Revolutionizing Road Safety and Performance: The Ascendancy of Silicon Carbide in Braking Systems
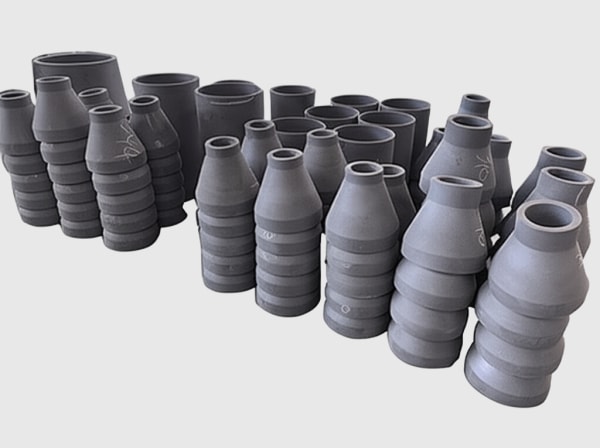
Share
The relentless pursuit of enhanced safety, superior performance, and increased efficiency in automotive and industrial applications has led to a paradigm shift in material science. Traditional braking systems, while functional, often reach their limits under demanding conditions such as high speeds, heavy loads, or repetitive stopping cycles. This is where custom silicon carbide (SiC) products step in, offering a quantum leap in braking technology. Silicon carbide, a formidable technical ceramic, is rapidly becoming the material of choice for high-performance braking systems, promising unparalleled durability, consistent stopping power, and significantly reduced wear. For engineers, procurement managers, and technical buyers in sectors ranging from high-performance automotive and motorsport to heavy-duty transport and industrial machinery, understanding the profound impact of SiC is no longer optional, but essential. These advanced braking systems demand materials that can withstand extreme temperatures, dissipate heat rapidly, and maintain structural integrity under immense mechanical stress – all characteristics inherent to silicon carbide.
The Unyielding Strength: Why Silicon Carbide Excels in Braking Applications
The secret to silicon carbide’s exceptional performance in braking systems lies in its fundamental material properties. Unlike conventional cast iron or even standard ceramic matrix composites, SiC offers a unique combination of characteristics that directly translate to superior braking. Its high thermal conductivity, often exceeding 120W/mK depending on the grade, allows SiC brake discs to dissipate heat far more effectively than traditional materials. This rapid heat dissipation is crucial in preventing brake fade, a dangerous phenomenon where braking efficiency diminishes due to overheating, especially during prolonged or aggressive braking scenarios.
Furthermore, silicon carbide boasts extreme hardness, typically ranking above 9 on the Mohs scale, second only to diamond. This inherent hardness translates into exceptional wear resistance. Silicon carbide brake rotors and pads exhibit significantly longer lifespans and maintain their frictional properties more consistently over time compared to their metallic counterparts. This means fewer replacements, reduced maintenance costs, and more reliable braking performance throughout the vehicle’s or equipment’s operational life.
Another critical advantage is SiC’s relatively low density (around 3.1−3.2g/cm3) compared to iron (around 7.8g/cm3). This results in a substantial reduction in unsprung mass when used for components like brake discs. Lower unsprung mass contributes to improved vehicle handling, responsiveness, and even fuel efficiency. The material’s high strength-to-weight ratio ensures that this weight reduction does not compromise the mechanical integrity required for safe and effective braking. Moreover, SiC maintains its mechanical strength even at elevated temperatures, a critical factor in high-energy braking events where temperatures can soar. Its chemical inertness also means it is highly resistant to corrosion from road salt, moisture, and other environmental factors, further extending its service life and ensuring consistent performance.
For businesses seeking OEM SiC solutions or wholesale silicon carbide brake components, understanding these scientific underpinnings is key to appreciating the value proposition. Companies like CAS new materials (SicSino), located in Weifang City, the hub of China’s silicon carbide customizable parts manufacturing, leverage these intrinsic material advantages to produce cutting-edge braking components. With a deep understanding of SiC material science, fostered through collaboration with the Chinese Academy of Sciences (CAS), SicSino is at the forefront of developing and supplying high-quality, custom SiC solutions for demanding braking applications worldwide.
Tailored Stopping Power: The Advantages of Custom Silicon Carbide Brake Components
The move towards custom silicon carbide brake components is driven by the understanding that a one-size-fits-all approach is insufficient for the diverse and demanding requirements of modern vehicles and industrial machinery. Customization allows for the optimization of brake system performance, longevity, and integration, tailored to the specific operational context. Whether it’s for high-performance sports cars requiring exceptional fade resistance and modulation, heavy-duty trucks needing reliable stopping power under extreme loads, or specialized industrial equipment operating in harsh environments, custom SiC solutions offer tangible benefits.
One of the primary advantages is the ability to engineer the thermal properties of the brake system. By selecting specific SiC grades and designing components like custom SiC brake discs with optimized ventilation patterns, manufacturers can achieve superior heat dissipation, crucial for maintaining consistent friction and preventing thermal deformation. This level of customization is paramount in applications where braking systems are frequently pushed to their thermal limits.
Wear resistance can also be precisely tuned. Different SiC composites and surface treatments can be employed to achieve the desired balance between brake pad and disc life, while ensuring optimal frictional characteristics. For procurement professionals looking for industrial SiC components for braking, this means reduced lifecycle costs due to fewer replacements and less downtime for maintenance.
Moreover, customization extends to the mechanical design. Technical ceramic braking systems utilizing SiC can be designed to exacting dimensional specifications, ensuring perfect fit and compatibility with existing vehicle or machinery architectures. This includes considerations for mounting points, interfacing with calipers, and overall system integration. The lightweight nature of SiC, when strategically exploited through custom design, can contribute significantly to reducing overall system weight, enhancing vehicle dynamics or reducing inertial loads in industrial machinery.
At CAS new materials (SicSino), we understand that customization is key. Situated in Weifang City, which accounts for over 80% of China’s total silicon carbide output, SicSino has been instrumental in advancing SiC production technology since 2015. Our deep expertise, backed by the formidable scientific capabilities of the Chinese Academy of Sciences, allows us to offer unparalleled customization support. We work closely with OEMs, distributors, and technical buyers to develop silicon carbide brake rotors wholesale and bespoke components that meet precise performance, durability, and integration requirements. Our domestic top-tier professional team specializes in the custom production of SiC products, translating unique customer needs into high-performance, reliable braking solutions.
Feature | Traditional Cast Iron Brakes | Standard Ceramic Brakes | Custom Silicon Carbide Brakes (e.g., from SicSino) |
---|---|---|---|
Thermal Conductivity | Moderate | Good | Excellent |
Wear Resistance | Fair | Good | Outstanding |
Weight | Heavy | Lighter than Iron | Significantly Lighter |
Fade Resistance | Prone to fade | Good | Exceptional |
Performance Consistency | Can vary with temperature | Generally good | Highly consistent across wide temperature range |
Lifespan | Shorter | Longer | Longest |
Corrosion Resistance | Poor | Good | Excellent |
Customization Level | Low | Moderate | High (geometry, composition, surface finish) |
Typical Applications | Standard passenger cars | Performance cars | High-performance sports cars, racing, heavy-duty, aerospace, specialized industrial |
This ability to tailor solutions makes custom SiC components a strategic choice for businesses aiming to achieve a competitive edge through superior braking performance and reliability.
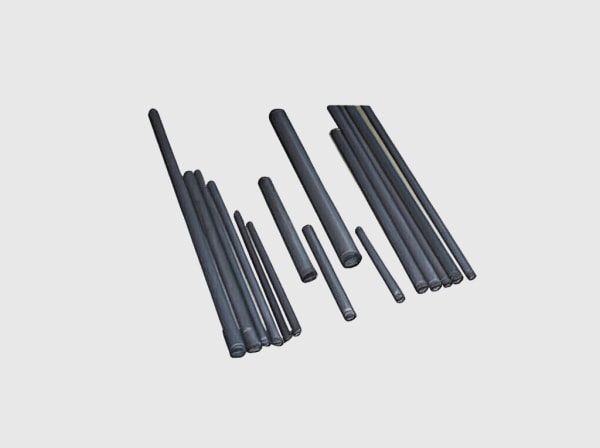
Selecting the Right Material: Key Silicon Carbide Grades for Braking Applications
Not all silicon carbide is created equal, especially when it comes to the demanding environment of braking systems. The choice of SiC grade or composite is critical in determining the final performance characteristics of the brake discs or pads. Different manufacturing processes and additives result in SiC materials with varying properties, making some more suitable for specific braking applications than others. For technical procurement professionals and engineers, understanding these distinctions is vital for specifying the optimal advanced materials for automotive brakes or industrial systems.
One of the most prominent types of SiC used in high-performance braking is Carbon Fiber Reinforced Silicon Carbide (C/SiC or C/C-SiC). These composites combine the extreme hardness and thermal stability of silicon carbide with the toughness and lighter weight of carbon fibers. The carbon fibers act as a reinforcement, improving the fracture toughness of the ceramic matrix and providing a pathway for even more efficient heat dissipation. C/SiC brake discs are renowned for their exceptional resistance to thermal shock, low wear rates at high temperatures, and consistent friction coefficient. They are commonly found in supercars, motorsport applications, and increasingly in luxury performance vehicles.
Reaction-Bonded Silicon Carbide (RBSC or SiSiC – Silicon Infiltrated Silicon Carbide) is another important grade. SiSiC is produced by infiltrating a porous carbon or SiC preform with molten silicon. The silicon reacts with the carbon to form SiC, and any remaining pores are filled with silicon metal. This results in a dense material with excellent thermal conductivity due to the presence of free silicon, high hardness, and good wear resistance. SiSiC brake components can offer a cost-effective solution for applications requiring high thermal performance and durability, though their operating temperature might be limited by the melting point of the residual silicon. CAS new materials (SicSino) possesses extensive expertise in RBSC technology, offering customized SiSiC components tailored for various industrial needs, including potentially specialized braking scenarios.
Sintered Silicon Carbide (S-SiC) is a high-purity form of SiC, produced by sintering SiC powders at very high temperatures, often with the aid of non-oxide sintering additives. S-SiC exhibits superior chemical resistance, high strength at extreme temperatures (up to 1600∘C or higher), and excellent wear and corrosion resistance. While potentially more expensive to manufacture, its purity and performance at the highest temperature ranges make it a candidate for the most extreme braking applications or specific industrial brake designs where chemical exposure is also a concern. SicSino’s technological portfolio, supported by the Chinese Academy of Sciences, includes advanced sintering techniques, enabling the production of high-quality S-SiC components.
The choice between these grades, and potentially other specialized formulations, depends on a thorough analysis of the application’s requirements:
- Maximum Operating Temperature: Will the brakes see extreme, sustained high temperatures?
- Thermal Shock Resistance: How rapid are the temperature changes the brakes will experience?
- Wear Life Expectation: What is the desired service interval for the brake components?
- Frictional Characteristics: Is a specific friction coefficient or stability required?
- Impact Resistance/Toughness: Is the application prone to impacts (e.g., off-road, industrial)?
- Cost Constraints: What is the budget for these high-performance components?
Partnering with a knowledgeable supplier like CAS new materials (SicSino) is crucial. We not only offer a range of SiC materials but also provide the technical expertise to help you select the most appropriate grade and design for your specific braking system needs, ensuring optimal performance and value. Our integrated process, from material selection to finished product, guarantees that you receive components that precisely match your specifications.
Blueprint for Braking Excellence: Design and Manufacturing Considerations for SiC Brake Systems
The transition from traditional brake materials to silicon carbide brake technology involves more than just a material swap; it necessitates a specialized approach to design and manufacturing. The unique properties of SiC, while highly advantageous, also present distinct challenges and opportunities that must be addressed during the engineering phase to ensure optimal performance, reliability, and manufacturability of custom SiC brake discs and related components.
Design Considerations:
- Thermal Management: While SiC has excellent thermal conductivity, the overall design of the brake disc (e.g., ventilation channels, surface area) must be optimized to maximize heat dissipation. Finite Element Analysis (FEA) is often employed to model thermal behavior under various braking conditions and refine the design to prevent localized overheating and ensure stable friction.
- Stress Distribution: Silicon carbide is a strong but brittle material. Designs must carefully manage stress concentrations, avoiding sharp corners or abrupt changes in thickness that could become initiation points for cracks under mechanical or thermal loads. Generous radii and smooth transitions are crucial.
- Interfacing with Other Components: The design must account for the attachment of the SiC brake disc to the wheel hub and its interaction with the brake calipers and pads. Differential thermal expansion between SiC and metallic hub materials needs careful consideration, often requiring specialized mounting systems (e.g., floating bobbins) to prevent induced stress.
- Weight Optimization: While SiC is inherently lighter, design efforts should further optimize the geometry to remove unnecessary material without compromising strength or thermal performance, fully leveraging the weight-saving potential.
- Acoustic Performance (NVH): Brake noise, vibration, and harshness (NVH) are critical aspects of user experience. The design of SiC brake components, including their interaction with pads, can influence NVH characteristics. Specific slot patterns, chamfers, or damping features might be incorporated.
Manufacturing Processes:
The manufacturing of performance ceramic brakes from SiC is a complex, multi-stage process. Common methods include:
- Powder Processing & Shaping: High-purity SiC powder is mixed with binders and formed into a green body using techniques like pressing, slip casting, or injection molding, depending on the complexity and volume of the part.
- Sintering/Reaction Bonding:
- For Sintered SiC (S-SiC), the green body is sintered at extremely high temperatures (often >2000∘C) to densify the material.
- For Reaction-Bonded SiC (RBSC/SiSiC), a porous carbon-SiC preform is infiltrated with molten silicon, which reacts with the carbon to form additional SiC, filling the pores.
- For C/SiC composites, carbon fiber preforms are infiltrated with SiC, often via Chemical Vapor Infiltration (CVI) or liquid silicon infiltration (LSI).
- Machining/Grinding: Due to its extreme hardness, machining SiC after sintering or bonding is challenging and typically requires diamond tooling. Precision grinding is used to achieve the final dimensions, tolerances, and surface finish.
CAS new materials (SicSino), located in the heart of China’s SiC manufacturing region in Weifang City, leverages its extensive technological capabilities, including material, process, design, measurement, and evaluation technologies. This integrated approach allows us to manage the complexities of SiC brake component manufacturing effectively. Our support has benefited over 10 local enterprises, enhancing their production capabilities and technological processes. For OEMs and distributors seeking reliable wholesale silicon carbide brake components or bespoke solutions, SicSino offers a distinct advantage through its deep manufacturing expertise and commitment to quality, ensuring that the design intent is perfectly translated into high-performing, durable products.
Manufacturing Stage | Key Considerations for SiC Brake Components | SicSino’s Expertise & Support |
---|---|---|
Material Selection | Optimal SiC grade (C/SiC, RBSC, S-SiC), purity, particle size | Guidance on material choice based on application, access to diverse high-quality SiC powders and formulations. |
Component Design | Thermal management, stress analysis, NVH, mounting interfaces | Collaborative design, FEA support, DFM (Design for Manufacturability) expertise for custom SiC brake discs. |
Forming/Shaping | Uniform density, complex geometries, minimizing green machining | Advanced forming techniques suited for intricate brake disc designs and consistent quality. |
Sintering/Bonding | Precise temperature control, atmosphere, achieving full density | State-of-the-art furnaces and process control for optimal material properties. Expertise in RBSC, S-SiC, and composites. |
Precision Machining | Diamond grinding, achieving tight tolerances and surface finish | Advanced CNC grinding capabilities, expertise in machining hard ceramics to exacting specifications. |
Quality Control | Dimensional accuracy, material integrity, defect detection | Comprehensive NDT (Non-Destructive Testing), metrology, and material characterization. |
Supply Chain Management | Raw material sourcing, production scheduling, consistent supply | Robust supply chain within the Weifang SiC hub, ensuring reliable delivery for OEM SiC solutions. |
This meticulous approach to design and manufacturing is fundamental to unlocking the full potential of silicon carbide in advanced braking systems.
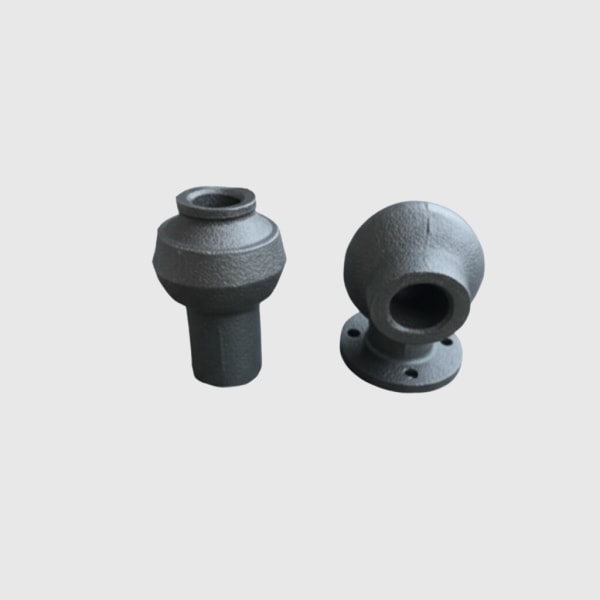
Perfecting the Contact: Surface Finish, Tolerances, and Post-Processing for SiC Brakes
The performance and longevity of silicon carbide braking systems are not solely determined by the bulk material properties and overall design; the precision of the manufacturing process, particularly concerning surface finish, dimensional tolerances, and any necessary post-processing, plays an equally critical role. These factors directly influence the friction characteristics, wear rate, noise generation, and overall effectiveness of SiC brake discs and pads. For engineers and procurement managers aiming for the highest echelons of braking performance, meticulous attention to these details is paramount.
Dimensional Accuracy and Tolerances: Achieving tight dimensional tolerances is crucial for the proper fit and function of SiC brake components within the larger braking assembly. This includes the overall diameter and thickness of the disc, the flatness of the braking surfaces, the parallelism between these surfaces, and the precise location and dimensions of mounting holes or features. Deviations can lead to issues like uneven pad wear, brake judder, improper heat distribution, and difficulties in assembly. Given SiC’s hardness, achieving these tolerances requires specialized diamond grinding equipment and precise process control. Typical tolerances for critical dimensions in high-performance SiC brake discs can be in the range of tens of microns.
Surface Finish: The surface finish of the SiC brake disc is a key determinant of the friction coefficient and the “bedding-in” process with the brake pads. A surface that is too smooth might lead to a lower initial friction, while a surface that is too rough can cause accelerated pad wear. An optimized surface texture, often achieved through controlled grinding and lapping processes, promotes an even transfer layer formation from the pad to the disc, which is essential for stable and predictable friction. The required surface roughness (e.g., Ra value) is typically specified based on the type of brake pad material being used and the desired braking characteristics.
Post-Processing Needs: Depending on the specific SiC grade and application, additional post-processing steps might be employed to further enhance performance or durability:
- Edge Treatment: Chamfering or radiusing sharp edges can help prevent chipping during handling, installation, or operation, given SiC’s brittle nature.
- Sealing: For certain grades of SiC, particularly those with some residual porosity like some RBSC types (though high-density RBSC aims to minimize this), sealing the surface can improve resistance to fluid penetration and corrosion, and can sometimes enhance wear properties. However, for brake applications, porosity is sometimes intentionally designed for outgassing or specific friction behavior.
- Coatings (Less Common for Discs, More for Other Components): While the SiC disc itself is highly wear-resistant, specialized coatings might be considered for other interacting components or for specific environmental protection in extreme cases, though this is not standard for the primary friction surface of SiC brake discs. The focus is usually on the inherent properties of the SiC itself.
- Balancing: Just like conventional brake discs, high-speed SiC brake discs may require dynamic balancing to eliminate vibration and ensure smooth operation, particularly in high-performance automotive applications.
At CAS new materials (SicSino), our commitment to quality extends to these critical finishing and post-processing stages. Leveraging our advanced measurement and evaluation technologies, we ensure that every custom SiC brake component meets the stringent dimensional and surface finish specifications demanded by our clients. Our integrated process, from raw material to the final polished product, allows for meticulous control at every step. This precision is what enables CAS new materials (SicSino) to deliver industrial SiC components and performance ceramic brakes that provide consistent, reliable, and superior braking performance. Our expertise in the customized production of silicon carbide products means we can accommodate highly specific requirements for tolerances and surface characteristics, crucial for OEMs and high-tier suppliers.
Understanding and specifying these finishing details are crucial for maximizing the benefits of advanced materials for automotive brakes and industrial systems, ensuring that the theoretical advantages of silicon carbide translate into tangible real-world performance gains.
Navigating the Roadblocks: Common Challenges and Solutions in SiC Brake System Implementation
While the advantages of silicon carbide for braking systems are compelling, its adoption and implementation are not without challenges. Engineers, manufacturers, and procurement teams must be aware of these potential hurdles to effectively integrate SiC brake technology and realize its full potential. Fortunately, ongoing advancements in material science, manufacturing processes, and design methodologies, often spearheaded by specialized firms like CAS new materials (SicSino), offer effective solutions.
Common Challenges:
- Brittleness and Fracture Toughness: Silicon carbide is a ceramic and, like many ceramics, exhibits lower fracture toughness compared to metals. This means it can be more susceptible to catastrophic failure from impact damage (e.g., from road debris) or if subjected to excessive stress concentrations.
- Solutions:
- Material Engineering: Development of SiC composites, such as Carbon Fiber Reinforced Silicon Carbide (C/SiC), significantly improves toughness and resistance to crack propagation.
- Design Optimization: Careful design to minimize stress risers, incorporate compliant mounting systems, and protect vulnerable areas. Finite Element Analysis (FEA) is crucial for identifying and mitigating high-stress zones.
- Quality Control: Rigorous non-destructive testing (NDT) like X-ray or ultrasonic inspection to detect internal flaws that could lead to failure.
- Solutions:
- Manufacturing Complexity and Cost: The extreme hardness of SiC makes it difficult and costly to machine. The high temperatures and specialized equipment required for sintering or infiltration processes also contribute to higher manufacturing costs compared to traditional metallic brakes.
- Solutions:
- Near-Net-Shape Manufacturing: Advanced forming techniques (e.g., injection molding, precision pressing) to produce components closer to their final shape, minimizing the need for extensive and expensive machining.
- Process Optimization: Continuous improvement in sintering and infiltration technologies to reduce cycle times and energy consumption.
- Economies of Scale: As adoption increases, economies of scale in raw material production and component manufacturing can help drive down costs. CAS new materials (SicSino), located in Weifang City, the heart of China’s SiC industry, benefits from and contributes to this ecosystem, aiming to provide more cost-competitive customized silicon carbide components.
- Specialized Expertise: Partnering with experienced SiC manufacturers like SicSino, who possess the specialized equipment and process knowledge, can lead to more efficient and cost-effective production.
- Solutions:
- Thermal Shock Sensitivity (in some grades): While generally excellent, some SiC grades, if not properly selected or designed for the application, can be susceptible to thermal shock if subjected to extremely rapid and severe temperature gradients.
- Solutions:
- Material Selection: Choosing grades like C/SiC with inherently superior thermal shock resistance.
- Design for Thermal Management: Ensuring efficient and uniform heat dissipation to prevent extreme temperature differentials across the component.
- Solutions:
- System Integration: Integrating SiC brake discs with existing caliper and hydraulic systems requires careful consideration of factors like thermal expansion differences between the SiC disc and metallic hub/caliper components, and ensuring compatibility with brake pad materials.
- Solutions:
- Specialized Mounting Systems: Utilizing floating bobbins or other compliant mounting hardware to accommodate differential thermal expansion.
- Pad Material Compatibility: Selecting or developing brake pad materials that are optimized to work with SiC discs to achieve desired friction, wear, and NVH (Noise, Vibration, Harshness) characteristics.
- Collaborative Engineering: Close collaboration between the SiC component supplier and the vehicle/equipment manufacturer is essential. SicSino prides itself on its ability to work with clients on integrated solutions.
- Solutions:
- Noise, Vibration, and Harshness (NVH): Ceramic brakes, including SiC, can sometimes exhibit different NVH characteristics compared to traditional brakes, which may require specific design features or tuning.
- Solutions:
- Optimized Disc/Pad Interface: Careful design of disc surface features (slots, holes) and pad chamfers.
- Damping Technologies: Incorporation of damping shims or other NVH countermeasures.
- Material Pairing: Extensive testing to find the optimal SiC disc and pad material pairing.
- Solutions:
Overcoming these challenges is a continuous process. CAS new materials (SicSino), with its strong foundation in the scientific and technological capabilities of the Chinese Academy of Sciences and its practical experience within Weifang’s SiC industrial cluster, is dedicated to advancing SiC brake technology. We offer not just components, but also the expertise to help clients navigate these complexities, ensuring successful implementation of high-performance ceramic brakes. Our commitment to quality and customized solutions makes us a reliable partner in harnessing the power of silicon carbide.
Challenge Area | Common Issue with SiC Brakes | Mitigation Strategies & Solutions Provided by SicSino |
---|---|---|
Brittleness/Fracture Toughness | Susceptibility to impact damage or stress concentration. | Material selection (e.g., C/SiC composites), robust design engineering (FEA), stringent NDT quality control. SicSino offers various SiC grades and design support. |
Manufacturing Cost & Complexity | Difficult machining, high-temperature processing. | Near-net-shape forming, process optimization, leveraging Weifang’s SiC hub economies. SicSino provides cost-competitive solutions through advanced manufacturing and integrated processes. |
Thermal Shock Sensitivity | Potential cracking under extreme thermal gradients. | Selection of high thermal shock resistant grades (e.g., C/SiC), design for uniform heat dissipation. SicSino guides material selection based on application demands. |
System Integration | Differential thermal expansion, pad compatibility. | Design of appropriate mounting systems (e.g., floating designs), collaboration on brake pad material selection. SicSino offers collaborative engineering for seamless integration of OEM SiC solutions. |
NVH (Noise, Vibration, Harshness) | Potentially different acoustic profile than metallic brakes. | Optimized disc surface features (slots, chamfers), guidance on pad pairing, collaborative NVH troubleshooting. SicSino aids in developing solutions for quiet and smooth technical ceramic braking systems. |
Supplier Reliability & Expertise | Ensuring consistent quality and technical support. | SicSino, backed by CAS, offers a domestic top-tier professional team, proven technology transfer, and a comprehensive service ecosystem, ensuring reliable quality and supply for wholesale silicon carbide brake components. |
By proactively addressing these challenges, the path to wider adoption of silicon carbide in braking systems becomes clearer, paving the way for safer, more efficient, and higher-performing vehicles and machinery.
Partnering for Peak Performance: Choosing the Right Silicon Carbide Supplier for Braking Systems
The successful integration and optimal performance of silicon carbide in braking systems heavily depend on the capabilities, reliability, and expertise of the SiC component supplier. Selecting the right partner is as crucial as choosing the right material grade. For technical buyers, procurement managers, and engineers, evaluating potential suppliers requires a comprehensive assessment of their technical prowess, material offerings, quality assurance processes, customization capabilities, and long-term support.
Key Criteria for Evaluating a SiC Supplier:
- Technical Expertise and R&D Capabilities:
- Does the supplier possess a deep understanding of silicon carbide material science, including different grades (RBSC, S-SiC, C/SiC composites) and their specific properties relevant to braking applications (thermal conductivity, wear resistance, fracture toughness)?
- Do they have in-house R&D capabilities or strong affiliations with research institutions to stay at the forefront of SiC brake technology?
- Can they provide expert consultation on material selection and component design for your specific application?
- Manufacturing Capabilities and Process Control:
- What manufacturing processes do they employ (e.g., pressing, sintering, infiltration, precision grinding)? Are these processes state-of-the-art and well-controlled?
- What is their capacity for producing custom SiC brake discs and other components to the required scale and complexity?
- How do they ensure consistency and repeatability in their manufacturing operations?
- Quality Assurance and Certifications:
- What quality management systems are in place (e.g., ISO 9001)?
- What are their procedures for raw material inspection, in-process quality checks, and final product testing (including dimensional accuracy, material integrity, NDT)?
- Can they provide material certifications and detailed quality documentation for industrial SiC components?
- Customization and Design Support:
- How flexible are they in accommodating custom designs and specifications?
- Do they offer design for manufacturability (DFM) support to optimize your component designs for SiC production?
- Can they assist with prototyping and iterative development for performance ceramic brakes?
- Supply Chain Management and Reliability:
- What is their track record for on-time delivery?
- How do they manage their raw material sourcing and supply chain to ensure continuity?
- What is their capacity to scale production if your demand for wholesale silicon carbide brake components increases?
- Cost-Effectiveness and Lead Times:
- While SiC is a premium material, does the supplier offer competitive pricing without compromising on quality? This involves assessing the total cost of ownership, including component life and performance.
- What are their typical lead times for prototyping and mass production?
Why CAS new materials (SicSino) Stands Out:
CAS new materials (SicSino) embodies many of these critical attributes, making us an ideal partner for your silicon carbide braking system needs.
- Unmatched Expertise: As part of the CAS (Weifang) Innovation Park and collaborating closely with the National Technology Transfer Center of the Chinese Academy of Sciences (CAS), we capitalize on robust scientific, technological capabilities, and a rich talent pool. Our domestic top-tier professional team specializes in the customized production of SiC products.
- Strategic Location: Situated in Weifang City, the hub of China’s silicon carbide customizable parts manufacturing (over 80% of national output), we have been instrumental in local technological advancements since 2015. This ecosystem provides access to a mature supply chain and skilled labor.
- Comprehensive Technological Portfolio: We possess a wide array of technologies, encompassing material science, process engineering, design optimization, and advanced measurement & evaluation techniques. This integrated approach, from materials to finished products, enables us to meet diverse customization needs for OEM SiC solutions.
- Commitment to Quality and Reliability: Our support has benefited over 10 local enterprises, a testament to our reliable technology and quality assurance. We aim to deliver higher-quality, cost-competitive customized silicon carbide components.
- Full-Spectrum Support: Beyond component supply, CAS new materials (SicSino) is committed to fostering the SiC industry. If you need to build a professional silicon carbide products manufacturing plant in your country, we can provide technology transfer for professional SiC production, along with a full range of turnkey project services, including factory design, procurement of specialized equipment, installation, commissioning, and trial production. This unique offering ensures an effective investment, reliable technology transformation, and a guaranteed input-output ratio.
Choosing a supplier like CAS new materials (SicSino) means more than just procuring components; it means engaging a knowledgeable partner dedicated to your success in leveraging the transformative potential of silicon carbide in braking systems.

Frequently Asked Questions (FAQ) about Silicon Carbide Braking Systems
As interest in silicon carbide for braking systems grows, so do the questions from engineers, procurement specialists, and end-users. Here are some common queries with concise, practical answers:
1. Are silicon carbide brakes significantly more expensive than traditional brakes, and are they worth the cost?
Yes, SiC brake discs and components are generally more expensive upfront compared to traditional cast iron brakes. This is due to the more complex and energy-intensive manufacturing processes involved, including high-temperature sintering or infiltration and the difficult machining of the extremely hard SiC material.
However, the “worth” is determined by the application and the total cost of ownership (TCO). For high-performance vehicles (sports cars, racing), heavy-duty applications, or industrial machinery with demanding braking cycles, the benefits often outweigh the initial cost. These benefits include:
- Significantly longer lifespan: Silicon carbide brake rotors can last several times longer than conventional rotors, reducing replacement frequency and associated labor costs.
- Consistent performance: Minimal brake fade even under extreme conditions, leading to enhanced safety and predictability.
- Weight reduction: Lower unsprung mass improves vehicle handling, acceleration, and potentially fuel efficiency.
- Reduced brake dust: Many SiC brake formulations produce less unsightly and corrosive brake dust.
- Corrosion resistance: SiC is highly resistant to corrosion from road salt and moisture.
For standard passenger cars used for daily commuting, the cost-benefit analysis might still favor traditional brakes. However, for applications where braking performance, durability, and safety are paramount, performance ceramic brakes made from SiC provide exceptional value. CAS new materials (SicSino) strives to provide cost-competitive customized silicon carbide components by leveraging its expertise and strategic location within China’s SiC manufacturing hub.
2. How does the maintenance of SiC brakes compare to conventional braking systems?
Maintenance for SiC braking systems is generally reduced due to the exceptional wear resistance of the SiC brake discs.
- Disc Replacement: SiC discs last much longer, so replacements are far less frequent. Some SiC discs are designed to last the lifetime of certain components or even the vehicle in specific use cases, though this varies greatly.
- Pad Replacement: While the SiC disc is very durable, the brake pads (which may or may not be SiC-based, often specialized organic or semi-metallic compounds designed for SiC discs) will still wear and require replacement. However, pad wear can also be more consistent when paired with SiC discs.
- Fluid Changes: Brake fluid changes will follow the vehicle manufacturer’s recommended schedule, irrespective of the disc material.
- Inspection: Regular visual inspection for any signs of unusual wear, damage (though rare for discs), or issues with mounting hardware is still necessary, similar to conventional systems.
One consideration is that if an SiC disc is damaged (e.g., by a severe impact causing a crack), it typically requires replacement rather than resurfacing, which might be an option for some metallic discs. However, the likelihood of such damage is low in typical operating conditions due to the material’s hardness and robust design.
3. Can silicon carbide brakes be retrofitted onto any vehicle or machine?
Retrofitting SiC brake technology is technically possible for many vehicles and machines, but it’s not always a simple drop-in replacement. Several factors need consideration:
- Component Matching: The SiC discs must be dimensionally compatible with the existing wheel hubs and calipers. Often, a retrofit involves a kit that may include new, larger calipers designed to accommodate the SiC discs and optimize performance.
- Brake Bias: Changing brake components can alter the front-to-rear brake bias, which might require adjustments to the braking system or ECU (Electronic Control Unit) programming in modern vehicles to maintain safe handling.
- Master Cylinder and Hydraulic System: The existing master cylinder and hydraulic system must be capable of providing the appropriate pressure and fluid displacement for the new SiC brake setup, especially if larger calipers are used.
- ABS and Stability Control Compatibility: Modern vehicles have sophisticated Anti-lock Braking Systems (ABS) and Electronic Stability Control (ESC) systems. Any significant change in braking characteristics must be compatible with these systems.
- Cost: Retrofit kits for technical ceramic braking systems can be quite expensive.
It is generally recommended that such retrofits are performed using kits specifically designed for the vehicle/machine model by reputable manufacturers or specialists. For OEM SiC solutions or new designs, CAS new materials (SicSino) works closely with clients to ensure that the custom SiC brake components are perfectly integrated into the overall system design from the outset, ensuring optimal performance and safety. Our expertise in design and measurement & evaluation technologies is crucial for such integrations.
Conclusion: The Unstoppable Momentum of Silicon Carbide in Advanced Braking
The journey through the landscape of silicon carbide for braking systems reveals a material poised to redefine standards in safety, performance, and durability across a multitude of industries. From the blistering speeds of motorsport to the relentless demands of heavy-duty transport and the precision requirements of industrial manufacturing, custom SiC brake components offer a compelling suite of advantages: superior thermal management, exceptional wear resistance, significant weight savings, and unwavering performance consistency.
While challenges related to cost and manufacturing complexity exist, the continuous innovation driven by specialized companies like CAS new materials (SicSino) is steadily making this advanced technology more accessible and adaptable. Our strategic position in Weifang City, the epicenter of China’s silicon carbide production, coupled with our deep-rooted collaboration with the Chinese Academy of Sciences, empowers us to deliver not just high-quality silicon carbide brake rotors wholesale and custom parts, but also comprehensive technical support and even turnkey solutions for establishing SiC manufacturing capabilities.
For engineers striving for the next leap in braking efficiency, for procurement managers seeking long-term value and reliability through industrial SiC components, and for OEMs aiming to equip their products with cutting-edge performance ceramic brakes, silicon carbide presents an undeniable value proposition. The path forward involves a collaborative approach, partnering with knowledgeable suppliers who can navigate the intricacies of material science, design engineering, and precision manufacturing. CAS new materials (SicSino) is committed to being that partner, helping you harness the full potential of silicon carbide to create braking systems that are not just effective, but truly exceptional. The era of advanced ceramic braking is here, and silicon carbide is undeniably leading the charge.
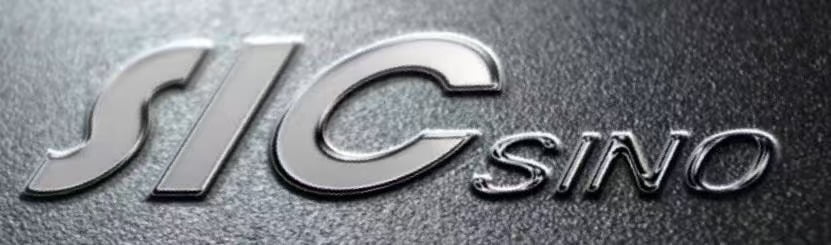
SicSino – CAS new materials
We, CAS new materials(SicSino), have been introducing and implementing silicon carbide production technology since the 2015, assisting the local enterprises in achieving large-scale production and technological advancements in product processes. We have been a witness to the emergence and ongoing development of the local silicon carbide industry.
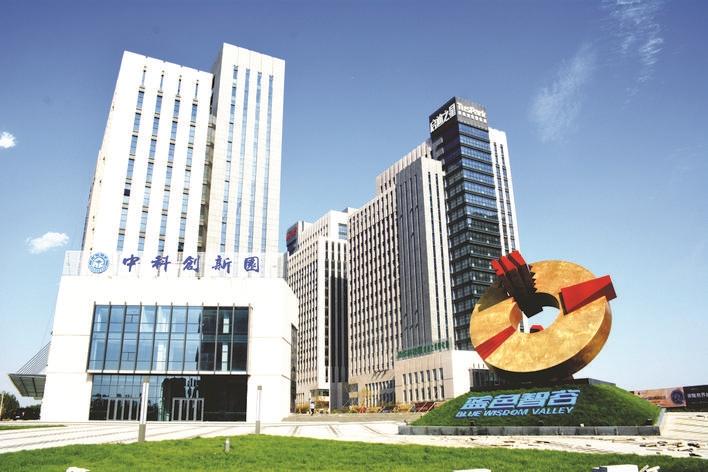