Silicon Carbide for Filtration: Revolutionizing Separation in Demanding Environments
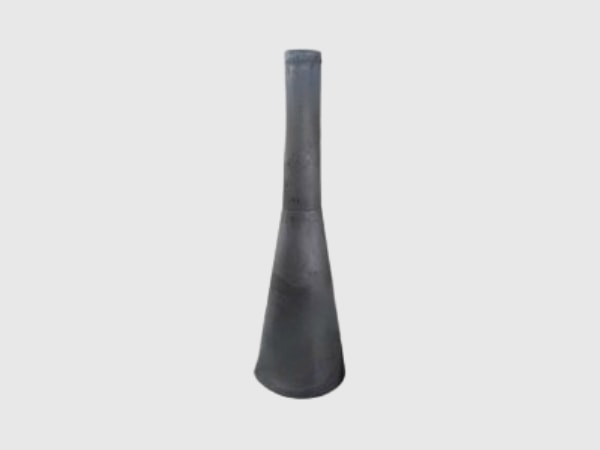
Share
In the ever-evolving landscape of industrial processing, the demand for highly efficient, durable, and reliable filtration solutions has never been greater. As industries push the boundaries of temperature, pressure, and chemical aggression, conventional filter materials often fall short. This is where custom silicon carbide (SiC) filtration products emerge as a game-changing technology. Renowned for their exceptional thermal resistance, mechanical strength, and chemical inertness, SiC ceramics offer unparalleled performance in some of the most challenging filtration applications imaginable. For engineers, procurement managers, and technical buyers in sectors ranging from semiconductor manufacturing and chemical processing to energy production and environmental protection, understanding the capabilities of custom SiC filters is crucial for optimizing processes, enhancing product quality, and achieving operational excellence.
The critical nature of filtration in industrial processes—whether for product purification, emissions control, or resource recovery—necessitates materials that can withstand extreme conditions without compromising performance. Standard filter materials like polymers, metals, or even other ceramics can degrade, corrode, or fail when exposed to high temperatures, abrasive particles, or corrosive chemicals. Silicon carbide, however, thrives in these environments. Its unique combination of properties makes it an ideal candidate for creating robust filter elements, including membranes, porous tubes, and diesel particulate filters (DPFs), tailored to specific operational needs. The ability to customize SiC filter components further amplifies their value, allowing for precise control over porosity, pore size distribution, and geometric configurations to meet the exacting demands of high-performance industrial applications. This ensures not just effective filtration, but also longevity and cost-effectiveness in the long run.
Key Industrial Applications: Exploring the Versatility of SiC Filters Across Sectors
The exceptional properties of silicon carbide make it a highly sought-after material for filtration applications across a diverse range of industries. Its ability to perform reliably under extreme conditions translates into significant operational advantages and cost savings. Custom SiC filters, including SiC ceramic membranes, porous silicon carbide tubes, and SiC filter elements, are increasingly being adopted where other materials fail.
One of the primary sectors benefiting from SiC filtration is the chemical processing industry. Here, filters are often exposed to highly corrosive acids, bases, and organic solvents, frequently at elevated temperatures. SiC’s outstanding chemical inertness ensures long service life and prevents contamination of the processed media. Applications include catalyst recovery, purification of aggressive chemicals, and separation of fine particles from corrosive slurries.
In the power generation sector, particularly in coal-fired power plants and waste-to-energy facilities, hot gas filtration is critical for removing particulate matter from flue gases before they are released into the atmosphere. SiC filters, often in the form of candle filters, can operate at temperatures exceeding 1000∘C, enabling efficient and reliable particulate removal in harsh environments, thus helping plants meet stringent emission regulations.
Wastewater treatment and water purification represent another significant area for SiC filtration. SiC ceramic membranes offer high flux, excellent chemical resistance for cleaning cycles (e.g., backwashing with aggressive chemicals), and resistance to fouling compared to polymeric membranes. They are used in microfiltration (MF) and ultrafiltration (UF) processes for treating industrial wastewater, oily water separation, and producing high-purity water.
The automotive industry relies heavily on SiC for diesel particulate filters (DPFs) and, increasingly, gasoline particulate filters (GPFs). SiC DPFs efficiently trap soot particles from diesel exhaust. The material’s high thermal conductivity and thermal shock resistance are crucial for the regeneration process, where trapped soot is burned off at high temperatures.
In the pharmaceutical and food & beverage industries, while stainless steel is common, SiC offers advantages in applications involving aggressive cleaning agents or high temperatures. Its inertness ensures no leaching or contamination, making it suitable for sterile filtration and clarification processes.
The semiconductor and electronics manufacturing industries require ultra-pure water and chemicals. SiC filters can provide fine filtration with high purity, ensuring that particulate contamination is minimized in critical manufacturing steps.
Moreover, the aerospace and metallurgy industries utilize SiC filters for molten metal filtration, removing inclusions and impurities to improve the quality and mechanical properties of cast components. The high-temperature strength and non-reactivity of SiC with molten metals are key advantages here.
CAS new materials (SicSino), situated in Weifang City, the hub of China’s silicon carbide customizable parts manufacturing, has been instrumental in advancing SiC production technology. Leveraging our deep understanding of material science and process engineering, developed through our association with the Chinese Academy of Sciences (CAS), we provide customized SiC filtration solutions to these diverse industries, ensuring optimal performance and reliability. Our expertise covers a wide array of SiC grades and manufacturing techniques, allowing us to tailor filter properties to the specific needs of each application.
Below is a table summarizing key applications and the benefits of SiC filters:
Industry Sector | Common SiC Filter Types | Key Benefits of Using SiC Filters |
---|---|---|
Chemical Processing | Porous tubes, membranes, catalyst carriers | Extreme corrosion resistance, high-temperature stability, longevity |
Power Generation | Candle filters, hot gas filter elements | High-temperature operation, thermal shock resistance, emission control |
Water & Wastewater | Membranes (MF/UF), tubular filters | High flux, chemical resistance, anti-fouling, long life |
Automotive | Diesel Particulate Filters (DPFs), GPFs | Efficient soot capture, high regeneration temperature tolerance |
Pharmaceutical | Fine filters, sterile filters | Inertness, cleanability, high-purity filtration |
Food & Beverage | Clarification filters, process stream filters | Chemical stability for cleaning, no taste/odor transfer |
Semiconductor | Ultrapure water/chemical filters | High purity, fine particle removal, chemical compatibility |
Metallurgy & Foundries | Molten metal filters (foam, extruded) | High-temperature strength, non-reactivity with molten metals |
Aerospace | Molten metal filters, specialized components | High-performance material for critical casting processes |
The versatility of industrial filtration solutions based on silicon carbide underscores its importance as a critical enabling technology for modern manufacturing and environmental protection.
Why Choose Custom Silicon Carbide for Your Filtration Needs? The Unmatched Advantages.
When standard filtration materials reach their limits, custom silicon carbide steps in to offer a robust and reliable solution. The inherent properties of SiC, combined with the ability to tailor components to specific application requirements, provide a compelling suite of advantages for technical procurement professionals, OEMs, and engineers seeking high-performance filtration. Choosing custom SiC filters is not just about replacing an existing part; it’s about upgrading the entire filtration process for enhanced efficiency, longevity, and operational reliability.
The primary advantages of silicon carbide in filtration include:
- Exceptional Thermal Resistance and Thermal Shock Capability: SiC can withstand extremely high operating temperatures (often exceeding 1400∘C for certain grades like Recrystallized SiC) without degradation. This is critical for applications like hot gas filtration or processes involving thermal cycling. Its low coefficient of thermal expansion and high thermal conductivity contribute to excellent thermal shock resistance, preventing cracking or failure during rapid temperature changes, such as during the regeneration cycles of Diesel Particulate Filters (DPFs).
- Superior Chemical Inertness and Corrosion Resistance: Silicon carbide exhibits remarkable resistance to a wide range of acids, alkalis, and corrosive gases across a broad temperature spectrum. This makes SiC ceramic membranes and filter elements ideal for chemical resistant filters in aggressive chemical processing, pharmaceutical manufacturing, and acidic wastewater treatment where other materials would quickly corrode and contaminate the process stream.
- High Mechanical Strength and Wear Resistance: SiC is an extremely hard and strong material, ranking close to diamond in hardness. This translates to excellent wear and abrasion resistance, crucial when filtering streams containing abrasive particles. Porous silicon carbide structures maintain their integrity even under high pressure differentials and in erosive environments, leading to longer filter life and reduced replacement frequency.
- Precisely Controlled Porosity and Pore Size Distribution: A key advantage of custom SiC filters is the ability to precisely engineer the microstructure. Manufacturers can tailor the porosity (the volume percentage of voids) and the pore size distribution to achieve specific filtration efficiencies, from coarse particle removal to microfiltration and even ultrafiltration. This ensures optimal particle capture while maintaining desired flow rates. CAS new materials (SicSino) leverages its advanced manufacturing technologies to produce SiC filters with highly uniform and customized pore structures.
- Excellent Permeability and Low Flow Resistance: Despite their fine pore structures, well-designed SiC filters can offer high permeability, leading to lower pressure drops across the filter. This reduces energy consumption for pumping and can increase throughput. The smooth internal surfaces of SiC pores can also contribute to reduced fouling.
- Long Service Life and Reduced Downtime: The combination of thermal stability, chemical inertness, and mechanical strength results in significantly longer operational lifetimes for SiC filters compared to many conventional filter media. This translates to reduced maintenance requirements, less frequent filter replacement, and minimized process downtime, leading to substantial cost savings over the filter’s lifecycle.
- Cleanability and Regenerability: Many SiC filters, particularly ceramic membranes and DPFs, can be effectively cleaned and regenerated multiple times. Common methods include backflushing, chemical cleaning (leveraging SiC’s chemical resistance), and thermal regeneration (for DPFs). This reusability further enhances the cost-effectiveness and sustainability of SiC filtration systems.
- Customization for Specific Applications: The term “custom” is key. Beyond material properties, custom SiC filter manufacturers like SicSino can produce filters in a wide variety of shapes (tubes, candles, discs, plates, complex geometries), sizes, and configurations, including specific end fittings or housing integrations. This allows for seamless integration into existing systems or the development of novel filtration solutions tailored to unique process challenges.
By opting for custom silicon carbide filtration components, industries can overcome the limitations of off-the-shelf solutions and achieve a higher degree of process control, efficiency, and reliability. The initial investment in custom SiC can be quickly offset by improved performance, extended filter life, and reduced operational costs, making it a strategically sound choice for demanding industrial applications.
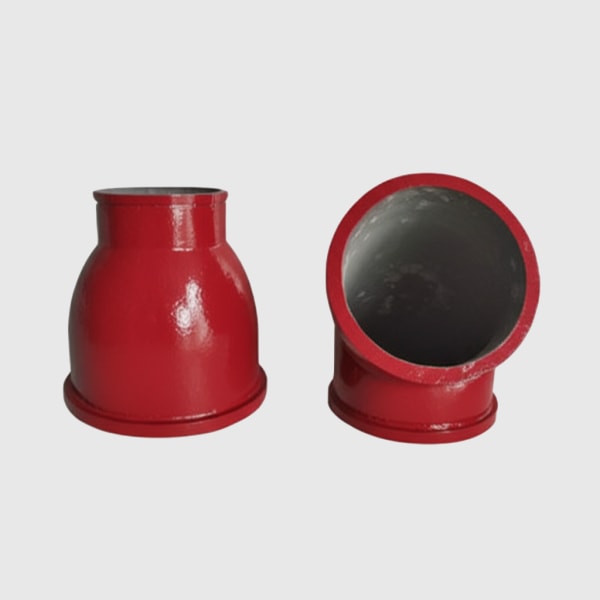
Navigating SiC Grades for Optimal Filtration Performance: Reaction-Bonded (RBSiC/SiSiC), Sintered (SSiC), and Recrystallized (RSiC) SiC
Choosing the correct grade of silicon carbide is paramount to achieving optimal performance and longevity in any filtration application. Different manufacturing processes yield SiC materials with varying microstructures, porosity levels, and thermomechanical properties. Understanding these distinctions allows engineers and procurement specialists to select the most suitable and cost-effective material for their specific needs. The primary commercially available grades relevant to filtration include Reaction-Bonded Silicon Carbide (RBSiC, also known as Siliconized Silicon Carbide or SiSiC), Sintered Silicon Carbide (SSiC), and Recrystallized Silicon Carbide (RSiC).
Reaction-Bonded Silicon Carbide (RBSiC / SiSiC): RBSiC is produced by infiltrating a porous compact of SiC grains and carbon with molten silicon. The silicon reacts with the carbon to form new SiC, which bonds the original SiC grains together. This process typically results in a dense material with little to no residual porosity, containing some free silicon (usually 8-15%).
- Properties for Filtration: While dense RBSiC is used for wear parts, porous versions can be engineered for filtration. The presence of free silicon can limit its use in extremely high temperatures (above 1350∘C) or in environments that react with silicon. However, it offers good mechanical strength, excellent wear resistance, and high thermal conductivity. Porous RBSiC can be tailored for specific pore sizes.
- Typical Filtration Applications: Molten metal filtration, hot gas filtration (at moderate temperatures), and applications requiring good abrasion resistance.
- Considerations: The free silicon phase might be a concern for chemical compatibility with certain aggressive media, particularly strong alkalis at high temperatures.
Sintered Silicon Carbide (SSiC): SSiC is produced by sintering fine SiC powder at very high temperatures (typically above 2000∘C) with the aid of sintering additives (like boron and carbon). This process results in a single-phase SiC material with very high purity and density, or controlled porosity if desired.
- Properties for Filtration: Porous SSiC offers exceptionally high chemical resistance across a wide pH range and can withstand very high temperatures (up to 1600∘C or higher in controlled atmospheres). It possesses excellent mechanical strength, hardness, and good thermal shock resistance. For filtration, SSiC can be manufactured into membranes with very fine and uniform pore sizes, making it suitable for microfiltration and ultrafiltration.
- Typical Filtration Applications: SiC ceramic membranes for aggressive liquid filtration, fine chemical purification, pharmaceutical applications, semiconductor process fluid filtration, and hot gas filtration where extreme purity and temperature resistance are required. SSiC DPFs are also common.
- Considerations: Generally, SSiC is more expensive than RBSiC due to the higher processing temperatures and finer raw materials required.
Recrystallized Silicon Carbide (RSiC): RSiC is produced by firing relatively coarse SiC grains at very high temperatures (often exceeding 2300∘C). During this process, finer SiC particles vaporize and re-condense around the coarser grains, forming strong intergranular bonds. This results in a material composed primarily of SiC with controlled, interconnected porosity.
- Properties for Filtration: RSiC is known for its excellent thermal shock resistance, high-temperature strength (usable up to 1650∘C or higher), and good permeability due to its typically larger and interconnected pores. It has good chemical resistance, though generally not as high as SSiC for certain extreme chemicals.
- Typical Filtration Applications: Diesel Particulate Filters (DPFs) benefit greatly from RSiC’s thermal properties. Also used for kiln furniture, setters, and supports where hot gas flow-through is desired, and in some coarse hot gas or molten metal filtration applications.
- Considerations: The porosity in RSiC is often coarser than what can be achieved with SSiC membranes, making it more suitable for particulate filtration rather than fine micro/ultrafiltration.
The following table provides a comparative overview of these SiC grades for filtration:
Property | Reaction-Bonded SiC (RBSiC/SiSiC) | Sintered SiC (SSiC) | Recrystallized SiC (RSiC) |
---|---|---|---|
Primary Composition | SiC, Free Silicon (8-15%) | SiC (High Purity) | SiC (High Purity) |
Max. Use Temperature | ∼1350∘C | ∼1600∘C (or higher) | ∼1650∘C (or higher) |
Porosity Control | Moderate to Good | Excellent (fine to coarse) | Good (typically coarser) |
Typical Pore Size Range | Microns to tens of microns | Sub-micron to tens of microns | Tens of microns to hundreds |
Chemical Resistance | Good (limited by free Si) | Excellent (best overall) | Very Good |
Thermal Shock Resistance | Good | Very Good | Excellent |
Mechanical Strength | High | Very High | Good to Moderate |
Relative Cost | Moderate | High | Moderate to High |
CAS new materials (SicSino), leveraging its position in Weifang, China’s SiC manufacturing heartland, and its strong backing from the Chinese Academy of Sciences (CAS), possesses deep expertise in all these SiC grades. We work closely with clients to understand their specific filtration challenges – be it temperature, chemical environment, particle size, or flow rate requirements. Our domestic top-tier professional team specializes in the customized production of silicon carbide products, assisting over 10 local enterprises with our advanced material, process, and design technologies. This allows us to recommend and manufacture the most appropriate SiC grade and filter design, ensuring higher-quality, cost-competitive customized silicon carbide components for wholesale buyers, technical procurement professionals, OEMs, and distributors worldwide. Whether you require the fine precision of SSiC membranes or the robust thermal stability of RSiC for DPFs, SicSino is your trusted partner.
Critical Design and Engineering Considerations for Custom SiC Filters: Maximizing Efficiency and Durability
Designing effective and durable custom SiC filters goes beyond simply selecting the right material grade. It involves a meticulous consideration of various engineering parameters that directly impact filtration efficiency, operational lifespan, and overall system performance. For procurement managers and engineers, understanding these design nuances is crucial when specifying custom silicon carbide filtration components. Collaborating with an experienced supplier like CAS new materials (SicSino), which offers in-depth customizing support, ensures these factors are optimized for your unique application.
Key design and engineering considerations include:
- Pore Size, Pore Size Distribution, and Porosity:
- Pore Size (μm): This is the most fundamental parameter, determining the size of particles that can be retained by the filter. It must be carefully matched to the application’s requirements – whether it’s coarse filtration, microfiltration (MF), or ultrafiltration (UF).
- Pore Size Distribution (PSD): A narrow PSD is generally preferred for precise separation, ensuring consistent performance. A wide PSD might lead to some larger pores allowing unwanted particles through or smaller pores clogging prematurely.
- Porosity (%): This refers to the void volume within the filter media. Higher porosity generally leads to higher permeability and lower pressure drop, but it can also affect mechanical strength. A balance must be struck based on flow rate requirements and mechanical load expectations. Porous silicon carbide structures need optimized porosity.
- Permeability and Flux:
- Permeability: This measures the ease with which a fluid can flow through the porous filter medium under a given pressure gradient. Higher permeability is desirable for achieving high flow rates with minimal energy consumption. It’s influenced by pore size, porosity, and the interconnectivity of pores.
- Flux: Defined as the volume of fluid passing through a unit area of the filter per unit time. It’s a critical performance indicator, directly related to permeability and the applied pressure.
- Mechanical Strength and Structural Integrity:
- SiC filters must withstand the mechanical stresses imposed during operation, including pressure differentials (transmembrane pressure), vibrations, and handling during installation and cleaning.
- The design must account for wall thickness, overall geometry, and potential stress concentration points. Finite Element Analysis (FEA) may be employed for complex designs to predict mechanical behavior.
- Filter Geometry and Configuration:
- SiC filter elements can be manufactured in various forms:
- Tubular filters: Common for cross-flow filtration and applications requiring high surface area.
- Candle filters: Often used in hot gas filtration, providing robust, elongated filtering elements.
- Disc filters/Membranes: Suited for dead-end filtration or applications where flat sheet configurations are preferred. SiC ceramic membranes are a prime example.
- Foam filters: Used in molten metal filtration, offering a tortuous path for particle capture.
- Custom shapes: For specialized equipment or unique process requirements.
- The choice of geometry impacts surface area, flow patterns, ease of cleaning, and how the filter integrates into the overall system.
- SiC filter elements can be manufactured in various forms:
- Sealing and Housing Integration:
- Effective sealing is critical to prevent bypassing of the filter element, ensuring that all fluid passes through the porous media.
- The design must consider appropriate sealing mechanisms (e.g., O-rings, gaskets, compression fittings) compatible with the operating temperature, pressure, and chemical environment.
- The interface between the SiC filter element and its housing requires careful design to avoid stress concentrations on the ceramic component.
- Thermal Management (for high-temperature applications):
- In applications like hot gas filtration or DPF regeneration, the filter’s ability to withstand and manage thermal stresses is crucial.
- Design considerations include material selection (e.g., RSiC for thermal shock), gradual heating/cooling rates if possible, and features that accommodate thermal expansion.
- Manufacturability and Cost:
- Complex geometries or extremely tight tolerances can increase manufacturing difficulty and cost.
- Design for Manufacturability (DfM) principles should be applied, balancing performance requirements with practical production capabilities. CAS new materials (SicSino), with its extensive experience in producing custom SiC parts, can provide valuable input on DfM to ensure cost-effective solutions without compromising quality. Our presence in Weifang, a hub for SiC production, allows us to optimize manufacturing processes.
By systematically addressing these design considerations, industrial filtration solutions utilizing custom SiC can be engineered for maximum efficiency, durability, and cost-effectiveness. SicSino’s approach, backed by the technological prowess of the Chinese Academy of Sciences, involves a collaborative process with our clients. We translate your specific operational needs into robust SiC filter designs, ensuring that the final product delivers superior performance in your demanding application.

Achieving Precision: Tolerance, Surface Finish, and Post-Processing for SiC Filters
Once the optimal SiC grade and fundamental design parameters for a filtration component are established, achieving the required precision through careful control of tolerances, surface finish, and necessary post-processing becomes critical. These factors significantly influence the filter’s fit, sealing, performance, and longevity, especially in applications demanding high accuracy and reliability. For B2B buyers and technical procurement professionals, understanding a supplier’s capabilities in these areas is key to sourcing high-quality custom SiC filters.
Dimensional Tolerances: Silicon carbide components, being hard ceramics, are typically formed to near-net shape and then machined (if necessary) using diamond grinding. The achievable dimensional tolerances depend on the SiC grade, the manufacturing process (pressing, extrusion, slip casting, etc.), the size and complexity of the part, and the extent of post-machining.
- As-Sintered Tolerances: Parts used in an “as-sintered” or “as-fired” condition will have wider tolerances, typically in the range of ±1% to ±2% of the dimension, or even larger for complex shapes. This is often sufficient for applications like some kiln furniture or larger hot gas filter elements where extreme precision is not paramount.
- Machined Tolerances: For applications requiring tighter fits, such as SiC ceramic membranes that need precise sealing in modules, or components for semiconductor equipment, diamond grinding is employed. With precision grinding, tolerances can be brought down significantly, often to the range of ±0.01 mm to ±0.05 mm (±10 to 50 μm), or even tighter for specific features on smaller parts.
- Geometric Tolerances: Beyond linear dimensions, tolerances for flatness, parallelism, perpendicularity, and concentricity are also crucial for proper assembly and function. These are typically specified on engineering drawings and achieved through precision machining.
CAS new materials (SicSino) possesses advanced machining capabilities and metrology equipment to ensure that custom silicon carbide components meet the stringent dimensional and geometric tolerances specified by our clients. Our integrated process, from materials to final product, allows for tight control at every stage.
Surface Finish: The surface finish (Ra, average roughness) of a SiC filter can be important for several reasons:
- Sealing Surfaces: Smoother surfaces are generally required for effective sealing with gaskets or O-rings to prevent leaks.
- Fouling Characteristics: In some liquid filtration applications, a smoother surface can be less prone to fouling or easier to clean.
- Flow Dynamics: While less critical for the porous structure itself, the surface finish of non-filtering surfaces or the housing interface can play a role.
Typical surface finishes achievable on SiC:
- As-fired: Can range from a few microns Ra to much rougher, depending on the SiC grade and forming method.
- Ground: Diamond grinding can achieve surface finishes typically in the range of Ra 0.2 μm to Ra 0.8 μm.
- Lapped/Polished: For ultra-smooth surfaces, lapping and polishing can achieve Ra<0.1 μm, though this is more common for non-porous SiC applications like seals or mirrors. For filter components, such high finishes are usually only required on specific sealing faces.
Post-Processing Needs for SiC Filters: Beyond basic shaping and grinding, some SiC filter components may require additional post-processing steps to enhance performance or meet specific application requirements:
- Cleaning: Thorough cleaning to remove any residues from manufacturing or machining is essential, especially for high-purity applications (e.g., pharmaceutical, semiconductor).
- Edge Chamfering/Radiusing: To prevent chipping of the brittle ceramic material and to improve handling safety.
- Pore Modification/Coating (Specialized): In some advanced membrane applications, the surface chemistry of the pores might be modified through thin coatings to alter hydrophilicity/hydrophobicity or to impart catalytic activity. This is a specialized area.
- Joining/Assembly: If the SiC filter element is part of a larger assembly, specialized joining techniques (e.g., ceramic-to-metal brazing, specialized adhesives for lower temperatures) might be needed. However, often the design relies on mechanical clamping or sealing.
- Testing and Characterization: This includes:
- Bubble Point Test: To determine the largest effective pore size and integrity of the filter.
- Permeability/Flux Testing: To verify flow characteristics.
- Porosity Measurement: Using techniques like mercury porosimetry or Archimedes method.
- Dimensional Inspection: Using CMMs, optical comparators, and other metrology tools.
- Non-Destructive Testing (NDT): Such as dye penetrant testing or X-ray inspection for critical components to detect cracks or flaws.
The table below outlines typical tolerances and surface finishes for SiC filter components:
Feature | As-Sintered/Fired | Ground | Lapped/Polished (Sealing Faces) |
---|---|---|---|
Dimensional Tolerance | ±1% to ±2% (or more) | ±0.01 to ±0.1 mm | <±0.01 mm |
Surface Finish (Ra) | 1 μm to >10 μm | 0.2 μm to 0.8 μm | <0.1 μm |
Suitability | Coarse filters, some DPFs | Most precision filters, membranes | Critical sealing areas |
At CAS new materials (SicSino), our commitment to quality extends through every phase of production, including meticulous attention to dimensional accuracy, surface finish requirements, and any necessary post-processing. Our team in Weifang, supported by the rigorous standards of the CAS National Technology Transfer Center, ensures that your custom SiC filters are delivered to your exact specifications, ready for integration and high performance.
Partnering for Success: Selecting Your Custom SiC Filtration Solution Provider
Choosing the right supplier for your custom silicon carbide filtration needs is as critical as selecting the material itself. The complexities of SiC manufacturing, coupled with the demanding nature of filtration applications, necessitate a partner with deep technical expertise, robust quality systems, and a commitment to customer collaboration. For OEMs, technical buyers, and procurement managers in industries like semiconductors, aerospace, and high-temperature furnace operations, the right supplier can be a strategic asset.
When evaluating potential SiC filter manufacturers, consider the following key factors:
- Technical Expertise and Material Knowledge:
- Does the supplier have a profound understanding of different SiC grades (RBSiC, SSiC, RSiC) and their suitability for various filtration environments (e.g., high-temperature filtration, chemical resistant filters)?
- Can they provide expert guidance on material selection based on your specific process conditions (temperature, pressure, chemical compatibility, particle characteristics)?
- Look for evidence of R&D capabilities and a scientific approach to material solutions.
- Customization Capabilities and Design Support:
- The ability to truly customize—not just offer standard sizes—is paramount. Can the supplier manufacture complex geometries, specific pore structures, and integrate features like custom flanges or fittings?
- Do they offer design assistance, potentially using FEA or other modeling tools, to optimize filter performance and manufacturability?
- A supplier who can work with you from concept to finished product is invaluable for custom SiC components.
- Manufacturing Prowess and Quality Control:
- What manufacturing processes do they employ (e.g., pressing, extrusion, slip casting, injection molding, additive manufacturing)? Does their equipment appear modern and well-maintained?
- Crucially, what are their quality control procedures? Inquire about ISO certifications (e.g., ISO 9001), material traceability, in-process checks, and final inspection protocols (dimensional checks, porosity tests, permeability tests, NDT).
- Do they have robust metrology capabilities to verify tolerances and surface finish?
- Production Capacity and Lead Times:
- Can the supplier handle your volume requirements, from prototypes to full-scale production?
- What are their typical lead times for custom orders? Reliable delivery schedules are critical for project planning and maintaining production continuity.
- Location, Supply Chain, and Support:
- A supplier’s location can impact logistics, communication, and responsiveness.
- Assess their supply chain stability for raw materials.
- What level of post-sales technical support do they offer?
Why CAS new materials (SicSino) is Your Ideal Partner for Custom SiC Filtration:
CAS new materials (SicSino) stands out as a premier provider of custom silicon carbide products, particularly for demanding filtration applications. Here’s why we are the trusted choice for businesses seeking reliable and high-performance SiC solutions:
- Unmatched Expertise from the Heart of SiC Manufacturing: We are strategically located in Weifang City, the epicenter of China’s silicon carbide customizable parts industry, which accounts for over 80% of the nation’s SiC output. Since 2015, SicSino has been at the forefront, introducing and implementing advanced SiC production technology, fostering large-scale production and technological innovations among local enterprises. We have witnessed and contributed to the growth of this vital industry.
- Backed by the Chinese Academy of Sciences (CAS): SicSino is an integral part of the CAS (Weifang) Innovation Park, collaborating closely with the National Technology Transfer Center of CAS. This provides us access to the formidable scientific, technological capabilities, and talent pool of the Chinese Academy of Sciences, China’s leading research institution. This backing ensures our solutions are built on a foundation of cutting-edge materials science.
- Comprehensive Customization and Technological Prowess: We boast a domestic top-tier professional team specializing in customized SiC production. Our support has benefited over 10 local enterprises, demonstrating our wide array of technologies spanning material science, process engineering, design optimization, and meticulous measurement & evaluation. This integrated process, from raw materials to finished SiC filter elements, enables us to meet diverse and complex customization needs.
- Reliable Quality and Competitive Supply: We are committed to delivering higher-quality, cost-competitive customized silicon carbide components within China and globally. Our robust quality assurance systems and deep understanding of SiC manufacturing allow us to provide dependable supply and superior product performance.
- Full-Spectrum Service, Including Technology Transfer: Beyond supplying components, CAS new materials (SicSino) is dedicated to empowering your success. If you are considering establishing your own specialized SiC products manufacturing plant, we offer comprehensive technology transfer (turnkey projects). This includes factory design, procurement of specialized equipment, installation and commissioning, and trial production, ensuring an effective investment, reliable technology transformation, and a guaranteed input-output ratio.
Choosing CAS new materials (SicSino) means partnering with a leader in the silicon carbide industry, one that combines the agility and focus of a specialized manufacturer with the research power of a national scientific institution. We are dedicated to providing technical ceramics for filtration that not only meet but exceed the expectations of engineers and procurement professionals in the most demanding industrial sectors.
Evaluation Criterion | What to Look For | How CAS new materials (SicSino) Excels |
---|---|---|
Technical Expertise | Deep knowledge of SiC grades, application suitability, R&D capabilities. | Backed by CAS, extensive experience in SiC production technology, team of specialists. |
Customization | Ability to produce complex shapes, specific porosities, design support. | Core focus on customized production, wide array of technologies (material, process, design), integrated process from materials to products. |
Quality Control | ISO certifications, material traceability, in-process & final inspections, metrology. | Rigorous quality systems, advanced measurement & evaluation technologies, commitment to high-quality components. |
Manufacturing & Supply | Capacity for various volumes, reliable lead times, stable raw material sourcing. | Located in Weifang SiC hub, partnerships with multiple local enterprises, optimized production for cost-competitiveness and reliable supply. |
Support & Partnership | Pre- and post-sales technical support, collaborative approach. | Comprehensive service ecosystem, technology transfer capabilities, dedicated to client success. |
By partnering with CAS new materials (SicSino), you gain access to a wealth of expertise and a commitment to excellence that will elevate your filtration processes.
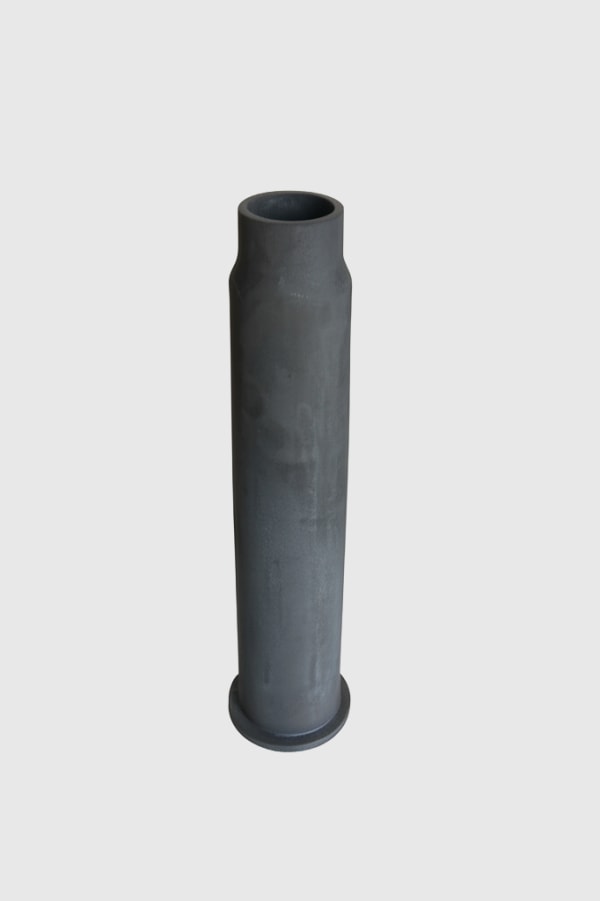
Frequently Asked Questions (FAQ) about Silicon Carbide Filtration
Navigating the specifics of advanced materials like silicon carbide for filtration often brings up questions for engineers, procurement managers, and technical buyers. Here are some common queries with practical, concise answers to help you better understand the capabilities and considerations of custom SiC filters.
1. What makes silicon carbide filters superior to other ceramic filters (e.g., alumina, zirconia) or metallic filters in certain applications?
Silicon carbide (SiC) offers a unique combination of properties that often surpass other materials in harsh environments:
- Thermal Performance: SiC generally has higher thermal conductivity and superior thermal shock resistance compared to alumina or zirconia. This makes it ideal for high-temperature filtration and applications with rapid temperature cycling, like Diesel Particulate Filters (DPFs). Metallic filters have temperature limitations far below SiC.
- Chemical Resistance: While alumina and zirconia offer good chemical resistance, Sintered SiC (SSiC) in particular provides exceptional resistance across a broader pH range and against more aggressive chemicals, especially at elevated temperatures. Metallic filters are prone to corrosion in many chemical environments.
- Hardness and Wear Resistance: SiC is significantly harder than alumina, zirconia, and most metals. This translates to better performance when filtering abrasive slurries or particulate-laden gases, leading to longer filter life.
- Permeability for a Given Strength: SiC can often be manufactured with high porosity (and thus good permeability) while maintaining excellent mechanical strength.
However, the “best” material always depends on the specific application’s combination of temperature, chemical exposure, mechanical stress, and cost considerations. CAS new materials (SicSino) can help analyze your specific needs to recommend the optimal SiC grade or advise if an alternative ceramic might be suitable in less demanding scenarios.
2. How is the porosity and pore size of a custom SiC filter controlled, and what level of precision can be expected?
The porosity and pore size of porous silicon carbide filters are controlled through several methods, depending on the SiC grade and manufacturing technique:
- Particle Size of Raw Materials: Using SiC powders with specific grain sizes and distributions is a primary factor. Finer powders generally lead to finer pores.
- Amount and Type of Pore Formers: Organic or inorganic materials can be mixed with the SiC powder before forming. These materials burn out during sintering, leaving behind pores. The size and amount of these pore formers influence the final pore structure.
- Sintering Parameters: The temperature, time, and atmosphere during the sintering process affect how the SiC grains bond and how porosity develops. For instance, Sintered SiC (SSiC) membranes can achieve very fine, controlled pore sizes (down to sub-micron levels for microfiltration and ultrafiltration) with narrow distributions. Recrystallized SiC (RSiC) typically results in coarser, interconnected porosity.
- Manufacturing Process: Techniques like slip casting, extrusion, and pressing allow for different levels of control over the green body structure, which translates to the final porous structure.
Precision Levels: For SiC ceramic membranes, pore sizes can be controlled with high precision, often specified within a narrow range (e.g., 0.1±0.02 μm). For coarser particulate filters, the specification might be in terms of a D90 or D50 particle removal efficiency. CAS new materials (SicSino) utilizes advanced material processing and characterization techniques to ensure that the porosity and pore size distribution of our custom SiC filter elements meet the specific requirements of your application, offering a high degree of precision tailored to your needs.
3. What are the typical cleaning methods for SiC filters, and how does their reusability compare to other filter types?
SiC filters are known for their excellent cleanability and reusability, which contributes significantly to their cost-effectiveness over the filter’s lifecycle. Common cleaning methods include:
- Backflushing/Backwashing: Reversing the flow direction with clean fluid (liquid or gas) to dislodge accumulated particles. This is very common for SiC ceramic membranes and tubular filters.
- Chemical Cleaning: Due to SiC’s high chemical inertness (especially SSiC), aggressive cleaning agents like strong acids, alkalis, or oxidizers can be used to dissolve or break down stubborn foulants that are not removed by backflushing. This is a major advantage over polymeric membranes which have limited chemical compatibility.
- Thermal Regeneration: Primarily used for SiC Diesel Particulate Filters (DPFs) and some hot gas filters. Trapped soot or combustible particulate matter is burned off at high temperatures, restoring the filter’s permeability. SiC’s excellent thermal stability makes it ideal for this.
- Ultrasonic Cleaning: Can be used in conjunction with chemical cleaning to enhance the removal of particulate and organic foulants.
- Mechanical Cleaning (Carefully): While robust, care should be taken to avoid damaging the ceramic structure.
Reusability Comparison: Compared to many disposable filter cartridges or polymeric membranes that degrade with aggressive chemical cleaning or high temperatures, SiC filters offer significantly longer service life and more regeneration cycles. This robust reusability reduces replacement frequency, waste generation, and overall operational costs, making industrial filtration solutions based on SiC a more sustainable and economical choice for demanding processes. CAS new materials (SicSino) can provide guidance on appropriate cleaning protocols for the specific SiC filters we supply, ensuring you maximize their operational lifespan.
Conclusion: The Enduring Value of Custom Silicon Carbide in Advanced Filtration
In the realm of advanced industrial filtration, where performance under pressure, heat, and chemical attack is non-negotiable, custom silicon carbide stands out as a material of exceptional capability. Its unique blend of thermal resilience, unparalleled chemical inertness, superior mechanical strength, and customizable porosity makes it the go-to solution for engineers and procurement specialists tackling the most demanding separation challenges. From safeguarding delicate semiconductor processes to ensuring clean emissions from power plants, and from purifying aggressive chemicals to refining molten metals, SiC filter elements are pivotal in enhancing efficiency, ensuring product purity, and promoting environmental responsibility.
The ability to tailor SiC components—be it SiC ceramic membranes with precise pore structures, robust Diesel Particulate Filters (DPFs), or intricately shaped porous silicon carbide elements—unlocks a level of performance and longevity that generic solutions simply cannot match. This customization, extending from material grade selection through to intricate design features and exacting tolerances, is where the true value of a knowledgeable and capable supplier becomes evident.
CAS new materials (SicSino), strategically positioned in Weifang City, the heartland of China’s SiC innovation, and fortified by the scientific expertise of the Chinese Academy of Sciences (CAS), embodies this ideal partnership. Our deep-rooted experience in SiC production technology, coupled with a comprehensive suite of customization services and a commitment to quality, ensures that our clients receive higher-quality, cost-competitive customized silicon carbide components. Whether you are an OEM seeking a reliable source for critical filter parts, a technical buyer needing specialized industrial filtration solutions, or an enterprise looking to establish your own SiC manufacturing capabilities through our turnkey technology transfer programs, SicSino is dedicated to your success.
By choosing custom silicon carbide, and by partnering with a leader like CAS new materials (SicSino), industries can confidently address their most critical filtration needs, paving the way for enhanced productivity, reduced operational costs, and a more sustainable future. We invite you to engage with our team of experts to explore how custom SiC filtration can revolutionize your processes.
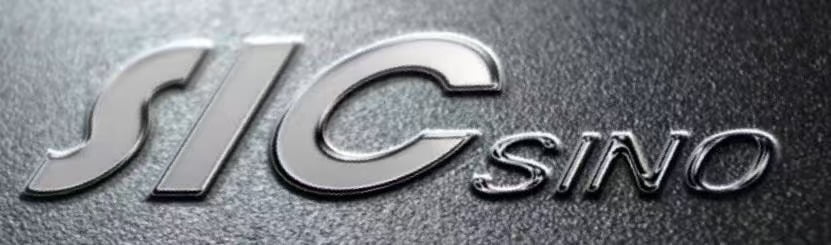
SicSino – CAS new materials
We, CAS new materials(SicSino), have been introducing and implementing silicon carbide production technology since the 2015, assisting the local enterprises in achieving large-scale production and technological advancements in product processes. We have been a witness to the emergence and ongoing development of the local silicon carbide industry.
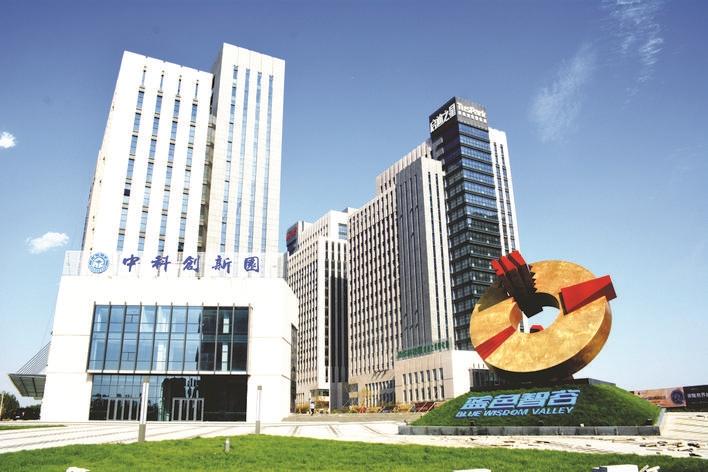