Tech Transfer
To build a SiC production plant: full process support and strategic cooperation
01. Industry opportunities
a blue ocean market worth hundreds of billions for SiC products
With the global manufacturing industry’s upgrade towards extreme working conditions such as high temperature, wear resistance, and corrosion resistance, silicon carbide (SiC), as the core material of third-generation semiconductors and advanced ceramics, is witnessing an explosive growth in demand.
In fields such as semiconductor wafer manufacturing, photovoltaic equipment, new energy vehicles, chemical engineering, and metallurgy, the market gap for high-performance silicon carbide parts (such as crucible supports, sealing rings, heat exchangers, etc.) continues to expand.
If your region has an industrial foundation or policy dividends, investing in the construction of a SiC production manufacturer will become a strategic choice to seize the market opportunity.
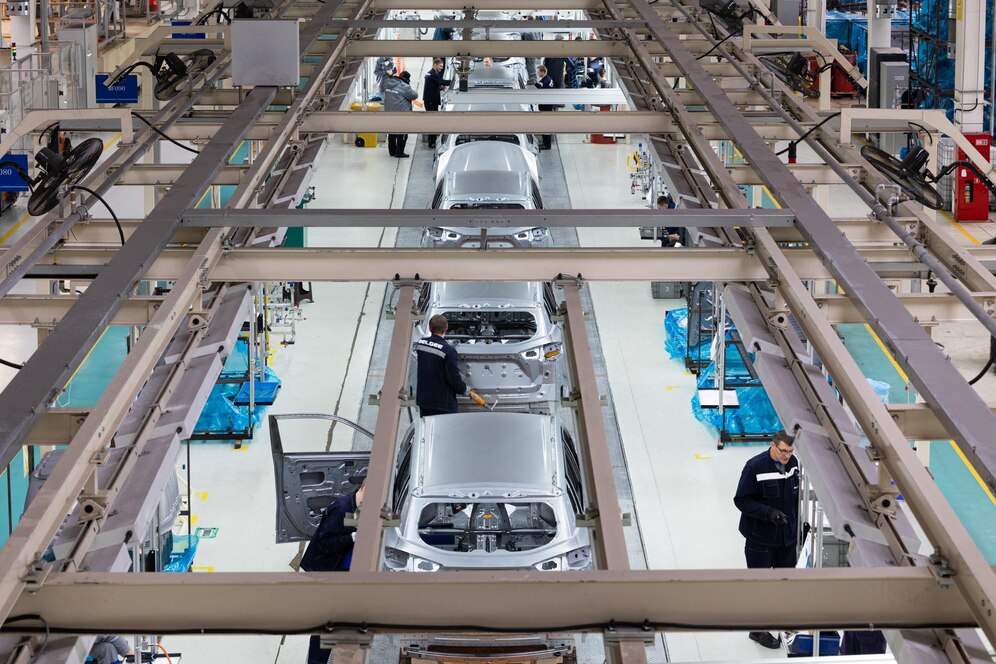
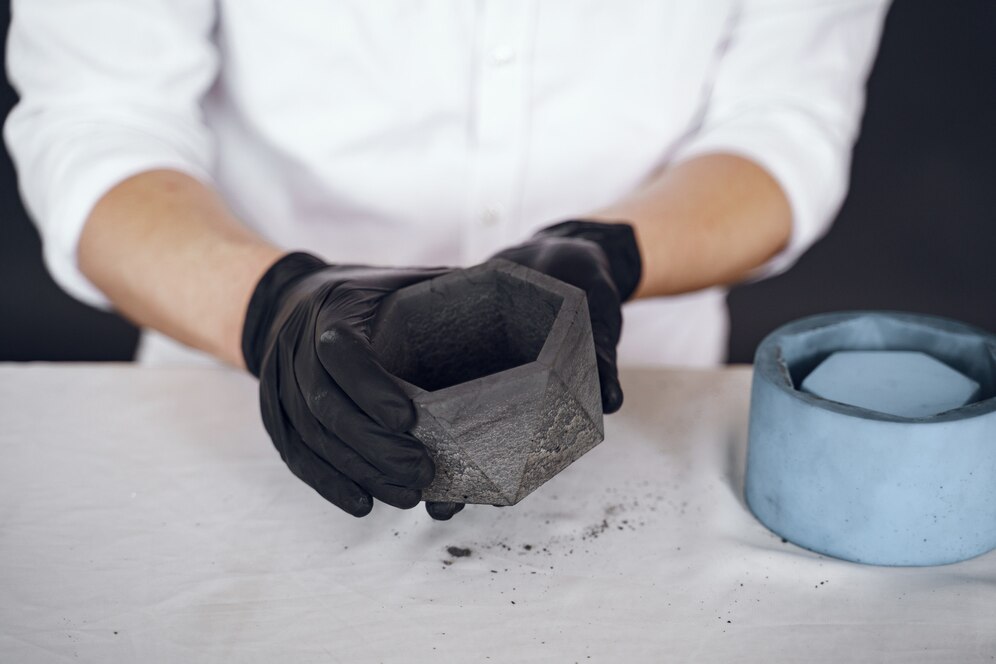
02.Our core strength
full-cycle empowerment from planning to implementation
CAS New Materials(SicSino), boasts a first-class professional team in China, which is dedicated to the customized production of SiC products. With our support, 19 local enterprises have already benefited from our technology.
Our background and technical support come from the Chinese Academy of Sciences (CAS). We possess a wide range of technologies, such as materials, process, design, measurement, and evaluation technologies, as well as an integrated process from materials to products.
As a technology-oriented team that has been deeply engaged in the field of silicon carbide for more than a decade, we adopt a dual-driven model of “technology + engineering” to provide you with one-stop solutions ranging from factory establishment consultation to production operation.
Whether you are a novice in the industry or an investor looking to expand production capacity, our services can precisely match your needs, reduce the cost of trial and error, and accelerate the realization of production capacity.
03.Full-process Support Service System for Factory Establishment
3.1 – Consultation on Establishing a SiC Parts Factory – The Key Link to Decode Technology and the Market
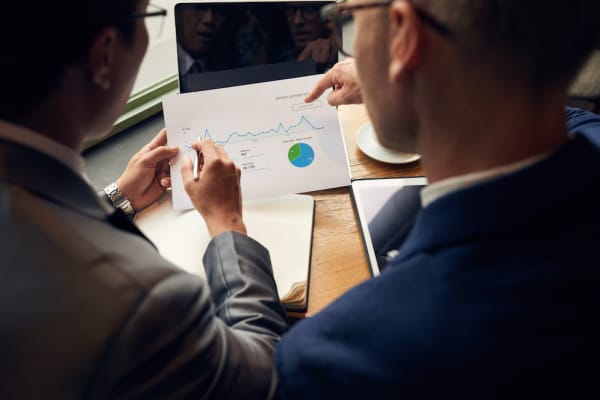
Market Feasibility Assessment
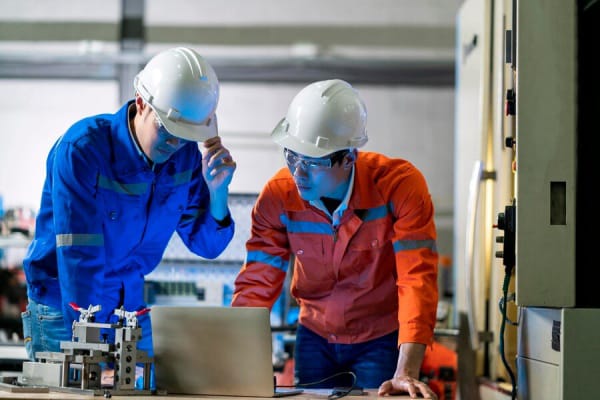
Customization of Technical Routes
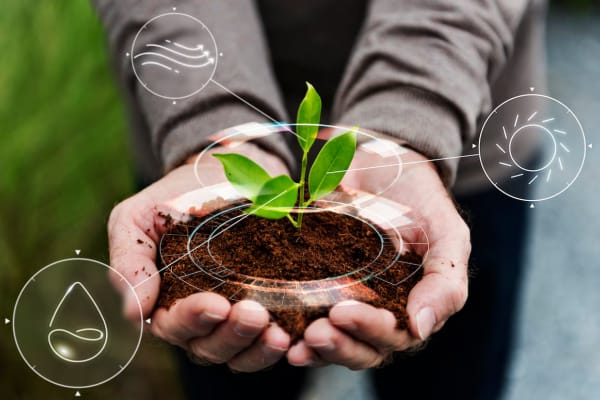
Compliance and Sustainability Planning
3.2 – Comprehensive Factory Planning and Design – Creating an Intelligent and Flexible Production Base
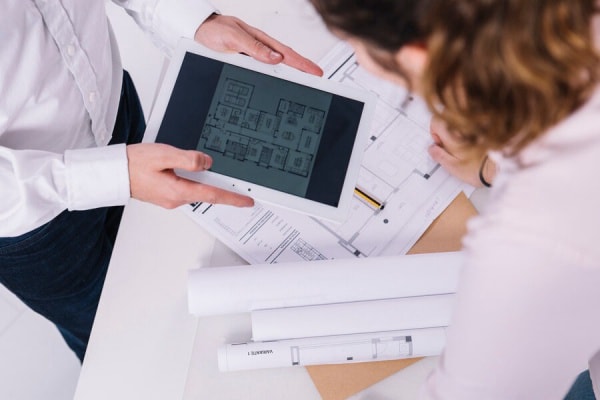
Factory Area Planning and Process Layout
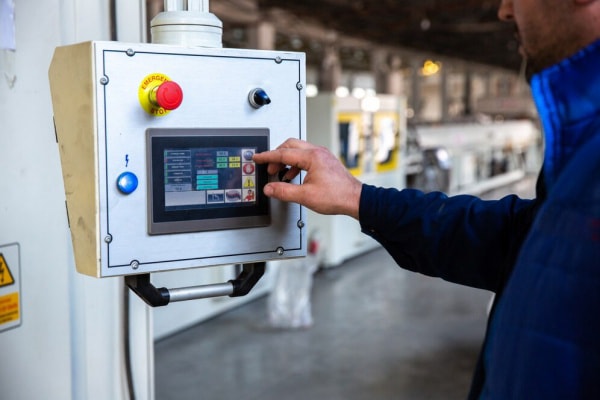
Construction of an Intelligent Production Line

Establishment of a Quality Control System
04. Why choose to collaborate with us?
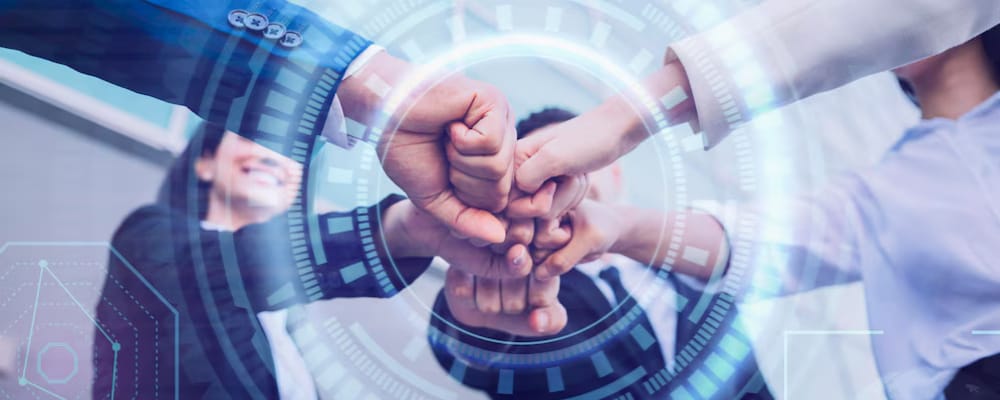
Profound Technical Accumulation
The core team consists of members from the Chinese Academy of Sciences and local personnel with more than 20 years of experience in silicon carbide production. We have successfully established over 10 silicon carbide parts factories, and on average, we have shortened the factory establishment cycle for users by 30%.
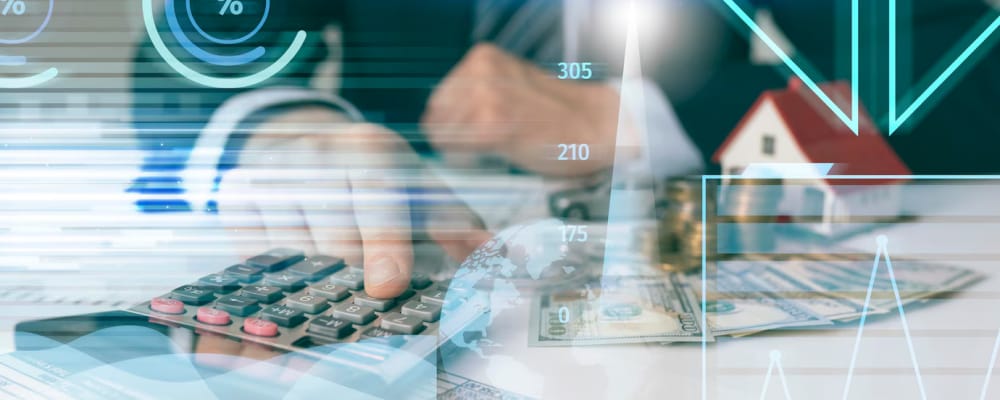
Precise Cost Control
Through large-scale procurement of equipment and optimization of process parameters (for example, reducing the sintering cycle from 72 hours to 48 hours), we help users reduce production costs by 20%-30%.
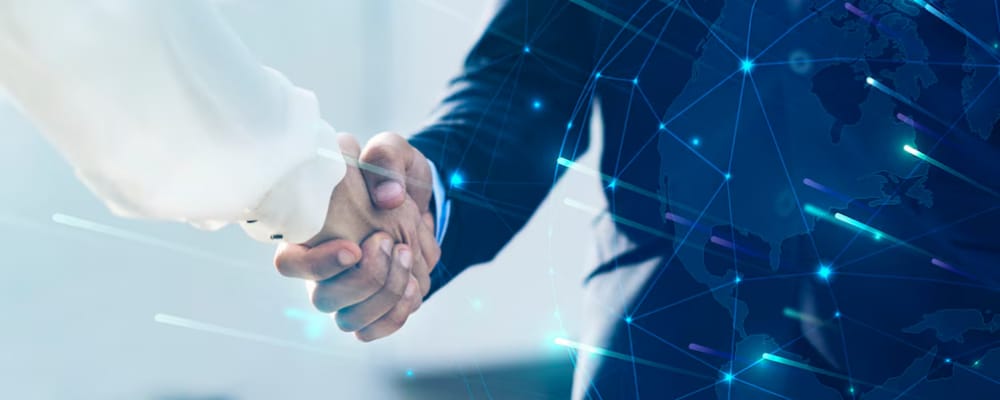
Long-term Empowerment and Support
We provide technical training during on-site installation as well as long-term technical training and support. We also offer technical upgrading services after production starts (such as the transformation plan from the RB-SiC production line to the SSiC production line).
05. Collaborate process
efficient implementation from blueprint to production
Demand Diagnosis
After receiving the user’s “Letter of Intent for Factory Establishment”, we will provide a preliminary feasibility analysis within 3 working days.
Scheme Design
After signing the cooperation agreement and receiving the advance payment, we will deliver the “Factory Planning Scheme” (including process flow diagrams, equipment lists, and investment budgets) within 4 to 8 weeks.
Construction Support
Assist in equipment procurement and provide on-site construction guidance to ensure that the project complies with industry standards (for example, the fire protection rating of high-temperature workshops is ≥ Class II).
Production Launch and Acceptance
Provide trial production process debugging and employee operation training until the qualified product rate stabilizes above 95%.
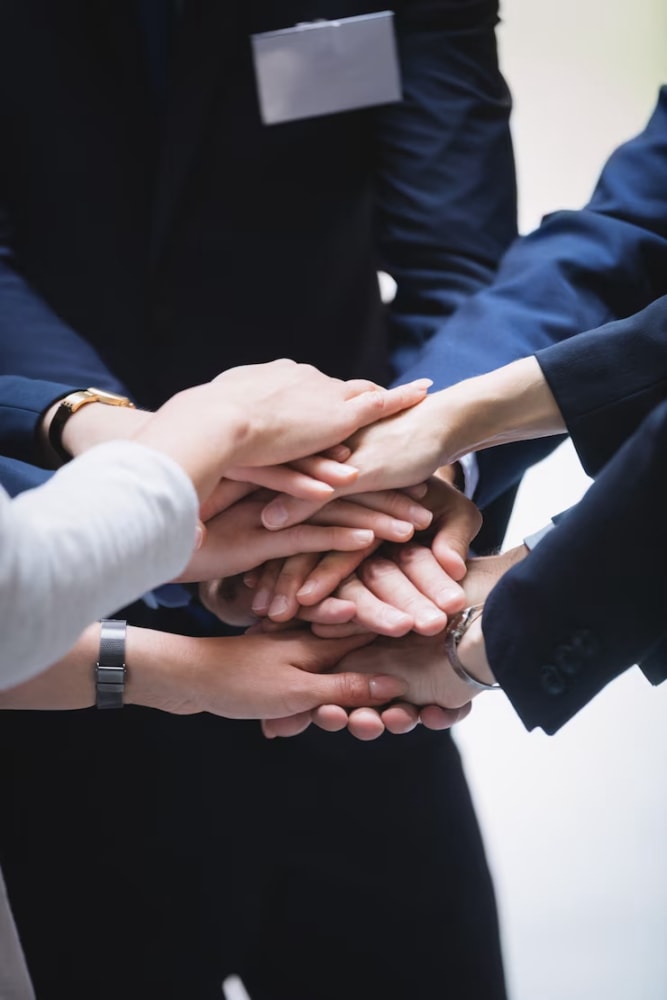
Join hands
to plan for the future and establish a new benchmark for SiC manufacturing
Against the backdrop of the upgrading of high-end manufacturing, silicon carbide materials are becoming an “essential requirement” in the industrial field.
We are not just suppliers of equipment and technology, we are strategic partners who deeply understand the pain points of the industry.
From the layout of every “screw hole” at the initial stage of factory construction to every technological iteration after production commences, we will always stand side by side with you.
Contact us immediately
Contact us immediately, and unlock a customized factory-building plan. Accelerate the transformation of your investment returns from a “blueprint” to a “real-life scenario”.