。
- レーザーシステム: 高出力レーザーダイオードおよび光学部品用のヒートシンク。
の多用途性 カスタム炭化ケイ素製品 は、これらの多様な産業全体で非常に具体的な熱的課題に対応できるソリューションを設計できることを意味し、最適な性能と信頼性を保証します。
熱システムにおけるカスタムシリコンカーバイドの利点
熱システムでカスタム炭化ケイ素コンポーネントを選択すると、標準の既製材料が提供できる範囲を超える多くの利点があります。材料特性とコンポーネント設計を特定のアプリケーションニーズに合わせて調整できることは、高度な産業システムで最高の熱性能、寿命、および費用対効果を達成するために不可欠です。主な利点は次のとおりです。
- 卓越した熱伝導率: SiCは高い固有熱伝導率を示し、グレードと製造プロセスに応じて、多くの場合120〜270 W/mK以上になります。これにより、発熱源からの迅速かつ効率的な放熱が可能になり、温度勾配が最小限に抑えられ、過熱が防止されます。これは特に、 高度なセラミックヒートシンク そして SiCヒートスプレッダ が高出力密度電子機器を冷却するように設計されている場合に重要です。
- 低熱膨張係数(CTE): 炭化ケイ素は比較的低いCTEを持ち、シリコンのような半導体材料のCTEとほぼ一致しています。これにより、特に熱サイクル中に、SiCコンポーネントと冷却するデバイスの間の界面での熱機械的応力が最小限に抑えられます。応力が軽減されると、信頼性が向上し、アセンブリの早期故障が防止されます。
- 高温安定性: 熱的および機械的特性が高温で大幅に低下する金属とは異なり、SiCは1000℃を超える温度(および制御された雰囲気の特定のグレードでは最大1650℃以上)でも、優れた熱伝導率、強度、および構造的完全性を維持します。これにより、炉のコンポーネントや排気システムなど、極端な熱を伴うアプリケーションに最適です。
- 優れた機械的強度と硬度: SiCは非常に硬く、強い材料であり、摩耗、摩耗、および侵食に耐性があります。これにより、SiC製の熱管理コンポーネントは、高い圧力または粒子を含む流れを含む過酷な動作条件に、大幅な劣化なしに耐えることができます。この耐久性は、より長い耐用年数と削減されたメンテナンス要件に貢献します。
- 優れた化学的不活性と耐食性: 炭化ケイ素は、高温でも、広範囲の腐食性化学物質、酸、およびアルカリに対して非常に耐性があります。これにより、化学処理プラントまたは腐食性冷却材を含むアプリケーションに見られるような、化学的に攻撃的な環境での熱管理に適しています。
- カスタマイズによる設計の柔軟性: カスタムSiC製造 エンジニアが複雑な形状を設計し、熱に関する課題に対して最適化された機能を組み込むことを可能にします。これには、液体冷却用の複雑なチャネル設計、精密な取り付け機能、および熱伝達を向上させるための最適化された表面積が含まれます。 CAS新素材(SicSino)は、SiCの加工と設計に関する深い専門知識を持ち、このようなカスタムソリューションの提供に優れています。
- 電気抵抗率(調整可能): SiCには半導体性のものもあれば、非常に抵抗率の高いものもあります。この特性は、熱伝導率に加えて電気絶縁が必要な用途で有利となり、短絡や電気的干渉を防ぎます。
下の表は、一般的な代替材料と比較した、熱システムにおけるSiCの主な利点をまとめたものです。
プロパティ | 炭化ケイ素(SiC) | アルミニウム(Al) | 銅(Cu) | アルミナ (Al2O3) |
---|---|---|---|---|
熱伝導率 | 高~非常に高い(120~270+ W/mK) | 高い(約200~240 W/mK) | 非常に高い(約400 W/mK) | 中程度(20~30 W/mK) |
最高使用温度 | 非常に高い(>1000℃) | 低い(<200℃) | 中程度(<300℃) | 非常に高い(>1500℃) |
CTE適合性(Si) | グッド | 悪い | 悪い | フェア |
機械的強度 | 非常に高い | 中程度 | 中程度 | 高い |
耐食性 | 素晴らしい | 可(酸化膜を形成) | 不可(酸化する) | 素晴らしい |
電気抵抗率 | 調整可能(半導体性~高抵抗率) | 導電体 | 導電体 | 高い絶縁体 |
カスタマイズを通じてこれらの固有の利点を活用することで、企業は熱管理システムの性能、信頼性、効率を大幅に向上させ、それぞれの市場で競争優位性を得ることができます。
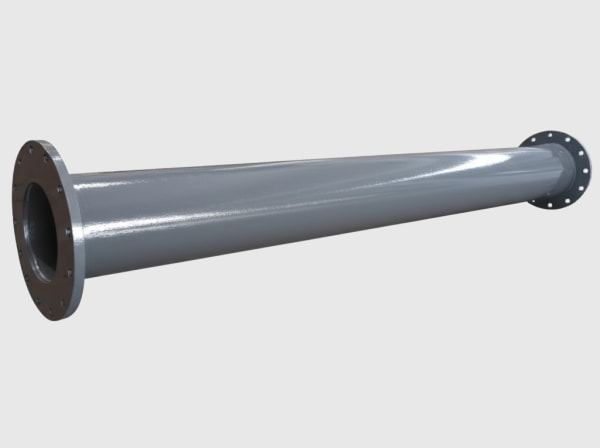
熱管理に推奨されるシリコンカーバイドグレード
炭化ケイ素は単一の材料ではありません。さまざまな製造プロセスを経て製造され、それぞれ独自の特性を示すさまざまなグレードが存在します。 適切なSiCグレードを選択することは、熱管理性能を最適化するために不可欠であり、機械的強度、コスト、および製造可能性も考慮する必要があります。 CAS新素材(SicSino)は、濰坊市のSiC製造クラスターにおける豊富な経験を持ち、お客様を理想的な カスタムSiCグレード へと導く専門知識を提供します。
以下に、熱管理によく推奨されるSiCグレードをいくつか示します。
- 反応結合炭化ケイ素(RBSiCまたはSiSiC - Silicon Infiltrated SiC):
- 製造: SiC粒子と炭素の多孔質プリフォームに溶融ケイ素を浸透させて製造されます。ケイ素は炭素と反応して追加のSiCを形成し、それが最初の粒子を結合します。残りの細孔は通常、遊離ケイ素で満たされます。
- プロパティ
- 良好な熱伝導率(通常120~180 W/mK)。
- 優れた耐熱衝撃性。
- 高い強度と耐摩耗性。
- 良好な寸法安定性と、厳しい公差で複雑な形状を製造する能力。
- 使用温度は通常、遊離ケイ素の融点(約1410℃)によって制限されます。
- 熱管理アプリケーション: 熱交換器、バーナーノズル、窯道具、良好な熱放散を必要とする耐摩耗性部品、ポンプ部品。
- 検討する: 遊離ケイ素の存在は、特定の高腐食性環境またはケイ素の融点を超える非常に高い温度では制限となる可能性があります。
- 焼結炭化ケイ素(SSiC):
- 製造: 微細なSiC粉末と焼結助剤(通常はホウ素や炭素などの非酸化物)を混合して作られます。次に、不活性雰囲気中で非常に高い温度(2000℃以上)で成形および焼結され、緻密な単相SiC材料になります。
- プロパティ
- 非常に高い熱伝導率(高純度グレードでは200~270 W/mKを超える可能性があります)。
- 優れた高温強度と耐クリープ性(最大1600℃以上で使用可能)。
- 優れた耐腐食性と耐エロージョン性。攻撃的な化学物質に対しても同様です。
- 高い硬度と耐摩耗性。
- 熱管理アプリケーション: 高性能ヒートシンク、パワーエレクトロニクス用基板、炉部品、シール面、ベアリング、半導体製造装置用部品。
- 検討する: より高い処理温度と原材料の純度要件のため、通常、RBSiCよりも高価です。その極端な硬さのため、機械加工はより困難になる可能性があります。
- 窒化物結合炭化ケイ素(NBSiC):
- 製造: SiC結晶粒は窒化ケイ素(Si3N4)相によって結合されている。
- プロパティ
- 中程度の熱伝導率。
- 優れた耐熱衝撃性。
- 溶融金属および摩耗に対する良好な耐性。
- 熱管理アプリケーション: 窯道具、非鉄金属接触用部品、るつぼ。
- 検討する: 一般に、SSiCまたはRBSiCと比較して熱伝導率は低くなります。
- 化学気相成長炭化ケイ素(CVD-SiC):
- 製造: 化学気相成長法によって製造され、超高純度の理論的に高密度のSiCコーティングまたはバルク材料が得られます。
- プロパティ
- 潜在的に非常に高い熱伝導率(300 W/mKを超える可能性があります)。
- 卓越した純度と耐薬品性。
- 他の基板上に薄膜またはコーティングを生成できます。
- 熱管理アプリケーション: ハイエンドの半導体製造部品、光学部品、要求の厳しい熱環境向けの保護コーティング。
- 検討する: 他のSiCグレードと比較して、大幅に高価であり、通常、サイズと厚さが制限されます。
SiCグレードの選択は、アプリケーションの熱要件、機械的応力、化学環境、動作温度、および予算の徹底的な分析によって異なります。 CAS新素材(SicSino) は、中国有数のSiC生産拠点における地位と、中国科学院(CAS)との連携を活用して、これらのSiCグレードの包括的な範囲を提供し、最適な材料選択を保証するための専門的なコンサルティングを提供します。 カスタムSiC熱管理ソリューション。当社の多様な製造技術へのアクセスにより、最も適切で 中国でコスト競争力のあるカスタマイズされた炭化ケイ素部品.
SiCグレード | 一般的な熱伝導率(W/mK) | 最高使用温度(概算) | 熱管理の主な利点 | 一般的な熱アプリケーション |
---|---|---|---|---|
RBSiC / SiSiC | 120 – 180 | 1350〜1400℃ | 優れた耐熱衝撃性、複雑な形状、費用対効果 | 熱交換器、窯道具、一般的な熱部品 |
SSiC | 200 – 270+ | 1600〜1700℃ | 最高の熱伝導率、優れた耐腐食性と耐熱性 | パワーエレクトロニクス基板、高性能ヒートシンク |
NBSiC | 50 – 100 | 1400〜1500℃ | 優れた耐熱衝撃性、溶融金属耐性 | 窯部品、非鉄金属接触 |
CVD-SiC | >300 | >1600∘C | 超高純度、最高の熱伝導率(理論値) | 半導体処理、特殊光学部品、コーティング |
各グレードのニュアンスを説明し、選択プロセスを支援できる知識豊富なサプライヤーと協力することは、望ましい熱性能とシステム全体の成功を達成するために最も重要です。
効果的な放熱のためのカスタムSiCコンポーネントの設計
カスタム炭化ケイ素部品の設計は、放熱効果を最大化する上で極めて重要な役割を果たします。SiCの固有の材料特性は優れていますが、綿密に考え抜かれた設計により、これらの特性が特定の熱管理システム内で最大限に活用されることが保証されます。エンジニアおよび調達担当者は、 カスタムSiC製造 を指定する際に、いくつかの重要な側面を考慮する必要があります。 SiC製造設計ガイドライン に準拠することで、性能を大幅に向上させ、コストを削減できます。
主な設計上の考慮事項:
- 熱流のための形状の最適化:
- 表面積の最大化: ヒートシンクなどの部品の場合、冷却媒体(空気または液体)にさらされる表面積を増やすと、対流熱伝達が向上します。これは、フィン、ピン、または複雑な格子構造によって実現できます。
- 熱経路長の最小化: 熱が熱源から冷却媒体に移動する経路が短く、より直接的であるほど、熱抵抗は低くなります。効率的な伝導経路を確保するように部品を設計します。
- 熱拡散の検討: 熱源が小さく集中している場合、SiC部品は、この熱を最終的なヒートシンクまたは冷却流体に伝達する前に、より広い領域に効果的に拡散するように設計する必要があります。SiCの高い熱伝導率は、これに特に役立ちます。
- 熱応力の管理:
- CTEの不整合: SiCはシリコンと比較して良好なCTEを持つものの、アセンブリ内の他の材料(例:金属製ハウジングやPCB)との不整合は、熱サイクル中に応力を誘発する可能性があります。設計には、これに対応するための機能、例えば、コンプライアントな界面材料や応力緩和構造などを組み込む必要があります。
- 角や応力集中部: 鋭角な内部角や断面の急激な変化は避けてください。これらは応力集中点となり、特にSiCのような脆性材料では、亀裂につながる可能性があります。大きな半径を推奨します。
- 均一な温度分布: SiCコンポーネント全体でより均一な温度分布を促進し、内部熱応力を最小限に抑える設計を目指してください。
- 界面材料と組み立て:
- 熱界面材料(TIM): SiCコンポーネントと熱源(または熱経路の他の部分)との間の界面における熱抵抗は非常に重要です。適切なTIM(例えば、熱グリース、相変化材料、導電性接着剤、またはろう付け用の金属層)を選択することは、この界面抵抗を最小限に抑えるために不可欠です。SiCコンポーネントの表面仕上げもここで重要な役割を果たします。
- 取り付けとクランプ: SiCコンポーネントの取り付けまたはクランプの方法は、熱接触と機械的応力の両方に影響を与える可能性があります。均一な圧力分布を確保し、点荷重を避けてください。
- 既存システムとの統合:
- 形状、適合性、機能: カスタム設計は、より大きなシステムにシームレスに統合される必要があります。これには、サイズ、重量、取り付け穴、および該当する場合は流体フローの接続に関する考慮事項が含まれます。
- 製造性: 最適な熱性能を目指すと同時に、設計は妥当なコストとリードタイムの制約内で製造可能である必要があります。複雑な機能は、製造の難易度とコストを増加させる可能性があります。経験豊富なSiCメーカーとの早期の相談は、 CAS新素材(SicSino) 非常に有益です。中国科学院(CAS)の技術力に支えられた濰坊市の当社のチームは、製造容易性を考慮した設計(DFM)に関する貴重なサポートを提供できます。
- 流体ダイナミクス(液冷システムの場合):
- チャネル設計: 液冷式SiC熱交換器またはコールドプレートの場合、内部チャネルの設計(幅、深さ、経路)は、流体フロー、熱伝達係数の最適化、および圧力損失の最小化にとって非常に重要です。
- 流量分布: すべての熱伝達面で冷却材が均等に分配されるようにする。
SiC部品設計のエンジニアリングのヒント:
- 性能のシミュレーション: 熱モデリングおよびシミュレーションソフトウェア(例:有限要素解析(FEA)、数値流体力学(CFD))を活用して、製造前にSiC部品設計の熱性能を予測および最適化する。
- 反復プロトタイピング: 複雑なアプリケーションの場合は、設計をテストおよび改良するために、反復的なプロトタイピングアプローチを検討する。
- 壁の厚さ: 機械的完全性を確保するために適切な壁厚を維持するが、熱抵抗または材料コストを不必要に増加させる可能性のある過度に厚いセクションは避ける。一般的な最小壁厚は、SiCグレードと製造プロセスによって異なる。
- 公差: 現実的で必要な公差を指定する。過度に厳しい公差は、製造コストを大幅に増加させる可能性がある。
これらの設計原則を慎重に検討することにより、エンジニアは作成できる カスタムSiC部品 これにより、優れた放熱が実現され、熱管理システムの全体的な効率、信頼性、および寿命に貢献する。 CAS新素材(SicSino), のような深い材料とプロセス知識を持つサプライヤーと協力することで、これらの設計上の考慮事項が専門的に対処され、最適化された OEM SiC部品 とソリューションが得られる。
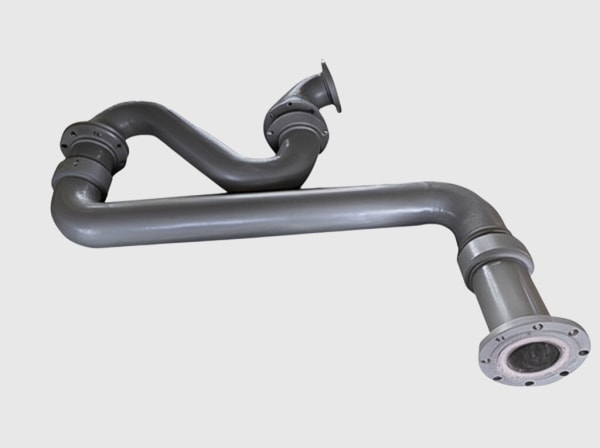
達成可能な公差、表面仕上げ、およびそれらが熱伝達に与える影響
について 精密SiC部品 熱管理アプリケーションを目的とした寸法精度、達成可能な公差、および表面仕上げは、単なる外観上の側面ではない。特にインターフェースにおいて、熱性能に大きく影響する。カスタム部品を指定する際、SiC製造プロセスの能力と、これらの特性が熱伝達にどのように影響するかを理解することは、エンジニアおよび調達担当者にとって非常に重要である。
公差: 炭化ケイ素は非常に硬い材料であるため、焼結または反応結合後の機械加工は困難である。 したがって、非常に厳しい公差を達成するには、精密研削、ラッピング、またはその他の特殊な仕上げ作業が必要になることが多く、コストが増加する可能性がある。
- 焼結/焼成後の公差: 「焼結後」または「焼成後」の状態(つまり、高温処理後で、重要な機械加工の前の状態)のコンポーネントは、寸法公差が広くなる。これらは通常、SiCグレード、サイズ、および部品の複雑さに応じて、寸法の±0.5%〜±2%の範囲になる可能性がある。正確なインターフェースが重要ではない多くのバルク熱コンポーネントでは、これらの公差が許容される場合がある。
- 機械加工された公差: 半導体ダイの直接接合または熱インターフェースの一部を形成する表面など、より厳密な制御が必要なアプリケーションの場合、SiCコンポーネントは通常、研削またはラッピングされる。
- 研磨: ±0.01 mm〜±0.05 mm($ \pm 10 \mu m$〜$ \pm 50 \mu m$)の範囲の公差を達成できる。
- ラッピング/研磨: 非常に平坦で滑らかな表面の場合、ラッピングおよび研磨により、数ミクロン($ \mu m$)までの寸法公差と、さらに優れた平坦度公差を達成できる。
- コストへの影響: 公差が厳しくなると、処理時間の増加、特殊な機器、および潜在的な歩留まりの低下により、製造コストが必然的に高くなる。過剰な指定ではなく、アプリケーションのパフォーマンスに本当に必要な公差を指定することが不可欠である。
表面仕上げ: 表面仕上げは、多くの場合、平均粗さ(Ra)などのパラメーターによって定量化され、2つの固体表面が接触したときの熱接触抵抗に直接影響する。粗い表面に存在する空気ギャップは絶縁体として機能し、熱の流れを妨げる。
- 焼結/焼成後の表面: これらの表面は比較的粗く、Ra値は通常、粒径とプロセスに応じて1μm〜10μm以上の範囲になる。
- 研削された表面: 研削により表面仕上げを大幅に改善でき、通常、Ra値は0.2μm〜0.8μmになる。これは、特に優れた熱インターフェース材料(TIM)と組み合わせて使用する場合、多くの熱インターフェースアプリケーションに十分である。
- ラップおよび研磨された表面: 直接ダイアタッチメントや光学アプリケーションなど、最小限の熱インターフェース抵抗を必要とする最も要求の厳しいアプリケーションの場合、ラッピングおよび研磨により、Ra値が0.05μm(50ナノメートル)未満の非常に滑らかな表面を実現でき、スーパーポリッシュ仕上げの場合は数ナノメートルまで実現できる。
- 熱伝達への影響: より滑らかな表面仕上げは、界面における微細な空気の隙間を減らし、より良好な固体同士の接触と低い熱接触抵抗につながります。これにより、SiCコンポーネントと隣接する材料(例えば、パワーデバイス、ヒートパイプ、またはヒートシンクアセンブリの別の部品)との間のより効率的な熱伝達が可能になります。高性能TIMを使用すると、これらの微細な空隙を埋めるのに役立ちますが、より良い初期表面仕上げは常に優れた結果をもたらします。
寸法精度: 個々の寸法の公差を超えて、全体的な寸法精度(平面度、平行度、垂直度を含む)は、適切な組み立てと熱界面全体にわたる均一な接触圧力を確保するために重要です。
- 平面度: ヒートシンクと基板にとって、平面度は最も重要です。完全な平面度からの逸脱は、大きな隙間を作り出し、熱抵抗を増加させる可能性があります。ラッピングは、かなりの面積にわたって1μmを大幅に下回る平面度を達成できます。
- 平行度: スタックで組み立てる必要のあるコンポーネントや、平行な接合面を持つコンポーネントにとって重要です。
以下の表は、達成可能な一般的な表面仕上げとその影響を示しています。
仕上げ工程 | 一般的なRa範囲(μm) | 達成可能な一般的な公差 | 熱界面抵抗への影響 | 相対コスト |
---|---|---|---|---|
焼結/焼成まま | 1.0 – 10.0+ | ±0.5% ~ ±2% | 高い(大きな空気の隙間) | 低い |
研削 | 0.2 – 0.8 | ±0.01〜±0.05 mm | 中程度(接触の改善) | 中程度 |
ラッピング | 0.05 – 0.2 | 数μmまで | 低い(良好な固体接触) | 高い |
研磨 | < 0.05 | 数μm / サブμmまで | 非常に低い(優れた接触) | 非常に高い |
CAS新素材(SicSino)は、濰坊市の高度な製造能力と当社の一流の専門チームを活用し、精密機械加工および仕上げ技術を含む、材料から完成品までの統合プロセスを所有しています。当社は、お客様の特定の SiC熱界面材料 アプリケーション、および全体的なコストに対する達成可能な公差、表面仕上げ要件の最適なバランスについてアドバイスを提供できます。 より高品質である、 コスト競争力のあるカスタマイズ炭化ケイ素部品。当社の専門知識により、お客様のコンポーネントが最大の熱効率に必要な正確な寸法および表面仕様を満たすことが保証されます。
SiCの熱性能を向上させるための後処理およびコーティングオプション
炭化ケイ素の固有の特性と慎重な設計は、効果的な熱管理の基礎ですが、後処理と特殊コーティングは、 カスタムSiC部品の性能、耐久性、および機能をさらに向上させることができます。これらのステップは、特定の動作環境に合わせてSiC部品を最適化したり、他の材料との統合を可能にするために不可欠な場合が多くあります。
一般的な後処理ステップ:
- 精密研削およびラッピング:
- 目的 前述のように、研削およびラッピングは、厳しい寸法公差と滑らかな表面仕上げを達成するために不可欠です。熱管理の場合、これにより界面での熱接触抵抗が減少します。
- メリット 平面度、平行度、および表面の滑らかさが向上すると、接合面とのより密接な接触につながり、熱界面材料(TIM)の有無にかかわらず、熱伝達が最大化されます。
- アプリケーション パワーエレクトロニクス用のSiC基板、熱源と直接接触するヒートスプレッダー、および最小限の熱境界抵抗を必要とするあらゆるアプリケーションに不可欠です。
- 研磨:
- 目的 ラッピングよりもさらに滑らかで鏡面のような表面仕上げを実現します。
- メリット 表面の欠陥をさらに最小限に抑え、直接接合や非常に薄いTIMを使用する場合などのアプリケーションに不可欠です。熱管理と組み合わせて使用される光学部品(レーザーシステムなど)にとっても重要です。
- アプリケーション 高性能半導体パッケージング、高度な光学系。
- エッジ面取り/ラジアス加工:
- 目的 鋭いエッジを取り除くため。SiCのような脆性材料では欠けが発生しやすい可能性があります。
- メリット 取り扱い安全性を向上させ、応力集中による組み立てまたは動作中の亀裂の発生リスクを軽減し、エッジ付近に適用されるコーティングの信頼性を向上させることができます。
- アプリケーション ほとんどの精密SiCコンポーネントの標準的な慣行。
- クリーニング:
- 目的 SiC表面から汚染物質、機械加工残留物、または粒子状物質を除去するため。
- メリット コーティング、接合、または組み立てなどの後続のプロセスに対してクリーンな表面を確保します。これは、強力な接着と最適な界面特性を実現するために不可欠です。
- アプリケーション コーティングまたは接合ステップの前に不可欠。
性能向上のためのコーティングオプション:
- 金属化:
- 目的 SiC表面に薄い金属層(例えば、ニッケル、金、銀、銅、チタン)を適用します。
- 方法: スパッタリングのような物理蒸着(PVD)、化学蒸着(CVD)、またはめっき技術。
- メリット
- はんだ付け性/ろう付け性: SiCコンポーネントを他の材料(例えば、銅ベースプレート、直接接合銅(DBC)基板、または金属製のコバール蓋)にはんだ付けまたはろう付けして、堅牢で気密性があり、熱伝導性の高い接合部を作成できるようにします。これは、 SiC熱界面材料 およびアセンブリの作成に不可欠です。
- 電気的接触の改善: SiCベースの半導体デバイスの場合、金属化は低抵抗の電気的接触を提供します。
- 熱拡散の強化: 特定の金属層は、横方向の熱拡散をさらに助けることができます。
- アプリケーション パワーエレクトロニクスモジュール、気密パッケージ、センサー、チューブとヘッダーの接合が必要な熱交換器。
- 誘電体コーティング(例えば、窒化ケイ素(Si3N4)、二酸化ケイ素(SiO2)):
- 目的 良好な熱結合を維持しながら電気絶縁を提供するため、または強化された環境保護を提供するため。
- メリット 高電圧アプリケーションでの電気的短絡を防ぎ、特定の化学環境での耐食性を向上させたり、拡散バリアとして機能したりできます。
- アプリケーション 高電圧パワーモジュール、過酷な環境で動作するセンサー。
- 耐腐食性/保護コーティング(例えば、CVD SiC、ダイヤモンドライクカーボン– DLC):
- 目的 非常に攻撃的な環境でのSiCの優れた耐食性をさらに強化するため、または耐摩耗性を向上させるため。
- メリット 困難な化学的または研磨的な条件下でのコンポーネントの寿命を延ばします。CVD SiCコーティングは、RBSiCのような一部のSiCグレードの多孔性を封止し、耐薬品性を向上させることができます。
- アプリケーション 化学処理装置、研磨スラリーまたは高温腐食性ガスにさらされるコンポーネント。
- 放射率を高めるコーティング:
- 目的 SiCコンポーネントの表面放射率を高め、それによって放射熱伝達を改善するため。
- メリット 放射が重要な熱伝達モードである高温アプリケーションでは、高放射率コーティングは熱をより効果的に放散するのに役立ちます。
- アプリケーション 宇宙アプリケーションの放射冷却コンポーネント、高温炉エレメント。
適切な後処理およびコーティングオプションの選択は、特定のアプリケーション要件、使用されるSiCのグレード、および全体的なシステム設計に大きく依存します。 CAS新素材(SicSino) は、当社の幅広い材料、プロセス、設計、測定、および評価技術を活用して、この分野で包括的なサポートを提供します。当社のチームは、お客様の カスタムSiC製品 の熱性能、信頼性、および費用対効果を最適化するための最適な表面処理およびコーティングについてアドバイスを提供し、半導体、航空宇宙、および高温処理などの業界の厳しい要求を満たすことを保証します。
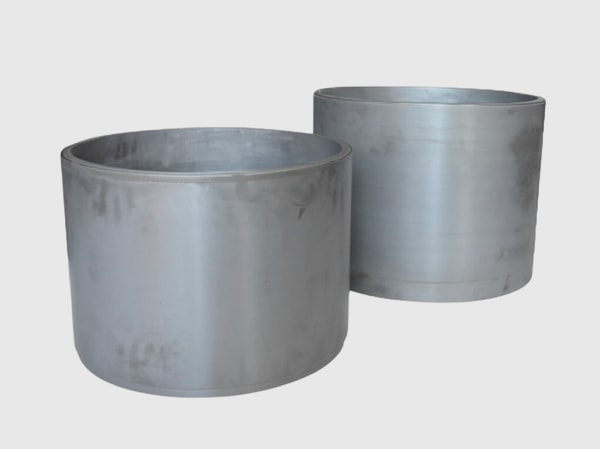
熱管理におけるSiCに関するよくある質問(FAQ)
エンジニア、調達マネージャー、および技術バイヤーは、熱管理の課題に炭化ケイ素を検討する際に、特定の質問をすることがよくあります。以下に、実践的で簡潔な回答を添えた一般的な質問をいくつか示します。
Q1:炭化ケイ素(SiC)は、性能の点で、アルミニウム、銅、アルミナなどの従来の熱管理材料とどのように比較されますか?
A:SiCは、要求の厳しいアプリケーションで従来の材料をしばしば上回る独自の特性の組み合わせを提供します。
- アルミニウム(Al)および銅(Cu)との比較:
- 熱伝導率: 高品質のSiC(特にSSiC)は、アルミニウムに匹敵する熱伝導率を持ち、場合によっては低グレードの銅に近づく可能性がありますが、AlおよびCuが軟化し、性能が低下する高温でも、この伝導率をはるかに良好に維持します。
- 温度安定性: SiCは、高温でAlおよびCuを大幅に上回ります(SiCは1000℃をはるかに超える温度で十分に動作できます。Alは200℃未満、Cuは構造/熱的完全性のために300℃未満に制限されています)。
- CTEマッチ: SiCは、AlまたはCuよりも熱膨張係数(CTE)がはるかに低いため、シリコンなどの半導体材料との互換性が高く、熱応力を軽減します。
- 機械的特性: SiCは、大幅に硬く、剛性が高く、耐摩耗性に優れています。
- 重量: SiCは銅よりも軽量です。
- コスト: 一般に、SiCコンポーネントは、原材料と加工コストのために、バルクAlまたはCu部品よりも高価ですが、過酷な条件下での優れた性能と寿命により、総所有コストを削減できます。
- アルミナ(Al2O3)との比較:
- 熱伝導率: SiCは、大幅に高い熱伝導率を持っています(SiC:120-270+ W/mK、アルミナ:20-30 W/mK)。これは、放熱の重要な差別化要因です。
- 機械的強度: どちらも硬いセラミックですが、SiCは一般的に優れた強度と耐熱衝撃性を提供します。
- コスト: アルミナは通常、SiCよりも安価です。
- アプリケーション アルミナは、電気絶縁体として、また優れた耐摩耗性で広く使用されていますが、高い熱伝導率を必要とするアプリケーションでは、SiCの方がはるかに優れています。
要約すると、SiCは、高温能力、半導体への良好なCTEマッチング、優れた機械的特性、または化学的安定性と組み合わせて高い熱伝導率が必要な場合に選択されます。これは、金属や他のセラミックでは提供できない組み合わせです。
Q2:炭化ケイ素が熱管理ソリューションに優れている一般的な動作温度範囲は何ですか?
A:炭化ケイ素は非常に広い温度範囲で優れていますが、その利点は、以下を含むアプリケーションで特に顕著になります。
- 中程度の高温(200℃〜600℃): この範囲では、アルミニウムや銅などの従来の金属は、効率や機械的完全性を失い始めたり、半導体とのCTEの不一致が問題になったりします。SiCは、優れた熱伝導率と安定性を維持します。これは、パワーエレクトロニクス、自動車アプリケーション、および一部の産業プロセスで一般的です。
- 高温(600℃〜1400℃): これは、SiCが真に輝く場所です。反応焼結SiC(RBSiC/SiSiC)は、約1350〜1400℃まで動作できます。多くの工業炉、熱処理プロセス、および高度なエネルギーシステムは、この範囲で動作します。
- 非常に高い温度(1400℃以上): 焼結炭化ケイ素(SSiC)は、最大1600℃または1700℃(および短時間または特定の雰囲気ではそれ以上)の温度で確実に動作できます。アプリケーションには、高度な窯道具、ガスタービン用コンポーネント、および研究機器が含まれます。
低温でも、SiCの高い熱伝導率と、電気抵抗率や剛性などの他の特性を組み合わせることで、最適な材料になる可能性があります。ただし、その高温能力は、多くの熱管理システムでの採用の主な推進力です。
Q3:CAS new materials(SicSino)は、カスタムSiC熱ソリューションの設計、材料選択、およびプロトタイピングを支援できますか?
A:もちろんです。 CAS新素材(SicSino) は、初期コンセプトから本格的な生産まで、 カスタム炭化ケイ素製品の包括的なサポートを提供することに特化しています。以下に、当社がどのように支援できるかを示します。
- 素材の選択: 当社は、様々なSiCグレード(RBSiC、SSiCなど)とそれらの特性に関する深い知識を活用し、お客様の用途に合わせて、熱性能、機械的要件、耐薬品性、コストのバランスが最適な材料の選定を支援します。中国SiC産業の中心地である濰坊市に拠点を置き、中国科学院(CAS)との連携により、幅広い材料オプションと最先端の知識にアクセスできます。
- 設計コンサルティングと最適化: カスタマイズされたSiC製造を専門とする国内トップクラスの専門チームが、お客様のエンジニアリングチームと協力して、製造性(DFM)と熱効率のためにコンポーネント設計を最適化します。形状、公差、表面仕上げ、統合戦略についてアドバイスを提供できます。
- プロトタイピング: SiC熱ソリューションのテストと検証を可能にするために、迅速なプロトタイピングを促進します。この反復プロセスは、大規模生産に移行する前に、設計を改良し、性能目標を満たしていることを確認するのに役立ちます。
- カスタム製造: 材料から製品までの統合プロセスにより、高度な成形、焼結、精密機械加工能力を含め、複雑かつ高精度な製品を製造できます。 カスタムSiC部品 お客様の仕様に合わせて調整します。
- 技術移転とターンキーソリューション: コンポーネントの供給だけでなく、独自のプロフェッショナルな炭化ケイ素製品製造工場を設立する必要がある場合は、 CAS新素材(SicSino) SiC製造の技術移転と、フルレンジのターンキープロジェクトサービスを提供できます。これには、工場設計、特殊機器の調達、設置、試運転、試作が含まれます。
当社のコミットメントは、単なるコンポーネントの提供ではなく、完全かつ効果的な 高度なセラミックソリューション 熱管理の課題に対するソリューションを提供し、より高い品質、コスト競争力、信頼性の高い供給を保証することです。
このFAQセクションは、最初の重要な質問に対処することを目的としています。特定のプロジェクトに関するより詳細な議論については、当社の技術チームまでお気軽にお問い合わせください。 CAS新素材(SicSino).
結論:要求の厳しい熱環境におけるカスタムシリコンカーバイドの比類なき価値
半導体やパワーエレクトロニクスから航空宇宙、高温製造に至るまで、業界全体でより高い効率、電力密度、および動作信頼性を絶え間なく追求する中で、効果的な熱管理は成功の礎となっています。 これまで見てきたように、 カスタム炭化ケイ素 は、優れた熱伝導率、卓越した高温安定性、低い熱膨張、優れた機械的強度、および優れた化学的不活性という、魅力的な特性を備えており、最も要求の厳しい熱的課題に取り組むための不可欠な材料となっています。
複雑なヒートシンク形状から精密に仕上げられた基板まで、特定の用途ニーズに合わせてSiCコンポーネントを調整できる能力は、その価値提案を大幅に高めます。一般的なソリューションでは不十分な場合に、 カスタムSiC製造 は、放熱を最大化し、システムの寿命を延ばし、最終的には優れた製品性能と信頼性に貢献する最適化された設計を可能にします。 高度なセラミックヒートシンク、堅牢な 産業用SiC部品、または 敏感な電子機器向けの精密SiC部品 であろうと、カスタマイズはこの注目すべき材料の可能性を最大限に引き出します。
これらの利点を活用するには、適切なサプライヤーを選択することが最も重要です。 CAS新素材(SicSino)は、中国の炭化ケイ素生産の中心地である濰坊市に戦略的に拠点を置き、中国科学院(CAS)の強力な科学技術力に支えられており、単なるコンポーネントプロバイダーではありません。私たちはイノベーションにおけるお客様のパートナーです。SiC材料科学、カスタム設計、高度な製造プロセス、および品質保証における当社の深い専門知識により、お客様は より高品質な、cスト競争力のあるカスタム炭化ケイ素部品。さらに、技術移転とターンキープラントソリューションを提供する独自の能力は、グローバルなSiC産業の発展に対する当社のコミットメントを強調するものです。
性能の限界を押し広げようとするエンジニア、信頼性の高い高性能材料を調達する購買担当者、次世代システムの構築を目指すOEMにとって、 カスタム炭化ケイ素 のような信頼できるパートナーから CAS新素材(SicSino) は、目標達成への道筋を提供します。当社の カスタム炭化ケイ素製品 と包括的なサポートが、要求の厳しい産業用途に最適な熱管理ソリューションを提供し、競争の激しい状況で優位に立てる方法について、ぜひ当社のチームにご相談ください。
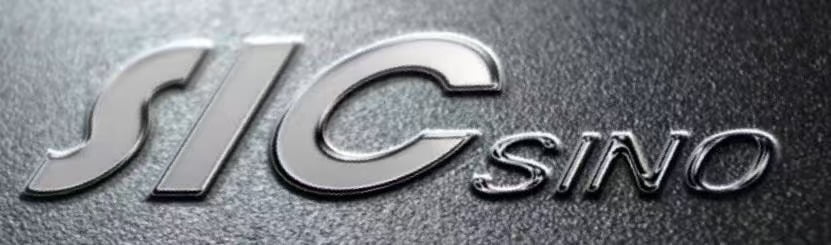
SicSino - CAS新素材
私たちCAS新材料(SicSino)は、2015年以来、炭化ケイ素製造技術の導入と実践を行い、現地企業の大規模生産と製品プロセスの技術進歩を支援してきました。当社は、現地炭化ケイ素産業の出現と継続的な発展の目撃者である。
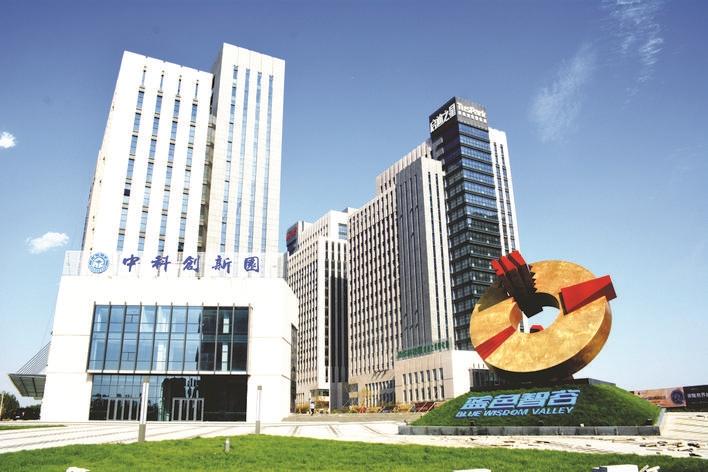