Silicon Carbide for Wear Parts: The Ultimate Solution for Extreme Industrial Environments
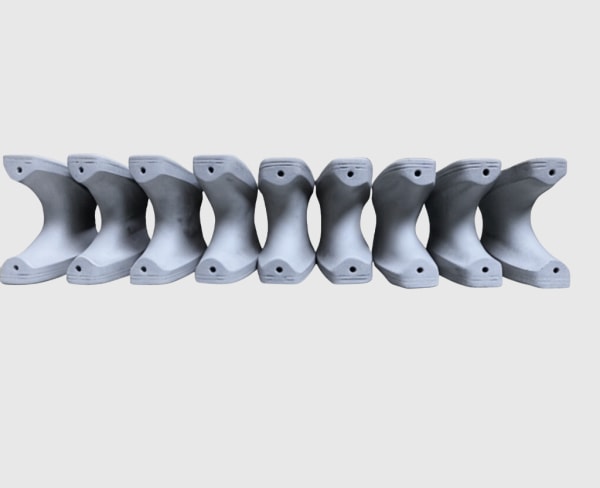
Share
In the relentless pursuit of operational efficiency and longevity, industries worldwide are increasingly turning to advanced materials that can withstand extreme conditions. Among these, custom silicon carbide (SiC) wear parts have emerged as a cornerstone for applications where abrasion, erosion, corrosion, and high temperatures conspire to shorten component life and inflate maintenance costs. For engineers, procurement managers, and technical buyers in sectors ranging from mining and material processing to energy and chemical production, understanding the profound benefits of SiC is no longer optional—it’s essential for maintaining a competitive edge. This blog post delves into the world of silicon carbide wear parts, exploring their applications, advantages, and the critical factors to consider when sourcing these high-performance technical ceramics.
Introduction: The Unyielding Strength of Custom Silicon Carbide Wear Parts in Demanding Industries
Wear is an omnipresent challenge in industrial operations, leading to equipment downtime, reduced efficiency, and significant replacement expenses. Traditional materials like hardened steels, alloys, or even some conventional ceramics often fall short when faced with aggressive media, high velocities, or extreme thermal cycling. This is where custom silicon carbide wear parts shine. Silicon carbide, a synthetic crystalline compound of silicon and carbon (SiC), is renowned for its exceptional hardness, second only to diamond, coupled with remarkable thermal stability, superior corrosion resistance, and high strength-to-weight ratio.
Custom SiC wear components are engineered to precise specifications, tailored to combat specific wear mechanisms encountered in unique industrial environments. These are not off-the-shelf solutions; they are meticulously designed and manufactured parts, such as SiC wear liners, industrial SiC nozzles, SiC mechanical seals, SiC pump components, and SiC cyclone liners, that deliver unparalleled performance where others fail. The ability to customize the shape, size, and even the grade of SiC allows for optimized solutions that integrate seamlessly into existing equipment, dramatically extending service life and improving overall process reliability. For businesses seeking durable ceramic components and long-lasting wear solutions, silicon carbide represents a significant technological advancement and a sound economic investment.
Key Industries Benefiting from Silicon Carbide Wear Components
The exceptional properties of silicon carbide make it an indispensable material for wear parts across a multitude of demanding industries. Its ability to resist various forms of wear – abrasion, erosion, and chemical attack – even at elevated temperatures, makes it a preferred choice for high-performance ceramic wear parts.
Here’s a look at some key sectors and their reliance on SiC wear components:
- Mining and Mineral Processing: This industry is notorious for severe abrasive wear. SiC slurry pump parts, hydrocyclone apexes and spigots, pipe liners, and chute liners made from silicon carbide significantly outlast conventional materials when handling abrasive ores, sand, and gravel. This translates to reduced downtime for mining wear parts and lower operational costs.
- Power Generation: In coal-fired power plants, SiC burner nozzles, pulverized fuel pipe bends, and ash handling system components offer extended life due to their resistance to erosion from high-velocity particulate matter and high temperatures.
- Chemical Processing: The chemical inertness of SiC makes it ideal for manufacturing SiC mechanical seals, pump shafts and sleeves, valve components, and chemical reactor linings that handle corrosive acids, alkalis, and solvents, even under pressure and at high temperatures. Corrosion-resistant SiC parts are critical in these environments.
- Pulp and Paper: Equipment in pulp and paper mills, such as cleaner cones, decanter centrifuge tiles, and nozzles, benefit from SiC’s resistance to both abrasive wood fibers and corrosive bleaching chemicals.
- Oil and Gas: Downhole tools, flow control chokes, valve seats, and pump components in the oil and gas sector utilize SiC for its ability to withstand abrasive slurries, high pressures, and corrosive environments. Durable SiC components for oil and gas are in high demand.
- Cement Manufacturing: The abrasive nature of clinker and cement dust requires highly wear-resistant materials. SiC classifier cones, preheater components, and kiln furniture offer superior performance.
- Steel and Metallurgy: Components like thermocouple protection tubes, furnace rollers, and material handling parts benefit from SiC’s high-temperature strength and wear resistance.
The versatility of custom SiC solutions allows for tailored designs that meet the specific challenges of each application within these industries, ensuring optimal performance and longevity.
Industry Sector | Common SiC Wear Part Applications | Key Benefits Provided by SiC |
---|---|---|
Mining & Mineral Processing | Slurry pump liners, hydrocyclone components, pipe liners, chute liners | Extreme abrasion resistance, extended part life |
Power Generation | Burner nozzles, ash handling components, PF pipe bends | High-temperature erosion resistance, durability |
Chemical Processing | Mechanical seals, pump components, valve trims, reactor linings | Superior corrosion resistance, chemical inertness |
Pulp and Paper | Cleaner cones, nozzles, centrifuge tiles | Abrasion and chemical attack resistance |
Oil and Gas | Downhole tools, chokes, valve seats, pump components | Resistance to abrasive slurries and high pressures |
Cement Manufacturing | Classifier cones, preheater components, kiln parts | High abrasion and high-temperature resistance |
Steel and Metallurgy | Thermocouple tubes, furnace rollers, guides | High-temperature strength, wear resistance |
The Unbeatable Advantages of Custom SiC for Superior Wear Resistance
When evaluating materials for applications prone to severe wear, custom silicon carbide components offer a compelling suite of advantages that translate directly into improved operational efficiency, reduced downtime, and lower lifecycle costs. These benefits stem from the inherent material properties of SiC, which can be further enhanced through careful grade selection and custom design.
Key advantages include:
- Exceptional Hardness and Abrasion Resistance: Silicon carbide is one of the hardest commercially available materials, with a Mohs hardness typically ranging from 9 to 9.5 (diamond is 10). This extreme hardness provides outstanding resistance to abrasive wear caused by hard particles in slurries, powders, or high-velocity gas streams. SiC wear plates and abrasion-resistant SiC liners can outperform hardened metals and other ceramics by orders of magnitude.
- Superior Corrosion Resistance: SiC exhibits excellent resistance to a wide range of corrosive media, including strong acids, alkalis, and oxidizing agents, even at elevated temperatures. This makes it an ideal choice for chemical-resistant ceramic parts in aggressive chemical processing environments where metallic components would quickly degrade.
- High-Temperature Stability and Strength: Unlike many metals that soften or oxidize at high temperatures, silicon carbide retains its mechanical strength and wear resistance up to very high temperatures (typically 1400°C to 1650°C or higher, depending on the grade). This makes high-temperature SiC components suitable for applications like furnace parts, burner nozzles, and exhaust systems.
- Excellent Thermal Shock Resistance: Certain grades of silicon carbide, particularly Reaction-Bonded Silicon Carbide (RBSiC or SiSiC), offer good thermal shock resistance, allowing them to withstand rapid temperature changes without cracking or spalling. This is crucial for components that experience fluctuating thermal loads.
- Low Coefficient of Friction: Polished SiC surfaces can achieve a very low coefficient of friction, especially when paired with another SiC surface or other compatible materials. This is highly beneficial for applications like SiC bearings, mechanical seals, and dynamic seal faces, as it reduces frictional losses, heat generation, and wear.
- High Stiffness (Young’s Modulus): Silicon carbide’s high modulus of elasticity means it deforms very little under load, maintaining dimensional stability and precision in demanding applications. This is important for components requiring tight tolerances and consistent performance.
- Lightweight: Compared to many metals like steel or tungsten carbide, silicon carbide has a lower density. This can be advantageous in applications where weight reduction is desirable, such as in rotating or moving parts, without sacrificing wear resistance.
- Customization Potential: The ability to produce custom-engineered SiC parts allows designers to optimize geometry, integrate features, and select the most appropriate SiC grade for the specific wear mechanism and operating conditions. This ensures that the component delivers maximum performance and service life.
By leveraging these advantages, industries can significantly enhance the reliability and efficiency of their equipment, making advanced ceramic wear solutions a smart investment for tackling the toughest wear challenges.
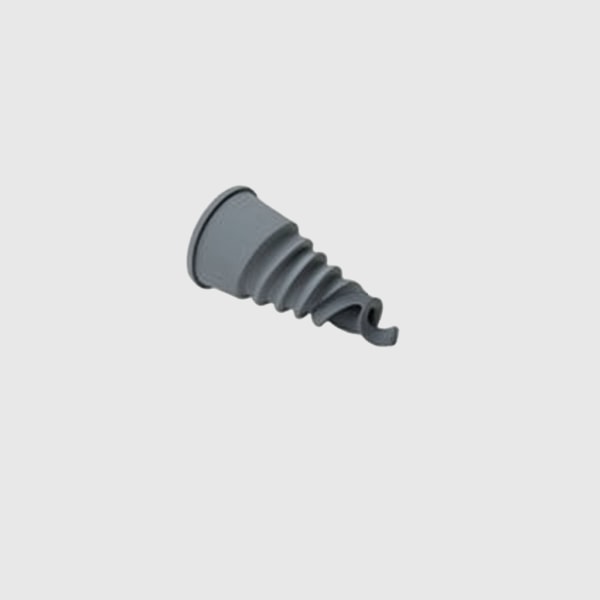
Selecting the Optimal Silicon Carbide Grade for Your Wear Application
Not all silicon carbide is created equal. Different manufacturing processes result in various SiC grades with distinct microstructures and property profiles. Choosing the right grade is paramount for optimizing the performance and lifespan of SiC wear parts. The selection process involves understanding the specific wear mechanisms (e.g., abrasion, erosion, corrosion, impact), operating temperatures, chemical environment, and mechanical stresses the component will face.
Here are some of the most common SiC grades used for wear applications and their characteristics:
- Reaction-Bonded Silicon Carbide (RBSiC or SiSiC):
- Manufacturing: Produced by infiltrating a porous preform, typically made of SiC grains and carbon, with molten silicon. The silicon reacts with the carbon to form new SiC, which bonds the original SiC grains. The resulting material usually contains some free silicon (typically 8-15%).
- Properties: Offers excellent wear and corrosion resistance, good thermal shock resistance, high thermal conductivity, and high strength. The presence of free silicon can limit its use in extremely high temperatures (>1350°C) or in contact with certain aggressive chemicals that attack silicon.
- Common Wear Applications: Ideal for RBSiC pump components, SiSiC wear liners, nozzles, mechanical seal faces, and kiln furniture. It is often a cost-effective choice for many abrasion and corrosion-resistant applications.
- Keywords for Procurement: Reaction bonded silicon carbide wear parts, SiSiC industrial components.
- Sintered Silicon Carbide (SSiC):
- Manufacturing: Produced by sintering fine SiC powder at very high temperatures (typically 2000°C to 2200°C), often with non-oxide sintering aids (like boron and carbon). This process results in a dense, single-phase SiC material with no free silicon.
- Properties: SSiC exhibits the highest hardness, strength, wear resistance, and corrosion resistance among common SiC grades. It also maintains its strength at very high temperatures (up to 1650°C or higher). It is generally more expensive than RBSiC.
- Common Wear Applications: Preferred for the most demanding wear and corrosion environments, such as SSiC bearings, high-performance mechanical seals, valve components for corrosive fluids, semiconductor processing equipment parts, and applications requiring extreme abrasion resistance.
- Keywords for Procurement: Sintered silicon carbide wear resistance, High-purity SiC components.
- Nitride-Bonded Silicon Carbide (NBSC):
- Manufacturing: SiC grains are bonded by a silicon nitride (Si3N4) phase.
- Properties: Offers good wear resistance, excellent thermal shock resistance, and good resistance to molten non-ferrous metals. It is generally not as hard or strong as RBSiC or SSiC.
- Common Wear Applications: Used in applications like kiln furniture for ceramic firing, parts for handling molten aluminum, and some types of liners and nozzles where extreme thermal cycling is a primary concern.
- Other Specialized Grades:
- Graphite-Loaded SiC: Incorporates graphite to improve tribological properties (self-lubrication) for dry running seals or bearings.
- Chemically Vapor Deposited (CVD) SiC: Produces ultra-high purity SiC coatings or bulk components with exceptional surface finish and properties, often used in semiconductor and optical applications, but can also be used for specialized wear surfaces.
The selection process should involve a thorough analysis of the application requirements and consultation with experienced SiC suppliers. CAS new materials (SicSino), with its deep expertise in SiC materials science and access to a wide array of production technologies through its association with the Chinese Academy of Sciences (CAS), can assist clients in selecting or even developing the optimal SiC grade for their specific wear challenges, ensuring a balance of performance, manufacturability, and cost-effectiveness.
SiC Grade | Key Characteristics | Typical Wear Applications | Relative Cost |
---|---|---|---|
RBSiC (SiSiC) | Excellent wear & corrosion resistance, good thermal shock resistance, free silicon content | Pump components, wear liners, nozzles, mechanical seals, kiln furniture | Moderate |
SSiC | Highest hardness, strength, wear & corrosion resistance, high-temperature stability | Bearings, high-performance seals, valve components, semiconductor parts | High |
NBSC | Good thermal shock resistance, good wear resistance, molten metal resistance | Kiln furniture, molten non-ferrous metal handling parts, some liners | Moderate |
Graphite-Loaded SiC | Improved self-lubricating properties | Dry running seals, specialized bearings | High |
Procurement managers and technical buyers should focus on SiC material specification for wear parts and work closely with suppliers to define the best grade.
Critical Design and Manufacturing Considerations for Maximizing SiC Wear Part Longevity
Simply selecting the right SiC grade is only part of the equation for achieving maximum wear part longevity. The design of the component and the manufacturing process itself play equally critical roles. Silicon carbide is a hard and brittle material, which presents unique challenges and opportunities in design and fabrication. Ignoring these considerations can lead to premature failure, even with the best material.
Key design and manufacturing aspects include:
- Designing for Manufacturability:
- Geometry: Complex geometries with sharp internal corners, thin walls, or abrupt changes in cross-section can create stress concentrations and make manufacturing difficult and costly. Generous radii, uniform wall thicknesses, and simplified profiles are preferred.
- Draft Angles: For pressed or molded parts, appropriate draft angles are necessary for easy removal from molds.
- Machining Allowances: While SiC can be machined to tight tolerances, it is a slow and expensive process (diamond grinding). Designs should minimize the amount of material that needs to be removed post-sintering or reaction bonding. “Near-net-shape” manufacturing is a key goal.
- Managing Brittleness and Stress Concentrations:
- Avoid Impact Loads: Designs should protect SiC components from direct impact loads where possible, or incorporate features to absorb or distribute impact energy.
- Fillets and Radii: Use generous fillets and radii at corners and transitions to reduce stress concentrations.
- Load Distribution: Ensure that loads are distributed evenly across the SiC component. Avoid point loads. Consider using compliant interlayers if clamping or bolting SiC parts.
- Interfacing with Other Materials:
- Thermal Expansion Mismatch: SiC has a relatively low coefficient of thermal expansion. When interfacing SiC with metals or other materials with different expansion rates, careful design is needed to accommodate differential expansion and prevent stress buildup, especially in applications with significant temperature variations. Techniques include using expansion joints, flexible attachments, or graded material interfaces.
- Attachment Methods: Bolting, clamping, brazing, or shrink-fitting are common methods. The chosen method must consider the brittle nature of SiC and avoid inducing excessive stress.
- Tolerances and Surface Finish:
- While extremely tight tolerances and fine surface finishes are achievable, they add cost. Specify tolerances and finishes that are truly necessary for the function of the wear part. For dynamic seals, a lapped or polished surface is crucial, but for a static wear liner, a ground finish might suffice.
- Manufacturing Process Selection:
- The choice between RBSiC, SSiC, or other grades often dictates the available manufacturing routes (e.g., slip casting, extrusion, isopressing, injection molding followed by sintering/reaction bonding). The complexity and size of the part also influence this decision.
- CAS new materials (SicSino) leverages its extensive network within Weifang, the hub of China’s silicon carbide production, and its own deep technological expertise rooted in the Chinese Academy of Sciences. This allows SicSino to guide customers through the optimal manufacturing pathway for their custom SiC wear resistant components, ensuring both quality and cost-effectiveness. Our team, specializing in customized production, assists in translating design concepts into robust, high-performance wear parts.
- Quality Control and Testing:
- Rigorous quality control throughout the manufacturing process, including raw material inspection, in-process checks, and final dimensional and NDT (Non-Destructive Testing) evaluations, is essential to ensure the integrity and performance of industrial SiC wear solutions.
By carefully considering these factors during the design and manufacturing stages, the inherent advantages of silicon carbide can be fully realized, leading to wear parts that offer exceptional service life and reliability. Working with an experienced supplier like SicSino, who understands the nuances of designing with technical ceramics, is crucial for success.
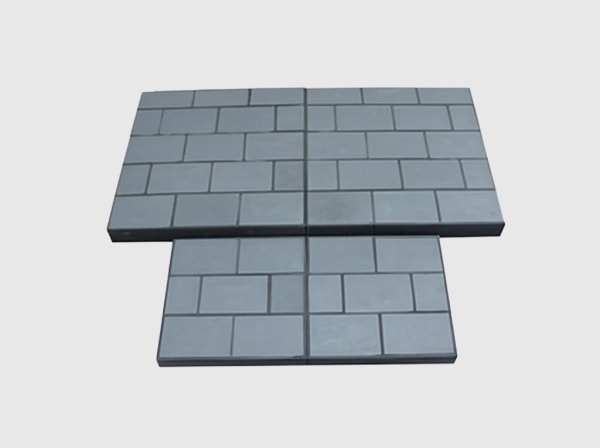
Achieving Precision: Tolerances, Surface Finish, and Their Impact on SiC Wear Performance
For many silicon carbide wear parts, particularly those involved in dynamic applications like seals, bearings, or precision flow control, the achievable tolerances and the quality of the surface finish are not just cosmetic details—they are critical determinants of performance and lifespan. The precision of custom ceramic components directly influences friction, wear rates, sealing efficiency, and overall system reliability.
- Achievable Tolerances:
- Silicon carbide components can be manufactured to very tight dimensional tolerances. As-sintered or as-reacted parts typically have wider tolerances. However, through precision diamond grinding, lapping, and polishing, tolerances in the micron (µm) range can be achieved.
- Typical Achievable Tolerances (after grinding):
- Dimensional Tolerance: ±0.01mm to ±0.05mm (can be tighter for specific features)
- Parallelism/Flatness: Down to 1−2µm for critical surfaces like seal faces.
- Cylindricity/Roundness: Down to a few microns.
- It’s important for procurement professionals and engineers to specify only the level of precision truly required by the application, as tighter tolerances significantly increase machining time and cost. Precision SiC machining is a specialized capability.
- Surface Finish Options and Their Importance:
- The surface finish of a SiC wear part plays a crucial role in minimizing friction and wear, especially in sliding or rotating contact.
- Grinding: Provides a good baseline finish, often suitable for static wear liners or components where surface micro-roughness is less critical. Typical Ra (average roughness) values can range from 0.4µm to 0.8µm.
- Lapping: Produces a very flat and smooth surface by abrading the SiC against a flat plate with fine diamond slurries. Lapped surfaces are essential for SiC mechanical seal faces to ensure proper sealing and minimize leakage. Ra values can be 0.1µm to 0.2µm or better.
- Polishing: Can achieve an even finer, mirror-like finish, further reducing the coefficient of friction and improving wear resistance in highly demanding applications like SiC bearings or optical components. Ra values can be well below 0.05µm.
- Impact of Surface Finish on Wear Performance:
- Reduced Friction: Smoother surfaces lead to lower coefficients of friction, reducing energy loss and heat generation in dynamic systems.
- Minimized Abrasive Wear: A fine surface finish reduces the number of asperities (microscopic high points) that can act as initiation sites for third-body abrasion or snagging.
- Improved Sealing: In mechanical seals, a highly lapped and flat surface is critical for maintaining a fluid film and preventing leakage.
- Extended Life: Lower friction and reduced wear directly translate to longer operational life for the SiC component and the entire assembly.
CAS new materials (SicSino) and its partner enterprises in Weifang possess advanced machining and finishing capabilities to produce high-precision SiC parts meeting the stringent requirements of various industrial applications. Our technical team can advise on the optimal surface finish and achievable tolerances to balance performance needs with cost considerations for your custom SiC wear solutions. This includes leveraging state-of-the-art measurement and evaluation technologies to ensure every component meets specification.
Finishing Process | Typical Surface Roughness (Ra) | Common Applications for Wear Parts | Key Benefit for Wear |
---|---|---|---|
As-Sintered/Reacted | >1µm (variable) | Some static liners, non-critical surfaces | Lower cost (no secondary machining) |
Grinding | 0.4µm−0.8µm | General wear liners, structural components, pre-lapping | Good balance of cost and improved surface |
Lapping | 0.1µm−0.2µm (or better) | Mechanical seal faces, valve seats, precision sliding components | Very low friction, excellent sealing |
Polishing | <0.05µm | High-performance bearings, optical windows, critical seal faces | Extremely low friction, minimal wear, high purity |
Understanding and specifying appropriate tolerances and surface finishes are vital steps in procuring effective silicon carbide wear components.
Partnering with the Right Supplier for Custom SiC Wear Solutions: Why CAS new materials (SicSino) Excels
Choosing the right supplier for custom silicon carbide wear parts is a critical decision that directly impacts component quality, performance, lead time, and overall project success. The ideal partner offers not just manufacturing capabilities but also deep material expertise, design support, and a commitment to quality. This is where CAS new materials (SicSino) stands out as a premier provider of custom SiC solutions in China.
Why SicSino is Your Trusted Partner:
- Deep Technical Expertise Rooted in CAS: SicSino is an integral part of the CAS (Weifang) Innovation Park, collaborating closely with the National Technology Transfer Center of the Chinese Academy of Sciences (CAS). This provides us with unparalleled access to cutting-edge research, advanced material science, and a vast talent pool. Our domestic top-tier professional team specializes in the customized production of silicon carbide products, possessing a wide array of technologies spanning material development, process optimization, design engineering, and meticulous measurement & evaluation.
- Strategic Location in China’s SiC Hub: We are situated in Weifang City, the epicenter of China’s silicon carbide customizable parts manufacturing. This region hosts over 40 SiC production enterprises, accounting for more than 80% of the nation’s total output. SicSino has been instrumental in this development since 2015, introducing advanced SiC production technology and fostering large-scale production and technological advancements among local enterprises. This unique position allows us to leverage a robust supply chain and offer cost-competitive custom SiC components without compromising on quality.
- Comprehensive Customization Capabilities: We understand that one size rarely fits all, especially in demanding wear applications. SicSino excels in providing highly customized SiC components tailored to your specific requirements. Our integrated process, from material selection and design optimization to manufacturing and post-processing, ensures that you receive parts that deliver optimal performance and longevity. We have supported over 10 local enterprises with our technologies, enabling them to meet diverse customization needs for OEM SiC wear solutions and end-users alike.
- Guaranteed Quality and Supply Assurance: Our commitment to quality is unwavering. By leveraging the scientific rigor of the CAS and our specialized in-house expertise, we ensure that every SiC wear part meets the highest standards of material integrity, dimensional accuracy, and performance. Our established network and technological support for local manufacturers provide a reliable and consistent supply chain for wholesale SiC wear components and specialized orders.
- Cost Drivers and Lead Time Transparency: We believe in transparent partnerships. Key cost drivers for custom SiC wear parts include:
- SiC Grade: SSiC is generally more expensive than RBSiC due to higher processing temperatures and purity.
- Part Complexity and Size: Intricate geometries and larger parts require more complex tooling and longer processing times.
- Tolerances and Surface Finish: Tighter tolerances and finer finishes necessitate more extensive machining, adding to the cost.
- Order Volume: Larger production runs typically benefit from economies of scale. Lead times can vary based on these factors, typically ranging from a few weeks for simpler parts to several months for highly complex components or large orders. SicSino works diligently to optimize production schedules and provide realistic lead time estimates, ensuring timely delivery of your industrial ceramic wear parts.
- Beyond Components: Turnkey Factory Solutions: For clients looking to establish their own specialized silicon carbide production capabilities, SicSino offers comprehensive technology transfer and turnkey project services. This includes factory design, procurement of specialized equipment, installation and commissioning, and trial production support. This unique offering allows you to build a professional SiC products manufacturing plant in your country, ensuring an effective investment, reliable technology transformation, and a guaranteed input-output ratio.
By choosing CAS new materials (SicSino), you are not just selecting a supplier; you are gaining a strategic partner dedicated to providing high-quality, reliable SiC wear solutions and fostering innovation in the advanced ceramics industry. We are committed to helping you overcome your toughest wear challenges and achieve superior operational outcomes.
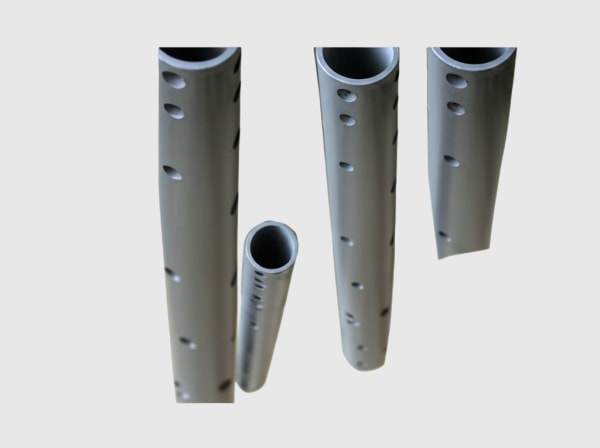
Frequently Asked Questions (FAQ) about Silicon Carbide Wear Parts
Engineers, procurement managers, and technical buyers often have specific questions when considering silicon carbide for their wear applications. Here are some common queries with concise, practical answers:
- What are the main advantages of using silicon carbide for wear parts compared to other materials like tungsten carbide or alumina ceramics? Silicon carbide generally offers a superior combination of properties for many wear applications.
- Compared to Tungsten Carbide (WC): SiC is significantly lighter (about 2.5 times less dense), has better corrosion resistance in many acidic and alkaline environments, and typically offers better high-temperature wear resistance (WC often uses a metallic binder like cobalt, which can limit its high-temperature performance and corrosion resistance). SiC is also generally harder than many WC grades. However, WC can offer superior toughness and impact resistance.
- Compared to Alumina (Al2O3): SiC is substantially harder and has much higher thermal conductivity than alumina, leading to better thermal shock resistance in many cases (though some specialized alumina grades can also have good thermal shock properties). SiC also exhibits superior wear resistance in most abrasive and erosive conditions. Alumina is often less expensive but may not provide the same lifespan in severe wear scenarios. The best choice depends on the specific application’s balance of wear type, temperature, chemical exposure, impact conditions, and cost considerations.
- How does the cost of custom silicon carbide wear parts compare to traditional metal components or other ceramics? Custom silicon carbide wear parts generally have a higher upfront cost compared to many traditional metal components (e.g., hardened steel, wear-resistant alloys) and some commodity ceramics like alumina. However, the true value lies in their significantly extended service life, reduced downtime, and lower maintenance requirements in aggressive wear environments.
- Factors influencing SiC cost: SiC grade (SSiC is more expensive than RBSiC), part complexity, size, precision (tolerances and surface finish), and order volume.
- Lifecycle Cost: When considering the total lifecycle cost (including replacement parts, labor, and lost production due to downtime), SiC wear solutions often prove to be more economical in the long run for demanding applications. The initial investment is offset by substantially longer operational periods and fewer interruptions. For example, a SiC pump sleeve might cost more than a metallic one, but if it lasts 5-10 times longer, the overall cost savings are significant.
- What information do I need to provide to get an accurate quote for custom SiC wear parts from a supplier like SicSino? To receive an accurate and timely quotation for custom SiC wear components, providing comprehensive information is crucial. Key details include:
- Detailed Engineering Drawings: These should specify all dimensions, critical tolerances, required surface finishes, and any geometric features (e.g., chamfers, radii, holes). CAD files (e.g., STEP, IGES) are highly preferred.
- Material Grade: Specify the desired SiC grade (e.g., RBSiC/SiSiC, SSiC) if known. If unsure, describe the application in detail so the supplier can recommend a suitable grade.
- Operating Conditions:
- Nature of the wear (abrasion, erosion, corrosion, impact).
- Type of media being handled (e.g., slurry composition, particle size and hardness, chemical nature, pH).
- Operating temperature (continuous and maximum, any thermal cycling).
- Pressure and velocity of media.
- Mechanical loads or stresses on the part.
- Quantity Required: Specify the number of parts needed for the initial order and anticipated annual demand, if applicable, as volume affects pricing.
- Application Description: A clear explanation of how and where the part will be used helps the supplier understand the functional requirements.
- Existing Part Information (if replacing a part): If replacing an existing component made of another material, provide details about its performance, failure modes, and lifespan. The more detailed the information, the better CAS new materials (SicSino) can understand your needs and provide a precise quotation and effective solution for your technical ceramic procurement.
Conclusion: Elevating Industrial Performance with Custom Silicon Carbide Wear Solutions
In the face of escalating operational demands and the relentless pursuit of efficiency, custom silicon carbide wear parts stand out as a transformative technology. Their exceptional hardness, unparalleled resistance to abrasion, corrosion, and high temperatures, coupled with the ability to be precisely engineered for specific applications, offers a powerful solution to the pervasive challenge of industrial wear. From the abrasive slurries in mining to the corrosive environments in chemical processing and the extreme temperatures in power generation, advanced SiC components are consistently proving their ability to extend equipment life, reduce costly downtime, and enhance overall productivity.
Choosing the right material and, just as importantly, the right partner is paramount. CAS new materials (SicSino), with its profound expertise rooted in the Chinese Academy of Sciences and its strategic position within Weifang’s SiC manufacturing hub, offers not just components, but comprehensive solutions. We provide access to a spectrum of SiC grades, cutting-edge design and manufacturing capabilities, and a commitment to quality that ensures your custom SiC wear parts deliver optimal performance and value. Whether you are an OEM seeking reliable high-performance ceramic wear parts or an end-user looking to upgrade critical equipment, SicSino is dedicated to helping you harness the full potential of silicon carbide. By investing in custom SiC technology, industries can significantly fortify their operations against wear, paving the way for enhanced reliability and a stronger bottom line in today’s competitive global landscape.
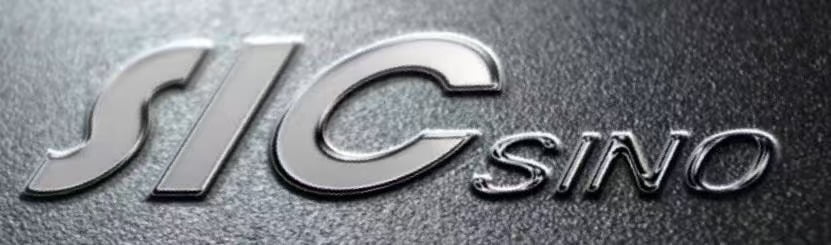
SicSino – CAS new materials
We, CAS new materials(SicSino), have been introducing and implementing silicon carbide production technology since the 2015, assisting the local enterprises in achieving large-scale production and technological advancements in product processes. We have been a witness to the emergence and ongoing development of the local silicon carbide industry.
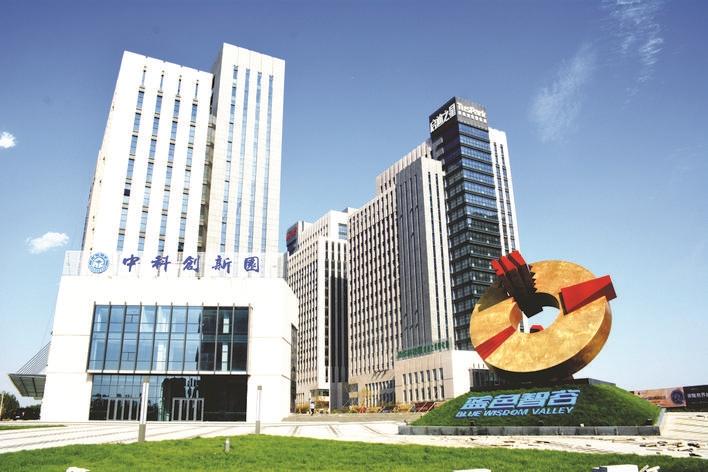