極限状態を極める:カスタム炭化ケイ素が流体ハンドリングに革命をもたらす理由
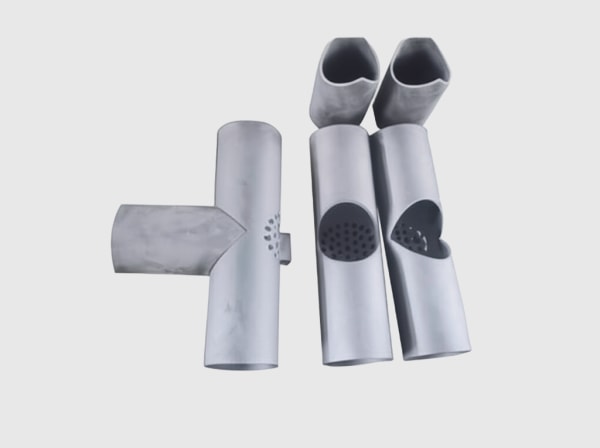
シェア
要求の厳しい産業用流体処理の世界では、機器は常に腐食性の化学物質、研磨性のスラリー、高温、および極端な圧力にさらされています。従来の材料では多くの場合不十分であり、頻繁なダウンタイム、コストのかかるメンテナンス、および損なわれた運用効率につながります。ここで、 カスタム炭化ケイ素(SiC)、高性能な技術 セラミック セラミックである炭化ケイ素が登場します。これは、重要な流体処理コンポーネントの材料として急速に普及しています。その卓越した特性は、他の材料では失敗する用途において、比類のない信頼性と寿命を提供します。このブログ投稿では、流体処理用のカスタムSiCの世界を掘り下げ、その用途、利点、設計上の考慮事項、および CAS新素材(SicSino)のような適切なサプライヤーを選択することが、お客様の業務にとってどのようにゲームチェンジャーになるかを探ります。
要求の厳しい流体処理用途におけるカスタム炭化ケイ素の紹介
炭化ケイ素(SiC)は、その優れた硬度、強度、および熱安定性で有名な高度な合成セラミック材料です。ケイ素と炭素の化合物によって形成されたSiCは、高性能な産業用途に非常に適した独自の特性の組み合わせを誇っています。標準的なSiCコンポーネントは大きな利点を提供しますが、 カスタム炭化ケイ素製品 は、これらの特性を特定の、多くの場合極端な流体処理環境の正確な要件に合わせて調整することで、これをさらに一歩進めます。
流体処理システムは、化学処理やエネルギー生産から半導体製造や製薬まで、多くの産業の生命線です。 輸送される流体は、超純水から高腐食性の酸、研磨性のスラリー、および高温の液体やガスまで多岐にわたります。課題は非常に大きいです。
- 腐食: 攻撃的な化学物質は、金属コンポーネントを急速に劣化させる可能性があります。
- 摩耗と浸食: 固体を含む流体は、部品をすばやく摩耗させる可能性があります。
- 高温と高圧: 多くのプロセスは、従来の材料の限界を超える条件下で動作します。
- 熱衝撃: 急激な温度変化により、材料に亀裂が入ったり、破損したりする可能性があります。
- 純度の要件: 半導体や製薬などの業界では、汚染を防ぐために材料の不活性が不可欠です。
シール、ベアリング、ポンプ渦巻き、インペラー、バルブシート、ノズルなどのカスタムSiCコンポーネントは、これらの過酷な条件に耐えるように設計されています。SiCグレード、設計、および製造プロセスをカスタマイズすることにより、エンジニアは最適な性能を実現し、摩耗を最小限に抑え、耐用年数を延ばし、総所有コストを削減できます。特定の流体、温度範囲、および機械的負荷に合わせてコンポーネントを正確に設計できることが、カスタムSiCを現代産業に不可欠なソリューションにしている理由です。これは、専門メーカーの専門知識が重要になる場所であり、SiCの独自の可能性が各用途で最大限に活用されることを保証します。
流体処理システムにおけるSiCの主要な産業用途
炭化ケイ素の汎用性と堅牢性により、多様な産業の流体処理システム内の幅広い重要なコンポーネントに適しています。 その採用は、ステンレス鋼、超合金、またはアルミナなどの他のセラミックなどの従来の材料が動作限界に達する場所で、信頼性と性能の向上に対するニーズによって推進されています。
ポンプ: SiCは、さまざまなポンプコンポーネント、特に研磨性のスラリー、腐食性の化学物質を処理するコンポーネント、または高温で動作するコンポーネントで広く使用されています。
- インペラーと渦巻き/ケーシング: 反応焼結炭化ケイ素(RBSiCまたはSiSiC) そして 焼結炭化ケイ素(SSiC) は、研磨性の粒子からの摩耗や攻撃的な化学物質からの腐食に対して優れた耐性を提供し、金属またはゴムで裏打ちされた部品よりも大幅に長持ちします。カスタム設計されたSiCポンプコンポーネントは、その形状をより長く維持し、一貫したポンプ性能を保証します。
- シャフトとシャフトスリーブ: SiCの高い剛性と耐摩耗性は、シャフトを研磨性の摩耗や化学的攻撃から保護し、早期の故障を防ぎ、 産業用SiCポンプ部品.
- のメンテナンスを削減します。 ベアリング(ジャーナルおよびスラスト): SiCベアリング、特にSSiCは、腐食性または研磨性の粒子を含むプロセス流体(製品潤滑ベアリング)でも動作できます。それらの低い摩擦と高い硬度は、 化学またはスラリーサービス用のSiCポンプ用ベアリング
などの用途で寿命を延ばします。 バルブ:
- 過酷な流体の流れを制御するバルブは、SiCの特性から大きな恩恵を受けます。 シート、ディスク、ボール、およびプラグ: カスタムSiCバルブコンポーネント
- は、非常に浸食性または腐食性の環境で優れたシール性と長寿命を提供します。SiCボールバルブ部品とシートは、金属製の同等品よりもはるかに長く、タイトな遮断機能を維持します。 ライナー:
過酷な条件にさらされるバルブ本体の場合、SiCライナーは摩耗や化学的攻撃に対する堅牢なバリアを提供します。 SiCの流体処理における最も確立された用途の一つは、メカニカルシールでしょう。
- シール面/リング: SiCは、それ自体またはカーボングラファイトと組み合わせて使用されることが多く、硬度、高い熱伝導率(摩擦熱を放散するため)、優れた耐食性、および低い摩耗率の理想的な組み合わせを提供します。 SiCメカニカルシール面は、 化学ポンプ、高圧ポンプ、温水サービスなどの要求の厳しい用途で標準となっています。ここでは、SSiCとグラファイトを充填したSiCが一般的な選択肢です。
その他の流体処理装置:
- ノズル: SiCスプレーノズルは、 オリフィス形状と噴霧パターンを維持できるため、腐食性または浸食性の流れにおける化学物質の注入、冷却、または洗浄に使用されます。
- パイプおよびサイクロン用ライナー: 鉱業および鉱物処理では、SiCライナーは極端な研磨摩耗から機器を保護します。
- 流量計: 腐食性の高い流体と接触する流量計内のコンポーネントは、精度と寿命を確保するためにSiC製にすることができます。
- 熱交換器チューブ: 非常に特定の腐食性の媒体または高温用途向けに、SiCチューブは優れた熱伝導率と耐食性を提供します。
以下の表は、主要な産業と、SiCが流体処理用途にもたらす利点をまとめたものです。
産業分野 | 使用される一般的なSiC部品 | 活用されるSiCの主な利点 |
---|---|---|
化学処理 | ポンプ部品(インペラ、ケーシング、ベアリング)、バルブトリム(シート、ボール)、メカニカルシール面、ノズル | 優れた耐食性、耐摩耗性、高温安定性 |
石油化学 | サワーガスまたは研磨性の原油用ポンプ部品、メカニカルシール、バルブ部品 | 化学的不活性、耐摩耗性、耐熱衝撃性 |
鉱業および鉱物処理 | スラリーポンプ部品、サイクロンライナー、パイプライナー、シュートライナー | 優れた耐摩耗性、耐エロージョン性 |
石油およびガス(上流/下流) | ポンプベアリング、メカニカルシール、チョークバルブコンポーネント | 砂状条件下での耐摩耗性、耐食性(H2S) |
発電 | ボイラー給水ポンプシール、排煙脱硫(FGD)ポンプ部品およびノズル | 高温強度、耐摩耗性、耐食性 |
半導体製造 | 超純水ポンプコンポーネント、ウェーハ処理部品、CMPスラリーコンポーネント | 高純度、化学的不活性、耐摩耗性 |
製薬および食品 | ポンプシール、ホモジナイザー部品、プロセス流体用ベアリング | FDAコンプライアンス(特定のグレードの場合)、洗浄性、耐摩耗性、化学的不活性 |
パルプおよび紙 | 研磨性/腐食性媒体用ポンプコンポーネント、メカニカルシール、ドクターブレード | 繊維およびフィラーに対する耐摩耗性、耐薬品性 |
産業用途における テクニカルセラミックスの広範な採用、特にSiCは、これらの用途において、困難な流体環境における運用効率の向上とメンテナンスコストの削減におけるその重要な役割を強調しています。
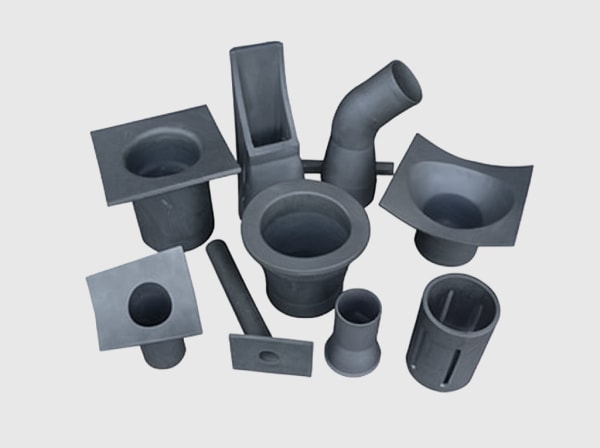
流体処理にカスタム炭化ケイ素を選択する理由
市販のSiCコンポーネントは大きな利点を提供できますが、 カスタム炭化ケイ素ソリューション 材料と設計を流体処理アプリケーションの特定の要求に正確に一致させることにより、さらに高いレベルのパフォーマンスと信頼性を提供します。カスタマイズを選択すると、運用効率、コンポーネントの寿命、およびシステム全体の完全性に直接影響するさまざまな利点が得られます。
- 優れた耐摩耗性と耐エロージョン性: 鉱業のスラリー、化学処理の顔料、触媒など、硬い粒子を含む流体は、従来の材料に大きな損害を与える可能性があります。焼結炭化ケイ素(SSiC)や特殊な反応焼結炭化ケイ素(RBSiC)などのグレードから設計されたカスタムSiCコンポーネントは、ダイヤモンドに次ぐ硬度を提供します。これは、最も 研磨性の高いスラリーを処理する場合でも、ポンプインペラ、ライナー、バルブシートなどの部品の耐用年数が大幅に延長されることを意味します。これにより、部品の交換に関連するダウンタイムが大幅に削減されます。
- 比類のない耐食性: 炭化ケイ素は、強酸(硫酸、硝酸、塩酸、フッ化水素酸など)、塩基、溶媒、酸化剤など、広範囲の化学物質に対して、高温下でも実質的に不活性です。カスタマイズにより、極度に腐食性の高い媒体を含むアプリケーション向けに、最も純粋なSiCグレード(遊離ケイ素を含まないSSiCなど)を選択できるため、 耐食性セラミック部品 が構造的完全性を維持し、製品の汚染を防ぎます。
- 卓越した高温安定性: 多くの流体処理プロセスは、金属が軟化、クリープ、または急速に腐食する高温で行われます。SiCは、1400℃を超える温度(一部のグレードではさらに高い温度)で、優れた機械的強度、硬度、および耐薬品性を維持します。カスタム設計では、熱膨張を考慮し、 高温SiCバルブ やポンプ部品などのコンポーネントが確実に信頼性高く動作するようにすることができます。
- 優れた耐熱衝撃性: 産業プロセスには急速な温度変化が伴う可能性があり、脆性材料が破損する可能性があります。特定のグレードのSiC、特に窒化ケイ素結合炭化ケイ素(NBSC)または特別に設計されたRBSiCは、優れた耐熱衝撃性を提供します。カスタム設計により、熱サイクル中の応力集中を最小限に抑えるようにコンポーネントの形状がさらに最適化されます。
- 高い熱伝導性: 機械式シール面やベアリングのような用途では、摩擦熱を放散する能力が非常に重要です。SiCは、アルミナやジルコニアなどの他のセラミックスよりも熱伝導率が著しく高くなっています。この特性は、過熱を防ぎ、熱による歪みを低減し、動的部品の寿命を延ばすのに役立ちます。SiCのグレードをカスタマイズすることで、この特性を微調整できます。
- 低摩擦係数と自己潤滑性: 動的なアプリケーションなどにおいて、 化学ポンプ用のSiCメカニカルシール または カスタムSiCベアリングSiC(特にSiC同士またはグラファイトとの組み合わせ)は、低い摩擦係数を示します。これにより、エネルギー消費が削減され、摩耗が最小限に抑えられ、潤滑剤が不十分な状態や、場合によっては短時間のドライ運転も可能になります。
- 化学的安定性と純度: 半導体製造(超純水システム)や製薬などの業界では、プロセス流体の汚染を防ぐことが最も重要です。高純度SSiCは非常に不活性であり、イオンを流体中に溶出させないため、製品の品質が保証されます。
- 長寿命と総所有コスト(TCO)の削減: カスタムSiC部品の初期投資は、従来の材料で作られた部品よりも高くなる可能性がありますが、大幅に長い運転寿命、メンテナンス要件の削減、ダウンタイムの最小化により、TCOが大幅に低くなります。平均故障間隔(MTBF)の延長は、生産性と収益性の向上に直接つながります。
カスタムSiCを選択するということは、材料と用途の両方のニュアンスを理解しているサプライヤーと提携することを意味します。 CAS新素材(SicSino)中国の炭化ケイ素製造の中心地である濰坊市に拠点を置くSicSinoは、その深い専門知識と中国科学院(CAS)とのつながりを活用して、正確に調整されたSiCソリューションを提供しています。40社以上の地元SiC企業への支援は、技術進歩の環境を育み、カスタム部品が最大限の性能を発揮することを保証しています。
流体処理に推奨されるSiCグレードと組成
適切な炭化ケイ素のグレードを選択することは、流体処理アプリケーションにおける性能と費用対効果を最適化するために非常に重要です。製造プロセスが異なると、微細構造と特性が異なるSiC材料が得られます。 以下に、最も一般的なSiCグレードと、流体処理への典型的な適合性を示します。
- 反応結合炭化ケイ素(RBSiCまたはSiSiC - Silicon Infiltrated Silicon Carbide):
- 製造: 多孔質の炭素-SiCプリフォームに溶融シリコンを浸透させることによって製造されます。シリコンは炭素の一部と反応してより多くのSiCを形成し、残りの細孔は金属シリコン(通常は8〜20%の遊離シリコン)で満たされます。
- プロパティ 優れた耐摩耗性、高い硬度、優れた熱伝導率、優れた寸法制御、および比較的低い製造コスト。複雑な形状に成形できます。
- 流体処理への適合性: 中程度の腐食性および研磨性の環境におけるポンプ部品(インペラ、ボリュート、シャフトスリーブ)、バルブトリム、サイクロンライナー、およびノズルに広く使用されています。多くの用途で主力となる材料です。 産業用SiC部品.
- 制限事項: 遊離シリコンの存在により、強アルカリ、フッ化水素酸、および特定の高温酸化環境による攻撃を受けやすくなります。超高純度アプリケーションには理想的ではありません。
- 焼結炭化ケイ素(SSiCまたはS-SiC):
- 製造: 微細な高純度SiC粉末を、非酸化物焼結助剤(例:ホウ素と炭素)とともに非常に高い温度(通常は> 2000℃)で焼結することによって製造されます。これにより、緻密で微細な単相SiC材料が得られます。
- プロパティ 最高の純度(通常は> 99%SiC)、全pH範囲にわたる優れた耐食性、優れた耐摩耗性と耐エロージョン性、優れた高温強度、および優れた耐熱衝撃性。
- 流体処理への適合性: 腐食性の高い化学ポンプのメカニカルシール面、攻撃的な媒体中で動作するベアリング、過酷なサービス用のバルブ部品、および超純水システム用の部品など、最も要求の厳しいアプリケーションに最適な選択肢です。多くの場合、重要なアプリケーションにおける高度なセラミックソリューションに指定されます。 高度なセラミックソリューション 重要なアプリケーションで使用されます。
- 制限事項: 一般にRBSiCよりも高価で、非常に大きい、あるいは非常に複雑な形状のものを製造するのは難しい。
- 窒化物結合炭化ケイ素(NBSC):
- 製造: SiC粒子は、窒化ケイ素(Si3N4)マトリックスによって結合されています。
- プロパティ 優れた機械的強度、優れた耐熱衝撃性、および溶融金属による濡れに対する優れた耐性。
- 流体処理への適合性: RBSiCまたはSSiCと比較して、直接流体接触部品の主要材料としてはあまり一般的ではありませんが、極端な熱サイクルが主な懸念事項であるアプリケーション、または高温流体プロセスに関連する耐火物部品として使用できます。
- グラファイト充填炭化ケイ素(SiC-C):
- 製造: 通常、SSiCまたはRBSiCに、SiCマトリックス内に分散した微細なグラファイト粒子が含まれています。
- プロパティ 低い摩擦係数や改善されたドライ運転能力など、強化されたトライボロジー特性。グラファイトは固体潤滑剤として機能します。
- 流体処理への適合性: 特に潤滑が不十分な場合や断続的なドライ運転のリスクがあるアプリケーションでは、改善された潤滑性が重要なメカニカルシール面およびベアリングに主に使用されます。高性能メカニカルシールに不可欠です。 高性能メカニカルシール.
- 多孔質炭化ケイ素:
- プロパティ 制御された多孔性、高い表面積、優れた熱的および化学的安定性。
- 流体処理への適合性: 高温ガスまたは腐食性液体のフィルター、ディフューザー、メンブレン、および触媒担体などの特殊なアプリケーションで使用されます。
次の表は、流体処理用の主要なSiCグレードの比較概要を示しています。
SiCグレード | 主な特徴 | 一般的な流体処理アプリケーション | 相対コスト | 耐食性 | 耐摩耗性 | 最大使用温度使用温度 |
---|---|---|---|---|---|---|
RBSiC (SiSiC) | 優れた全体的な特性、複雑な形状、適度なコスト、遊離シリコンを含む | 中程度の腐食/摩耗に対するポンプインペラおよびケーシング、バルブ部品、ノズル、摩耗ライナー | 中程度 | 良好(強アルカリ、HFを除く) | 非常に良い | 1350℃ |
SSiC(焼結SiC) | 最高の純度、優れた耐食性および耐摩耗性、高温での高い強度 | 過酷な化学物質および研磨剤サービス、超純水用のメカニカルシール面、ベアリング、バルブ部品 | 高い | 素晴らしい | 素晴らしい | 1600℃ |
窒化結合SiC(NBSC) | 優れた耐熱衝撃性、良好な強度 | 過酷な熱サイクルを伴うアプリケーション、耐火物部品 | 中〜高 | グッド | グッド | 1550℃ |
グラファイト充填SiC(例:SSiC+C) | 潤滑性の向上、摩擦の低減、良好なドライラン機能 | 強化されたトライボロジー性能を必要とするメカニカルシール面、ベアリング | 高い | 優れた(ベースSiC) | 非常に良い | 1600℃(ベースSiC) |
正しいSiCグレードを選択することは、重要なステップです。 CAS新素材(SicSino)SicSinoは、その豊富な経験と中国科学院からの支援により、この選択プロセスにおいて非常に貴重な支援を提供します。濰坊のSiC産業クラスターで多数の企業を支援することによって培われた材料科学と製造プロセスに関する深い理解により、クライアントは特定の流体処理の課題に完全に最適化されたソリューションを受け取ることができます。 カスタムSiC部品 特定の流体処理の課題に完全に最適化されたソリューションを受け取ることができます。
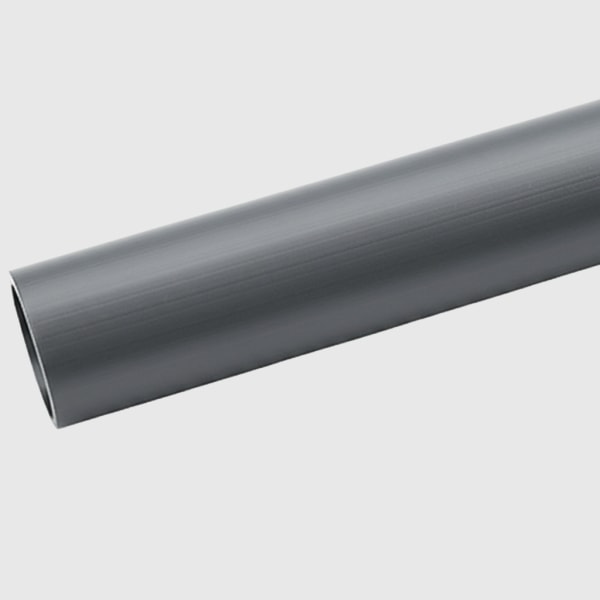
カスタムSiC流体処理部品の重要な設計および製造可能性に関する考慮事項
炭化ケイ素で部品を設計するには、その固有の硬度と脆性のため、金属やプラスチックとは異なるアプローチが必要です。SiCは優れた性能を発揮しますが、流体処理システムにおける製造可能性、構造的完全性、および最適な機能を確保するには、慎重な設計上の考慮事項が不可欠です。設計の初期段階でSicSinoのような経験豊富なSiCメーカーと協力することを強くお勧めします。 CAS新素材(SicSino) 設計の初期段階でSicSinoのような経験豊富なSiCメーカーと協力することを強くお勧めします。
SiC部品の主要な設計原則:
- シンプルさと形状:
- シャープな角やエッジを避ける: これらは、チッピングや破損につながる可能性のある応力集中を引き起こします。十分な半径と面取りを組み込む必要があります。
- 均一な肉厚: 焼結および熱サイクル中の応力を防ぐのに役立ちます。断面の急激な変化を避けてください。
- 複雑な内部機能を最小限に抑える: 可能ではありますが、複雑な内部空洞またはアンダーカットは、製造の複雑さとコストを大幅に増加させる可能性があります。離型またはグリーン加工の容易さを考慮して設計してください。
- アスペクト比: 非常に長く薄い部品は、破損せずに製造および取り扱いが難しい場合があります。
- 脆性の管理:
- 引張荷重と圧縮荷重: SiCは、引張よりも圧縮の方がはるかに強力です。設計では、可能な限りSiC部品を圧縮的に負荷することを目指す必要があります。
- ストレス分析: 重要な部品の場合、有限要素解析(FEA)は、高応力領域を特定し、製造前に設計を最適化できます。
- 耐衝撃性: SiC部品を直接的な衝撃から保護するために、設計ハウジングまたは周囲構造を設ける。
- SiCと他の材料との接合:
- 流体処理システムでは、SiC部品を金属製ハウジングや他の部品と統合する必要がある場合が多い。
- 熱膨張の差: SiCは一般的に金属よりも熱膨張係数が低い。この差は、温度変化時の応力集中を防ぐために設計で考慮する必要がある。その手法としては、コンプライアントな中間層の使用、特定のろう付け合金の使用、または焼きばめ(慎重な干渉計算が必要)や適切なガスケット材を使用したボルト締めなどの機械的締結方法がある。
- ろう付けと接合: 特殊な活性ろう付け合金または接着接合技術を使用できるが、慎重な表面処理とプロセス管理が必要となる。
- 表面のシーリング:
- メカニカルシール面やバルブシートなどの部品では、シール面の設計が最も重要となる。
- 平坦度と表面仕上げ: 効果的なシールを確保し、摩擦/摩耗を最小限に抑えるために、適切な平坦度と表面仕上げの要件を指定する。
- 接触圧力: 設計により、シール界面全体で均一な接触圧力が得られるようにする。
- 製造性を考慮した設計(DFM):
- 成形プロセスの制限: 選択された成形方法(例:乾式プレス、静水圧プレス、スリップキャスティング、押出成形、射出成形、または最新のアディティブマニュファクチャリング技術)が設計の可能性に影響を与える。たとえば、プレスは単純な形状に適しており、スリップキャスティングまたはアディティブマニュファクチャリングはより複雑な形状を作成できる。
- 焼結収縮: SiC部品は焼結中に大幅に収縮する(通常、SSiCで15〜20%)。最終寸法を達成するために、これはグリーン(焼結前)段階の設計で考慮する必要がある。
- 機械加工の余裕: 厳しい公差を達成するために焼結後のダイヤモンド研削が必要な場合は、焼結後の設計に十分な材料の余裕を含める必要がある。
成功のためのエンジニアリングのヒント:
- 早期のサプライヤー関与: 設計の初期段階で、 CAS新素材(SicSino), などのSiCサプライヤーと連携する。 カスタムSiC製造 および材料科学に関する専門知識は、性能と製造性を考慮した設計を最適化することで、時間とコストを大幅に節約できる。CAS(Weifang)イノベーションパークを基盤とし、WeifangのSiC業界を支援してきた豊富な経験を持つCAS new materials(SicSino)は、設計、材料、プロセス、および評価技術に関する深い理解を有している。
- 包括的なアプリケーションの詳細を提供する: 流体組成、温度範囲、圧力、流量、研磨剤の有無と性質、および予想される部品寿命など、動作条件を明確に定義する。
- 反復プロトタイピング: 複雑または重要な部品については、大規模生産に移行する前に、設計と性能を検証するためのプロトタイピング段階を検討する。
これらの設計原則を遵守し、専門家と緊密に連携することで、エンジニアは堅牢で長寿命の流体処理ソリューションのために炭化ケイ素の優れた特性を最大限に活用できる。
精度の実現:SiC流体部品の公差、表面仕上げ、および寸法管理
要求の厳しい流体処理アプリケーションにおける炭化ケイ素部品の性能は、特にメカニカルシール面、ベアリング、バルブシート、および精密ノズルなどの部品の場合、厳しい寸法公差と特定の表面仕上げを実現できるかどうかに大きく依存する。SiC固有の硬度により、機械加工は困難になり、特殊なダイヤモンド工具と技術が必要となる。 達成可能な精度を理解することは、設計エンジニアと調達担当者の両方にとって不可欠である。
寸法公差:
- 焼結公差: 焼結炉から直接取り出された部品(焼結後)は、寸法公差が広くなる。これらは、成形方法、粉末特性、および焼結サイクルによって影響を受ける。SiCの一般的な焼結後の公差は、サイズと複雑さに応じて、寸法の±0.5%〜±2%の範囲になる場合がある。これらの公差が許容されるアプリケーションでは、焼結後の機械加工が最小限に抑えられ、または排除されるため、コストを削減できる。
- 機械加工された公差: 高精度を必要とするアプリケーションの場合、SiC部品は焼結後にダイヤモンド研削を受ける。これにより、はるかに厳しい公差が可能になる。
- 標準的な機械加工公差: 通常、±0.025 mm〜±0.1 mm(±0.001インチ〜±0.004インチ)の範囲。
- 精密機械加工公差: 重要な機能については、高度な研削およびラッピングプロセスにより、±0.005 mm〜±0.01 mm(±0.0002インチ〜±0.0004インチ)という厳しい公差を達成できる。ただし、不必要に厳しい公差を追求すると、コストが大幅に増加する。
表面仕上げ(粗さ):
SiC部品の表面仕上げは、特に動的シール面およびベアリングの場合、摩擦、摩耗、およびシール効率に直接影響するため、非常に重要である。
- 焼結後の表面: 焼結後の部品の表面仕上げは一般的に粗く、多くの場合、Ra = 1.0〜3.0μmの範囲。
- 地表: ダイヤモンド研削により、通常Ra = 0.2〜0.8μmの、より滑らかな表面を実現できる。これは、多くの汎用流体処理部品に適している。
- ラップおよび研磨された表面: メカニカルシール面や精密ベアリングなどの高性能アプリケーションでは、ラッピングと研磨を使用して、非常に細かい表面仕上げを実現する。
- ラップ: Ra = 0.05〜0.2μm。
- 研磨仕上げ: Ra<0.025 μm(鏡面仕上げ)を実現でき、極めて低い摩擦と優れたシール性能が得られます。このような仕上げは、 高性能SiCメカニカルシール.
に不可欠です。以下の表は、異なる加工段階における一般的な表面仕上げ値を示しています。
加工段階 | 代表的な表面粗さ (Ra) | 一般的な用途 |
---|---|---|
焼結まま | 1.0〜3.0 μm | ライナー、重要度の低い構造部品 |
研削 | 0.2-0.8 μm | 一般的なポンプ部品、バルブ本体 |
ラップ仕上げ | 0.05-0.2 μm | 標準的なメカニカルシール面、重要度の低いベアリング |
研磨仕上げ(精密ラップ仕上げ) | <0.05 μm | 高性能メカニカルシール面、精密ベアリング |
寸法精度と安定性:
炭化ケイ素は、広範囲の温度にわたって優れた寸法安定性を示し、一般的な工業運転温度ではクリープを起こしません(一部の金属やプラスチックとは異なります)。 これは、コンポーネントが必要な精度で製造されると、その耐用年数を通じて寸法と形状を維持し、一貫した性能に貢献することを意味します。
性能とコストへの影響:
- より厳しい公差とより微細な表面仕上げは、追加の機械加工工程(研削、ラップ、研磨)と増加した検査要件により、必然的に製造コストの上昇につながります。
- しかし、重要な用途では、改善された性能(例えば、シールの漏れの減少、ベアリングの摩擦の低下、寿命の延長)が投資を正当化することがよくあります。
- 性能とコストのバランスを取るためには、用途に本当に必要な精度レベルのみを指定することが重要です。
CAS新素材(SicSino)は、中国のSiC産業の中心地である濰坊における地位と、中国科学院の高度な技術力を活用し、厳しい公差と表面仕上げの要件を満たすための十分な設備を備えています。材料開発から最終製品評価まで、統合されたプロセスにより、 カスタムSiC流体処理部品 が、卸売業者、技術調達の専門家、OEMの要求の厳しい仕様を満たすことを保証します。国内トップクラスの専門チームがカスタマイズされた生産を専門とし、高度な測定および評価技術を含む幅広い技術の恩恵を受けています。
SiC流体部品における最高の性能のための課題の克服と後処理
炭化ケイ素は流体処理において優れた利点を提供しますが、製造および用途において特定の課題も提示します。これらの課題と必要な後処理工程を理解することが、材料の潜在能力を最大限に引き出し、信頼性の高い長期的な性能を確保するための鍵となります。ここで、経験豊富な 工業用SiCサプライヤー は貴重なものとなる。
の専門知識が役立ちます。炭化ケイ素に関する一般的な課題:
- 脆さ: ほとんどのセラミックと同様に、SiCは金属と比較して破壊靭性が低い脆性材料です。これは、高い衝撃荷重または過度の引張応力を受けた場合、壊滅的な故障を起こしやすいことを意味します。
- 緩和: 慎重な設計(応力集中を避け、圧縮荷重を使用)、組み立ておよびメンテナンス中の適切な取り扱い、および機械的衝撃からのコンポーネントの保護が重要です。材料の選択(例えば、特定の衝撃シナリオに対するより強靭なグレードまたは複合材料。ただし、他の特性が損なわれる可能性があります)も役割を果たす可能性があります。
- 加工の複雑さとコスト: SiCの極端な硬度は、焼結後の成形または仕上げをダイヤモンド工具を使用して行う必要があることを意味します。これは、金属の機械加工よりも遅く、コストのかかるプロセスです。
- 緩和: 設計は、初期の成形および焼結段階でニアネットシェイプを達成し、焼結後の研削量を最小限に抑えることを目指すべきです。のようなメーカーとの早期の連携 CAS新素材(SicSino) は、製造可能性のために設計を最適化するのに役立ちます。
- 熱衝撃感受性(一部のグレード/設計の場合): SiCは一般的に優れた耐熱衝撃性を持っていますが、急速かつ極端な温度変化は、特に複雑な形状または拘束された設計において、亀裂につながる応力を誘発する可能性があります。
- 緩和: 適切なSiCグレード(例えば、微細な結晶構造を持つNBSCまたはSSiC)の選択、均一な加熱/冷却のための設計、および用途の熱サイクルパラメータの理解が重要です。
- 他の材料との接合: 設計上の考慮事項で述べたように、熱膨張係数の違いにより、SiCを金属部品に効果的に接合することは複雑になる可能性があります。
- 緩和: 特殊な接合技術(例えば、活性金属ろう付け、慎重な設計による焼きばめ、コンプライアントな中間層を使用した機械的クランプ)を採用するには、専門知識が必要です。
SiC流体部品に必要な後処理工程:
最初の焼結工程の後、高性能流体処理部品の寸法および表面仕上げの要件を満たすために、いくつかの後処理工程が必要になることがよくあります。
- 精密研削: これは最も一般的な後処理工程であり、ダイヤモンド砥石を使用して、シャフト、ベアリングレース、およびシール面などの重要な領域で、厳しい寸法公差、特定のプロファイル、および改善された表面仕上げを実現します。
- ラッピングとポリッシング: のような、非常に滑らかで平坦な表面を必要とする用途の場合、 SiCメカニカルシール面は、 または高精度バルブシートの場合、ラッピングおよび研磨が採用されます。これらのプロセスでは、徐々に微細なダイヤモンド研磨剤を使用して、鏡面のような仕上げ(Ra<0.05μm)を実現し、摩擦と漏れを最小限に抑えます。
- エッジ処理(面取り/R付け): 亀裂の開始点として作用する可能性のある鋭いエッジでのチッピングのリスクを軽減するために、エッジはしばしば面取りまたはR付けされます。これは、頻繁に取り扱われる部品または接触応力を受ける部品にとって特に重要です。
- クリーニング: 洗浄:
- シール(高密度SiCではあまり一般的ではありません): SSiCは本質的に高密度ですが、一部のRBSiCグレードにはわずかな残留気孔率がある可能性があります。絶対的な不浸透性が必要な特定の用途、または多孔質SiCがろ過に使用される場合は、樹脂または他のシーラントによる含浸が行われる場合があります。ただし、ほとんどの耐腐食性および耐摩耗性流体処理用途では、後シールなしの高密度SSiCまたはRBSiCが推奨されます。
- 検査と品質管理: 高度な計測機器(CMM、表面粗さ測定器、干渉計)を使用した厳格な検査は、寸法、公差、および表面仕上げに関するすべての仕様が満たされていることを確認するために不可欠です。
これらの課題を克服し、適切な後処理を実施するには、高度な専門知識と特殊な機器が必要です。 CAS新素材(SicSino) はこの分野で優れています。材料科学、プロセスエンジニアリング、設計最適化、および綿密な測定と評価を含む包括的な技術力により、高品質でコスト競争力のある製品を製造できます。 カスタム炭化ケイ素部品. 濰坊の地元企業への支援は、SiC生産チェーン全体の技術進歩を推進し、顧客が最先端の製造慣行の恩恵を受けることを保証します。この統合されたアプローチにより、一般的なSiCの課題を効果的に軽減し、最高の性能を発揮できる状態の部品を提供できます。
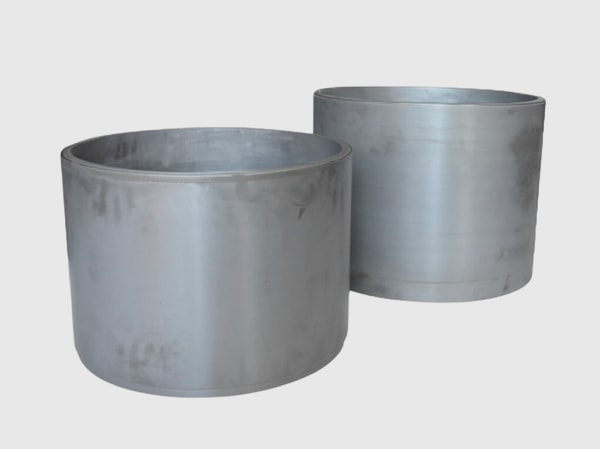
流体処理における炭化ケイ素に関するよくある質問(FAQ)
調達管理者、エンジニア、および技術バイヤーは、流体処理用途に炭化ケイ素を検討する際に、しばしば質問があります。以下は、一般的な質問への回答です。
Q1: 腐食性流体処理において、ステンレス鋼や他のセラミック(例えば、アルミナ)のような従来の材料と比較して、SiCの主な利点は何ですか?
A1: 炭化ケイ素(SiC)は、いくつかの明確な利点を提供します。* 優れた耐食性: SiC(特にSSiC)は、ほとんどのステンレス鋼やアルミナよりも広い温度範囲にわたって、強酸や強塩基を含む、はるかに広範囲の攻撃的な化学物質に対して実質的に不活性です。 例えば、アルミナは強アルカリおよびフッ化水素酸による攻撃を受けやすいです。* 卓越した耐摩耗性: SiCはステンレス鋼やアルミナよりも著しく硬いです。これにより、研磨スラリーからの摩耗に対する耐性がはるかに高くなり、コンポーネントの寿命が劇的に延びます。* 高温能力: SiCは、ステンレス鋼や他のほとんどの工業用セラミックよりもはるかに高い温度で、その機械的特性と耐腐食性を維持します。* 熱伝導率: SiCは一般的にアルミナよりも高い熱伝導率を持ち、これはメカニカルシールのような用途で熱を放散するのに有益です。 * 硬度と剛性: SiCの高い硬度と剛性は、寸法安定性と負荷下での変形に対する耐性に貢献します。
ステンレス鋼は良好な一般的な耐腐食性と靭性を提供し、アルミナは適度な摩耗と腐食に対する費用対効果の高いセラミックですが、SiCはこれらの材料が早期に故障する最も極端な条件で優れています。
Q2: カスタムSiCコンポーネントのコストは、大量生産された金属またはプラスチック部品と比較してどうですか?
A2: の初期調達コストは、 カスタムSiC部品 一般的な金属(ステンレス鋼など)またはプラスチックで作られた大量生産部品よりも通常は高くなります。これは、原材料のコスト、エネルギー集約的な製造プロセス(高温での焼結)、および精密なダイヤモンド機械加工によるものです。
しかし、 総所有コスト(TCO)SiC部品の利点:* 大幅な長寿命化: 交換頻度の低減。* ダウンタイムの削減: 生産性の向上。* メンテナンスコストの削減: 修理・交換の減少。* プロセス効率の向上: 耐摩耗性による安定した性能。 多くの要求の厳しい用途において、SiC部品の長寿命と信頼性は、頻繁な交換が必要な安価な代替品と比較して、TCOの削減につながります。 OEM用SiC部品 長期的な信頼性が最も重要な重要な用途によく指定されます。
Q3:CAS new materials (SicSino)のようなサプライヤーからカスタムSiC流体処理部品の正確な見積もりを得るには、どのような情報を提供する必要がありますか?
A3:正確かつ迅速な見積もりを受け取るには、以下の情報をできる限り提供してください。* 詳細な図面またはCADモデル: すべての寸法、重要な公差、表面仕上げの要件を含みます。* 材料グレード: 希望するSiCグレード(例:SSiC、RBSiC)を指定するか、用途を説明して、サプライヤーが適切なグレードを推奨できるようにします。 * 動作条件: * 流体組成: 特定の化学物質、濃度、pH。* 研磨剤の有無: 固体の種類、サイズ、濃度。* 温度範囲: 最小、最大、および通常の動作温度。* プレッシャーだ: 運転圧力と圧力変動の有無。* 流量: 摩耗または腐食に関連する場合。* 必要量: 該当する場合は、予想される年間使用量を含みます。* アプリケーションの説明 部品がどのように、どこで使用されるかを簡単に説明してください。* 特定の試験または認証要件。
包括的な情報を提供することで、次のようなサプライヤーは、 CAS新素材(SicSino) お客様のニーズを十分に理解し、最も適切で費用対効果の高いソリューションを提供できます。彼らのチームは、 卸売バイヤー そして 技術調達の専門家 仕様を正確に定義するために協力した経験があります。
Q4:SiC部品は修理できますか、それとも通常は交換されますか?
A4:一般的に、SiC部品は非常に硬く、脆い性質があるため、損傷したSiC部品の修理は非常に難しく、経済的に実行可能でないことがよくあります。SiCを溶接またはパッチしようとすると、欠陥が生じたり、元の特性を回復できなかったりする可能性があります。十分な材料ストックが存在し、損傷が表面的なものであれば、一部の限られたケースでは、シール面の再ラッピングのような軽微な表面再加工が可能かもしれません。ただし、ほとんどの種類の損傷(亀裂、重大な欠け、または公差を超える摩耗)の場合、 交換が標準的なアプローチです。SiC部品の設計思想は、介入の必要性を最小限に抑えるために、初期の耐用年数を最大化することに重点を置いています。
Q5:カスタムSiC流体処理部品の標準的なリードタイムはどのくらいですか?
A5: カスタムSiC流体処理部品 のリードタイムは、いくつかの要因に基づいて大きく異なる場合があります。* 部品の複雑さ: より複雑な設計では、より複雑なツーリングとより長い製造時間が必要です。* 材料グレード: 一部の特殊なグレードでは、製造サイクルが長くなる場合があります。* 注文数量 大量生産では、全体的なリードタイムが長くなる可能性がありますが、生産効率が向上する場合があります。少量で高度にカスタマイズされた注文には、専用のセットアップが必要になる場合があります。* 公差と表面仕上げの要件: より厳しい仕様では、より広範な機械加工と検査が必要になり、時間がかかります。* ツーリングの要件: 新しい金型または特殊なツーリングが必要な場合は、初期のリードタイムが長くなります。* 現在のサプライヤーの作業負荷: 需要がピークの時期には、リードタイムに影響を与える可能性があります。
標準的なリードタイムは、単純な繰り返し注文の部品の場合は数週間から、新しいツーリングを必要とする非常に複雑な初回部品の場合は数か月まで幅があります。リードタイムの要件については、常にサプライヤーと話し合うのが最善です。 CAS新素材(SicSino)は、統合されたプロセスと効率的な生産への取り組みにより、中国国内およびグローバルな顧客向けに、高品質のカスタマイズされた炭化ケイ素部品の競争力のあるリードタイムを提供するよう努めています。
結論要求の厳しい産業環境におけるカスタム炭化ケイ素の不変の価値
産業用流体処理における卓越した運用と信頼性を絶え間なく追求する中で、重要な部品の材料の選択は最も重要です。カスタム炭化ケイ素は、腐食、摩耗、高温、および極端な圧力が従来の材料を限界を超えて押し上げる環境において、その優れた能力を明確に示しています。 SiC固有の特性、つまり、その卓越した硬度、化学的安定性、熱安定性、および耐摩耗性は、部品の寿命の大幅な延長、メンテナンス間隔とダウンタイムの大幅な削減、およびプロセスの一貫性の向上という具体的な利点に直接つながります。
を選ぶ カスタムSiCソリューション エンジニアや調達担当者は、標準的な製品を超えて、特定のアプリケーションの課題に合わせて正確に設計された部品を入手できます。この調整されたアプローチは、最適なパフォーマンスを保証し、特に総所有コストを考慮する場合に、投資収益率を最大化します。ポンプインペラーやメカニカルシールから、バルブトリムや特殊ノズルまで、 カスタマイズされた炭化ケイ素部品 は、化学処理、エネルギー、航空宇宙、製造など、多数の業界にわたる流体処理システムの効率と安全性を高める上で極めて重要です。
適切なサプライヤーの選択は、適切な材料の選択と同じくらい重要です。 CAS新素材(SicSino) のようなパートナーは、単なる部品以上のものを提供します。中国のSiC製造の中心地である濰坊市に根ざした包括的な専門知識を提供します。中国科学院(CAS)とその国立 技術移転 センターの強力な科学技術力に支えられたSicSinoは、より高品質でコスト競争力のあるカスタムSiC部品を提供するだけでなく、材料選択、設計最適化、プロセス統合に関する豊富な知識も提供します。数多くの地元企業の技術進歩を支援してきた実績は、品質と革新へのコミットメントを裏付けています。
さらに、独自の特殊SiC生産を確立しようとしている組織のために、CAS新材料(SicSino)は比類のない技術移転サービスを提供し、工場設計から試作までターンキーソリューションを提供します。この独自の能力により、高度セラミックスにおける自給自足と技術的リーダーシップを目指す企業にとって、戦略的パートナーとしての地位を確立しています。
結論として、カスタム炭化ケイ素を採用することは、回復力、効率、長期的な性能への投資です。最も要求の厳しい流体処理の課題を克服しようとしている技術バイヤー、エンジニア、OEMにとって、 CAS新素材(SicSino) のような知識豊富で有能なサプライヤーとの提携は、世界クラスのSiCソリューションへのアクセスと、産業生産性の向上と優れた競争力を得るための道筋を保証します。
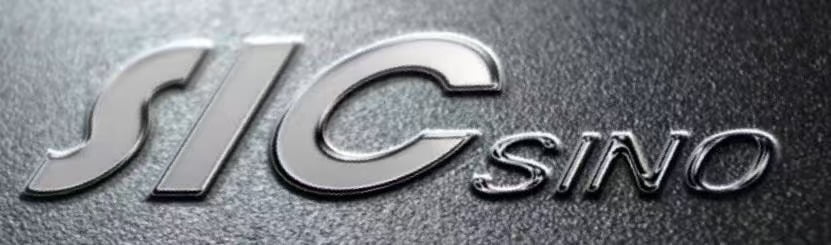
SicSino - CAS新素材
私たちCAS新材料(SicSino)は、2015年以来、炭化ケイ素製造技術の導入と実践を行い、現地企業の大規模生産と製品プロセスの技術進歩を支援してきました。当社は、現地炭化ケイ素産業の出現と継続的な発展の目撃者である。
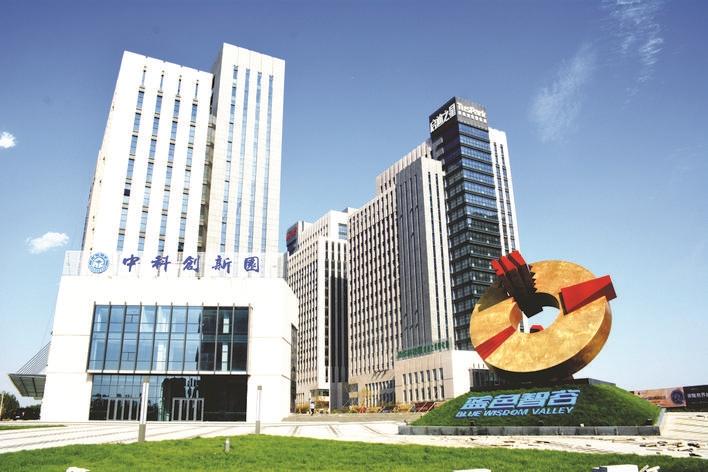